Chapter 5 Control and use of materials in practice
Learning Objectives
Introduction
The manufacturer is required to provide the material to the end user in an ideal condition for use. It is the responsibility of the dental team to maintain the product in this condition up to and including the time of use. In order to achieve this, a method of stock control and ordering is essential. Materials should be ordered in good time to prevent untoward absences of any material during critical procedures. Furthermore, manufacturers’ instructions should be followed when using the material. Suitable methods of achieving these objectives have been set out below.
Stock Control Management
Rationalize materials
A good working relationship and communication between the various dentists in a clinic can significantly reduce the volume of stock held. Many of the generic groups of materials are produced by more than one manufacturer as they compete for market share. There is little point in a clinic carrying more than one product of the same generic type of material from different manufacturers. For example, there is nothing to be gained by stocking two (or even more!) types of resin-modified glass ionomer lining cement. If the practice decides to use either Vitrebond Plus (3M ESPE) or Fuji Lining LC (GC) (Figure 5.1) then there is no duplication of similar materials. This rationalization between clinicians will decrease stock quantities hugely with no detriment to clinical care.
Same material, multiple indications
Some dental materials may be used appropriately for more than one indication and in different applications. This again permits the reduction in material range required by a clinic, as the dentist may use the same material for different indications. For example, the clear bite registration material (e.g. Memosil, Heraeus) can also be used as an occlusal matrix for posterior composites, obviating the need to carry other bite registration products (Figure 5.2). Similarly, a material such as a flowable resin composite may be used in many applications (see Chapter 7).
Importance of the use-by date
With a smaller stock, a rapid turnover of materials will result in less wastage as the use-by date (following which the manufacturer will not guarantee the product will perform satisfactorily) will not be reached. Prior to use in the clinic, the use-by date of each dental material should be checked (Figure 5.3). If this date has been passed then the material should be discarded. Some of the ingredients might have degraded and the material may not perform as intended. For example, a catalyst not functioning properly will result in the material not setting fully, which in turn will impact on the material’s physical properties and therefore its clinical performance. When removing materials from the stock cupboard, the material with the closest use-by date should be selected to decrease the risk of the stored stock exceeding its shelf-life. The shelf-life of the material may play a part in influencing the dentist’s selection of one material in preference to another. A longer shelf-life reduces the risk of the use-by date being exceeded and the material having to be discarded.
Stock ordering
• At stock take (in many establishments an annual exercise or possibly even more frequently such as quarterly) the process can be carried out quickly by accessing the data by interrogating the computer program.
• Weekly ordering can be more quickly and easily done by determining what stocks were used since the last ordering day and therefore what needs to be replaced.
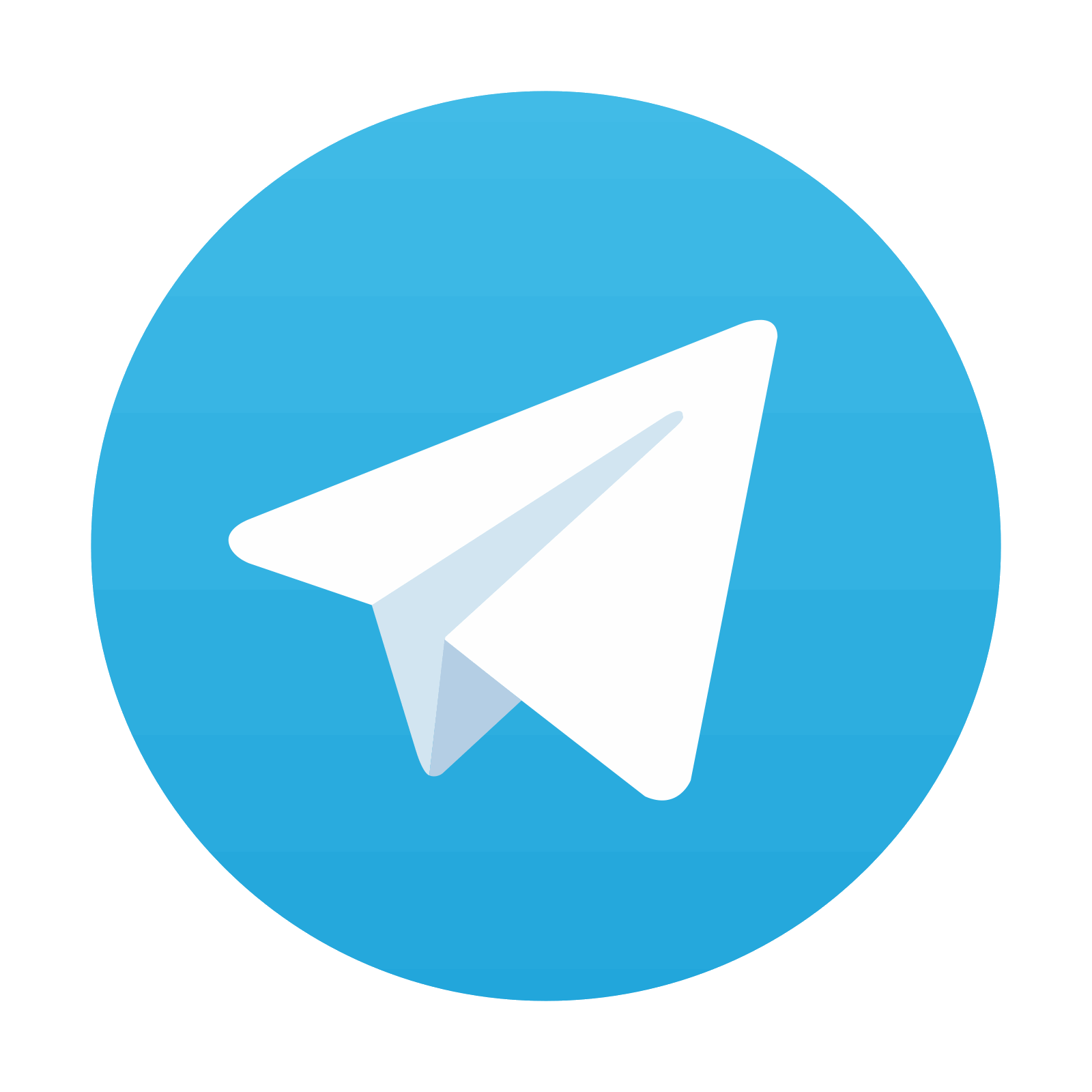
Stay updated, free dental videos. Join our Telegram channel

VIDEdental - Online dental courses
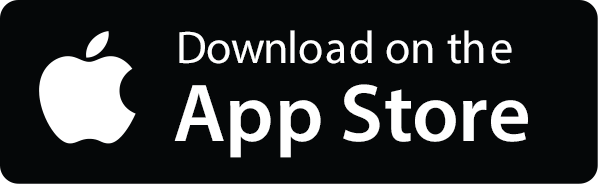
