Chapter 23 Polymers in prosthodontics
Learning Objectives
From this chapter, the reader will:
• Be aware of the denture base materials available
• Understand the properties of these materials and the influence of these properties on clinical performance
• Understand the significance of some of the manufacturing procedures in relation to the production of an optimized product
• Appreciate the types of denture teeth available and how their construction affects their function
• Be aware of the materials used for soft linings, tissue conditioners and mouthguards
• Know the names of currently available commercial products.
Introduction
A denture is a removable dental prosthesis. It can be a full (sometimes also referred to as complete) denture, where it replaces all the teeth in an arch. It can also be a partial denture, replacing one or more teeth with some natural teeth remaining in the arch. This chapter discusses the resin polymers used in the construction of both types of denture and other associated materials.
Denture Base Resins
The denture base is the part of the denture which is in contact with the oral tissues and supports the teeth (Figure 23.1). The denture base may be constructed of a metal alloy (discussed in Chapter 21) or a ‘plastic’ such as an acrylic.
What is required of a denture base resin?
The material of which the denture base is constructed must have certain requirements to perform satisfactorily (Box 23.1). While many materials can achieve some of these requirements, no material currently available achieves all of them. The materials which fulfil most of these criteria are the resin polymers and more specifically polymethylmethacrylate (PMMA).
Box 23.1 Requirements of a denture base resin
From the perspective of both the dentist and technician, the material should:
• Be of adequate strength to withstand occlusal loading
• Be easy to manipulate and process
• Not produce toxic fumes or dust during processing
• Remain unstained and unaffected by fluids and temperature changes in the oral cavity
• Be simple to repair when necessary
• Maintain its shape, form and aesthetics in normal function
Constituents
Polymer
The PMMA polymer powder is composed of small spheres called beads or pearls. It may also be in a fine granular form in some products. This enables the polymer to dissolve more readily in the monomer as its surface area to volume ratio is higher. The size of these particles is approximately 150 μm in those resins which are processed by heat, the most commonly used method. Other chemicals are added to the PMMA poly-mer to modify the final product (Table 23.1). For example, PMMA is inherently translucent and so pigments and opacifiers must be added to change its appearance unless a clear acrylic is desired.
Table 23.1 Typical chemical constituents of the powder component of a heat-cured resin
Constituent | Percentage (%) | Reason for inclusion |
---|---|---|
Polymethylmethacrylate | 95–98% | Principal component |
Benzoyl peroxide | 1 | Initiator |
Titanium dioxide | Small amount | Increases opacity to match the translucency of the oral soft tissues |
Zinc oxide | ||
Inorganic pigments | 1 | Varies colour, respectively: |
Mercuric sulphide | Red | |
Cadmium sulphide | Yellow | |
Ferric oxide | Brown | |
Dibutyl phthalate | Small amount* | Plasticizer |
Dyed synthetic fibres – nylon or acrylic | Small amount | Simulate anatomical structures such as capillaries within the denture base material |
Monomer
The liquid monomer is mainly MMA. This is a volatile liquid whose boiling point is 100.3°C. It is toxic if inhaled for a prolonged period and it is also highly flammable. It should therefore be handled in a well-ventilated room or preferably a fume cupboard. As with the powder, additional chemicals are added to the liquid to modify the final product (Table 23.2). In some products higher methacrylate monomers such as ethyl and butyl are substituted for the methylmethacrylate because they are less irritant.
It is advantageous that the mechanical properties of the acrylic are improved to increase the wear and fracture resistance of the material and also its resistance to the action of organic solvents which may cause surface cracking or crazing. This is achieved by adding cross-linking polymers such as diethylene glycol dimethacrylate. These different monomer units (co-polymers) can react with another growing chain at each end of the molecule when the polymer chains are growing so linking the chains. They are present in relatively small amounts and they have little effect on the transverse strength or hardness of the denture base material.
Setting reaction
The reaction is highly exothermic and this temperature must be carefully controlled as the volatile monomer, whose boiling point is 101°C, may vaporize during processing. Since the processing is carried out in a plaster mould, this heat is slow to dissipate and there is a risk of gas bubbles being produced. These bubbles of gas can become entrapped in the denture base resin, leading to gaseous porosity (Figure 23.2).
Properties
Mechanical properties
Its fracture toughness is also low and as it behaves as a brittle material on impact, a denture will frequently fracture if dropped onto a hard surface. To avoid this, patients should be advised to clean their denture over a bowl of water rather than directly over an empty hard ceramic bathroom basin (Figure 23.3). Dentures dropped on this type of surface will break very readily.
Thermal properties
• During processing, the heat produced as a product of the exothermic reaction cannot escape; this may cause gaseous porosity of the denture base
• The low diffusivity means that the transfer of heat from one side of the denture to the other is slow, that is, it takes time for heat to permeate the denture base and reach the underlying soft tissues. This has two consequences:

Dimensional stability
• It (or the benzoic acid which can also leach out) is an irritant to oral soft tissues. Improper processing will compound this problem. Concern has been expressed that it may cause an allergic reaction but has largely been dismissed as the reaction of the oral soft tissues is irritancy to the monomer and not a true allergy
• It acts as a plasticizer so softening the polymer, making the denture base weaker and increasing its flexibility. Fracture may also result.
The polymer may creep under load over the long term and deform the denture base. This phenomenon is more marked with cold-cure acrylics and can create greater problems. The addition of cross-linking agents is an attempt to minimize this effect.
Crazing
Crazing may also be seen if the denture is not kept moist at all times during its life. This is due to mechanical stresses set up within the denture base as it contracts and expands during the drying and wetting cycle. The cross-linked resins are less likely to craze as they contain fewer lines of weakness (Figure 23.4).
In order to prevent crazing, the polymer should not be allowed to dry out and so the finished denture should always be supplied to the dentist in water (Figure 23.5). The patient should then be advised to store the prosthesis in water when it is not in use. Wrapping in gauze or cotton wool is inadequate as the resin does not remain saturated.
Shade of denture base acrylics
Denture base acrylics are available in different shades to match the patient’s natural gingival tissues. This is more significant in patients whose mucosa is more pigmented. Some acrylics are available with small fibres of red acrylic in them which mimic small blood vessels and these are called veined materials (Figure 23.6). These fibre inclusions are frequently coated with a coupling agent, commonly triethoxysilane, to improve their wettability.
Types of Acrylic
Acrylics can be categorized based on their means of curing or their properties:
Heat-cured acrylic
When the polymer and monomer are mixed they initially form a sand-like mixture. This changes to a tacky mass as the surface of the polymer beads start to dissolve in the monomer. Under normal conditions once the polymer and monomer have been mixed then the mixture is left undisturbed in the mixing container until the dough stage is reached (Figure 23.7).
The next stage is described as the dough stage. As the name implies, the mixture at this point is similar in appearance to the dough used in bread making. The mixture does not stick to the container walls and ‘snaps’ when pulled apart (Figure 23.8). Failure to pack the mixture into the mould at the dough stage will result in the material becoming too rubbery and stiff. It cannot then be moulded properly.
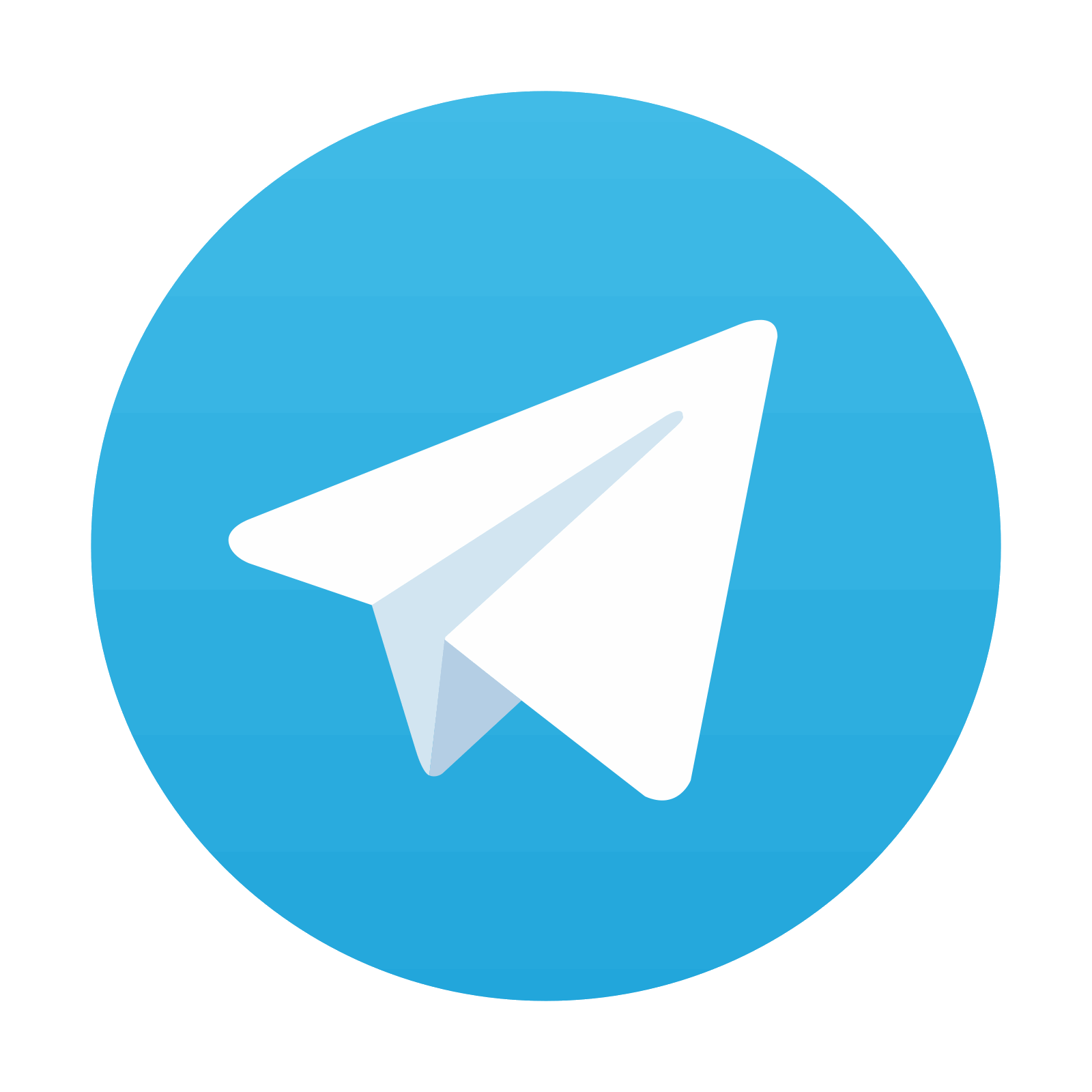
Stay updated, free dental videos. Join our Telegram channel

VIDEdental - Online dental courses
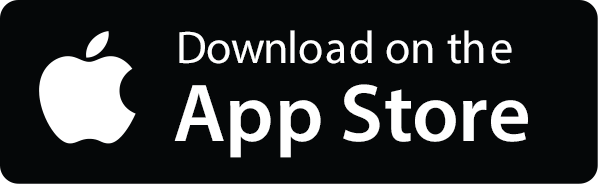
