Chapter I
Reproducing Natural Teeth in Dental Porcelain
Reproducing Natural Teeth in Dental Porcelain
The main features in a natural tooth that must be reproduced in dental porcelain are colour, translucency and texture.
The total colour effect in a natural tooth is derived from a combination of light directly reflected from the tooth surface combined with light that has been reflected from the dentine and which has already undergone some internal reflection and refraction. The dentine is the prime source of colour and the reflected rays of light which are emitted through the enamel are modified by the thickness and degree of translucency of the enamel. Human enamel contains approximately 97 per cent by weight mineral matter, mostly in the form of hydroxyapatite. Enamel is very translucent and may transmit up to 70 per cent light through a 1 mm thick section. By contrast, dentine only contains about 70 per cent by weight of hydroxyapatite and the rest is collagen matrix. Dentine is still translucent but will generally not transmit much more than 30 per cent light on a 1 mm thick section.
The reflection and transmission of light producing colour and translucency in a tooth are illustrated in Figure 1-1 and compared with a section through a natural tooth (Fig. 1-2). The tooth can be divided into three areas.
Figure 1-2a
Enamel constitutes the major part of this area and as the thinner incisal edge is approached it can assume almost a glass-like clarity (Fig. 1-1). The enamel also extends around the approximal areas and will highlight the approximal space. High translucency in this area is one of the reasons why human teeth do not have a stark appearance; the edges are softened by light transmission (Fig. 1-3a and b). Failure to capture this effect in ceramics is a common fault resulting in a solidity and starkness that is totally unnatural. The metal-ceramic crowns in Figure 1-4a have been replaced with more translucent aluminous porcelain crowns and higher light transmission has softened their appearance (Fig. 1-4b).
The middle third of the tooth contains a major quantity of dentine and is less translucent. Colour of the enamel will be influenced by the dentine hue and its natural blue-greyness will have overtones of yellow, orange and brown (Fig. 1-1).
Figure 1-4b
Fig. 1-4a and b (a) Poorly made metal-ceramic crownson the maxillary incisors showing high specular reflection and solidity of outline due to lack of approximal translucency. (b) Metal-ceramic crowns replaced with Vita-Pt crowns with higher translucency and reduced specular reflection. The approximal areas are softer in appearance and the crowns blend in with the natural dentition. The distal aspect of 22 has also been recessed giving a better front-to-back progression in the dentition.
As the enamel approaches the cervical line of the tooth crown, it thins down to a chisel or chamfer edge. The influence of the underlying dentine on the colour of the tooth is quite marked. The neck of the tooth will assume a deeper hue which will vary in colour from orange-yellow to a distinct brown, depending on the age and degree of calcification of the dentine. In addition, the pink gum will have some effect on hue (Fig. 1-1). Tooth manufacturers have recognised this gradation in colour and therefore produce porcelain to match each area (Fig. 1-5):
Incisal enamels for high translucency.
Overlay enamels for general coverage.
Body dentines for bulk build-up.
Gingival dentines for increasing colour intensity.
In addition, opaque porcelain for masking metal or cement surfaces and concentrated colours for duplicating internal and surface stains are supplied.
A natural tooth in its unworn state does not present an absolutely smooth surface. In general, it may be seen as a gentle, undulating surface, traversed horizontally with very fine grooves. These are the perikymata, and accurate simulation of these surface irregularities is as important as the matching of shade and shape. If light should reflect off a restoration in a different way from the neighbouring teeth, even if shade and form matching are accurate, it will give the effect of being artificial. Glazing of a ceramic crown is therefore a critical procedure. In addition to the effect on texture, if a crown is over-glazed, it will produce an homogenous glassy surface which obliterates all the “prismatic” effect of dental porcelain. A correctly glazed enamel will only melt to a depth of about 25 µm (McLean, 1979) and the rest of the porcelain should only be fused or sintered at its grain boundaries, i.e. the surfaces of the glassy grains of porcelain should remain almost intact (Fig. 1-6). When the grain boundaries are fused together and not obliterated a prismatic effect is created which can closely simulate the hydroxyapatite structure of human tooth enamel (Fig. 1-2b).
A perfectly matched ceramic crown should submerge itself in the mouth. It must have depth of translucency, with colour built in to the various layers of porcelain. Ridge and point angles should blend with the surrounding teeth and facial and lingual planes must harmonise with the dental arch. In order to achieve these objectives it is clear that only complete porcelain veneer crowns can be made with all these desirable characteristics since once a metal coping is used to reinforce the porcelain, most of the light transmission is blocked in the cervical two-thirds of the crown.
A natural tooth always allows diffuse transmission of light (Figs. 1-1 and 1-2) and the metal-ceramic crown violates this property. This point is well illustrated in Figure 1-7 in which a metal-ceramic crown has been illuminated with a fibre-optic light to show the dark shadow cast by the metal. By contrast, a complete aluminous porcelain veneer crown shown in Figure 1-8 is transmitting light throughout the entire body. Because of this property these crowns can be made with greater depth of translucency and they exhibit less specular reflection from the facial surfaces.
By contrast the metal-ceramic crown will only permit diffuse reflection and specular reflection of light in the body area and resultantly tend to look brighter in the mouth. This brightness is due to high reflection from paint-on opaques and is difficult to eliminate unless there is at least 1.5 mm of porcelain covering the metal.
The greatest problem in making metal-ceramic crowns is to reduce specular reflection from the facial surfaces. The ceramist is always fighting for space to avoid high spots. Methods of creating the illusion of translucency will be shown but it must be clearly recognised that ultimate perfection still lies in duplicating the structure of natural teeth. This can only be done where there is depth of porcelain, and translucent veneer porcelains can be used to advantage. Surface colourants can never provide the answer since colour must be seen in depth. Surface colourants behave like opaque porcelains and produce highly reflective surfaces (Fig. 1-9). Surface stain should be confined to its correct place, to simulate surface stains or defects that are naturally occurring in human teeth. In very special circumstances it may be necessary to use a wash of stain to reduce a bright spot over the opaque but this is an undesirable compromise.
The metal-ceramic technique will be given great prominence since it is the most useful and widely used system available in dental ceramics. However, an awareness of the aesthetic problems of these materials can only help both the dentist and the technician to raise their standards even further.
There is a tendency today, often because of commercial pressures, to use only one brand or system of porcelain. No single system can answer all the clinical problems presented, and for this reason, both metal-ceramics and aluminous porcelains are used in our laboratory to meet the specific requirements of each case. In many instances the two are combined in one rehabilitation with alumina reinforced crowns being used on the incisors and cast metal-ceramic crowns on the posterior teeth. In view of the versatility of current porcelains, it is essential that technicians become familiar with all systems and types of porcelain available.
There are three main types of porcelain:
- Regular felspathic porcelain.
- Aluminous porcelain.
- Metal bonding porcelains.
For convenience, all the above porcelains may be classified in their temperature ranges (British Standard No. 5612).
Temperature | Maturing |
High | 1200°C – 1400°C |
Medium | 1050°C – 1200°C |
Low | 800°C – 1050°C |
There are two main types of crown. The complete porcelain veneer and the metal-reinforced porcelain crown. These will now be considered in detail.
The Complete Porcelain Veneer Crown
Porcelains made for this technique have been in existence the longest and continue to set a high aesthetic standard. They are generally in the medium maturing range (1050°C–1200°C) and made for vacuum firing. The types of felspathic porcelain used in making a jacket crown are illustrated in Figure 1-10.
The opaque – a felspathic glass loaded with opacifiers such as zirconium or titanium dioxide.
Body dentine – coloured felspathic glasses with high translucency.
Gingival dentine – coloured felspathic glasses with reduced translucency.
Overlay enamel – highly translucent felspathic glasses often containing sub-micron opacifiers or crystalline material to create special colour effects.
Incisal enamel– colourless glasses to simulate thin incisal edges.
Concentrated stains and modifiers.
A typical medium maturing felspathic porcelain for vacuum firing would have a formula as follows:
Oxide | Weight percent |
SiO2 | 64.2 |
B2O3 | 2.8 |
K2O | 8.2 |
Na2O | 1.9 |
Al2O3 | 19.0 |
Li2O | 2.1 |
MgO | 0.5 |
P2O5 | 0.7 |
Maturing temperature 1060°C–1080°C
2. The Aluminous Porcelain Crown
The aluminous porcelains were developed in England by McLean and Hughes (1965) with the object of improving the strength of the porcelain jacket crown without sacrificing aesthetics.
The porcelains used in this technique are illustrated in Figure 1-11.
Core porcelain – the highest strength porcelains containing up to 50 per cent by weight fused alumina crystals. The fused alumina crystals (specific surface area of approximately 3500 cm2/gram) are mixed or fritted with a glass powder of matching thermal expansion. The transverse strength of these alumina-glass composites is 130 to 150 N/mm2 (dental porcelain strength 70 to 85 N/mm2). Their low expansion and refractory nature also makes them very resistant to thermal shock.
Dentine or body porcelain – made from a borosilicate glass, containing a high dissolved alumina content or, alternatively, a completely dissolved (fritted) felspar glass flux containing additional quantities of alumina both in the free state and dissolved in the glass. The free alumina crystal content of these glasses is restricted to about 5 to 10 percent. Details of their composition are given in Volume I, page 99 (McLean, 1979).
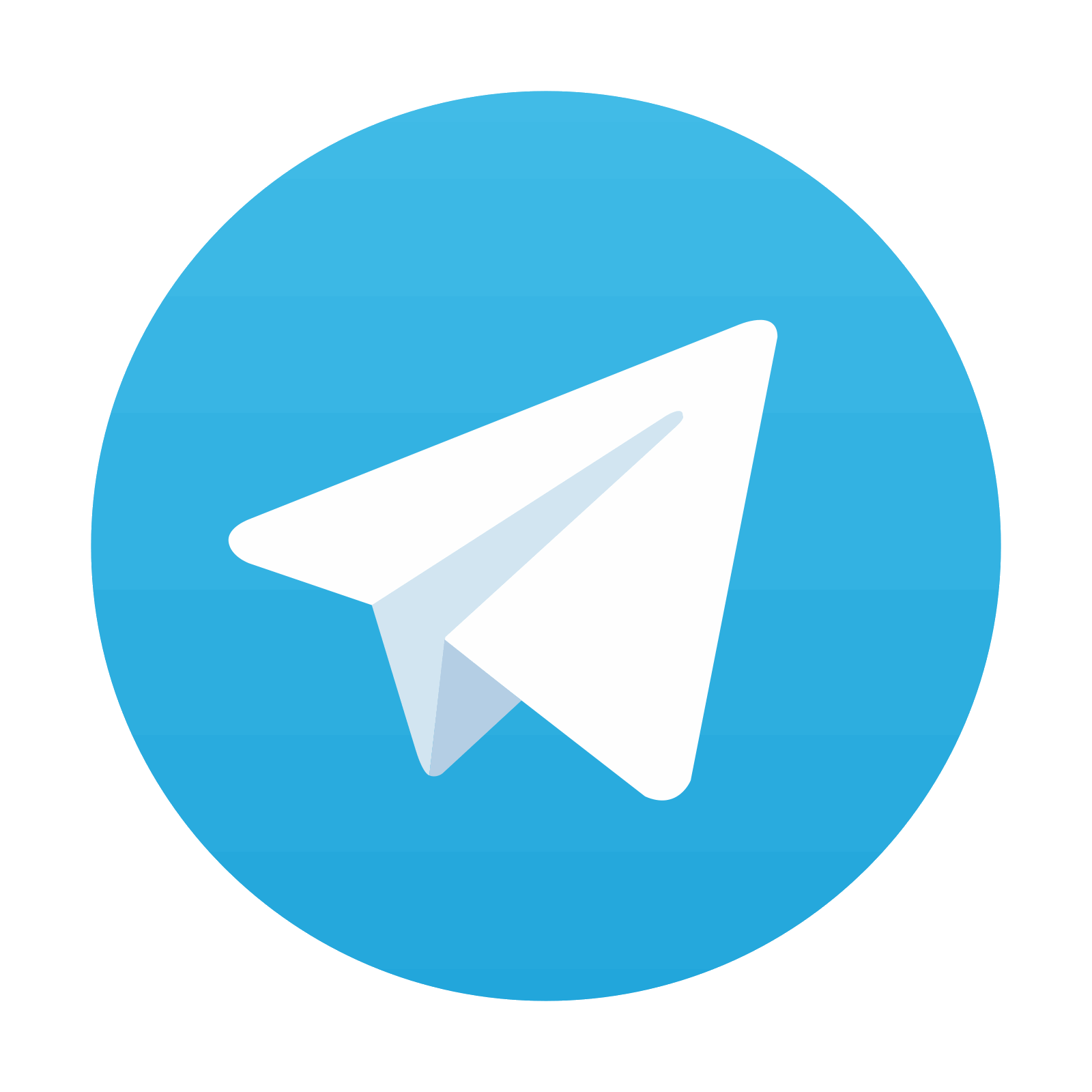
Stay updated, free dental videos. Join our Telegram channel

VIDEdental - Online dental courses
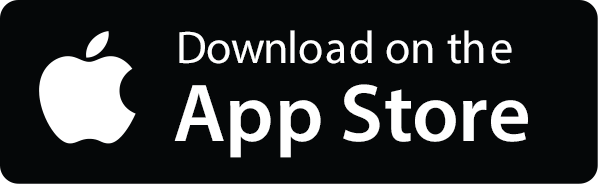
