3
Direct Digital Manufacturing
Gerald T. Grant
3.1 Introduction
Advances in medical imaging, light, and laser scanning technologies, development of dental and medical design software, and adaptation of computer‐manufacturing techniques have all contributed to the digital revolution. Over the past two decades, medical images have merged with digital fabrication processes to become an essential process in the fabrication of medical models and have been used extensively in creating cranial implants for the U.S. military (Gronet et al. 2003). Indeed, these days, medical modeling of cranial defects is routine for U.S. military medical facilities for cranioplasty and craniofacial reconstructions (Taft et al. 2011) (Figure 3.1).
Several digital impression systems are available in the market (see Chapter 2). They offer excellent scanning accuracy and user‐friendly software and allow for a seamless integration of computer‐aided design/computer‐assisted manufacturing (CAD/CAM) techniques in the dental office and laboratory. Computer‐aided design/computer‐assisted manufacturing techniques have the potential to streamline the conventional dental laboratory process, by minimizing or eliminating traditional impressions and lost wax casting techniques; thus, reducing the time to deliver a dental restoration. Faced with a shortage of skilled dental laboratory technicians, alternative methods that provide dental prostheses in a timely manner are becoming more attractive. The Bureau of Labor Statistics (United States Department of Labor 2013) reports that they expect little or no change in the job outlook of dental laboratory technicians for the next 10 years citing a less than 1% growth with a median annual wage of about $35 000. As CAD/CAM and other direct digital manufacturing (DDM) techniques become more advanced, the traditional skills of the dental laboratory technician will necessarily be redefined to include more digital knowledge. As CAD/CAM skills replace traditional craftsman skill sets in dental laboratory, increased productivity should offset the shortage of laboratory technicians.
The use of DDM techniques in dentistry and medicine is based on the “Scan, Plan, and Manufacture” principle of digital workflow paradigm (Figure 3.2). Each part of this workflow paradigm is based on distinct technologies: scanning technology to capture the anatomy, software applications to digitally compose the design, and DDM technology to render the design into a durable restoration or prosthesis. The development of all of these technologies continues to improve, characterized by the number of new hardware and “advancements” or upgrades of each step of the process.
3.2 Scanning Devices
Intraoral scanning devices preclude the need for impressions and casts, which streamlines the dental restoration to a purely digital process. However, many of the digital scanning technologies still depend on traditional impression and casts to generate a digital copy of the oral anatomy. Whether intraoral scanning or a scan of the impression or cast is used, the captured digital files of the oral anatomy possess sufficient detail resolution to fabricate a well‐fitting restoration by a variety of DDM approaches. Scanning technologies are based on a variety of optical or laser surface capture approaches, which present no exposure risk to the patient, unlike conventional medical imaging techniques that currently cannot match this level of detail resolution.
Conventional medical imaging from CT, magnetic resonance imaging (MRI), and ultrasound has transitioned from stacks of film to a standardized digital format (Figure 3.3). Digital imaging and communications in medicine (DICOM) is the current standard for digital storage and retrieval of medical images, DICOM files are compatible with a variety of medical image viewers from different vendors.
Software has been developed that allows DICOM images to be converted into a three‐dimensional (3D) surface model, providing access to the use of CAD manipulation for virtual surgical manipulation, design of surgical guides, custom fixation devices, medical devices, and their digital manufacturing as a device or model. Although these images generally lack the details necessary for direct restoration planning, they do offer a picture of the internal anatomy at sufficient resolution for treatment planning and development of treatment aids, such as oral surgery guides. When translated into a standard 3D digital format, anatomy from medical images and oral scanning techniques may be merged in CAD/CAM applications.

3.3 Digital Manufacturing
Prostheses designed using a CAD application are fabricated by a DDM device. These devices generally fall into one of two categories, subtracting manufacturing technology (SMT) or additive manufacturing technology (AMT). Subtractive manufacturing technology is the more common technology; based on conventional computer numerical control (CNC) milling (Figure 3.4). Subtractive manufacturing technologies are generally limited by geometric complexity and are not suitable to produce all shapes; however, AMT can fabricate the far more complex organic forms (Figure 3.5). Although SMT‐based CNC milling systems have been the predominant DDM technology in dentistry, the advancement of AMT provides the flexibility in design, fabrication, and economy of cost to support digital manufacturing in the future.
Subtractive manufacturing technology approaches generally process the model into tool paths to direct a cutting tool and spindle. Additive manufacturing technology generally slices the 3D model into regular planes with instructions for material deposition, polymerization, or fusing in each plane. Additive manufacturing technology is more sensitive to the integrity of these 3D model files as opposed to the SMT process.
3.4 File Format in The Digital Workflow
Historically, most dental CAD/CAM systems have been generally “closed” systems; the image file, CAD application, the CAD output file, and tool paths (instructions of movement to the cutter of a milling system) are compatible only in that system; therefore, there has been limited ability to select different imaging systems, design software, and digital manufacturing as a preference. However, as newer technologies and a better understanding of CAD/CAM technologies by the dental profession begin to prevail, there has been a trend toward flexibility between scanners, design software, and manufacturing devices, with more open options (interoperability) available.




System interoperability is dependent on the use of a common file format for the “Scan” step forward in the workflow. This has been achieved in medical imagery with the near universal adoption of the DICOM file format, developed by the National Electrical Manufacturers Association (NEMA) for storage of all medical images. MRI, CT, ultrasound, and other medical imaging systems all use this file format to describe their images. DICOM enables the integration of scanners, servers, workstations, printers, and network hardware from multiple manufacturers into a picture archiving and communication system. The different devices come with DICOM conformance statements that clearly state which DICOM classes they support. DICOM has been widely adopted by hospitals and the Department of Defense Medical Care systems. However, the standard is not widely accepted in dentistry, demonstrated by the proprietary image formats common in some cone beam CT scanners, intraoral scanners, and dental CAD/CAM systems.
Interoperability during planning and manufacturing stages depends on the use of a common 3D file format between the imaging output, the CAD application, and the DDM device. A number of suitable digital file formats exist:.ply,.obj,.vrml,.amf to list but a few; however, the most common digital file format is the.stl (surface tessellation format) file format. The.stl file format enables the approximation of the shape of a part or the entire assembly using triangular surface facets (Figure 3.6).
Generally, the smaller the facet, the higher the quality of the surface produced. When linked together into a closed surface, these triangular facets compose a 3D approximation of an object such as the patient’s anatomy or a prosthesis design. This 3D surface is processed into machine code to direct the DDM fabrication, usually using vendor‐specific software applications provided with the DDM device.

The.stl file format is limited to surface geometry, which is a suitable definition for most currently available DDM devices. However, the future direction of AMT‐based DDM will allow for esthetic and mechanical material properties to be varied in the fabrication process. New 3D file formats, such as.amf (AM format), are under development, which will allow for the 3D definition of shape, esthetic properties, and mechanical properties in 3D. Future workflow will necessarily be based on a common 3D file format that supports these additional pieces of information.
3.5 Additive versus Subtractive Manufacturing Technologies
As discussed earlier, DDM technologies can manufacture parts by two basic approaches: (i) SMT in which material is selectively removed from a bulk billet by mechanical cutting, chemical processes, electrical discharge, or directed energy and (ii) AMT in which materials are selectively fused or deposited, typically in layers.
3.5.1 Subtractive Manufacturing Technology
Subtractive manufacturing technology has been the dominant method for dental fabrication since the advent of dental CAD/CAM systems. A wide range of dental restorative materials, from composites, to ceramics, to metals can be processed by these systems. Typically, these systems are based on high‐speed CNC milling technology, whereby a billet of homogeneous material is shaped by the removal of small chips by one or more cutters moved in a number of axis, and/or rotated, with respect to the work piece (Figure 3.7).
The number of degrees of freedom of cutter and material movement limits the complex geometry and features of the manufactured part. Typically, SMT milling devices have three to five degrees of freedom; four or more degrees of freedom are required to mill overhang features. They utilize high‐speed milling cutters and because they rotate much faster than conventional milling machines, the cutting forces remain small. Thus cooling is not needed for most materials since the removal of the chips buffers the heat and vibrations can be minimized (Gunnink 1998). Minimum feature size and surface finish quality are governed by the cutter tool size and rotational speed.

A 3D geometry from a CAD file is used to create tool paths to direct the SMT device. Posts, or sprues, must be added to the manufactured shape to hold the work piece during the fabrication process. Next, a digital file is generated, which specifies the tool selection: spindle movement paths, work piece movement, and spindle speeds (Figure 3.8). Generally vendor‐specific software provided with the SMT device prepares this file. These software packages often limit the user to specific material billets, in specific shapes (“blocks” or “pucks”). Depending on the material employed, some post‐processing manipulation of the material is necessary, such as sintering of a green ceramic restoration, or application of esthetic treatments, such as stain and glazing, or stacking conventional porcelains to a coping.

The advantages of SMT include:
- SMT is well suited for fabrication when the surface finish and shape is important;
- Ease of use – the process of removing material is not complicated; therefore, chances of failure are low;
- Capable of handling incorrect STL files–systems are not sensitive to small inconsistencies in solid geometry and can even handle single surfaces with minimal thickness;
- Choice of materials – materials can be manufactured in a manner that lends itself to quality assurance and consistancy
- Definable accuracy – the distance between the tool paths can be chosen, generally from 0.01 to 10 mm or larger. However, the slower the building speed, the greater the resolution;
- Cost – light CNC milling machines can be relatively inexpensive.
The disadvantages of SMT include:
- Not suited for cross‐sectional fabrication – cannot produce structures within structures or enclosed hollow structures;
- Limited axis of rotation – there is some limitation of the accuracy and achievability of an organic shape due to the number of axes the mill allows. The basic CNC machine uses three controlled axes: x, y, and z. Advanced machines may be equipped with a fourth axis (rotation table), or with five axes where the tool and the material can be rotated to approach the geometry from different directions;
- Cutter wear – due to the nature of the technology, cutters can become dull and inefficient if hard materials are desired. In dental fabrication, non‐sintered materials are often used to increase cutter life.
- Cost of Material – milling stock is available in standard size and there can be excessive waste depending upon the size of the item to be milled in relation to the stock size available.
3.5.2 Additive Manufacturing Technology
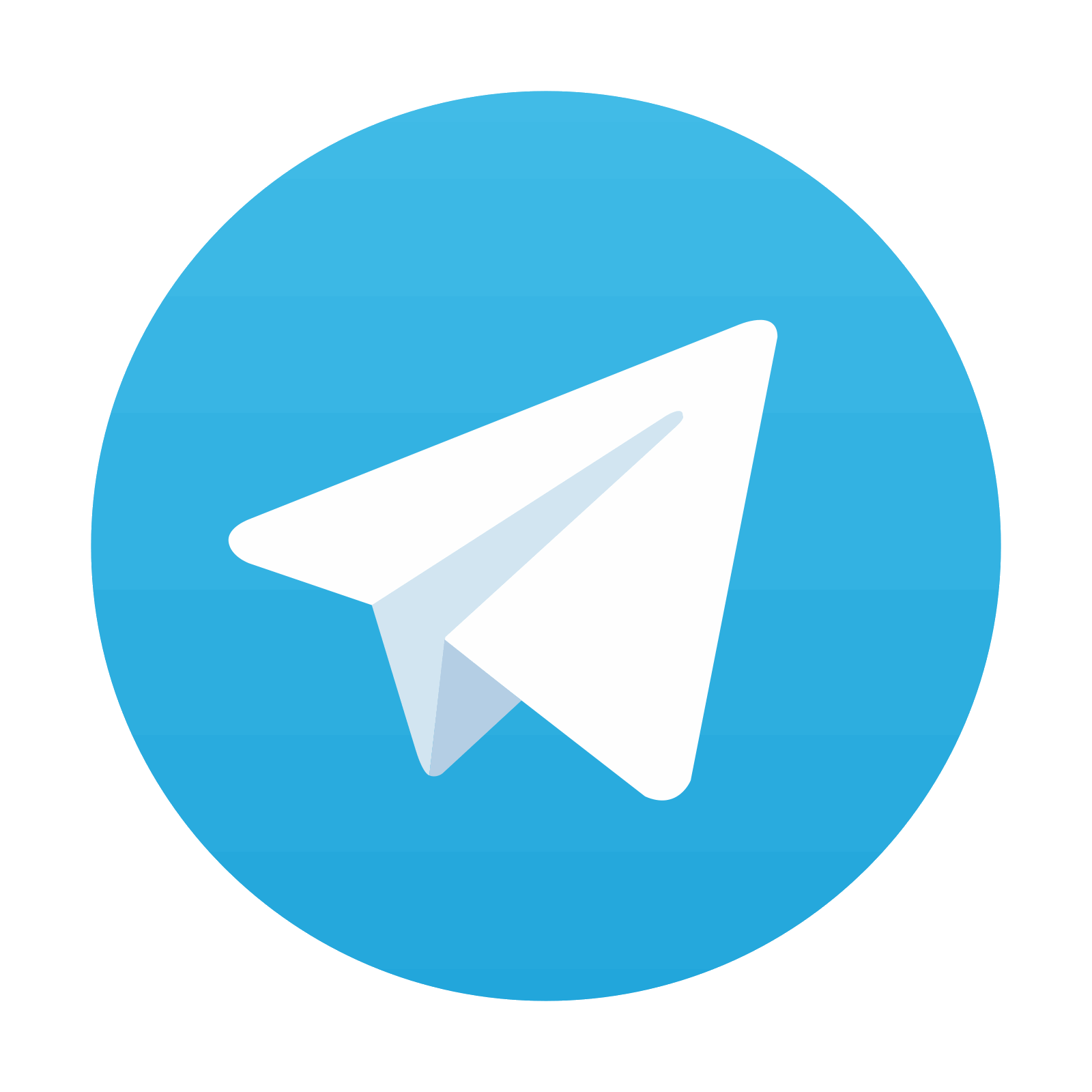
Stay updated, free dental videos. Join our Telegram channel

VIDEdental - Online dental courses
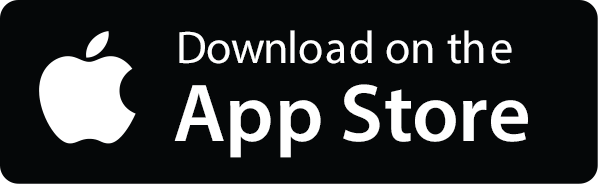
