Graphical abstract

Abstract
Objective
This investigation tested pre-shaded 3Y-TZP materials on optical, mechanical and structural properties and calculated correlations between these properties.
Methods
Seven A2-shaded 3Y-TZP zirconia materials were investigated on translucency (T) via UV–vis-spectrophotometer, fracture load of 3-unit FDPs (FL), biaxial flexural strength (FS), Chevron-Notch Beam (CNB), fracture toughness ( K IC ) and Martens parameter (hardness: HM and indentation modulus: E IT ). FL, FS and K IC were measured in a universal testing machine. The grain size was evaluated by scanning electron microscopy (SEM). Data was analyzed using one-way ANOVA followed by post hoc Scheffé, Kruskal–Wallis-, Mann–Whitney- U – and Pearson-test ( p < 0.05).
Results
For translucency, negative correlations were found with results of facture load ( R = −0.444, p < 0.001) and K IC ( R = −0.503, p < 0.001). While a positive correlation was found between translucency and flexural strength ( R = 0.238, p = 0.019), between fracture load and E IT ( R = 0.227, p < 0.029), between fracture load and K IC ( R = 0.362, p < 0.001) as well as between fracture load and the grain size ( R = 0.598, p = 0.007). While the grain size positively correlated with E IT ( R = 0.534, p = 0.017) as well as E IT with HM ( R = 0.720, p < 0.001).
Significance
Despite of being based on the same raw material, tested zirconia materials significantly differed regarding optical, mechanical (except biaxial flexural strength and Martens hardness) and structural properties. Materials with highest optical properties were those with lowest mechanical properties (CER, COP).
1
Introduction
The development of dental zirconia materials made remarkable progress during the past years resulting in a diversity of different products offered on the market . Despite that the raw material (zirconia powder) is provided by nearly one single supplier only, many dental companies have been specialized in processing the raw material into semi-finished products, namely zirconia blanks. Even though, the basic material is the same, the quality of zirconia blanks and thus the quality of the final product varies from manufacturer to manufacturer. This might depend on different approaches and parameters during processing the powder to zirconia blanks with respect to the pressing and pre-sintering process.
Zirconia blanks in the white body state are made for the subtractive processing via CNC (Computerized Numerical Control) milling machines to produce cost-effective dental restorations. Thus, the overall goal of the manufacturers is to produce zirconia blanks that are easily processable and obtain the best mechanical and optical properties for the final product. The overall high mechanical properties of zirconia allow the fabrication from single-unit restorations to multi-unit bridges.
Originally, zirconia was used as framework material, but for the past years the development of zirconia powders was triggered by the early demand for monolithic zirconia restorations using high translucent materials. The intention was to avoid chipping or delamination of more esthetic multilayered restorations . The translucency of zirconia materials highly depends on the microstructure . Depending on the amount of light being transmitted, absorbed and reflected, different optical properties of the material can be achieved . Since the high translucency of zirconia materials is aspired, modifications of the established 3 mol% yttria-stabilized tetragonal zirconia powder (3Y-TZP) were required to meet the trend toward the use of monolithic restorations and thus the demand for high translucent zirconia materials occurred. The change of the microstructure was obtained by reducing the content of the dopant alumina (Al 2 O 3 ) from 0.25 to 0.05 wt% . At the same time, the grain size of the dopant was reduced and relocated to the zirconia boundaries, which allows higher light transmittance . By this procedure two different raw material powders were created based on 3Y-TZP. For both zirconia powders, the manufacturers needed to adjust the processing parameters in order to sustain the different characteristic properties of the powders in form of the milling blank. Not only varying press and pre-sintering parameters have an effect on the final outcomes of the zirconia blank, but also the coloring recipe has an impact on certain properties.
Most zirconia blanks are available as non-shaded, but some are also accessible as pre-shaded or even multilayered providing good color matching to the esthetic characteristics of natural teeth . In pre-shaded materials, the color matching is obtained by the addition of various metal oxide dopants such as Fe 2 O 3 . Depending on the type of dopant and its concentration, different shades are created and assigned to the VITA classical shades. Due to the addition of metal oxide dopants, impacts on the mechanical properties beyond the optical ones were assumed .
Among mechanical properties, flexural strength is one of the preferred parameters used in dentistry for determining the clinical indication of a material. However, the standard classification of ceramic materials based on their flexural strength was objected since in many cases the performance of products made of ceramics is controlled by their deformation behavior and fracture resistance . The fracture resistance, also referred to as fracture toughness, is known to be one of the most important parameters in evaluating ceramic materials and material selection for specific engineering uses that include cyclic loading, like it is the case in dental applications. The fracture toughness is strongly recommended to be evaluated wherever mechanical stability is of interest and has become a key property to evaluate and compare the material quality . But it was stated that standardized mechanical tests measuring flexural strength and fracture toughness only afford figures of merit for ranking materials but offer little physical insight into long-term performance or as to how critical configurational parameters may be optimized. In this context, it was demanded that testing protocols should at least embody the basic elements of clinical geometry and stress state, since dental restorations are subject to loading by occlusal contact and flexure at high loads under onerous cyclic conditions in aqueous environment .
The present investigation included the above mentioned standardized mechanical tests to evaluate and compare pre-shaded 3Y-TZP zirconia materials that are based on the same raw material (alumina: 0.05 wt%) on flexural strength, fracture toughness and fracture load measurements after thermal, mechanical and cyclic loading in a chewing simulator. For identifying further characteristics and the relations to each other, Martens hardness parameter as well as translucency and the grain size of the tested A2-shaded zirconia materials were determined. The null hypothesis stated that based on the same raw material, the tested materials result in comparable results of translucency ( T ), biaxial flexural strength (FS), fracture toughness ( K IC ), fracture load (FL), Martens hardness parameter (HM and E IT ) and grain size. The further hypothesis stated that no correlations between the properties are found.
2
Material and methods
This study tested the mechanical and optical properties of seven different A2-shaded 3Y-TZP materials ( Table 1 ). All specimens were designed and milled using a five-axis milling machine (Ceramill Motion 2, Amann Girrbach, Koblach, Germany) and sintered in a sintering furnace (LHT 02/16, Nabertherm, Lilienthal/Bremen, Germany) according to individual manufacturer’s instruction ( Table 1 ). Translucency was analyzed with a UV/vis spectrophotometer (Lambda 35, PerkinElmer LAS, Rodgau, Germany). FL, FS and K IC were measured in universal testing machine (1445 Zwick/Roell, Ulm, Germany). HM and E IT were measured with testing machine ZHU 2.5 (Zwick Roell, Ulm, Germany).
Product name Abbreviation |
LOT-No. | Manufacturer | Composition (wt%) | Sintering parameters | ||
---|---|---|---|---|---|---|
Temperature (°C) | Heating/cooling rate (°C/min) | Holding time (hh:min) | ||||
Argen Z Esthetic ARG |
Z564791 | ARGEN dental; Düsseldorf, Germany |
ZrO 2 : 90.95 Y 2 O 3 : 4.5–6.0 HfO 2 : ≤5 Al 2 O 3 : 0.5 |
RT-1525 1525 1525–100 100-RT |
7 0 7 |
03:30 02:00 03:25 Uncontrolled |
Ceramill Zolid PS CER |
1702000 | Amann Girrbach; Koblach, Austria |
ZrO 2 + HfO 2 + Y 2 O 3 : ≥99.0 Y 2 O 3 : 4.5–5.6 HfO 2 : ≤5 Al 2 O 3 : ≤0.5 other oxides: ≤1 |
RT-1450 1450 1450-RT |
8 0 5 |
02:56 02:00 04:42 |
Cercon HT CON |
18030239 | Dentsply Sirona; Hanau, Germany |
ZrO 2 : 90 Y 2 O 3 : 5 HfO 2 : <3 Al 2 O 3 : <1 SiO 2 : <1 |
RT-900 900–1500 1500 1500-RT |
22 11 0 |
00:40 00:55 02:25 Uncontrolled |
Copran Monolith COP |
IM2630A2 | White Peaks; Essen, Germany |
ZrO 2 : 94.02–94.75 Y 2 O 3 : 4.88–5.55 Al 2 O 3 : 0.03–0.07 Fe 2 O 3 : 0–0.06 Er 3 O 3 : 0–0.05 CO 2 O 4 : 0–0.0016 other oxides: 0–0.02 |
RT-950 950–1500 1500 1500-RT |
10 6 0 |
01:30 01:32 01:30 Uncontrolled |
DD Bio ZX 2 DDB |
6161725010 | Dental Direkt; Spenge, Germany |
ZrO 2 + HfO 2 + Y 2 O 3 : >99 Y 2 O 3 : <6 Al 2 O 3 : <0.5 other oxides: <0.25 |
RT-900 900 900–1450 1450 1450–200 200-RT |
8 0 3 0 10 |
01:50 00:30 03:00 02:00 02:05 Uncontrolled |
NexxZr T NEX |
TAAFQJ | Sagemax Bioceramics; Federal Way, WA, USA |
ZrO 2 + HfO 2 + Y 2 O 3 : >99.5 ZrO 2 : 91.6 Y 2 O 3 : 5 HfO 2 : 3 Al 2 O 3 : <0.15 other oxides: <0.2 |
RT-900 900 900–1540 1540 1540–80 80-RT |
10 0 3 0 8 |
01:26 00:10 03:33 02:30 03:02 Uncontrolled |
Zirlux 16+ ZIR |
808325-338 | Henry Schein; Melville, NY, USA |
ZrO 2 : ≥98 Fe 2 O 3 : ≥0.3 Pr 2 O 3 : ≤0.2 Er 2 O 3 : ≤1 other oxides: 0.5 |
RT-1200 1200 1200–1300 1300–1530 1530 1530–800 800-RT |
8 0 2 4 0 8 |
02:25 00:30 00:50 00:58 02:00 01:31 Uncontrolled |
For translucency (T) measurements round zirconia specimens (diameter: 16 mm, final thickness: 1 ± 0.05 mm; N = 84, n = 12/zirconia material) were fabricated. The polishing process was made in several steps with polishing pads (40–1 μm) in combination with diamond (Struers, Ballerup, Denmark). Specimens were cleaned (80% alcohol, Alkopharm 80) and translucency was measured at room temperature (23 °C) in dry and dimmed ambience. Each specimen was run through a spectrum of light in the range of a wavelength between 400 and 700 nm. Translucency was calculated by the intensity of the monochromatic light I 0 , and the light I , transmitted through the specimen. The transmission coefficient t c (%) was calculated using following equation: <SPAN role=presentation tabIndex=0 id=MathJax-Element-1-Frame class=MathJax style="POSITION: relative" data-mathml='I/I0=tcx’>?/?0=???I/I0=tcx
I / I 0 = t c x
. The overall light transmission T for each specimen was calculated as the integration ( t c ( λ ) dλ ). To receive light transmission in %, the T value of each specimen group was absorbed with the T value of the blank specimen holder (baseline).
Biaxial flexural strength (FS) was tested using for the translucency measurements fabricated specimens ( N = 84, n = 12/zirconia material) according to DIN EN ISO 6872-2015 with a test apparatus with three tempered steel balls with a diameter of 3.2 mm, that were arranged in an equilateral triangle with a lateral length of 10 mm and the ball support circle was 120°. The specimen was positioned centrally on the steel balls and loaded with a plunger with a diameter of 1.4 mm at a crosshead speed of 1 mm/min until fracture. The biaxial flexural strength was calculated:
σ=−0.25N(X−Y)/d2
with σ : flexural strength (N/mm 2 ); N : fracture load (N) and d : thickness of the specimen (mm); coefficients X and Y with:
X=(1+ϑ)ln[(r2/r3)]2+[(1−ϑ)/2](r2/r3)2
Y=(1+ϑ)[1+ln(r1/r3)]2+(1−ϑ)(r2/r3)2
with <SPAN role=presentation tabIndex=0 id=MathJax-Element-5-Frame class=MathJax style="POSITION: relative" data-mathml='ϑ’>?ϑ
ϑ
: Poisson’s ratio (0.25) ; r 1: (mean) support contact diameter (mm); r 2: (mean) loaded contact diameter (mm); r 3: diameter of the specimen (mm)
For Chevron-Notch Beam (CNB) fracture toughness (K IC ) measurements bar-shaped zirconia specimens (3.0 ± 0.2 mm × 4.0 ± 0.2 mm × 45.0 mm) were fabricated ( N = 84, n = 12/zirconia material). The notch was prepared according to the guidelines specified in DIN EN 14425-3 and ISO 24370. For this, specimens were singly placed and fixed in an adjusted specimen holder for a universal cutting machine (Secotom-50; Struers, Ballerup, Denmark) providing an angle of 26° between two coplanar cuts for the notch. The two coplanar cuts were inserted successively centered using a diamond cut-off wheel (150 μm, M0D08, Ballerup, Struers) at a displacement speed of 0.05 mm/min, a speed rotation of 5,000 rpm and a cutting length of 15 mm. After ultrasonic cleaning in distilled water, the inserted notch dimensions were microscopically checked for validity as specified in ISO 24370 (Zwick/Roell Z 2.5, Zwick, Ulm, Germany). To provide an inert environment during fracture toughness measurements silicon oil (Ballistol, F.W. Klever, Aham, Germany) was applied in the notch. Specimens and silicone oil were separately heated at 110 °C for 1 h, subsequently the specimen was covered with silicone oil. Before K IC measurements, each specimen was centrally placed in the specimen holder for 4-point flexural strength measurements with the notch pointing upward. Each specimen was loaded three times. After turning the specimen so that the notch pointed downward, the flexural strength was measured at a crosshead speed of 0.05 mm/min in the displacement-controlled mode until fracture. The force-displacement curves were analyzed, and measurements were evaluated as valid when a stable crack growth was identified as specified in DIN EN 14425-3 and ISO 24370. For all valid measurements, fracture toughness was calculated using following equation:
KIC=F(s1−s2)/bw3/2⋅Ymin*/1000
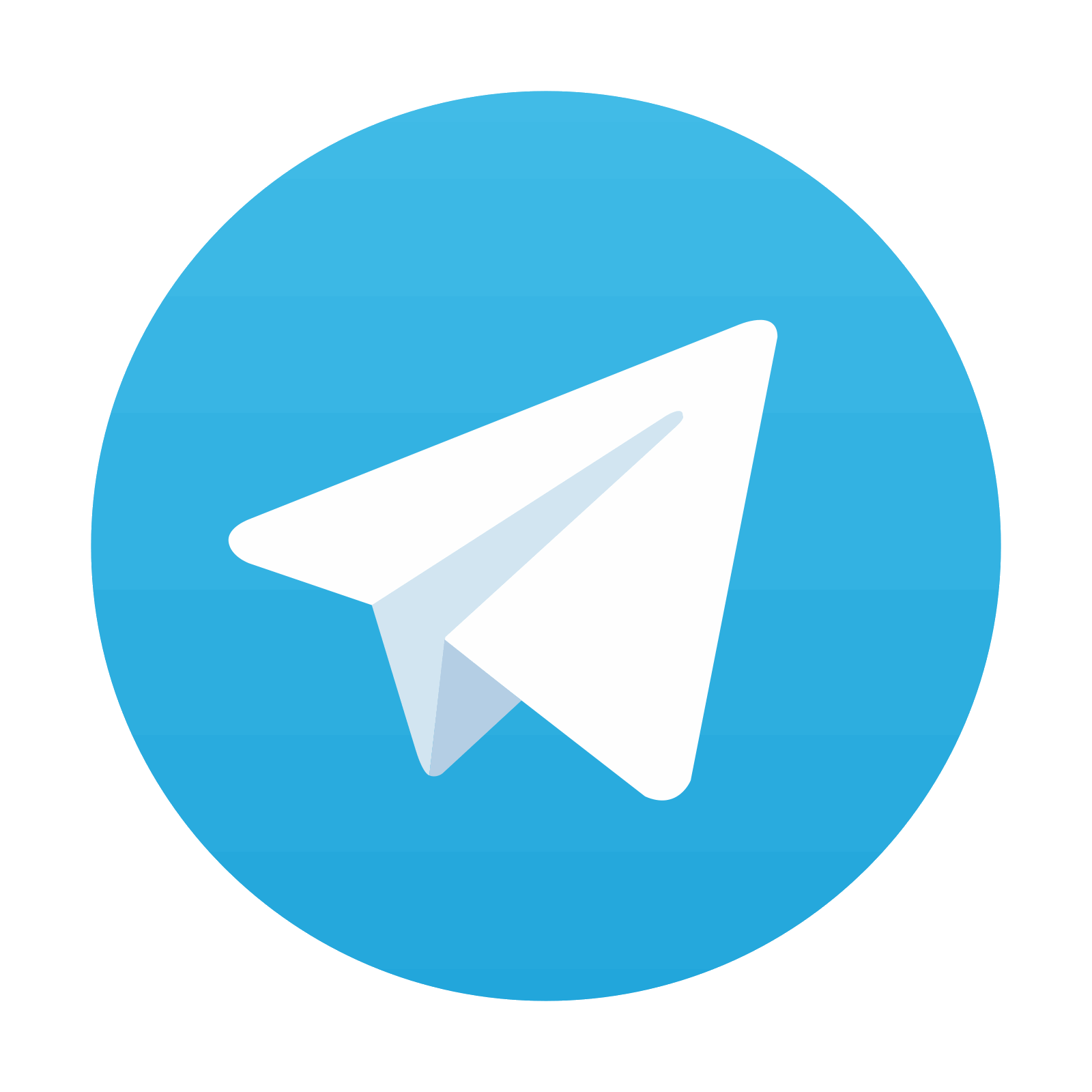
Stay updated, free dental videos. Join our Telegram channel

VIDEdental - Online dental courses
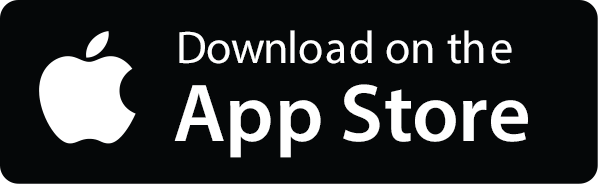

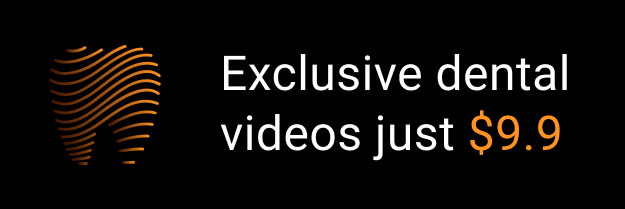