Chapter 22 Dental ceramics
Learning Objectives
From this chapter, the reader will:
• Understand what constitutes a dental ceramic and the different types of dental ceramic
• Understand their properties and how these affect their manufacture, clinical applications and performance
• Understand how ceramics may be strengthened with other materials, for example alloys, alumina or zirconia
• Understand the principles of preparation when ceramic restorations are planned
• Be aware of the role of CAD-CAM in the construction of all-ceramic restorations
• Know the names of the currently available commercial products.
Introduction
For many years the term dental porcelain described the material which was used to construct aesthetic restorations such as anterior crowns (Figure 22.1). Dental porcelain or ceramic is related to other ceramics which are used to make objects such as Chinese porcelain vases, engine mouldings, ballistic protection, roof tiles and the heatproof tiles on NASA’s space shuttle (Figure 22.2).
It is now acknowledged that the term ‘dental porcelain’ was incorrect. This is because little or no kaolin is present in the dental version, unlike the other (decorative) ceramics mentioned above (Table 22.1). Kaolin is a clay (chemically hydrated aluminium silicate). The reason for the absence of kaolin from dental ceramics is that it is opaque and this influences the optical properties and therefore the aesthetics of the final restoration.
Table 22.1 Comparison of the composition of decorative and dental ceramics
Composition | Decorative ceramic (%) | Dental ceramic (%) |
---|---|---|
Kaolin | 50–70 | 3–5* |
Quartz (silica) | 15–25 | 12–25 |
Feldspar | 15–25 | 70–85 |
Metallic colourants | <1 | 1 |
Glass | 0 | Up to 15 depending on fusing temperature |
The ceramics now used in dentistry have been specifically produced for dental applications. A ceramic may be defined as a material which is an inorganic non-metal solid produced by the application of heat which is then cooled. It may be amorphous and partly or wholly crystalline. Dental ceramics need to be translucent and so feldspar and silica are incorporated into the material to achieve this. Dental ceramics are therefore really glasses called feldspathic ‘porcelains’. Pigments are also included to improve and optimize the aesthetics.
Conventional Dental Ceramics
Conventional dental ceramics are vitreous ceramics made up of a silica network with either potash feldspar (potassium alumino silicate) and/or soda feldspar (sodium alumino silicate) (Figure 22.3 and Table 22.2). This latter material is also called albite. Feldspars are a mixture of both of these materials with the proportions differing to yield different properties. Feldspar is the lowest fusing component and melts and flows during firing, forming a solid mass uniting the other constituents. Borax is also frequently included to further lower the fusing temperature.
Table 22.2 Typical composition of two dental ceramics, an enamel and a dentine shade, used in the construction of an all-ceramic crown
The flux, in the case of a ceramic material, is a material which increases the viscosity of the molten glass and lowers the fusion and softening temperature of the glass. Binders act by holding the ceramic particles together prior to firing. As well as conveying opacity to the final product, cerium also produces fluorescence. Feldspathic porcelains are also referred to as opalescent porcelains as various metallic oxides are added to convey opalescence and provide colour. The amounts and constituents vary as to the requirements of the final product. Table 22.3 lists the metallic oxides used together with the colour which their inclusion imparts.
Table 22.3 Metallic oxides convey various colours to the ceramic
Metallic oxide of | Colour |
---|---|
Chromium | Green |
Cobalt | Blue |
Copper | Green |
Iron | Brown |
Manganese | Lavender |
Nickel | Brown |
Titanium | Yellow/brown |
Types of dental ceramic
The composition of the ceramic powder is such that a further chemical reaction is not required. Instead the particles of the ceramic powder fuse when it is heated to just above its glass transition temperature. This is called sintering (see Chapter 9). It is very important that the powder particles are very closely packed so that a dense compact structure without air inclusions is produced. During sintering, the glass phase will soften and start to coalesce. This is termed liquid phase sintering. This process takes time and may be halted at any stage by removing the ceramic from the heating oven. During the heating process, the glass phase will initially soften and a friable matrix is established. As the temperature rises the other components tend to fill the voids within the glass matrix. There is controlled diffusion between the particles, and as this continues, a dense solid is formed.
Dental laboratory procedure
• It formed a supporting matrix for the ceramic which was laid down to build up the restoration
• Prevented the ceramic powder coming into contact with the die so protecting it from damage
• Provided support during the firing process and ensured that the fit to the model was maintained.
Building up the restoration: dentine portion
The ceramic powder is mixed with distilled water to form a creamy paste, which is then laid down onto the coping. It is important that the minimum amount of air is incorporated into the powder slurry during this process to avoid porosity and stress concentrations in the final product. To produce minimum shrinkage during the firing process the powder must be condensed to remove water and pull the ceramic particles closer together. This is called compacting and is achieved by either vibration, spatulation or smoothing/burnishing with a brush. Once condensation has been achieved, the excess water is blotted away using absorbent tissue (Figure 22.4).
Building up the restoration: enamel portion
Once the dentine portion of the restoration has been applied, the appropriate shade of enamel is selected and this is built up as previously described. The final built-up mass is substantially oversized than the restoration it will finally become. A combination of the condensation process and firing will reduce the size markedly. At this point, the mass is referred to being in the green state, i.e. the prefiring state. It is very fragile and must be handled very carefully (Figure 22.5).
Firing: first bake
The mass is fired to fuse the particles together and form the final restoration, by a series of ‘bakes’ in the furnace. It is important that the mass is slowly heated initially to eliminate the water from the slurry and allow shrinkage to occur. To achieve this, it is usually held near the entrance to the furnace for sometime before being introduced inside (Figure 22.6).
During the first ‘bake’ the water is driven off and the powder particles sinter together. The majority of the shrinkage occurs during this firing and is in the range of 10–20%. The temperature of the furnace is set at about 50 °C below the fusing temperature of the ceramic powder being used. During this time, the binders are burned off and the ceramic particles start to fuse at the points of contact, forming a porous mass. The voids in the porous mass start to disappear as the molten glass flows between the particles, drawing them closer. This is called pyroplastic flow. Shrinkage continues to occur until an almost void-free material results. This is often referred to as the biscuit bake or biscuit firing (Figure 22.7).
Firing: subsequent bakes
If the technician deems that further ceramic is required to complete the restoration, this is added and the restoration fired again. Figure 22.8 shows a crown just prior to firing with the various ceramic powders built up. The different colours help in differentiating the dentine and enamel powders. These colours are lost in the firing.
Some considerations in firing
• This process must be carefully controlled as the temperature of the furnace and time that the ceramic is in it is critical.
• Overfiring can result in molten glass flowing too much and the restoration losing its shape. Modern furnaces are usually computer controlled and the changes required during the firing process can be programmed into the memory. This may involve firing in air or a partial vacuum, producing an atmosphere about 10% of normal. Some ceramic products come supplied with a bar code which is scanned to input the firing cycles required by that particular ceramic. This is of particular importance as each manufacturer’s ceramics have different firing parameters that should be adhered to precisely.
• The size of the particles of the ceramic powder also has an influence on the finished crown. Finer grained powders produce more uniform surfaces than coarser grains. Although the firing process and the densification which occurs will leave a structure which is solid, there is still a risk of small air voids being present. This is the case even when the firing process is carried out under vacuum. Much of the air within the ceramic structure is removed as the vacuum develops. The little that remains will be below atmospheric pressure. Once the furnace temperature has reached to within about 50 °C of the final firing temperature, the vacuum is released and this results in the voids collapsing as the pressure external to the crown is increased by a factor of 10 above the internal pressure in the crown.
Staining
Stains may now be applied using a paint brush to characterize the final restoration, such as the staining of occlusal fissures or hypoplastic spots. The staining kit resembles an artist’s palate (Figure 22.9). The stains may be applied to the surface of the restoration or become incorporated within the ceramic. If the stain is applied on surface, it may be lost if any adjustment is made or during function. Generally speaking, stains are better incorporated within the structure of the ceramic (Figure 22.10).
Glazing
The final stage of the firing process is the glazing of the restoration. This produces a glassy smooth surface on the restoration, sealing it. It will also fill in any small areas of porosity at the surface. Glazing is achieved by either very carefully re-firing the restoration to fuse the outer layer of ceramic completely or by using glazes with lower fusing (transparent glass) temperatures which are applied as a thin layer to the outer surface of the restoration. The restoration may then be adjusted with fine diamonds and polishing rubbers (Figure 22.11).
Properties of fired dental ceramics
Aesthetics
It is widely recognized that ceramic is the best dental restorative material with respect to aesthetics. When the shade and any characterization has been carefully prescribed and then replicated into the restoration, the aesthetics can be excellent creating an almost imperceptible result. It can be quite a challenge to notice the difference even for dental care professionals, particularly with all-ceramic restorations. Ceramics are colour stable and achieve a very smooth surface finish and have the ability to retain the finish better than other materials. However, they will be affected by acids. In particular, topical fluoride gels can etch the surface of the ceramic. This etching leads to the surface glaze being disrupted quite rapidly, possibly resulting in surface staining. Bulk colour changes can occur if the tints incorporated during the crown construction are involved.
Effects of tooth preparation
Ceramics may also fracture during function if the initial tooth preparation was inadequate. If the height of an anterior crown preparation is reduced excessively then a large area of tooth must be replaced by ceramic. If the unsupported ceramic is thicker than 1 mm it will have no support from the underlying tooth structure and therefore is at risk of flexure during chewing and biting, and thus fracture (Figure 22.12).
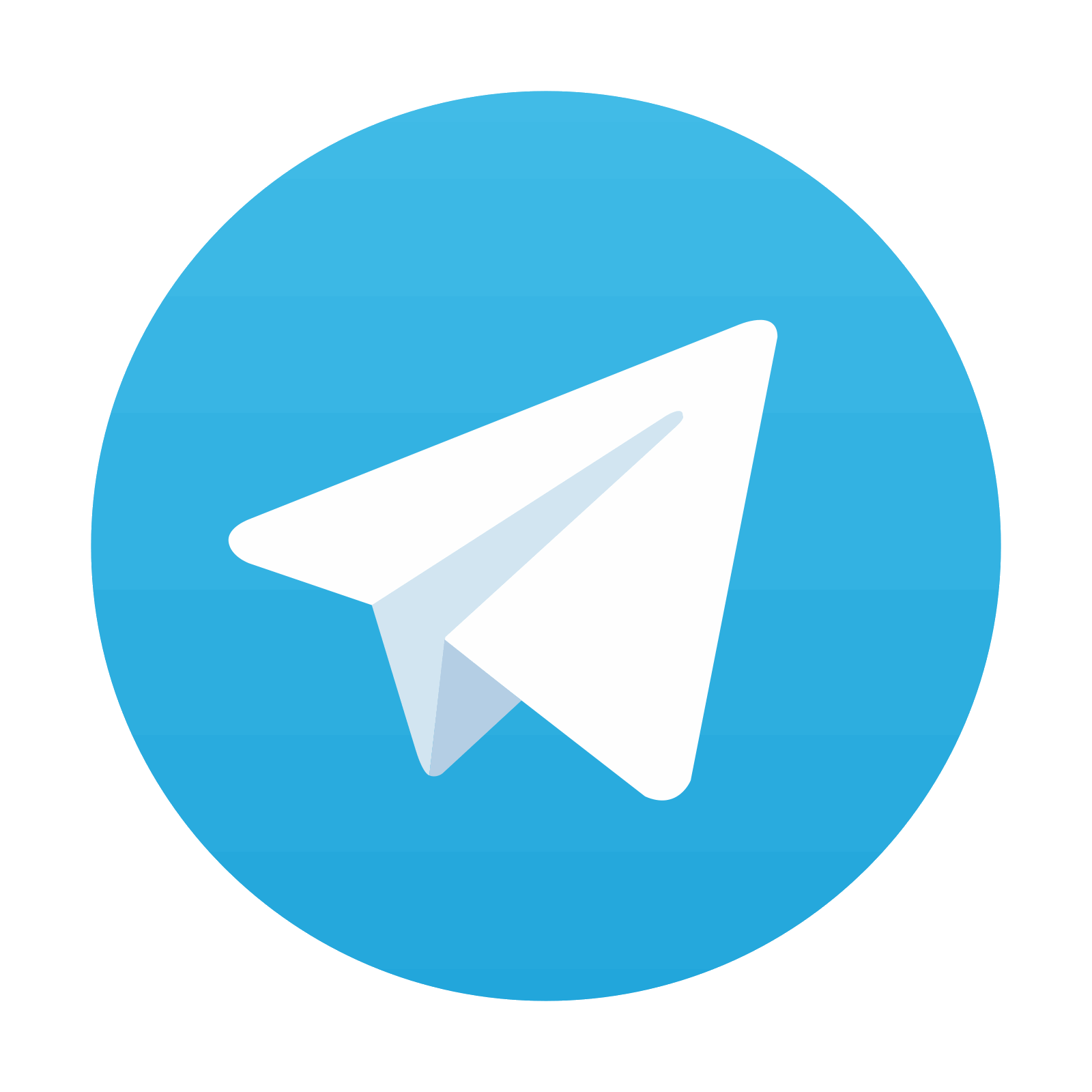
Stay updated, free dental videos. Join our Telegram channel

VIDEdental - Online dental courses
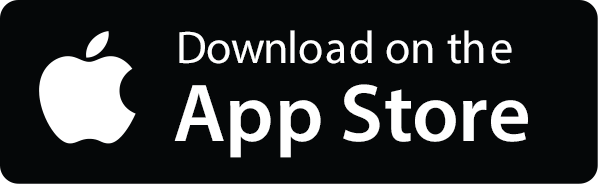
