Highlights
- •
Similar primary zirconia properties by speed-sintering as conventional sintering.
- •
Speed-sintering 3Y-TZP decreased its translucency but not that of 5Y-PSZ.
- •
Speed-sintering lowered the mechanical reliability of 3Y-TZP and 5Y-PSZ zirconia.
Abstract
Objective
To evaluate the performance of zirconia ceramics sintered in a speed sintering induction furnace by comprehensive understanding of their optical and mechanical properties, microstructure, phase composition and aging stability, in comparison to ceramics sintered in a conventional furnace.
Methods
Speed sintered (SS) Katana STML SS (Kuraray Noritake) (total thermal cycle/sintering time/dwell temperature: 30 min/16 min/1560 °C) and CEREC Zirconia (CEREC Zr SS ) (Dentsply Sirona) (15 min/2 min/1578 °C) were compared to conventionally sintered (CS) Katana STML CS (6.8 h/2 h/1550 °C) and inCoris TZI CS (4 h/2 h/1510 °C). The translucency parameter (TP) and contrast ratio (CR) were measured with a spectrophotometer. The chemical composition of the materials was determined by XRF and phase composition was characterized using XRD. Hydrothermal aging behavior was evaluated by measuring the tetragonal-to-monoclinic ZrO 2 phase transformation after accelerated hydrothermal aging in steam at 134 °C. The indentation fracture toughness, Vickers hardness and biaxial strength of the sintered ceramics were assessed.
Results
Speed and conventionally sintered zirconia revealed similar density, microstructure, average strength and hydrothermal aging stability. Both Katana STML SS/CS 5Y-PSZ ceramics were characterized with a higher content of cubic phase (≈53 wt%), which resulted in a higher amount of Y 2 O 3 in the remaining tetragonal ZrO 2 phases compared to the 3Y-TZP CEREC Zr SS and inCoris TZI CS (8 and 20 wt%, respectively). The sintering program did not affect the hydrothermal aging behavior of Katana STML SS and CEREC Zr SS . TP of Katana STML SS (TP ≈ 32) was not affected by speed sintering, while the translucency of CEREC Zr SS (TP = 14) was significantly reduced. Hardness, fracture toughness and Weibull characteristic strength of Katana STML SS and CEREC Zr SS also reached the optimal level, but speed sintering substantially lowered their mechanical reliability.
Significance
Speed sintering of 3Y-TZP and 5Y-PSZ in a speed sintering induction oven appeared suitable for clinical applications. However, further studies should focus on improving of translucency and mechanical reliability of the speed-sintered zirconia ceramics.
1
Introduction
In the last decade, computer-aided design/computer-aided manufacturing (CAD/CAM) systems have transformed the fabrication of dental restorations in both dental laboratories and clinics . Three different CAD/CAM approaches have been developed and introduced: (1) in office or so-called ‘chairside’, (2) in-lab systems and (3) centralized production in milling centers . In contrast to in-lab systems, where the production of the restoration is to some extend related to the dental laboratory, chairside fabrication allows a dentist to complete all the phases of restoration production within one single appointment, completely independent from a dental technician. One of the most popular chairside systems is the CEREC (computer assisted CERamic REConstruction, Dentsply Sirona, Bensheim, Germany) CAD/CAM system, which was introduced to the market in 1985. Even though some researchers have expressed their concern regarding the precision of the CEREC restoration marginal fit in the past, recent studies confirmed that it is possible to produce clinically long lasting restorations after the latest technological CEREC improvements .
So far, different ceramic and non-ceramic materials have become available for chairside CEREC CAD/CAM systems. In particular, esthetic ceramics (feldspatic and leucite reinforced ceramics), polymer-infiltrated ceramics and high-strength ceramics (lithium (di)silicate glass ceramics) or composite resins can be milled efficiently (usually in less than 20 min) in their final structure without any major mechanical damage. This is crucial as only minimal post-milling processing is needed in order to complete the restoration. The fabrication process has thus been substantially shortened, so the final restoration can be fabricated and cemented in only one appointment. However, zirconia ceramics have always been a chairside CAD/CAM issue. Zirconia restorations could be CAM fabricated either by hard machining of a fully sintered zirconia block or by soft machining of a partially sintered zirconia block . Hard milling of fully sintered zirconia is rather difficult and expensive due to its high strength and hardness, and longer milling times, which cause a significantly faster wear of the milling tools. For this reason, zirconia blocks are normally milled in the pre-sintered porous form by so-called soft machining. The milled restorations have to be additionally sintered to achieve full density, which usually takes 6–8 h including heating, cooling and dwell time; this thermal process normally takes place overnight.
The recent introduction of speed-sintering furnaces and the development of novel speed-sintering protocols have substantially shortened the sintering time of zirconia ceramics (from 6 h up to 10 min) allowing the fabrication of zirconia restorations in only one visit. Such speed-sintering furnace (SpeedFire, Dentsply Sirona) was introduced to the market 2 years ago and has gained a high popularity among dentists in a short period. In comparison with conventional sintering furnaces, where heat is generated by electrical resistive heating elements, a SpeedFire furnace generates heat by electromagnetic induction . In brief, an induction heating coil surrounds a susceptor body, which in turn surrounds the pre-sintered zirconia ceramics. The induction coil emanates a fluctuating induced magnetic field, which generates heat in the electroconductive susceptor body, usually composed of zirconium or graphite. More information is provided elsewhere . This induction sintering method is considered to be beneficial compared to conventional sintering as high temperatures can be achieved extremely fast. The most advanced conventional sintering furnaces in air can achieve maximum heating rates of 40–70 °C/min up to maximum 1800 °C using MoSi 2 heating elements .
At the same time, the popularity of zirconia-based restorations have been rapidly increased among dentists due to their superior biocompatibility, favorable mechanical properties and promising esthetic potential . Specifically, biomedical grade 3 mol% yttria-stabilized tetragonal zirconia (3Y-TZP) is used in dentistry for fabricating dental crowns and fixed partial dentures. Since it is characterized by a high strength (≈1000 MPa), it is considered a material of choice for the fabrication of long-span fixed dental prosthesis (FDP). However, the main drawback of 3Y-TZP ceramics is its high opacity, especially when placing anterior restorations next to natural teeth. One way to improve the esthetic appearance of zirconia ceramics and to mimic optical properties of natural tooth enamel is to cover the opaque zirconia with high-translucent porcelain veneering. The brittle nature of porcelain however frequently caused chipping or delamination from the zirconia framework . For that reason, there is a clear trend toward monolithic zirconia restorations that could solve the problem of chipping and additionally avoid excessive tooth preparation inevitable for placement of bi-layered zirconia ceramics. Different approaches were proposed to improve the translucency. Zirconia materials with a higher Y 2 O 3 content (>4 mol%) successfully increased the translucency but lowered the mechanical properties due to a reduction or absence of transformation toughening, restricting the usage of these materials to low stress-bearing areas.
Sintering of zirconia is considered to be a critical step in ceramic processing and has been a focus of interest of many researchers . Previous research has already shown that changes in the sintering procedure directly influence the density and microstructure, including grain size and phase composition, which that can reflect on the mechanical and optical properties of zirconia ceramics . Conventional sintering of Y-TZP ceramics usually includes slow and stable heating and cooling rates (up to 20 °C/min) to a sintering temperature of 1400–1500 °C which lasts for a couple of hours of dwell time . On the other hand, speed sintering has been proposed as a potential strategy to obtain a finer microstructure by preventing grain growth by applying a fast heating rate while maintaining a high material density . A recent study reported that an increased sintering temperature in combination with a decreased sintering time indeed yielded a smaller grain size and higher translucency . In a different study where the samples were fast sintered by putting them in a pre-heated furnace at 1580 °C for 10 min, the flexural strength of zirconia ceramics was significantly improved . So far, the main reported drawbacks of conventional rapid sintering are correlated with inhomogeneous densification or so-called shell densification of 3Y-TZP, which can have a negative impact on the microstructure of ceramics, consequently causing mechanical defects and lowering its mechanical and optical properties .
In this respect, it has also been reported that an uneven low radial density distribution caused by a combination of cold isostatic powder compaction and non-optimized sintering protocol, can increase the hydrothermal aging susceptibility of 3Y-TZP ceramics . Namely, in between 1999 and 2001, hundreds of zirconia femoral heads suffered from a catastrophic failure which led to their sale suspension and withdrawal from the market . Subsequently, the femoral heads were subjected to a thorough examination revealing that the applied thermal sintering cycle of the ball-heads resulted in the presence of residual stresses and an uneven radial core density. This consequently lead to the unexpected rapid aging rate and the growth of aging-induced defects in the region of maximum tensile loading .
To the best of the authors’ knowledge, a detailed evaluation of zirconia ceramics sintered in a CEREC SpeedFire (Dentsply Sirona) furnace is still missing. Therefore, the main objective of this study was to evaluate the performance of speed-sintered commercially available monolithic zirconia. The null hypothesis to be tested was that speed sintering would not affect the mechanical properties, microstructure, optical properties and aging behavior of monolithic dental zirconia.
2
Materials & methods
2.1
Experimental materials and specimen preparation
Four commercial pre-sintered zirconia ceramics, of which two grades were indicated to be sintered conventionally (“CS”; Katana STML, Kuraray Noritake, Tokyo, Japan and inCoris TZI, Dentsply Sirona, York, PA, USA) and two additional grades (“SS”; Katana STML, 12Z, Kuraray Noritake, Tokyo, Japan and CEREC Zirconia medi S, Dentsply Sirona, York, PA, USA) following a speed-sintering protocol, were cut into plates with dimensions of approximate 15 × 15 × 3.5 mm. Katana STML SS and CEREC Zr SS samples were subsequently sintered in a SpeedFire furnace (Dentsply Sirona, York, USA) following the sintering program provided by the furnace manufacturer ( Fig. 2 ). The total sintering time for Katana STML SS was 28 min and heating was done in 3-steps: (1) 350 °C/min up to 1300 °C; (2) 150 °C/min up to 1500 °C; (3) 10 °C/min up to 1560 °C. The dwell time at 1560 °C lasted for 16 min, after which the samples were cooled at 170 °C/min to 1200 °C in a closed furnace and at 480 °C/min to room temperature by opening the furnace. The sintering program for CEREC Zr SS started with a heating rate of 330 °C/min up to 1050 °C and continued with the rate of 150 °C/min until the sintering temperature of 1580 °C. After 3 min dwell at 1580 °C, the samples were cooled down at 175 °C/min to 1200 °C and at 400 °C/min to room temperature. On the other hand, Katana STML CS (total sintering time: 6.8 h; dwell time: 2 h at 1550 °C) and inCoris TZI CS (total sintering time: 4 h; dwell time: 2 h at 1510 °C), indicated only for conventional sintering, were sintered in a conventional furnace (Nabertherm, Lilienthal, Germany), following the instructions of the respective material manufacturers. Details on the thermal cycles are provided in Fig. 2 . Both Katana STML CS and Katana STML SS are multilayered, while CEREC Zr SS and inCoris TZI CS are monolayer materials with the same A2 color grade.
The sintered materials were ground parallel and gradually polished down to 1 μm with diamond suspensions and with colloidal silica until a mirror surface was achieved. The final sample size was 12 × 12 × 0.5 mm for evaluating density, microstructure, optical properties and hydrothermal aging, and 12 × 12 × 1.2 mm for analyzing biaxial flexural strength, hardness and toughness ( Fig. 1 ).


2.2
Chemical, phase and microstructural characterization
The chemical composition of the zirconia grades was evaluated by wavelength dispersive X-ray fluorescence spectroscopy (WD-XRF; Bruker S8 Tiger, Germany) using a 4 kW X-ray tube. The raw data of the chemical composition of the sample were automatically provided using Quant-Express software (Bruker, Karlsruhe, Germany).
The density of the sinteredf ceramics ( n = 6) was determined according to the Archimedes principle in ethanol.
Phase identification was performed by X-ray diffraction (XRD; 3003 T/T, Seifert, Ahrensburg, Germany). Mirror-polished surfaces of each material were scanned using Cu K α (40 kV, 40 mA) from 20 to 90° (2 θ ) with the step size of 0.01° for 3 s. Rietveld analysis was used to assess the phase composition and lattice parameters using TOPAS academic V5 software (BRUKER AXS, Karlsruhe, Germany). The Y 2 O 3 content in the tetragonal ZrO 2 phase was calculated based on the a and c unit cell parameter of the tetragonal ZrO 2 phase, as explained by Yamashita et al. and Gibson et al. .
The microstructure of the ceramics zirconia was characterized using scanning electron microscopy (SEM; Philips XL-30 FEG, Eindhoven, The Netherlands). Prior to analysis, the samples were mirror polished and thermally etched (1250 °C) to reveal the grain boundary network and Pt coated. Secondary electron (SE) images were acquired at 10 −5 mbar pressure, an acceleration voltage of 10 kV and 144 μA beam current. The zirconia grain size of at least 1000 grains was measured on SE micrographs using Image-Pro PLUS 6.0 software (Media Cybernetics, Rockville Pike, USA) according to the linear intercept method . The average grain size with standard deviation and grain-size distributions were reported without any corrections.
2.3
Low-temperature degradation
In vitro hydrothermal aging was performed following ISO standard 13356. Double-sided mirror-polished specimens were autoclaved at 134 °C and 2 bar in water vapor up to 60 h. The autoclave with specimens was placed in an oil bath in order to obtain an internal temperature of 134 °C. The amount of monoclinic ZrO 2 phase was determined using XRD (Seifert 3003 T/T, Seifert) at 40 kV and 40 mA of Cu-K α radiation. XRD patterns were recorded in the range of 27–33° (2 θ ) in the θ –2 θ mode with a scan speed of 2 s/step and a scan step of 0.02° (the maximum X-ray penetration depth was calculated to be 7.5 μm (Cu K α with 98% absorption)). The surface monoclinic phase ( V m ) content was calculated using the formula of Garvie et al. and Toraya :
Vm=1.311×(Im−111+Im111)1.311×(Im−111+Im111)It101
with I representing the intensity of monoclinic (−111 and 111) and tetragonal (101) phase peaks indicated by the subscripts m and t . For each curve, two specimens (four exposed surfaces) were evaluated and the average value was reported.
2.4
Optical property characterization
The translucency of the ceramics was measured on a double-sided mirror-polished plate specimens ( n = 7, thickness = 0.5 mm) using a spectrophotometer (SpectroShadeTM MICRO, MHT Optic Research, Niederhasli, Switzerland) before and after 60 h of hydrothermal aging. Lithium-(di)silicate glass-ceramic (LS 2 ) samples ( n = 7, thickness = 0.5 mm) were fabricated from IPS e.max CAD HT block (Ivoclar Vivadent, Schaan, Liechtenstein; “HT” = high translucency) as translucency reference control. The spectrometer was used to record the CIELAB coordinates ( L *, a * and b *) from the specimens positioned on a black and white background. A thin layer of vaseline was put in-between specimen and background for better optical contact. The translucency parameter (TP) was calculated according to:
TP=(LB*−LW*)2+(aB*−aW*)2+(bB*−bW*)2
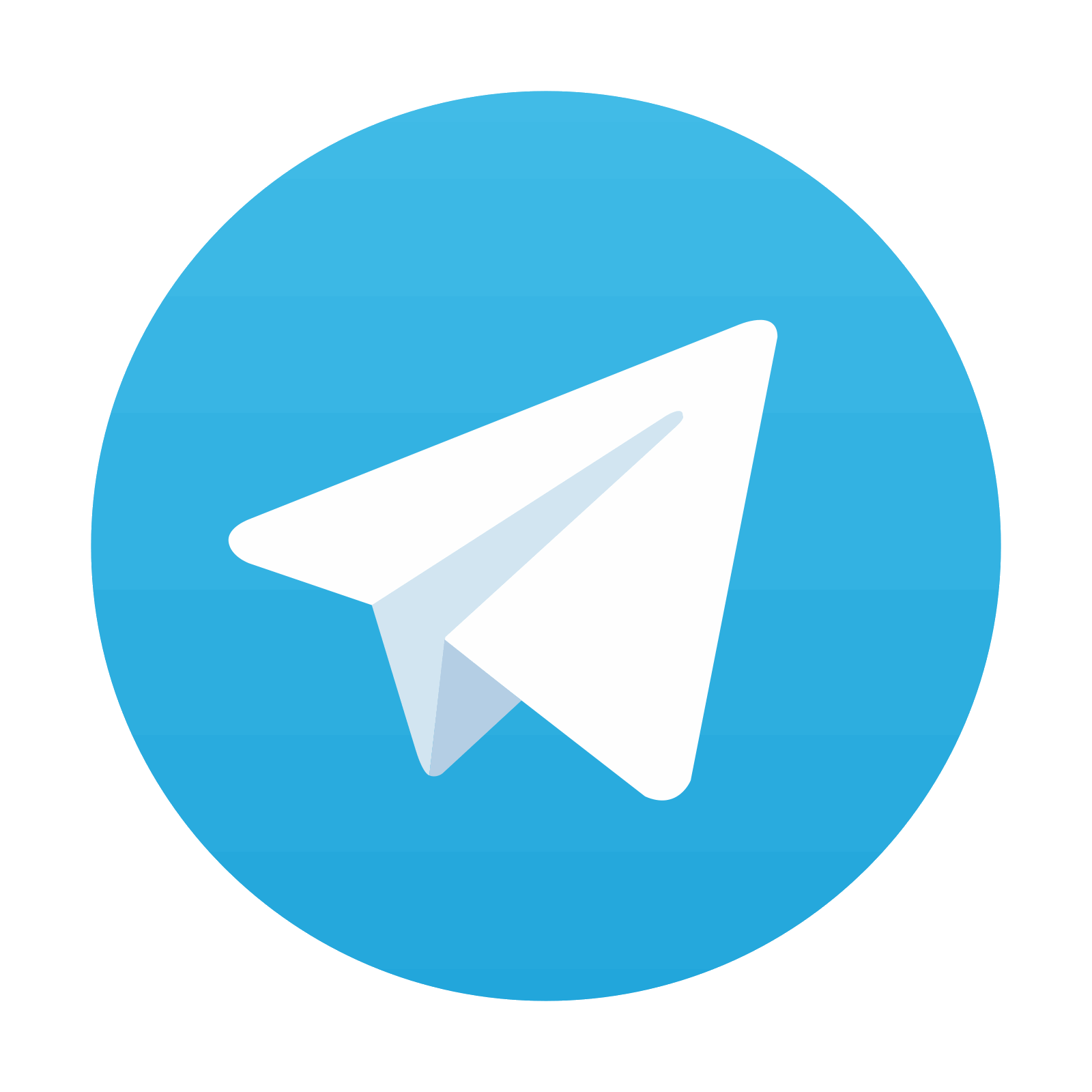
Stay updated, free dental videos. Join our Telegram channel

VIDEdental - Online dental courses
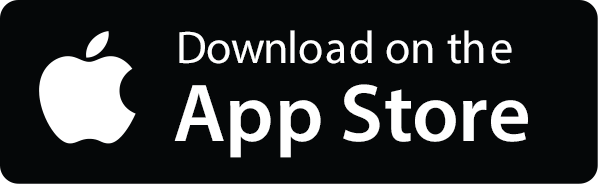

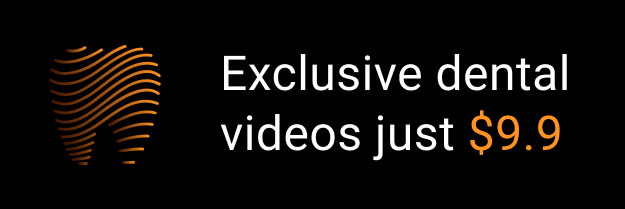