2
Chemical Properties of MTA
David W. Berzins
General Dental Sciences, Marquette University, USA
INTRODUCTION
Mineral trioxide aggregate (MTA) was first described in the scientific literature in 1993 (Lee et al. 1993) as an aggregate of mineral oxides added to “trioxides” of tricalcium silicate, tricalcium aluminate, and tricalcium oxide silicate oxide. The initial patent (United States Patent #5,415,547, continued to #5,769,638) on what would become known as MTA was filed the preceding April by Mahmoud Torabinejad and Dean White, and described the tooth filling material as being comprised of Portland cement. In 1997, Tulsa Dental Products (now Dentsply Tulsa Dental Specialties) received a decision from the US Food and Drug Administration (FDA) that MTA was substantially equivalent in intended use and technological characteristics to similar products on the market for repairing pulpal tissues. With its designation as a Class II medical device for root canal filling from the FDA, MTA was subsequently marketed as ProRoot MTA. The commercial product was first available as a gray variety, and a tooth-colored version commonly referred to as “white MTA” was introduced in 2002 (Figs 2.1 and 2.2). Since the first research reports, further studies, numbering in the hundreds, were conducted on the initial experimental cement and the commercial ProRoot MTA products (as well as individual constituents and/or similar products). Despite some differences between the experimental and commercial materials, except when noted, no delineation will be made in this chapter between the varieties of MTA.
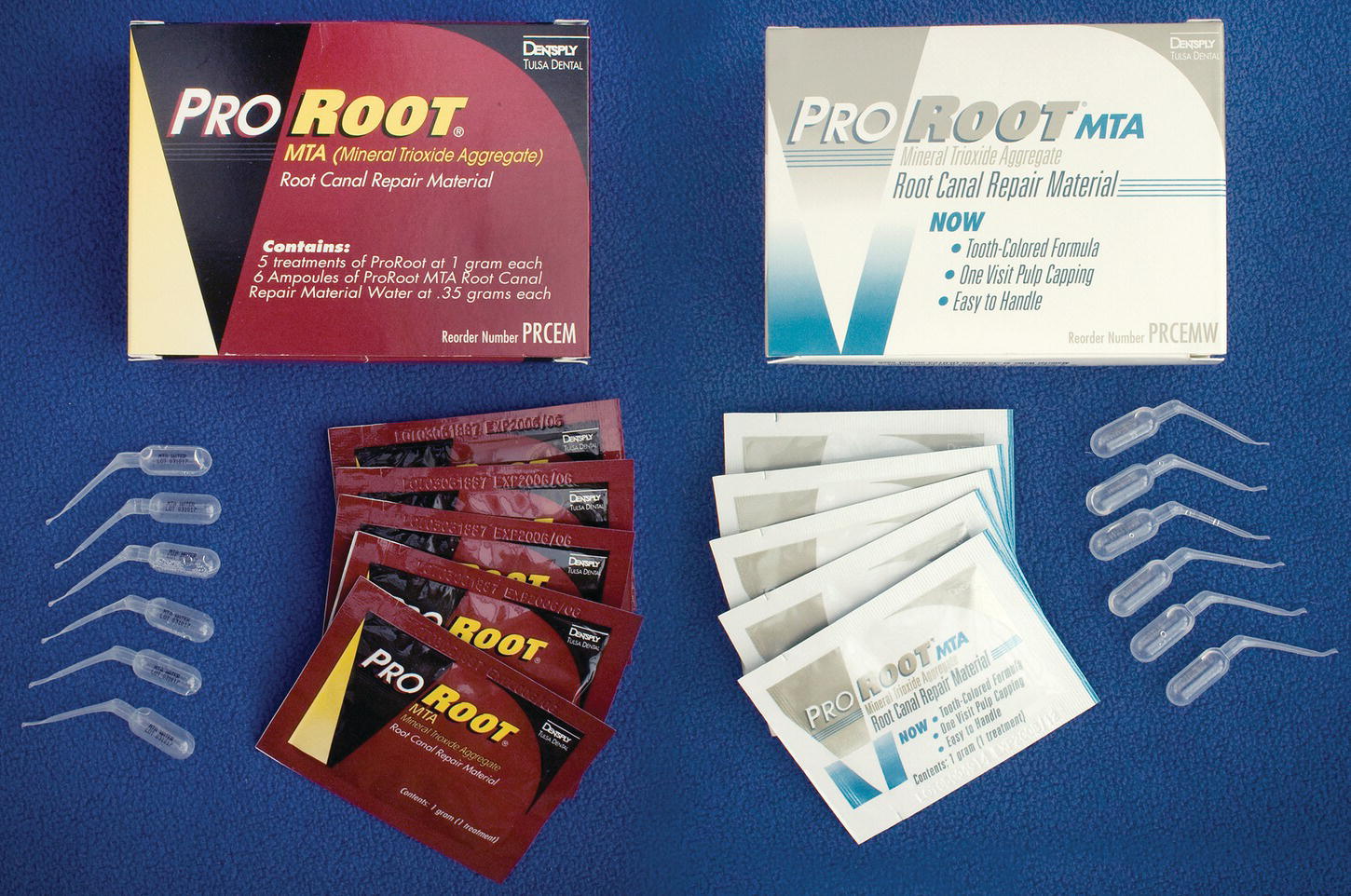
Fig. 2.1 Gray and tooth-colored ProRoot MTA.
Courtesy of James Brozek.
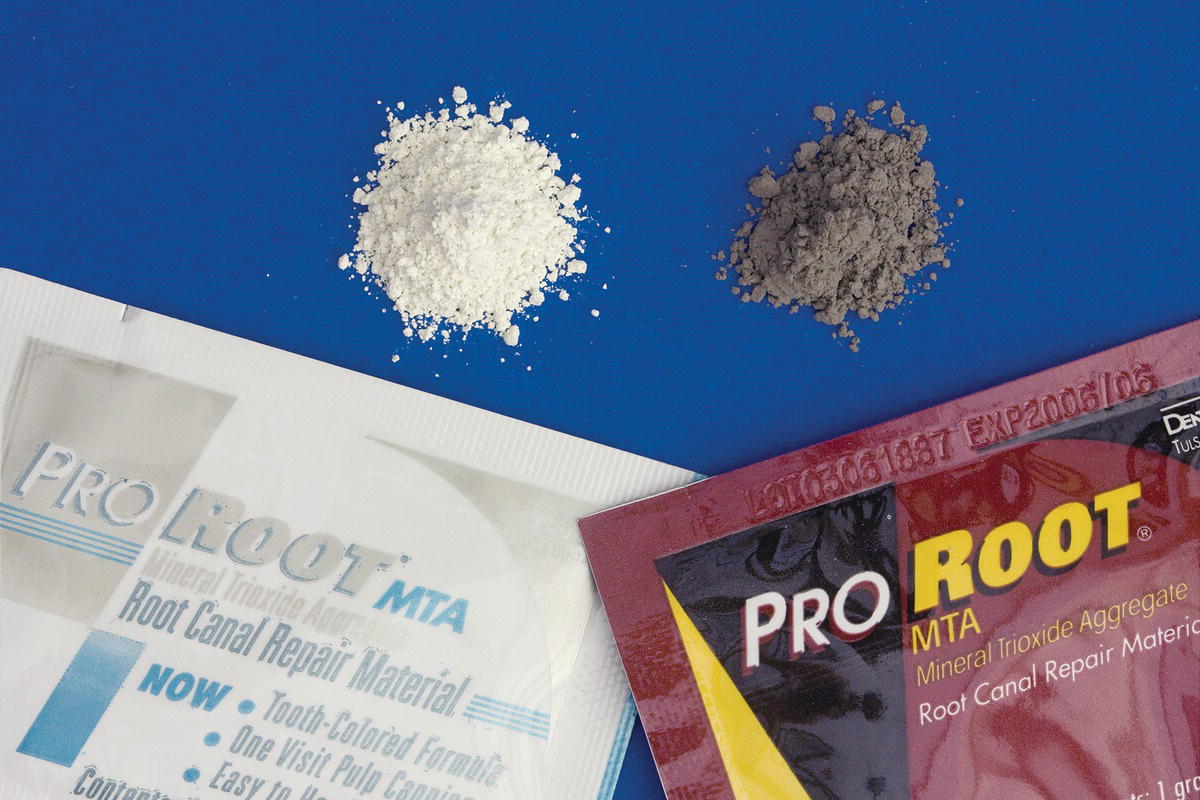
Fig. 2.2 Gray and white ProRoot MTA powder.
Courtesy of James Brozek.
MTA COMPOSITION
As stated in the patent, MTA is comprised primarily of Portland cement. The Material Safety Data Sheet (MSDS) of ProRoot MTA states that it is approximately 75 wt% Portland cement, 20 wt% bismuth oxide (Bi2O3), and 5 wt% calcium sulfate dihydrate or gypsum (CaSO4 ∙ 2H2O). Additional minor trace elements may also be present as stated in the MSDS.
Portland cement
The origins of Portland cement date back to the early to mid-1800s in Britain where the Aspdin family was involved in its development. Its name is derived from its similarity to a type of limestone quarried on the Isle of Portland in the county of Dorset in southwest England. Today, it is a very common hydraulic cement due to its inclusion in concrete, stucco, and mortar. The ASTM International (formerly the American Society for Testing and Materials) recognizes 10 types of Portland cement (ASTM Standard C150/C150M – 12 2012), but the Portland cement in MTA is restricted to Type I Portland cement. From ASTM C150/C150M, it is apparent that a strict, fixed composition for Portland cement is not set and a range of constituent component concentrations is tolerable. Additionally, variability in raw sources and manufacturing processes among different cement producers is to be expected; therefore, interpretation of research reports that compare MTA to Portland cement should be mindful of this.
Ordinary Portland cement is manufactured by first obtaining the raw materials (typically limestone or calcium carbonate, clay, and/or other materials), crushing the individual raw materials to acquire a smaller particle size, and proportioning them to create a specific composition. Next, the mixture is ground and blended together and introduced into a rotary, cylindrical kiln where it is heated to 1430−1650 ºC. This fuses the materials together after a series of reactions which include evaporation of water, dehydration of the clays, and decarbonation of the calcium carbonate (loss of carbon dioxide to yield calcium oxide). At this point, the mixture is called clinker. Once the clinker cools, it is ground to a fine powder size and is now considered Portland cement.
The Portland cement component in MTA consists of tricalcium silicate (3CaO ∙ SiO2 or Ca3SiO5, also known as alite), dicalcium silicate (2CaO ∙SiO2 or Ca2SiO4, also known as belite), and tricalcium aluminate (3CaO ∙ Al2O3 or Ca3Al2O6). Less of the latter component is contained in white MTA versus gray MTA, but it is still present (Asgary et al. 2005). Tetracalcium aluminoferrite (4CaO ∙ Al2O3 ∙ Fe2O3), on the other hand, is considered present in gray MTA but not in white MTA. Alternatively, the Portland cement fraction in MTA may also be thought of as mixtures of CaO (lime), SiO2 (silica), and Al2O3 (alumina) – as well as Fe2O3 (iron oxide) for gray MTA. In a typical Portland cement powder, tricalcium silicate and dicalcium silicate are in greatest proportion and are estimated to be roughly 75–80% of the cement, with tricalcium aluminate and tetracalcium aluminoferrite at approximately 10% each (Ramachandran et al. 2003). However, MTA has lower amounts of tricalcium aluminate compared with ordinary Portland cement, and it has been determined that the content of Ca3SiO5, Ca2SiO4, Ca3Al2O6, CaSO4, and Bi2O3 in white MTA is 51.9, 23.2, 3.8, 1.3, and 19.8 wt%, respectively (Belío-Reyes et al. 2009). This leads to the suggestion that MTA powder is not produced in a kiln but in a laboratory (Camilleri 2007, 2008), although others have said it is manufactured the same way as Portland cement (Darvell & Wu 2011). Alternatively, the amounts of CaO, SiO2, Al2O3, and Fe2O3 may be considered to be approximately 50–75, 15–25, <2, and 0–0.5 wt%, respectively (Darvell & Wu 2011).
Role of bismuth oxide and gypsum
Bismuth oxide is included in MTA to serve as a radiopaque agent because Portland cement is not sufficiently radiopaque for dental purposes. Although generally considered insoluble in water, speculation exists that it is not totally inert and plays a limited role in the setting of MTA as some bismuth oxide has been shown to form part of the calcium silicate hydrate structure (described below) and leach out over time (Camilleri 2007, 2008). However, others debate this (Darvell & Wu 2011). Regardless, it appears that the addition of bismuth oxide to Portland cement decreases its compressive strength and increases porosity (Coomaraswamy et al. 2007), suggesting that bismuth oxide has effects other than radiopacity as well.
Gypsum is added to Portland cement/MTA to alter the setting time and does so primarily by influencing the reactions of the tricalcium aluminate. Some conflicting reports exist as to whether it is truly calcium sulfate dihydrate in MTA, with other possibilities being calcium sulfate hemihydrate (CaSO4 ∙ ½H2O) or the anhydrous form (CaSO4) (Camilleri 2007, 2008; Belío-Reyes et al. 2009; Gandolfi et al. 2010b; Darvell & Wu 2011). Comparatively, ordinary Portland cement contains approximately double the amount of calcium sulfate species as found in MTA.
MTA powder morphology
The size and shape of the powder fraction of MTA has been examined by several researchers (Fig. 2.3). The size of Portland cement particles in the powder of white MTA generally range from <1 µm to 30–50 µm, and the bismuth oxide particles are approximately 10–30 µm (Camilleri 2007). Between MTA products, it appears the particles are more homogeneously sized in white MTA compared with gray MTA (Komabayashi & Spångberg 2008) and have fewer larger particles (Camilleri et al. 2005), which may explain the better handling properties of white versus gray MTA. In terms of shape, many of the particles are rather irregular, with some appearing needle-like (Camilleri et al. 2005). As mentioned above, comparison to ordinary Portland cement is problematic due to variations in Portland cement commercial products, but using microscopy, Dammaschke and associates observed white MTA powder to have a more uniform and smaller particle size compared with Portland cement powder (Fig. 2.4) (Dammaschke et al. 2005), but few differences have been noted as to the shape of particles between MTA and Portland cement (Komabayashi & Spångberg 2008). As would stand to reason, if the initial powder particles in MTA are smaller than those in Portland cement, the particles contained in set (hydrated) MTA are, similarly, smaller than in ordinary Portland cement (Asgary et al. 2004). This also holds true for white MTA versus gray MTA (Asgary et al. 2005, 2006). Overall, the Portland cement fraction of MTA appears to be more refined than industrial ordinary Portland cement.
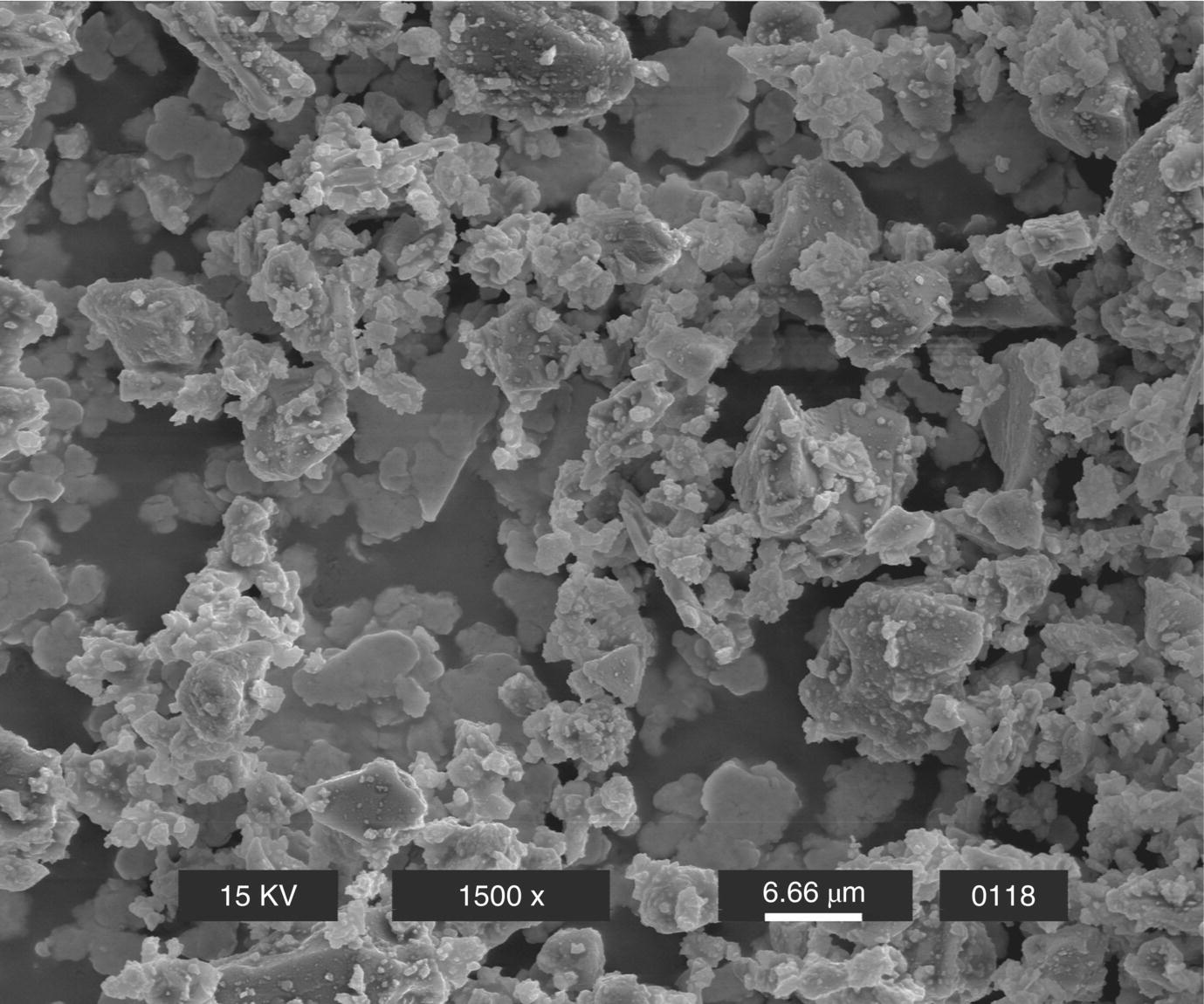
Fig. 2.3 Scanning electron micrograph of MTA powder.
Source: Lee et al. 2004. Reproduced with permission of Elsevier.
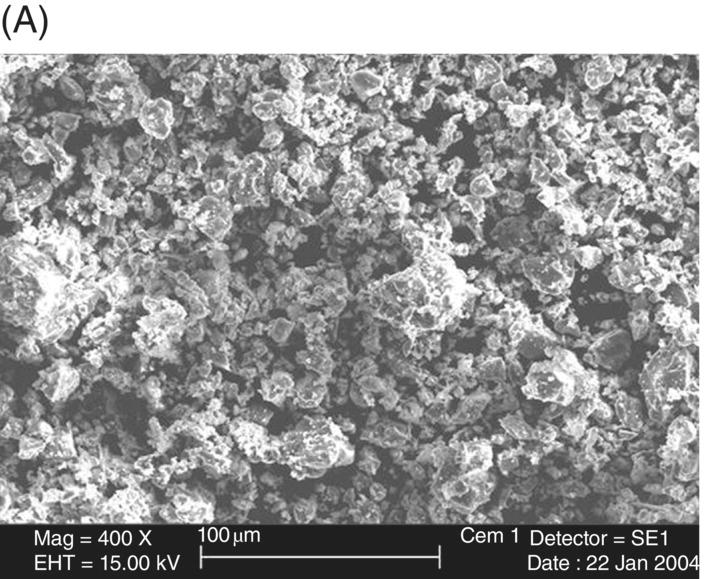
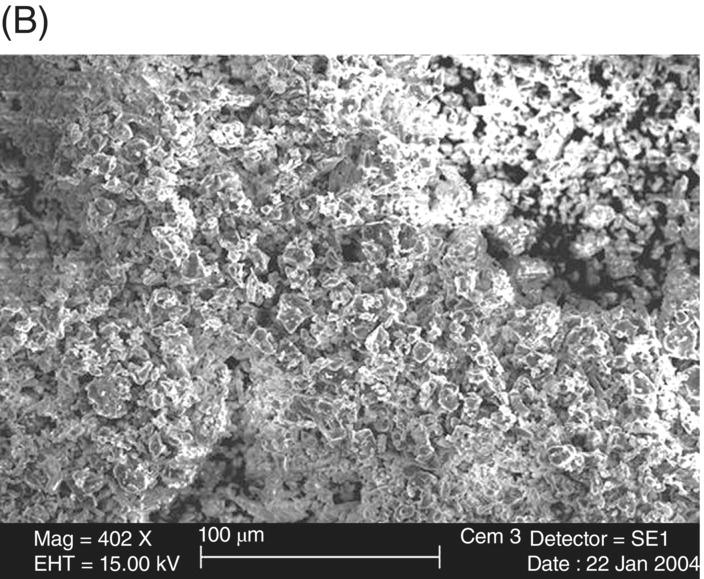
Fig. 2.4 Scanning electron micrograph comparison of (A) Portland cement and (B) MTA powders.
Source: Dammaschke et al. 2005. Reproduced with permission of Elsevier.
Trace elements and compounds
Several researchers have noted the absence of iron in white MTA in contrast to its presence in gray MTA (Camilleri et al. 2005; Song et al. 2006). However, others have observed trace amounts of iron in white MTA (Belío-Reyes et al. 2009). Additionally, magnesium (or a magnesium oxide form) is also frequently observed in greater proportion in gray MTA than in white MTA (Song et al. 2006), and also accounts for some of the color difference. Other elements and compounds observed in MTA have been: As, Ba, Cd, Cl, Cr, Cu, Ga, In, K, Li, Mn, Mo, Ni, P2O5, Pb, Sr, TiO2, Tl, V, and Zn (Funteas et al. 2003; Dammaschke et al. 2005; Monteiro Bramante et al. 2008; Comin-Chiaramonti et al. 2009; Chang et al. 2010; Schembri et al. 2010). While some of these elements would generally be of concern from a toxicological point of view, given their low concentration in MTA and MTA’s excellent biocompatibility, they likely have no impact on health. Although calcium hydroxide is a reaction product, as mentioned below, some does appear in MTA powder, possibly due to reaction with ambient humidity (Camilleri 2008; Chedella & Berzins 2010). Compared with Portland cement, MTA typically has less heavy metal content (Cu, Mn, Sr) (Dammaschke et al. 2005) but greater amounts of bismuth (as Bi2O3 for radiopacity), and, therefore, its Portland cement component is of purer form. Although it has been debated in the literature whether a clinician could use Portland cement in place of MTA due to its general similarities, it should be pointed out again that MTA is approved for use in patients by the FDA and is sterilized. Thus, substituting Portland cement for MTA is not advised in clinical procedures.
SETTING REACTIONS
MTA is a hydraulic type of cement, meaning that it sets by reacting with water, and is then stable in water. When mixed with water, it forms via an exothermic reaction. The setting reactions in MTA are approximated to be similar to those in Portland cement, which are best studied by analyzing the hydration of its individual components. The two most important hydration reactions are those of the greatest constituents, tricalcium silicate and dicalcium silicate. Tricalcium silicate sets via the following reaction (Bhatty 1991; Ramachandran et al. 2003):

The setting of dicalcium silicate is similarly given by the following reaction (Bhatty 1991; Ramachandran et al. 2003):

The principal products are calcium silicate hydrates and calcium hydroxide (also known as Portlandite). While the calcium hydroxide is mostly crystalline and able to be detected using X-ray diffraction (XRD; Camilleri 2008), the calcium silicate hydrates are primarily amorphous and may exhibit a range of compositions. Thus, water is both a reactant and is contained in the reaction products of MTA. This is important for understanding the effects of water on properties as discussed below. The calcium silicate hydrate may be considered a gel that forms on the calcium silicate particles and hardens with time to form a solid network with the calcium hydroxide nucleated within the pore and void space (Gandolfi et al. 2010b). The amount of calcium hydroxide produced in MTA has been found to be approximately 10–15% of the hydrated material (Camilleri 2008; Chedella & Berzins 2010), which is below that expected for Portland cement (20–25%; Ramachandran et al. 2003). Furthermore, exposure of the calcium hydroxide to carbon dioxide contained in physiological fluids is expected to convert some of it to calcium carbonate (Chedella & Berzins 2010; Darvell & Wu 2011).
The hydration reactions of the two minor components of Portland cement are influenced by gypsum. In the presence of gypsum and water, tricalcium aluminate forms ettringite [Ca6(AlO3)2(SO4)3 ∙ 32H2O] according to the following reaction:

Related posts:
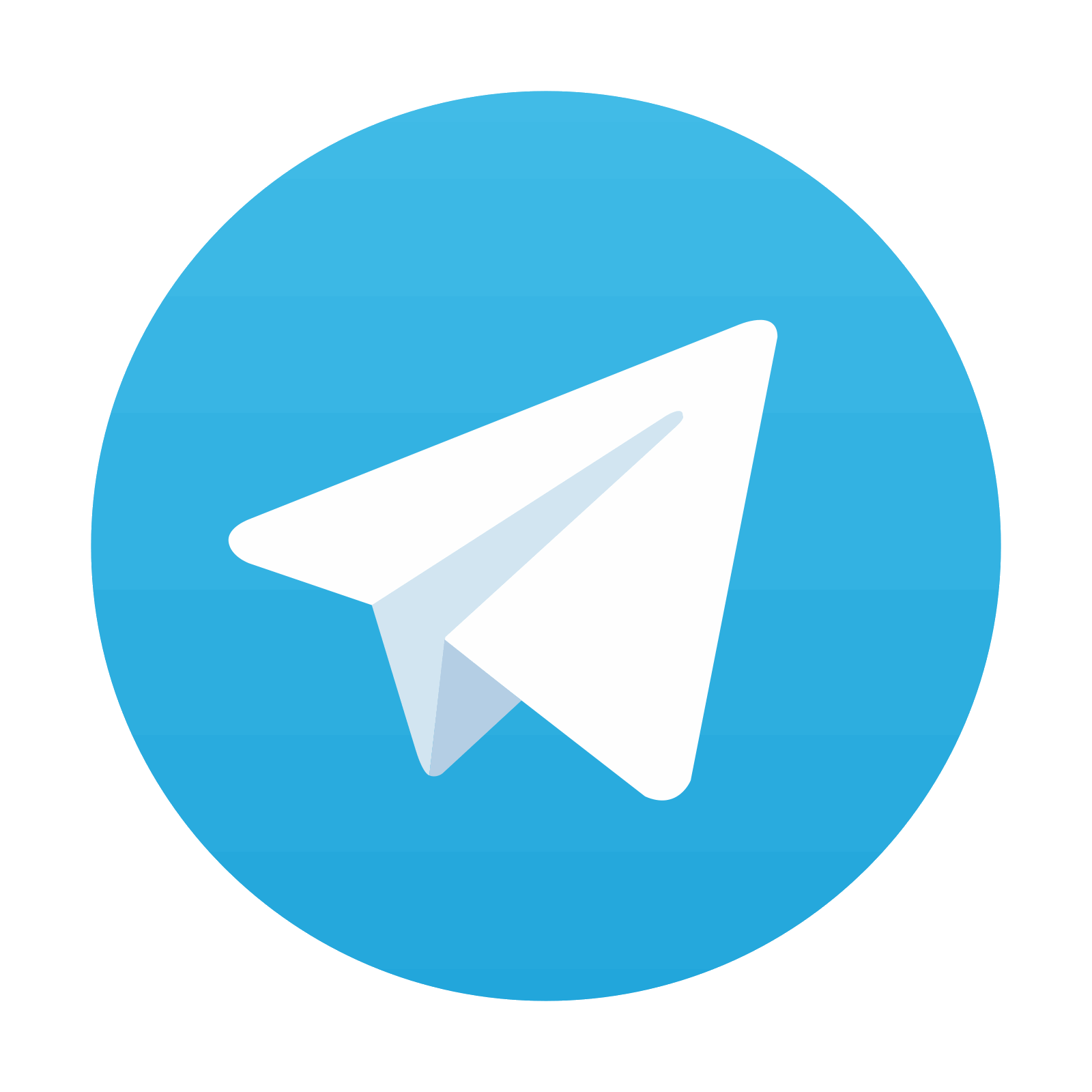
Stay updated, free dental videos. Join our Telegram channel

VIDEdental - Online dental courses
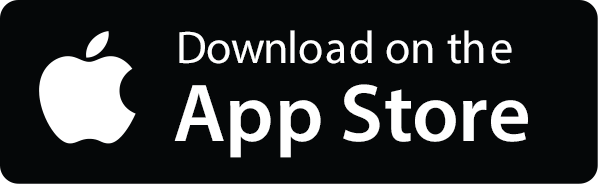
