Introduction
The aim of this study was to determine the effects of variations in thread shape on the axial pullout strength of orthodontic miniscrews.
Methods
A total of 35 miniscrews, 7 of each design being considered, were tested by performing pullout tests on a synthetic bone support. We used self-tapping and self-drilling miniscrews having a diameter of 2 mm and a thread shaft length of 12 mm (the longest and the largest supplied by the manufacturer). A buttress reverse thread shape served as the control design and was tested against 4 experimental designs, each manufactured with a modification in thread shape while maintaining all other characteristics. The experimental groups had the following thread designs: buttress, 75° joint profile, rounded, and trapezoidal.
Results
The control group with a buttress reverse thread shape had consistently higher pullout strength values than did the other designs. A statistically significant reduction in pullout force was found between the buttress reverse and the buttress thread miniscrews.
Conclusions
Thread design influenced the resistance to pullout of the orthodontic miniscrews. The buttress reverse thread shape provided the greatest pullout strength.
The group of temporary anchorage devices, also known as skeletal anchorage systems, includes screw-type implants (miniscrews, mini-implants, microscrews, and micro-implants), onplants, miniplates, zygoma implants, and palatal implants. With respect to other systems, miniscrews and miniplates are being progressively adopted into clinical orthodontics. Miniscrews are generally more widely used because of their lower cost structure, ease of insertion and removal, and versatility of placement. In clinical practice, miniscrews are loaded immediately after insertion, and achieving maximum primary stability—ie, the screw’s initial holding power in the bone—is therefore of prime importance. Only with such stability are miniscrew micromovements reduced, thereby favoring good tissue healing, a necessary condition to maintain the device in situ.
Primary stability can be affected by various miniscrew design features, including length, diameter, thread design (shape, pitch, and depth), and self-drilling vs self-tapping threads. Concerning thread design, little scientific evidence is available regarding the influence of thread shape on the mechanical yield of miniscrews.
Without an established gold standard for measuring primary stability, research has been focused on the in-vitro assessment of the biomechanical properties of miniscrews as indicators for their primary stability. Measuring performance in pullout tests with axial forces is a well-established method to compare different screw designs, and the resulting pullout strength has been described in the orthopedic, maxillofacial surgery, and orthodontic fields as a fundamental biomechanical parameter contributing to the primary stability of screws. The aim of this in-vitro study was to evaluate the role that variations in thread shape might have on the axial pullout strength of orthodontic miniscrews.
Material and methods
Miniscrews with 4 different experimental designs were manufactured, each with a single feature altered while maintaining all other characteristics constant compared with a commercially available control design. By hypothesizing a mean difference of 15 N (SD, 9) in the pullout strengths between the different screw designs (derived from a pilot study), with power of 80% and α = 0.05, a minimum of 6 miniscrews was required for each group.
Seven miniscrews made of titanium grade V (Ti 6 Al 4 V), 12.0 mm in length and 2.0 mm in external diameter, were selected as the control (VectorTAS; Ormco, Glendora, Calif). The longest miniscrews with the largest possible diameter offered by the manufacturer were chosen because these characteristics have been shown to provide greater resistance to pullout. The aim was also to develop an experimental condition under which the greatest number of threads was available to better understand how the variations in thread design of miniscrews affect the pullout load values. The screws were self-drilling and self-tapping, with a cutting flute at their apex. They had a 15° conical shaft and an asymmetrical buttress reverse thread shape ( Fig 1 , A ).

Four experimental design groups of 7 miniscrews each were made by modifying the thread shape: (1) buttress thread, opposite to the buttress reverse, with thread peaks inclined toward the miniscrew tip ( Fig 1 , B ); (2) 75° joint profile thread, with the threads joining the shaft at an angle of 75° ( Fig 1 , C ); (3) rounded thread, with the thread peaks rounded ( Fig 1 , D ); and (4) trapezoidal thread, with the thread profile trapezoidal ( Fig 1 , E ). All the other geometries of the screws were identical to the control design.
Thus, in total, 35 miniscrews were tested, 7 of each design. A synthetic bone support (1522-12 Cellular Rigid Polyurethane Foam; Sawbones Europe, Malmö, Sweden) was used to ensure uniformity in the pullout strength evaluations. On the upper surfaces of each sample, the geometric center was marked, and the miniscrews were inserted at these points to a depth corresponding to the entire thread length. Insertion was carried out through a hole (2 mm in diameter), made at the center of an appositely created steel bar (1.5 mm in thickness) bent into a U shape. The bar served as a guide for the miniscrews to be placed in a perpendicular orientation to the foam bone surface and minimized any wobbling during insertion. All procedures were performed manually by the same operator (A.G.) using a dynamometric torque driver calibrated to 15 Ncm to ensure optimal control of insertional torque.
For pullout testing, each synthetic bone support was housed securely in a frame that was fastened to a testing machine (Instron model 4467; TestResources, Shakopee, Minn) by a series of threaded bolts. This configuration of the testing setup ( Fig 2 ) permitted a perfect axial coincidence between the miniscrew, the synthetic bone support, and the dynamometric cell. The distal ends of the steel bar were secured to the testing machine so that vertical forces, oriented parallel to the long axis of the miniscrews, were applied to the heads of the miniscrews. A crosshead speed of 10 mm per minute was chosen in accordance with previous reports.
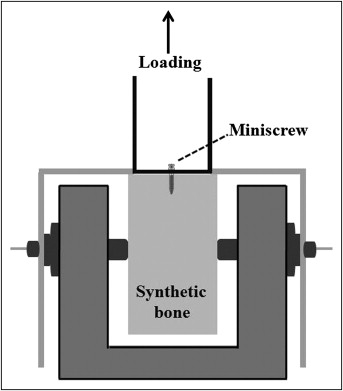
Statistical analysis
The pullout strength was measured as the peak force when the screw loosened from the synthetic bone support. The Levene and Lilliefors tests were used to verify the equality of variance and the normality of distribution of the examined variables. One-way analysis of variance (ANOVA) and Tukey post-hoc tests were used to compare the results obtained for each group. Statistical analyses were performed by using the statistical software (SPSS for Windows, version 16.0; SPSS, Chicago, Ill). The level of significance was set at 0.05.
Results
Since the Levene and Lilliefors tests confirmed the equality of variance and the normality of distribution of the examined variables, 1-way ANOVA was used for the between-group comparisons. A statistically significant difference was detected between the groups (F = 4.56; P <0.05). Table I shows the means, standard deviations, and standard errors of the maximum pullout forces for each design of miniscrew. The means in the pullout tests ranged from 170.0 ± 10.3 N (buttress) to 192.8 ± 13.3 N (buttress reverse). The Tukey post-hoc test subsequently showed a statistically significant difference between the buttress reverse screw (192.8 N) and that of the buttress thread profile (170.0 N) ( Table II ). All other paired comparisons showed no statistically significant differences.
Group | n | Mean (N) | SD | SE | 95% CI | Minimum (N) | Maximum (N) | |
---|---|---|---|---|---|---|---|---|
Lower limit | Upper limit | |||||||
Buttress reverse (control) | 7 | 192.8 | 13.3 | 5.0 | 180.5 | 205.2 | 182.2 | 217.7 |
Buttress | 7 | 170.0 | 10.3 | 3.9 | 160.5 | 179.6 | 159.3 | 186.0 |
75° joint profile | 7 | 181.2 | 11.6 | 4.4 | 170.5 | 191.9 | 161.5 | 193.4 |
Rounded | 7 | 188.4 | 8.7 | 3.3 | 180.4 | 196.5 | 174.4 | 199.6 |
Trapezoidal | 7 | 184.7 | 8.8 | 3.3 | 176.6 | 192.9 | 173.6 | 197.3 |
Groups | Mean difference | SE | Significance | 95% CI | |
---|---|---|---|---|---|
Lower limit | Upper limit | ||||
Buttress reverse vs buttress | 22.8 | 5.7 | 0.003 | 6.2 | 39.4 |
Buttress reverse vs 75° joint profile | 11.6 | 5.7 | NS | −5.0 | 28.2 |
Buttress reverse vs rounded | 4.4 | 5.7 | NS | −12.2 | 21.0 |
Buttress reverse vs trapezoidal | 8.1 | 5.7 | NS | −8.5 | 24.7 |
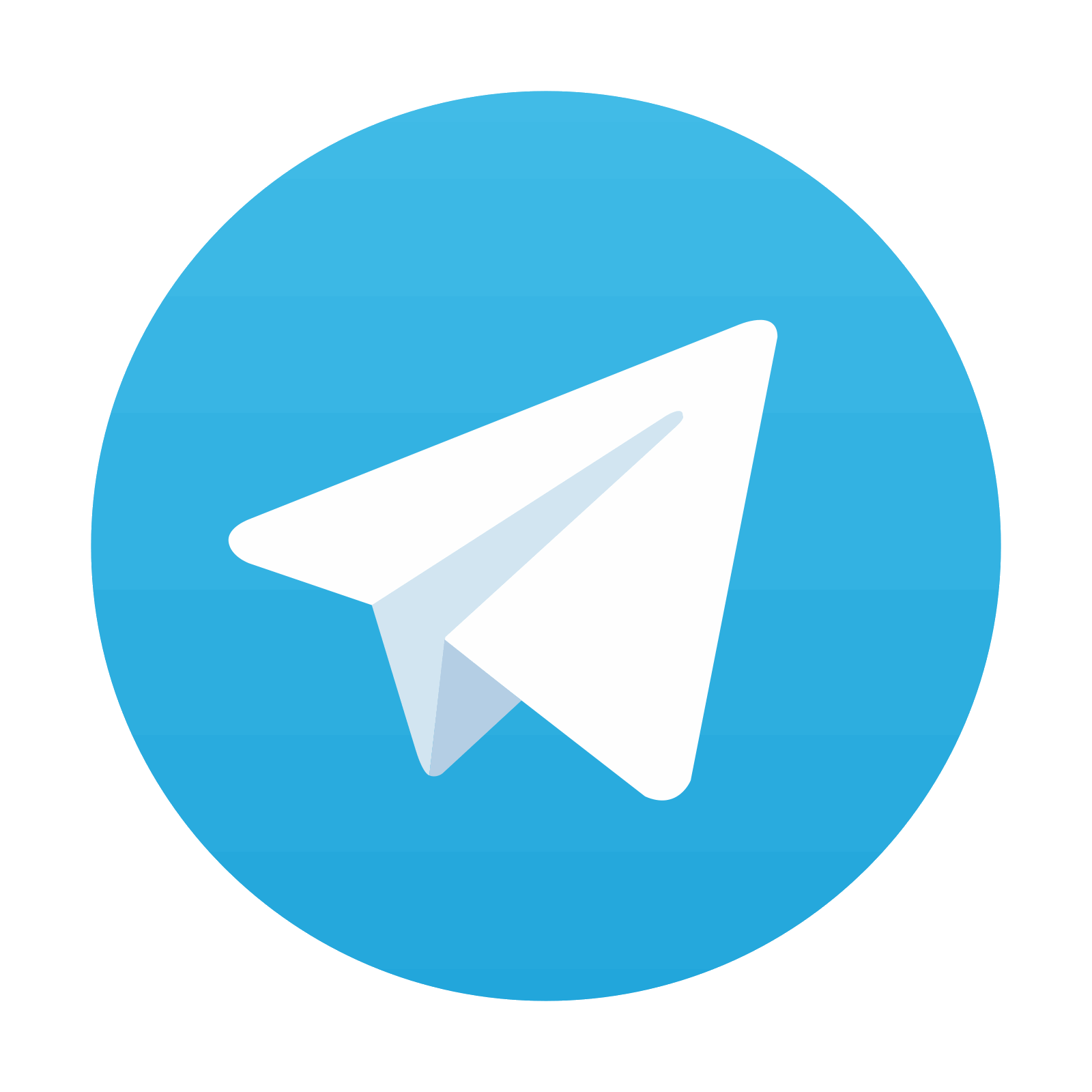
Stay updated, free dental videos. Join our Telegram channel

VIDEdental - Online dental courses
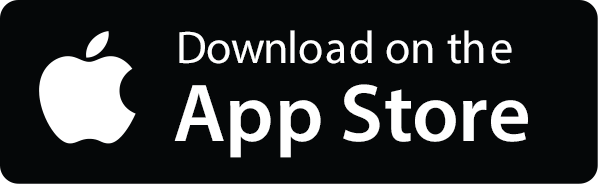

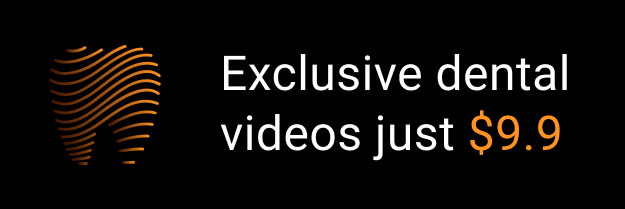