Chapter 6 Dental amalgam
Learning Objectives
After studying this chapter, the reader will:
• Understand what dental amalgam is and the significance of its constituents
• Be aware of the types of alloy available, their advantages and disadvantages and the names of the currently available commercial products
• Understand the properties of dental amalgam and how they influence clinical performance
• Be aware of its manipulation and handling
• Understand the rationale behind bonding amalgam in situ
• Have an increased appreciation of how to use the material more effectively
• Understand the health and safety aspects of using dental amalgam.
Definition
An amalgam is formed when an alloy of two or more metals is mixed with mercury. This reaction is called amalgamation. Dental amalgam is the product of the amalgamation between mercury and an alloy containing silver, tin, often copper, and sometimes other elements combined in varying amounts.
When to Use Dental Amalgam
• The restoration of Class I and Class II cavities, particularly those of moderate to large size
• Core build-ups: when the definitive restoration will be a cast restoration, such as a crown or bridge retainer, as more tooth structure will need to be replaced and the tooth reinforced.
Dental amalgam is used mainly in the posterior sextants of the mouth because of its unaesthetic appearance (Figure 6.1). However, as amalgam is not tooth coloured, the core material and the tooth tissue can be easily identified, ensuring that the margins of the crown are placed onto tooth tissue and not the core material (Figure 6.2).
Alloy: the by-product of the fusion of two or more metal elements after heating above their melting temperatures.
Class I cavity: a one surface preparation involving the occlusal surface of a posterior tooth.
Class II cavity: a two or more surfaces preparation that involves the proximal surface of a posterior tooth.
Sextant: One of the three sections into which a dental arch can be divided.
Composition of Dental Amalgam
The basic amalgamation reaction is that of mercury reacting with the surface of the alloy particles.
The alloy
Conventional alloys
The typical constituents of commercially available conventional alloys, their functions and clinical influence are shown in Table 6.1.
Element | Function |
---|---|
Silver | Main constituent of alloy, combines with tin |
Tin | Combines with silver |
Copper | Increases mechanical properties, decreases creep, increases corrosion resistance, decreases the amount of the γ2 phase formation |
Zinc | Acts as a scavenger of oxygen |
Mercury | Sometimes added to increase the rate of reaction (pre-amalgamation) |
Indium, palladium, selenium, platinum, gold | All increase corrosion resistance and improve certain mechanical properties of the final product. Decrease creep |
Amalgamation reaction of a conventional alloy
The mercury reacts with the outer layer (3–5 μm) of the silver–tin alloy particle in a reaction shown in Figure 6.3A. This means the bulk of the particle is left unreacted. These unreacted cores sit within a matrix of the silver–mercury and tin–mercury phases. The structure of the set material is shown in Figure 6.3B.
High copper amalgam alloys (Figure 6.5)
• Early full strength achieved within 1 hour of placement
• Increased mechanical properties, e.g. compressive strength
• Reduction in creep and therefore ditching (creep values of these alloys are between 0.09% and 1.8%)
Setting reaction of high copper amalgam
The setting reaction of these alloys is the same as the reaction for conventional alloys (see Figure 6.3A). After the formation of the γ2 phase, there is a reaction between this and the silver–copper component, leading to the formation of a copper–tin phase and γ1. Although silver is present in the alloy particles, there is a preferential reaction between the copper and tin, thus forming a silver–tin–copper complex. The result is that little or no γ2 is left in the final amalgam.
Types of high copper amalgam alloy
There are two types of high copper amalgam alloy:
• Dispersed phase alloys – in these alloys, the copper is dispersed throughout the alloy and has the effect of increasing its strength. The alloy particles consist of either silver–tin or silver–copper. This means that the total silver content may be kept the same as in conventional alloys.
• Ternary alloys – ternary means a compound containing three elements, usually silver, tin and copper in this case. Ternary alloys are sometimes called unicompositional alloys as they have all three components in one particle.
Many manufacturers reduce the silver and tin content when increasing the copper content. A small amount of zinc is sometimes added to high copper amalgam to improve its clinical performance, in particular by decreasing marginal breakdown. Table 6.2 gives the general composition of the three types of alloy.
Types of alloy
Currently, three types of dental amalgam alloys are available: lathe cut, spherical and admixed (Figure 6.6). Their handling characteristics are all very different and it is important that they are manipulated correctly when used in the clinic for optimal performance of the set product (see pp. 63–65).
Properties of Dental Amalgam
Dimensional stability
Working time
The working time of a dental amalgam is influenced by:
Cavity design
Correct cavity design is important for the success of the final (amalgam) restoration.
• A minimum cavity depth of 2 mm is required because of the risk of fracture.
• No sharp internal line angles (Figure 6.7) should be left as this will lead to stress concentration in the juxtaposed material or lead to fracture.
• Attention should also be paid to the cavo-surface angles (see Figure 6.7) so that neither weak amalgam nor weak unsupported tooth is left at the margin.
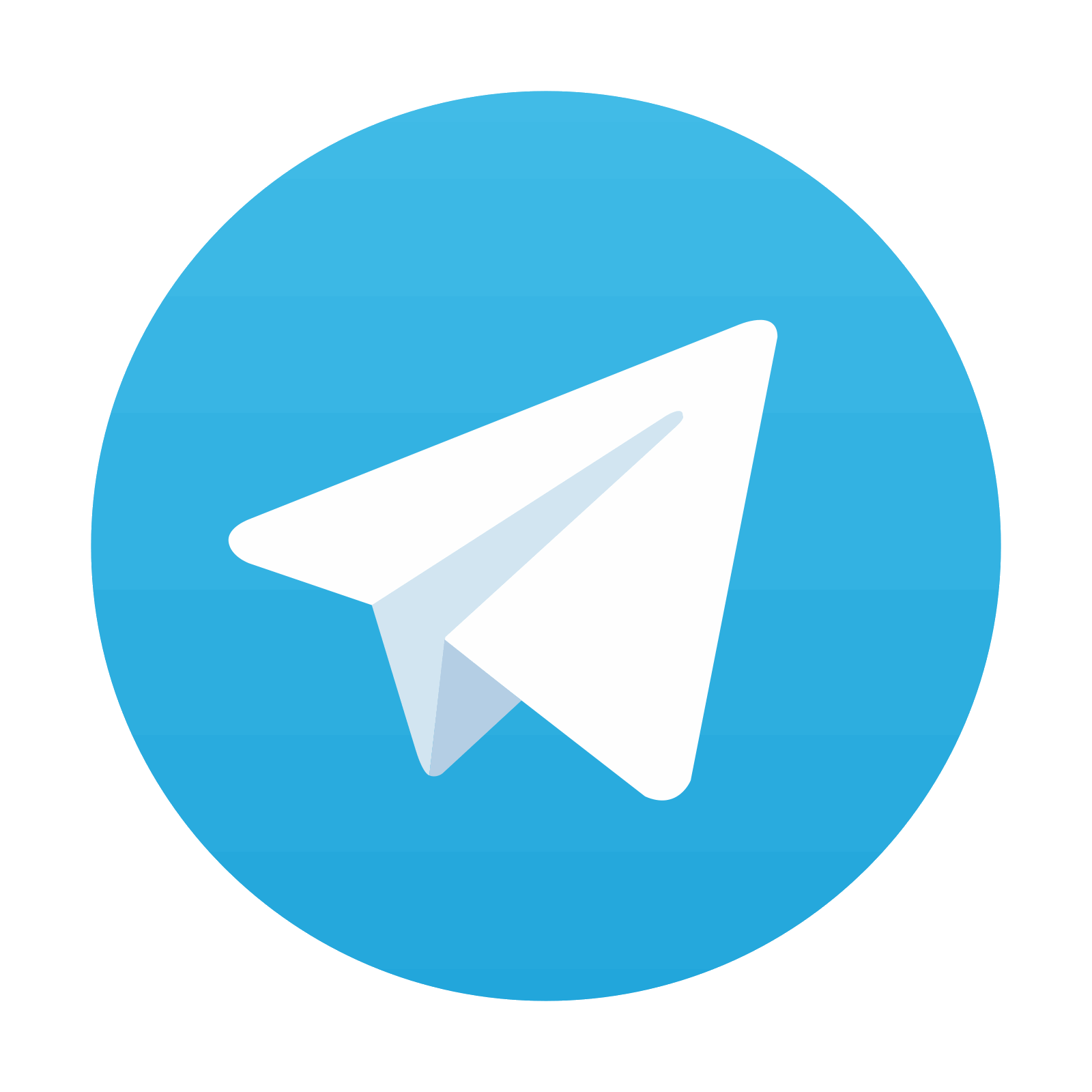
Stay updated, free dental videos. Join our Telegram channel

VIDEdental - Online dental courses
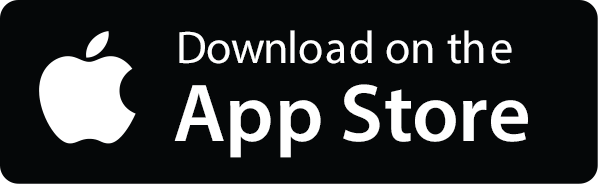
