Fig. 5.1
Image by transmission electronic microscope of the sintering process involving hydroxyapatite particles
The firing of porcelain promotes physical–chemical reactions responsible for the final properties of the ceramic products. In this process, it must be considered the kinetic limitations, the development of the phases, and the complexities of the microstructure. Generally, all the steps, since raw material preparation, drying conditions and firing cycle are going to have a strong influence in the product qualities. The firing cycle influence is related to the kind of furnace, firing atmosphere, maximum temperature and soaking time. All these parameters are related to quality and cost of the products.
The sintering mechanism comprises three stages: the initial, intermediate and late phase. Figure 5.2 presents schematically the sintering process stages.
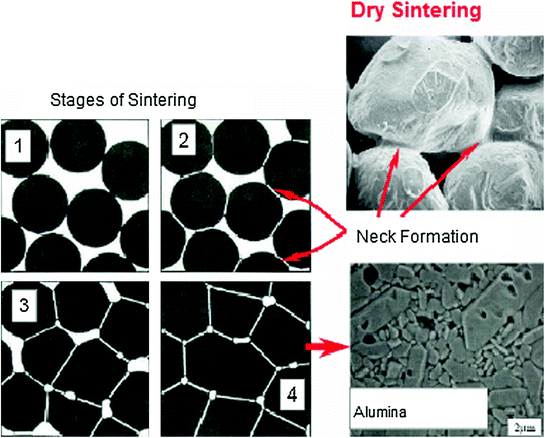
Fig. 5.2
Sintering process stages (dry sintering)
In the initial phase, the process of sintering involves little or no densification and shrinkage and is mainly characterized by the formation of a “neck” between neighboring particles and by the decrease in surface area. In this phase, pore geometry is open and interconnected. The growth of these contact areas (neck) is responsible for changes in material properties associated with sintering.
The intermediate phase is characterized by regular and continuous pores with interconnected cylindrical structure. At this stage, the theoretical density is between 70 and 92 %, the sintering rate decreases and is very sensitive to the morphology of the pore-grain boundary region.
In the last stage of sintering, the pores are closed and spherical and grain growth is evident. The pores gradually decrease by diffusion to the grain boundary region. This densification is sensitive to grain size and the connection of pores to the grain boundary.
The sintering process is a thermally activated process. The energy required to do so is closely correlated with the diffusion mechanisms, such as the diffusion in the grain boundary. Densification can occur with the superposition of external loads combined with sintering, as occurs in pressure assisted sintering.
The transport mechanisms by which mass movement occurs can be of 2 types: by surface transportation or by material volume (bulk). The first process involves neck growth without densification and the second occurs through contraction and includes various types of diffusion, such as volume and grain boundary diffusion. During sintering, bulk transport changes the space between the particles with the growth of contact area between the grains, increasing the density and strength of the material. Sintering is more intense at higher temperatures due to the increase in active atoms and available sites.
During sintering, interaction between the pores and grain boundaries can occur in three ways: (1) the pores can slow down grain growth, (2) the pores can be moved to the grain boundary region during grain growth; and (3) the grain boundary region can move away from the pores, leaving them isolated within the grain, which lowers density. It is important to avoid this last scenario by combining small grains and pores and increasing the rate of movement of the grain boundary. Another approach to reducing pores is the elimination of gases (vacuum sintering).
The interrelationship between microstructure and sintering variables such as temperature, heating rate, sintering additives and atmosphere has been demonstrated by several authors (Kovar et al. 2000; Lawn et al. 1993 and Oh et al. 2002). For many applications, where the goal is maximizing mechanical strength, optimum sintering corresponds to maximum densification with minimal grain growth. For this to occur, as a first requirement the grain size of raw material needs to be reduced.
The sintering process performed in conventional electric ovens results in intensive grain growth, resulting in a coarse grain microstructure. Incomplete sintering leaves the material porous and recommend increasing the sintering temperature to 1,780 °C. Large pores migrate rapidly during sintering, collapsing in the grain boundaries. Small pores, however, stay trapped within the matrix. The consequence of rapid consolidation is that gas cannot migrate to the surface of the material, staying within the materials mass. The excessive presence of porosity may therefore be due to an inadequate sintering process.
It is noted that in the presence of high porosity, defects appear to be interconnected pores and their size appears to be greater at the beginning of sintering. These authors suggest a longer sintering process. The pores appear as a result of trapped gasses from organic compounds used as compression additives.
Chinelatto et al. (2008) cite several ways to control the sintering process, obtaining ceramic materials of high density and with small grains. German (1996) indicates that controlling the heating curve is a simple and economically viable way of manipulating the microstructure. Ideally, this control is done by determining the temperature, which allows for a better rate of densification.
Chen and Wang (2000) have developed an effective method of Y2O3 sintering by heating in two steps. In the first step, the material is heated at a very high temperature (T1) and then rapidly cooled to a lower temperature (T2) for a long period of time, reducing grain growth in the final stages of sintering and obtaining high densification. Wang et al. (2009) also recommend this technique for alumina, where T1 was performed between 1,400 and 1,450 °C (allowing a high rate of densification) and T2 between 1,350 and 1,400 °C for an extended period, but not longer than 24 h (avoiding surface diffusion and maintaining densification). The authors state that this sintering technique generates a density above 99 % and controlled grain size in alumina.
Han et al. (2008 ) have also investigated alumina concerning the relation between the increase of sintering temperature and the decrease in porosity by the rise in densification. When temperature was increased from 1,400 to 1,500 °C, porosity fell by almost 3 % and resistance doubled. Between 1,500 and 1,550 °C, there was little change in porosity, but the grains grew and had greater contact with each other, further improving the mechanical strength. These authors demonstrate, however, that too elevated temperatures (1,600 °C) leads to the excessive growth of some grains in comparison to others, leading to a reduction in mechanical strength.
To improve the properties of a material it is often necessary to increase its densification through phase stabilization (the use of another phase to prevent grain growth); active sintering (the use of an additive to increase bulk transport); reactive sintering (the use of additives to prevent loss of stoichiometry), and through liquid phase sintering.
Hence, the sintering process can be improved with sintering additives, which are used to stabilize desired crystalline structures or to form a liquid phase to assist in the increase of densification. In this sense, a glassy phase can be a sintering additive. In fact, the sintering process in presence of a glass (liquid phase sintering) can occur at lower temperature in comparison of dry sintering (sintering process without a glassy phase). Figure 5.3 presents schematically the stages of a liquid phase sintering process.
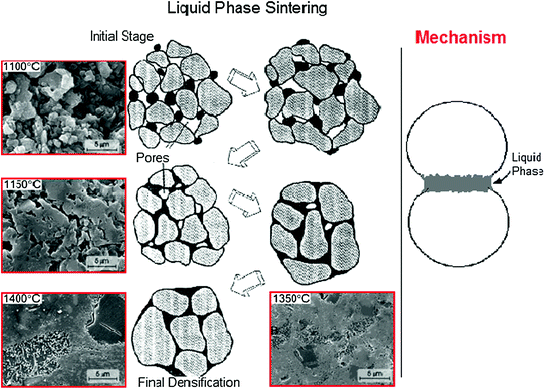
Fig. 5.3
Stages of a liquid phase sintering process
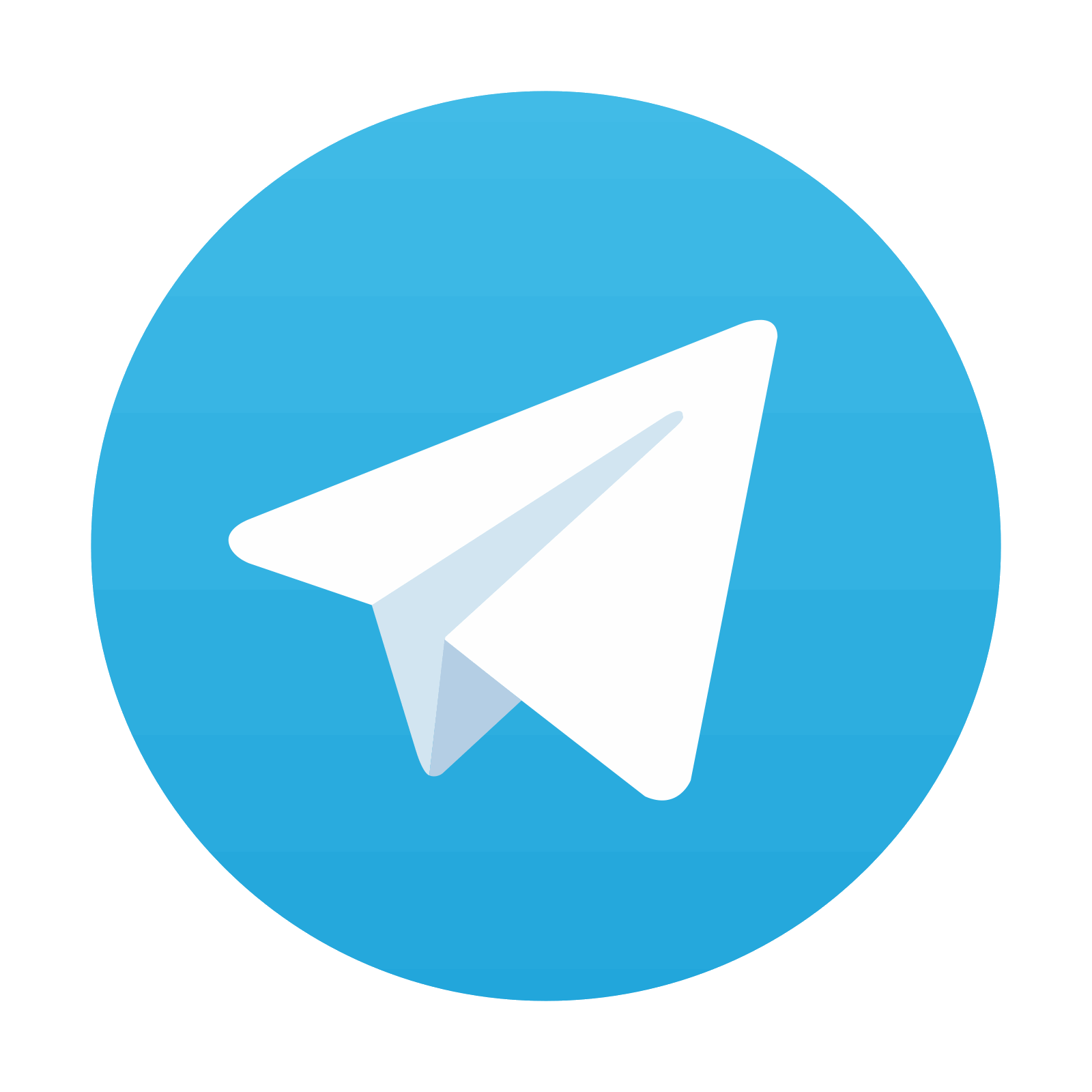
Stay updated, free dental videos. Join our Telegram channel

VIDEdental - Online dental courses
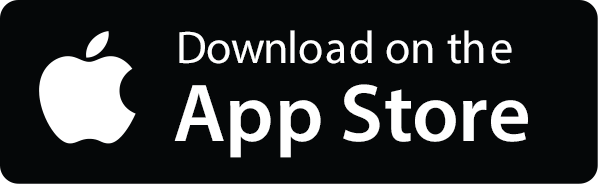
