Introduction
Understanding the biologic requirements of orthodontic patients requires proper characterization studies of new archwire alloys. The aims of this study were to evaluate properties of wires made of 2 new materials and to compare their properties with those of stainless steel.
Methods
The sample consisted of 30 straight lengths of 3 types of wires: stainless steel, titanium-molybdenum alloy, and beta-titanium alloy. Eight properties were evaluated: wire dimension, edge bevel, composition, surface characteristics, frictional characteristics, ultimate tensile strength (UTS), modulus of elasticity (E), yield strength (YS), and load deflection characteristics. A toolmaker’s microscope was used to measure the edge bevel, and x-ray fluorescence was used for composition analysis. Surface profilometry and scanning electron microscopy were used for surface evaluation. A universal testing machine was used to evaluate frictional characteristics, tensile strength, and 3-point bending.
Results
Stainless steel was the smoothest wire; it had the lowest friction and spring-back values and high values for stiffness, E, YS, and UTS. The titanium-molybdenum alloy was the roughest wire; it had high friction and intermediate spring-back, stiffness, and UTS values. The beta-titanium alloy was intermediate for smoothness, friction, and UTS but had the highest spring-back.
Conclusions
The beta-titanium alloy with increased UTS and YS had a low E value, suggesting that it would have greater resistance to fracture, thereby overcoming a major disadvantage of titanium-molybdenum alloy wires. The beta-titanium alloy wire would also deliver gentler forces.
Tooth movements and the associated changes are the result of an applied force system and the tissue response to it. Orthodontic wires, which generate the biomechanical forces, communicate through brackets for tooth movement and are central to the practice of orthodontics. Changes in the field of mechanotherapy have largely been made possible by new orthodontic materials. Selecting the appropriate archwire requires a thorough knowledge of the biomechanical and clinical applications of various archwires.
Archwire alloys require proper characterization to predict their outcome when used clinically. Most of the time, the exact compositions and material properties are not specified and, in some cases, are even not available from the manufacturers. Evaluating tensile properties, bending characteristics, frictional characteristics, and surface properties are the initial steps toward understanding archwire behavior in clinical situations and are integral to archwire alloy characterization.
Titanium-based alloys have gained immense popularity over the years, mainly with the introduction of nickel-titanium and beta-titanium (TMA), with titanium’s superior properties of biocompatibility, corrosion resistance, and low stiffness. Garner et al reported that stainless steel (SS) provided significantly less frictional resistance than nitinol and TMA. They suggested that, when high stiffness was required during sliding mechanics, SS should be used over nitinol or TMA. Burstone and Goldberg reported that the modulus of elasticity (E) of TMA is approximately twice that of nitinol and less than half that of SS. Its stiffness makes it ideal in applications where less force than steel is required but the lower modulus would be inadequate to develop required force magnitudes. Furthermore, Kapila and Sachdeva stated that the relatively low forces generated by TMA wires would imply that the counterproductive forces generated by TMA wires can be counteracted by smaller forces that those required for SS wires.
Although various archwire alloys are available for retraction of teeth, SS archwires have always been the mainstay for this phase of treatment. Titanium-based archwires, also used for this purpose, are available in various forms and brands. TMA, for example, has an excellent balance of properties, including high spring-back, low stiffness, high formability, and the ability of direct welding. However, a major drawback is its high coefficient of friction. Also, some batches of TMA archwires are susceptible to fracture during clinical manipulation. TMA wires demonstrate higher levels of bracket wire friction than SS or cobalt-chromium wires.
In the past few years, a relatively new entrant, Connecticut new archwire (CNA), a beta-titanium alloy, has gained immense popularity. However, little information is available in the orthodontic literature regarding its mechanical properties. The aims of this study were therefore to evaluate and compare the following properties: wire dimensions, edge bevel, composition, surface characteristics, frictional characteristics, ultimate tensile strength (UTS), E, yield strength (YS), and load deflection characteristics of 3 wires used in orthodontics: SS, TMA, and CNA.
Material and methods
Thirty straight lengths of each wire brand were divided into group I, SS (Ortho Organizers, Carlsbad, Calif); group II, TMA (SDS Ormco, Glendora, Calif); and group III, beta CNA (Ultimate Wireforms, Bristol, CT, USA; Libral Traders, Delhi, India).
The wire dimension used in this study for all types was 0.43 × 0.64 mm (0.017 × 0.025 in), and the wires were tested under similar conditions.
The height and width of each wire were measured to the nearest 0.001 mm with a digital micrometer accurate to ±1 μm (Mitutoyo, Kyoto, Japan). Five wires were taken from each group, a total of 15 readings with 3 such readings along each segment were measured, and the arithmetic mean was used in the subsequent calculations.
The transverse section of wire from each specimen was viewed with a tool maker’s microscope (Mitutoyo) with 150 times magnification, measured to the nearest 5 μ, and readings were taken. The values were fed into software (version 2000, Auto CAD, Autodesk, CA, USA) from which cross-sectional dimensions and the radius of the edge bevel were obtained. All 4 corners were measured, and, from these measurements, the mean was calculated.
The various wire specimens were examined by using x-ray fluorescence spectroscopy (Alpha-2000, serial number 8325, Innov-X Systems, Woburn, Mass) to evaluate the composition of the wires.
Surface roughness measurements of each wire were made with a surface profilometer (Taly surf 50 profilometer, FTSI-6960, and Ultra Analysis program, version 5.5.4.20, Taylor Hobson, Leicester, United Kingdom) with speeds of 0.5 mm per second (0.02 in/s) along the length of the 0.64-mm side over a distance of 10 mm. Proprietary software was used to calculate the arithmetic average roughness, Ra (the arithmetic mean of the absolute departures of the roughness profile from the mean line) and Rz (the maximum peak-to-valley height of the roughness profile).
Surface characteristics were studied with a scanning electron microscope (SEM) (QUANTA 200, FEI, Eindhoven, Netherlands).
Frictional measurements were made with a universal testing machine (Autograph AG 2000G, Schimadzu, Kyoto, Japan) with a 400-kg load cell at a crosshead speed of 10 mm per minute set in standard tensile mode and force levels required to pull the wire through the bracket (022 × 028-in slot, Gemini maxillary right first premolar bracket, Roth prescription, 3M Unitek, Monrovia, Calif), which was fixed on a metal sheet. The archwires were ligated by using 0.012-in elastomeric ligatures. The archwire and bracket were tested so that a new wire and a new bracket with fresh ligation were used for each combination and then discarded to eliminate the influence of wear.
Sample wires from each group were pulled through the bracket by a distance of 20 mm, the force levels needed for the movement of the wire were recorded from the digital readout, and the average was calculated. All tests were conducted in dry conditions.
We tested the mechanical properties as follows. A standard tensile test with each archwire from the 3 groups was performed in the universal testing machine. A full-scale load of 1000 N was set in the machine with a crosshead speed of 1 mm per minute. The span of the wire between the grips was standardized at 40 mm. The load taken to break the wire divided by the cross-sectional area of the wire gave the value for UTS. Young’s modulus (E) was then calculated from the load deflection data obtained from the tensile testing.
For the load deflection test, the wire samples from each group were tested by using a specially made 3-point wire-testing jig attached to the testing machine. The load deflection characteristics were evaluated by a 3-point bend test described by Miura et al and modified by Krishnan and Kumar.
Statistical analysis
A standard statistical software package (version 10, SPSS, Chicago, Ill) was used for data analysis. Absolute and percentage mean errors, standard deviations, and 95% confidence levels were calculated. The Kruskal-Wallis 1-way analysis of variance (ANOVA) was used to calculate the P values. The Mann-Whitney U test was used to identify the significant groups at the 5% priori level of significance ( P ≤0.05).
Results
The results of the measurements for wire dimensions and edge bevels are given in Table I . There were highly significant differences in height of the wires between groups I and II, and groups II and III ( P <0.001) but no significant difference between groups I and III ( P >0.05). There were highly significant differences in the widths of the wires between groups I and II, and groups I and III ( P <0.001) but no significant difference between groups II and III ( P >0.05). There were also highly significant differences in the edge bevel between groups I and II, and groups II and III ( P <0.001) but no significant difference between groups I and III ( P >0.05).
Group | Measured dimensions | Difference | ||||||
---|---|---|---|---|---|---|---|---|
Stated wire dimensions | Height | Width | Height | Width | Edge bevel | |||
Height | Width | Mean ± SD | Mean ± SD | Mean ± SD | Mean ± SD | Mean ± SD | P value | |
SS | 0.4318 | 0.635 | 0.4333 ± 0.0025 | 0.6387 ± 0.0031 | 0.0015 ± 0.0003 | 0.0038 ± 0.0005 | 0.0616 ± 0.0045 | 0.001 |
TMA | 0.4318 | 0.635 | 0.4252 ± 0.0031 | 0.6263 ± 0.0057 | 0.0066 ± 0.0031 | 0.0088 ± 0.0031 | 0.0786 ± 0.0065 | |
CNA | 0.4318 | 0.635 | 0.4333 ± 0.0025 | 0.6304 ± 0.0060 | 0.0015 ± 0.0006 | 0.0046 ± 0.0007 | 0.0582 ± 0.0008 |
The CNA wires had more titanium but less molybdenum, zirconium, and tin ( Table II ).
Group | Composition (%) | Sum | ||||||
---|---|---|---|---|---|---|---|---|
Iron | Chromium | Nickel | Titanium | Molybdemun | Zirconium | Tin | ||
SS | 72.39 | 18.17 | 9.02 | 0 | 0 | 0 | 0 | 99.58 |
TMA | 0 | 0 | 0 | 78.4 | 11.33 | 6.28 | 4.05 | 100.06 |
CNA | 0 | 0 | 0 | 80.75 | 9.78 | 5.75 | 3.78 | 100.06 |
Surface roughness measurements with surface profilometry ( Table III ) showed a highly significant difference between the 3 groups ( P <0.001). The surface topography evaluation of the wires with SEM photomicrographs showed that the SS wire ( Figs 1, A , 2, A , 3, A , and 4, A ) was the smoothest, and the TMA wire ( Figs 1 , B , 2 , B , 3 , B, and 4 , B ) was the roughest, whereas the CNA wire ( Figs 1 , C , 2 , C , 3 , C , and 4 , C ) was intermediate.
Group | Surface roughness-Ra Mean ± SD |
Surface roughness-Rz Mean ± SD |
|
---|---|---|---|
Group I | 0.0286 ± 0.0030 | 0.2788 ± 0.016 | 0.0001 |
Group II | 0.2321 ± 0.0082 | 1.9541 ± 0.033 | |
Group III | 0.1739 ± 0.0015 | 1.7945 ± 0.063 |
The results of frictional characteristics are given in Table IV . There were highly significant differences in static friction between the 3 groups and in kinetic friction between groups I and II ( P <0.001), and significant differences between groups II and III, and groups I and III ( P <0.05).
Group | Static friction Mean ± SD (g) |
Kinetic friction Mean ± SD (g) |
P value |
---|---|---|---|
Group I | 0.783 ± 0.003 | 0.729 ± 0.007 | 0.0001 |
Group II | 1.02 ± 0.006 | 0.970 ± 0.020 | |
Group III | 0.87 ± 0.022 | 0.835 ± 0.011 |
The results of E, YS, UTS, and YS:E are given in Table V . There were highly significant differences in E, UTS, and YS between groups I and II, and groups I and III ( P <0.001) but no significant difference between groups II and III ( P >0.05). There was a highly significant difference in the stiffness strength between groups I and II, and groups I and III ( P <0.001), but no significant difference between groups II and III ( P <0.05).
Wire | Flexural modulus of elasticity (E) (GPa) Mean ± SD |
0.2% offset yield strength (YS) (Mpa) Mean ± SD |
Ultimate tensile strength (UTS) (Mpa) Mean ± SD |
Tensile modulus of elasticity (GPa) Mean ± SD |
Stiffness (YS:E) Mean ± SD |
P value |
---|---|---|---|---|---|---|
Group I | 194.33 ± 11.15 | 1886.33 ± 23.86 | 2047.67 ± 50.64 | 176 ±13.53 | 0.0097 ± 0.00046 | 0.0001 |
Group II | 81 ± 6.56 | 1116.67 ± 93.78 | 1180 ± 85.56 | 79 ± 5 | 0.0138 ± 0.00025 | |
Group III | 73 ± 4.00 | 1156.33 ± 54.15 | 1287 ± 52.85 | 73.33 ± 4.93 | 0.0158 ± 0.00089 |
The results of the load deflection characteristics are given in Table VI . There were highly significant differences in the load deflection characteristics during loading at 0.5 mm between groups I and II, and groups I and III ( P <0.001) but no difference between groups II and III ( P >0.05). There were highly significant differences in the load deflection characteristics during loading at 1 mm between all groups ( P <0.001). There were also highly significant differences in the load deflection characteristics during unloading at 0.5 mm between groups I and II, and groups I and III ( P <0.001), and a significant difference between groups II and III ( P <0.05).
Sample | Mean ± SD (g) | P value |
---|---|---|
0.5 mm loading | ||
Group I | 2350 ± 91.65 | 0.0001 |
Group II | 1627 ± 55.08 | |
Group III | 1437 ± 41.63 | |
1 mm loading | ||
Group I | 3480 ± 115.33 | 0.0001 |
Group II | 2697 ± 116.76 | |
Group III | 2143 ± 50.32 | |
0.5 mm unloading | ||
Group I | 947 ± 58.6 | 0.0001 |
Group II | 1323 ± 61.1 | |
Group III | 1507 ± 55.07 |
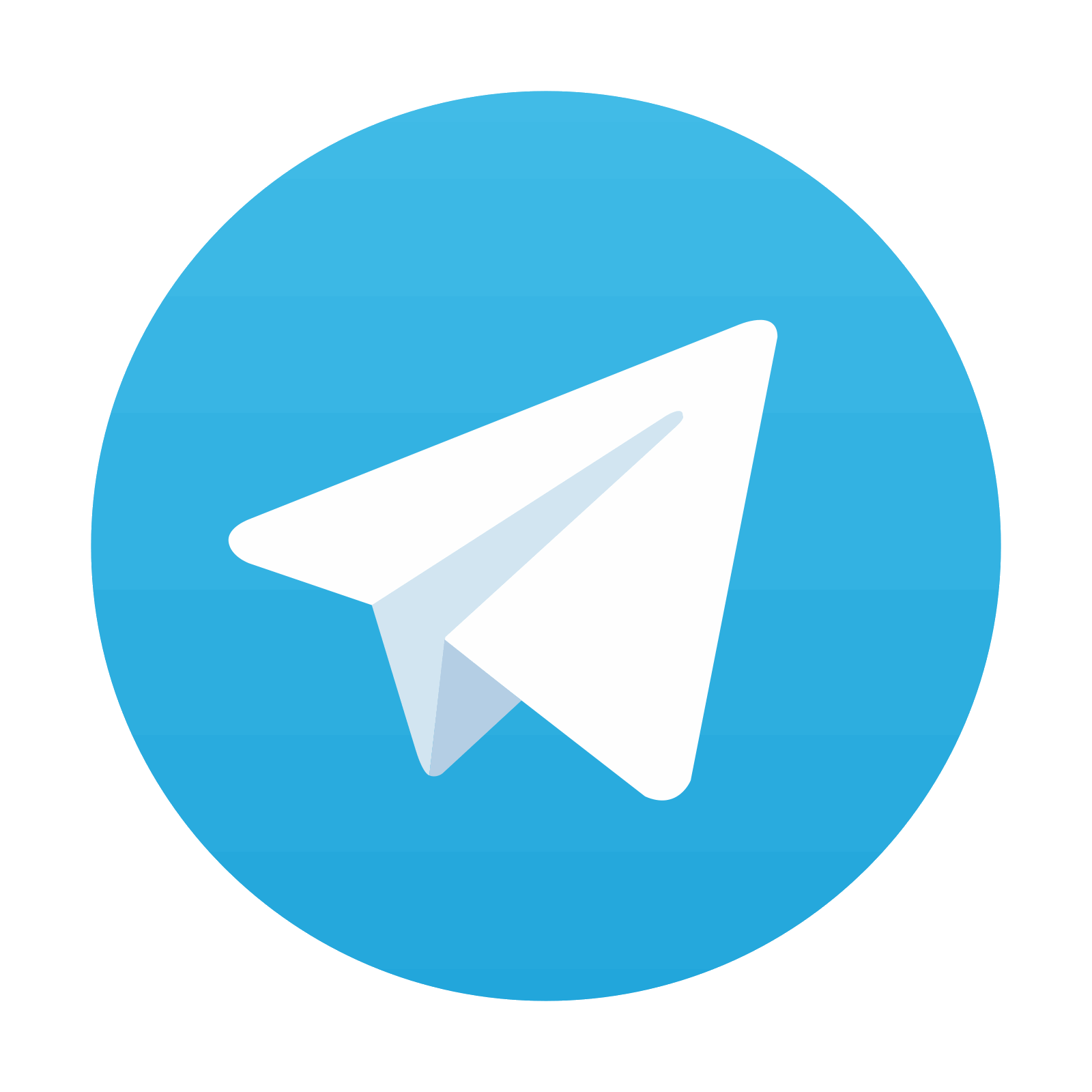
Stay updated, free dental videos. Join our Telegram channel

VIDEdental - Online dental courses
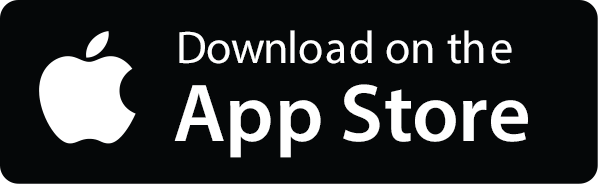

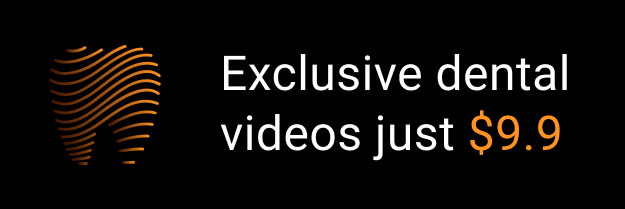