Fig. 8.1
Mechanical resistance of alumina and alumina-feldspar ceramic bodies sintered at different temperatures when exposed (b) or not to acetic acid (a)
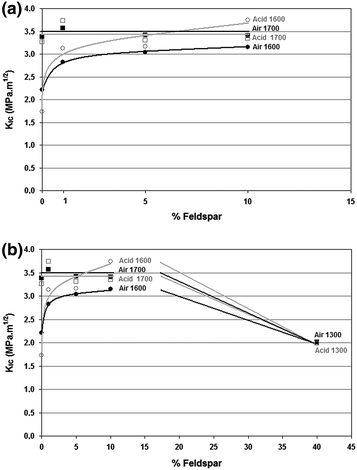
Fig. 8.2
Fracture resistance of alumina and alumina-feldspar ceramic bodies sintered at different temperatures when exposed (b) or not to acetic acid (a)
The results of Stumpf et al. (2010) investigation indicate that for these ceramic bodies, at a temperature of 1,700 °C sintering is nearly complete, with or without the addition of feldspar. In samples sintered at 1,600 °C it was possible to observe that the mechanical strength increases with the addition of feldspar. In these ceramic bodies such a small amount of glassy phase (between 5 and 10 %) is beneficial, since it can reduce the porosity and increase the density in ceramic bodies sintered at lower temperatures. The addition of feldspar in small amounts increases the mechanical strength of ceramic bodies heated at 1,600 °C, through the higher densification arising from more intense sintering.
In fact, the addition of feldspar to alumina acts as a glassy phase former in the sintering process. The presence of silicates in feldspar promotes a liquid phase that surrounds the alumina grains. The addition of this phase increases the rate of densification of ceramic bodies. In both cases, the surface area is effective in promoting greater contact and in intensifying the sintering phenomenon (by its effective further reduction). These phenomena lead to higher densification of ceramic bodies.
It is clear that when 40 % of feldspar is added, fracture toughness (K IC ) tends to decrease in both groups (exposed or not to acetic acid). This is probably because the amount of feldspar forms glassy phase in excess. The K IC values were lower for samples sintered at 1,600 °C. At this temperature, the highest value obtained for fracture toughness occurred in samples with 10 % feldspar. This way, at 1,600 °C K IC increased linearly with the addition of feldspar from 0 to 10 %. This behavior shows that sintering is incomplete at the temperature of 1,600 °C in the absence of feldspar. The addition of 10 % feldspar enables liquid phase sintering, increasing the values of K IC .
The variations in the K IC confirm that the presence of a small amount of feldspar contributes to increase the densification of the material, when lower firing temperatures are used. Several authors agree that the grain boundary region can determine the behavior of ceramic materials and that therefore the control of this region is critical.
K IC has a specific value for a given material. For alumina, this value is around 3.5 MP a.m1/2 (Matasa 1999). K IC values obtained for the investigated ceramic samples validate the assumption that the presence of a small amount of glassy phase improves the sintering process of alumina based ceramics, through greater densification.
On the other hand, the results obtained by Stumpf et al. (2010) also confirm that an excessive amount of glassy phase causes a decrease of K IC . The addition of glassy phase above this value increases the area of “vitreous cavities” that form in the contact area between three and four grains of the crystalline phase, while the film of the glassy phase that occurs between two grains does not increase much. The increase in the area of the “vitreous cavities” may therefore be a factor for reducing mechanical strength since it is a phase with lower mechanical strength (Fig. 8.3).
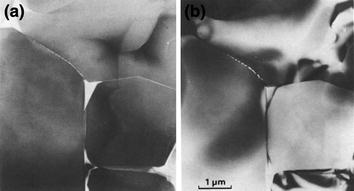
Fig. 8.3
Vitrous phase accumulation in the grain’s boundary area of alumina. Diffuse dark-field (a) and bright-field (b) transmission electron micrographs illustrating the continuous, inter-granular nature of the glass phase along the two-grain and three-grain junctions of the alumina phase. The glass phase, appearing bright in the diffuse dark-field image, is concentrated at the three-grain junctions (Clarke 1985)
K IC value increases after exposure to acetic acid in ceramic bodies sintered at 1,600 °C. This effect, however, did not occur in the samples fired at higher temperatures. Jestel et al. (1998) also report that when testing a feldspathic dental ceramic (Duceram® LFC, Ducera Dental,) its mechanical strength improved after exposure to a solution of 4 % acetic acid for 16 h. The authors attributed this effect to an ion exchange mechanism that modified the surface structure.
According to Roman et al. (2008), the existence of a second phase in alumina influences the mechanical behavior of the material.
Acetic acid also had a very interesting effect on fracture toughness in samples with no feldspar, acetic acid reduced K IC . This effect was also observed by Barinov et al. (1998) when comparing the mechanical strength of high purity alumina (99.5 %) and alumina with the addition of glassy phase exposed to an acidic medium (hydrochloric acid and citric acid). The authors attributed the results to the low corrosion resistance in the alumina grain boundary region.
Moreover, Stumpf et al. (2010) reported that the chemical elements that were most attacked by acetic acid, were silicon and aluminum. The chemical element that was least attacked, regardless of firing temperature, was iron. In general it is also possible to observe that the test samples sintered at 1,700 °C were attacked less than the ceramic bodies sintered at 1,600 °C, demonstrating that greater densification of these ceramic bodies improves their resistance in harsh environments.
Stumpf et al. (2010) also reported that the alumina and alumina-feldspar bodies fired at lower temperatures are less dense and have a higher degree of porosity, in accord with the literature concerning the quality of the ceramic sintering process. In the same study, Stumpf et al. reported that in the ceramic bodies sintered at 1,600 °C it was possible to verify that the amount of porosity was lower in those ceramic bodies with more than 5 % of glassy phase. This behavior can be explained by the ease of sintering when there is a glassy phase present.
Cerecedo et al. (2005) have reported a similar effect in alumina ceramic bodies sintered at 1,650 °C for 6 h. The increase in strength with increasing densification reflects better sintering conditions (ASM 1991). The interdependence between the amount of porosity, sintering temperature and mechanical strength has been demonstrated by other authors (HAN et al. 2002).
Kingery (1960) has reported an exponential decrease of mechanical strength in alumina ceramics with an increasing amount of pores in the material. It is possible to observe that the addition of certain amounts of feldspar to alumina is deleterious, since the majority of test samples at the Stumpf et al. (2010) study showed mechanical strengths below the proposed curve (Fig. 8.4).
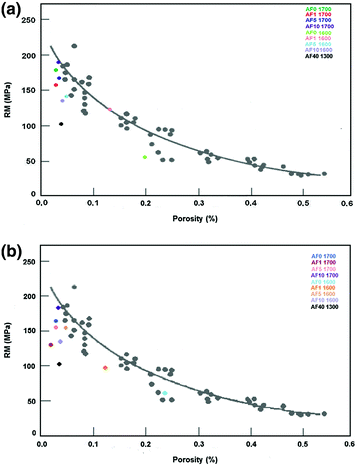
Fig. 8.4
Mechanical resistance and porosity’s comparison in the Kingery’s proposed curve for alumina’s ceramics exposed (b) or not to acetic acid (a)
The influence of feldspar on alumina ceramic bodies is well illustrated by sample with 40 % of feldspar. Although these test samples have low porosity (less than 3 %), their strength is 40 % lower than samples with similar porosity. For the ceramic bodies exposed to acetic acid, the mechanical strength behavior was similar to those samples exposed only to air. The presence of porosity was higher in some groups, especially those fired at 1,600 °C. This could mean that acetic acid can better penetrate the less dense samples, increasing their porosity and reducing flexural strength.
Despite the fact that the increase in porosity was higher after exposure to acetic acid, especially in test samples sintered at lower temperatures, the decrease in strength was greater in the ceramic bodies fired at 1,700 °C. Perhaps the reduction in flexural strength was lower in samples sintered at 1,600 °C, because in these ceramic bodies some larger pore was already the largest defect and the increase in porosity after exposure to acetic acid did not make it more critical as occurred in the samples fired at higher temperatures.
Considering this behavior, it is possible to improve the formulation and firing temperature of ceramics based on the introduction of glassy phase in the microstructure of materials such as orthodontic brackets, restorations and dentures, so that these devices may face the rigors of the oral environment.
Cho et al. (2003) have evaluated the effect of temperature and humidity on alumina in four-point bending tests. The authors tested the effect of temperature variation between 10 and 55 °C and relative humidity between 20 and 80 %. They concluded that the flexural strength of alumina decreases with increasing temperature and humidity. There are few studies, however, on the influence of intra-oral temperature fluctuations on dental ceramics.
The corrosion of stainless steel orthodontic arches, for example, increases in acidic environments. When the bracket with metal channel and orthodontic arch are tested, the movement of both these elements can induce corrosion. Saliva also has a deleterious effect on the sliding performance of the arches on orthodontic braces, since it increases frictional stress.
Saliva is also subject to various pH fluctuations throughout the day, depending on the type of diet and food intake frequency of the patient. Because of this saliva can contain acids from food items, making the intraoral environment more corrosive.
The gastric contents may have a pH lower than 1. This means regurgitation can cause damage to tooth enamel and intraoral ceramic materials. It is important to point out that the presence of braces increases the retention of bacterial plaque and that this change in the quantity and quality of bacterial flora may alter salivary composition. According to Fournier et al. (1998), ceramic brackets favor the accumulation of bacterial plaque.
Patients can also use daily or weekly mouthwashes of fluoride solutions. The use of fluoride is recommended for patients with the incidence or risk of caries. Many dentists recommend regular, preventive use of fluoride solutions throughout treatment, especially for adolescent patients who do not always closely follow hygiene instructions. Daily exposure to fluoride can reduce the incidence of caries and heal existing carious lesions.
Fluoride solutions promote the formation of calcium fluoride globules that adhere to tooth enamel, stimulating its remineralization and protecting it from acid attacks. Fluorides are also present in teas, mineral water and vitamin supplements. According to Giertsenie et al. (1999
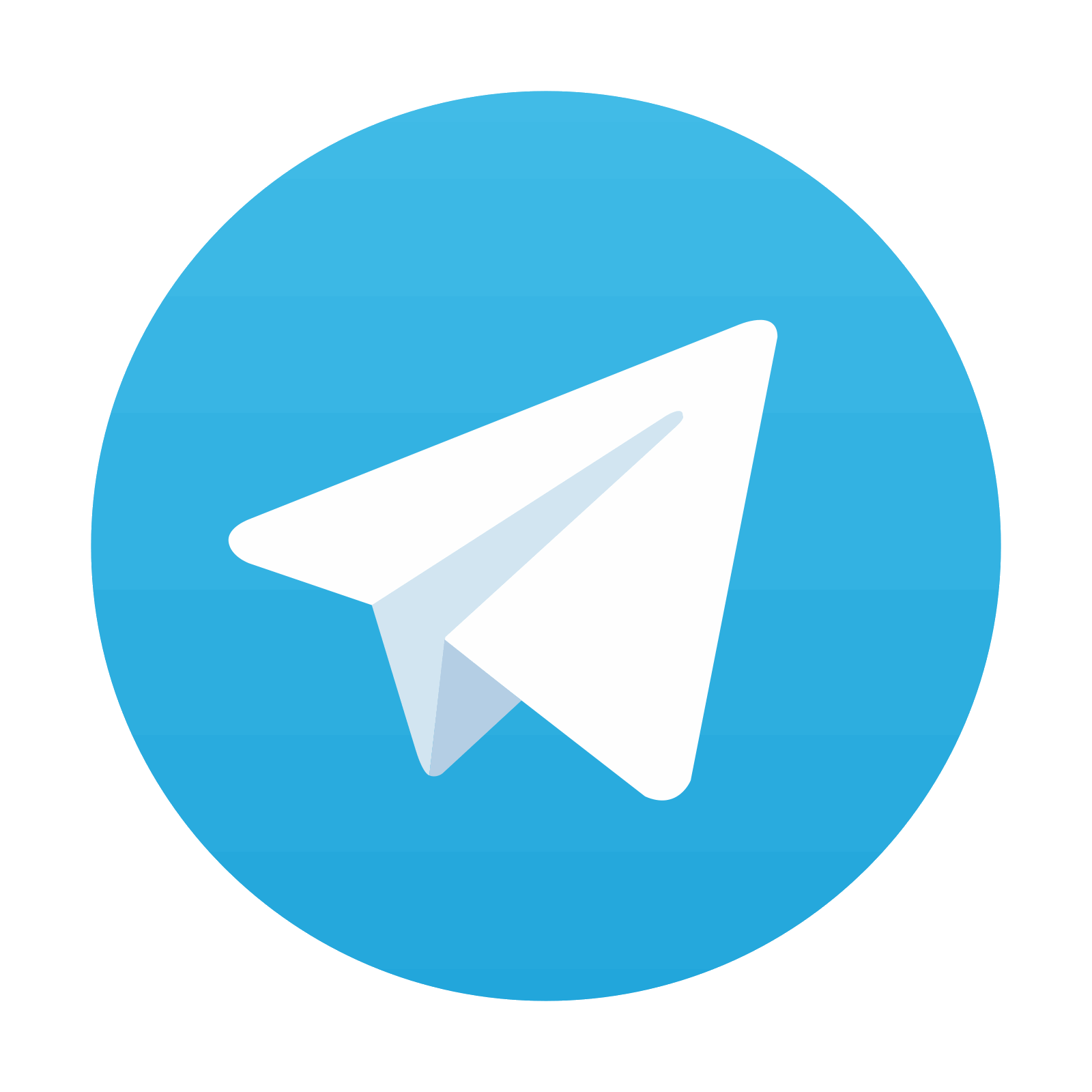
Stay updated, free dental videos. Join our Telegram channel

VIDEdental - Online dental courses
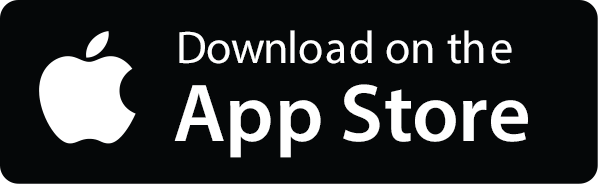
