Highlights
- •
Contemporary CAD/CAM resin composites display different degrees of water sorption.
- •
Fracture toughness is importantly degraded by water ageing in all materials.
- •
Some resin composites display a better tolerance to strength degradation in water.
- •
Susceptibility to subcritical crack growth shows a high material dependency.
Abstract
Objective
The aim of the present study was to assess the effect of water storage on the quasi-static properties and cyclic fatigue behavior of four contemporary CAD/CAM resin composite materials.
Methods
The CAD/CAM resin composites Grandio Blocs, Lava TM Ultimate, Cerasmart TM and Brilliant Crios, as well as the direct resin composite Grandio SO, were evaluated. Rectangular plates were cut from the blocks or fabricated using a silicon mold to obtain specimens for fracture toughness ( K Ic , n = 10), biaxial strength ( σ 0 , n = 30) and cyclic fatigue testing (n = 30). Half of the specimens was stored for 24 h in dry conditions and the other half was aged for 60 days in distilled water at 37 °C. K Ic was determined using the Compact-Tension (C(T)) method and σ 0 and cyclic fatigue were tested using the Ball-on-Three-Balls assembly. Additional disc-shaped specimens (n = 5) were produced to obtain water sorption curves of the materials. Weibull statistics and two-way ANOVA with Tukey’s post-hoc test were used for data assessment.
Results
The highest water sorption was observed for Lava TM Ultimate (42.6 μg/mm 3 ), whereas Grandio SO displayed the lowest uptake (14 μg/mm 3 ). A statistically significant drop in K Ic and σ 0 was measured for all materials after water storage, except for the σ 0 of Cerasmart TM . Water ageing had a dissimilar effect on the cyclic fatigue behavior, increasing the slow crack growth susceptibility of Lava TM Ultimate, but decreasing it for Cerasmart TM and Brilliant Crios.
Significance
Contemporary CAD/CAM resin composites are susceptible to water driven degradative processes, although differences in filler content and resin matrix constitution play an important role in how it impacts their mechanical properties.
1
Introduction
Among technological advances incorporated to dentistry in the last decades, computer-aided design and manufacturing (CAD/CAM) of restorations has shown one of the most noticeable growths, causing a complete revolution in the dental laboratory workflow [ ]. This sustained expansion has been enabled to a large extent by the adaptation of dental materials to the requirements of the milling process. Originally developed for glassy materials [ ], CAD/CAM systems cover at present the entire restorative spectrum, including various types of metal alloys, polycrystalline ceramics, such as zirconia, as well as glass-ceramics and reinforced glass matrices. In recent years, the dental industry has also strongly promoted the use of resin composite for the fabrication of machined restorations, opening a new market niche for this material. Its indication for indirect restorations is, however, not a new concept. Laboratory resin composites were first launched during the early 1980’s [ ], seeking to enhance monomer conversion, as well as to reduce polymerization shrinkage stress on the adhesive interfaces. The application of post-curing mechanisms in specialized polymerization units, at higher temperatures and under higher pressure, allowed a substantial increase in the mechanical properties of these materials, mainly due to a increment in the conversion rate of the polymer network [ ]. Still, limited by inherent disadvantages of hand-built techniques (i.e. pores, inhomogeneities, etc.), their indication was restrained to partial restorations (inlays, onlays) and veneering of metallic frameworks. The advent of CAD/CAM technologies allowed the manufacturers to produce highly polymerized materials under industrial environments, further increasing monomer conversion rates and thus, mechanical properties [ ]. Moreover, the lower hardness and brittleness displayed by resin composite blocks when compared to ceramic and glassy materials, favors the machining process, as less wear of the milling tools [ ] and absence of material chipping [ ] has been reported.
Despite the good mechanical properties measured in vitro for resin composite blocks [ ], their clinical performance is conditioned to an adequate chemical stability in water environments. Polydimethacrylate-based resin matrices absorb water due to the presence of voids and defects between the polymer chains [ ], as well as a result of the hydrophilic nature of groups and bonds in the polymer network [ ]. Thus, shortly after water immersion, swelling and plasticization processes take place, causing a general reduction in the mechanical properties of the material [ ]. In addition, water molecules are responsible for hydrolytic degradation of siloxane bonds between the matrix and the filler particles, leading to interfacial debonding during crack propagation [ ]. The industrial curing process of CAD/CAM resin composite materials enhances the cross-linking density of the polymer network and reduces the presence of pores and voids [ ]. This enhanced matrix properties, in conjunction with a larger filler fraction, theoretically limit the extent of water sorption of these new materials [ ], preserving them, suggestively, from chemical and mechanical degradation over time. However, only scarce information regarding their mechanical performance in aqueous environments is available in the literature. Therefore, the aim of the present study was to determine the water sorption of four contemporary CAD/CAM resin composite materials and to assess its impact on their fracture toughness, biaxial flexural strength, as well as cyclic fatigue behavior. A direct light-polymerized resin composite was use as a control group.
2
Material and methods
2.1
Materials and sample preparation
Four commercial resin composite materials intended for CAD/CAM processing and one direct resin composite were used in the present study. Their polymer matrix composition, as well as filler characteristics and content are presented in Table 1 . For strength and fatigue specimens, CAD/CAM blocks were first ground square with a fine diamond wheel (D46) to obtain 12 × 12 mm cross sections. Plates were then cut from the blocks using a precision cutting machine (IsoMet 5000, Buehler, Illinois, USA) under constant water irrigation and then ground parallel on both sides with the diamond wheel. Fine polishing was conducted on one side with SiC paper (P600 to P4000) to obtain specimens with a final thickness of 1.20 ± 0.05 mm. For fracture toughness specimens, the blocks were ground rectangular with cross sections of 12 × 12.5 mm and then sawed with a 0.1 mm diamond disc along the center of one of their narrow long sides. The obtained pre-notch was further sharpened with multiple razor blades lubricated with 9 to 0.5 μm Al 2 O 3 polishing pastes in a notching machine (Karg Industrietechnik, Germany). The final depth of this notch ranged between 7.0–8.0 mm, depending on the final specimen configuration ( Fig. 1 A). The razor blade cut had a minimum depth of 1.5 times the radius produced by the 0.1 mm-thick diamond disc pre-notch root, creating a final notch radius that ranged between 5-10 μm. Specimens with a 2.5 mm thickness were cut from the notched blocks and the fixing holes were then drilled using a diamond bur ( Fig. 1 A). Further details on this method can be found elsewhere [ ].
Material | Description | Fillers | Filler content | Matrix monomers |
---|---|---|---|---|
Grandio SO | Nano-hybrid direct resin composite | 0.5–3 μm glass ceramic particles | 89 wt %/73 vol % | Bis-GMA, Bis-EMA, TEGDMA |
Voco, Cuxhaven, Germany | 0–40 nm SiO 2 nanoparticles | |||
Grandio Blocs | Nano-ceramic hybrid CAD/CAM block | 0.5–3 μm glass ceramic particles | 86 wt %/71 vol% | Bis-GMA, Bis-EMA, TEGDMA |
Voco, Cuxhaven, Germany | 0–40 nm SiO 2 nanoparticles | |||
Lava TM Ultimate | Resin nano-ceramic CAD/CAM block | 20 nm SiO 2 and 4−11 nm ZrO 2 nanoparticles | 80 wt %/65 vol % | Bis-GMA, UDMA, Bis-EMA, TEGDMA |
3M, Seefeld, Germany | 0.6−10 μm silica and zirconia nanoclusters | |||
Cerasmart TM | Hybrid ceramic CAD/CAM block |
300 nm barium glass and 20 nm SiO 2 nanoparticles | 71 wt %/55 vol% | UDMA, Bis-MEPP, DMA |
GC, Leuven, Belgium | ||||
Brilliant Crios | Reinforced composite CAD/CAM block | <1 μm barium glass and <20 nm SiO 2 nanoparticles | 70.7 wt %/51.5 vol % | Bis-GMA, Bis-EMA, TEGDMA |
Coltene, Altstätten, Swizerland |

Grandio SO specimens were produced by inserting the material into silicon molds with respectively 12 × 12 × 1.5 mm and 12 × 12.5 × 2.5 dimensions. Glass slides on top and bottom of the molds were fixed with metal clamps and the material was light polymerized on both sides in nine overlapping points, each 20 s, as recommended in ISO 4049 [ ], using a halogen-curing unit with a 750–800 mW/cm 2 energy output (Elipar TriLight 3M, Seefeld, Germany). Strength and fatigue specimens were then ground parallel and fine polished on one side (P600 to P4000) to obtain 1.20 ± 0.05 mm thick plates. Fracture toughness samples were mounted together and notched following the protocol described above.
Specimens for the determination of water sorption were obtained by grinding the CAD/CAM blocks round with a fine diamond bur to a final circular cross-section of Ø = 12.00 ± 0.1 mm and then trimming 1.40 mm thick discs. After grinding them parallel, fine polishing (P1000) was conducted on both sides, leading to a final specimen thickness of 1.00 ± 0.05 mm. A disc-shaped metal mold was used to produced Grandio SO specimens, following a similar protocol as that described for mechanical testing samples.
A total of 145 specimens (60 for strength, 60 for fatigue, 20 for fracture toughness and 5 for water sorption) were produced for each material.
2.2
Water sorption
Water sorption was determined according to the ISO 4049 standard [ ]. After a 24 h storage in a desiccator at 37 °C, specimens were repeatedly weighted using a digital balance (R 160 P, Santorius Research GmbH, Göttingen, Deutschland) until a constant value (<0.1 mg variation) was obtained. This initial weight was termed m 1 . Aging was conducted in individual containers filled with distilled water. Specimens were weighted after 1, 2, 4, 6, 24, 30, 48, 54, 72 and 96 h, and then after 7, 10, 14, 21 and 60 days, strictly following the protocol described in the ISO 4049 standard. Each of these values ( m 2 ) were used to calculate the mass gain (μg/mm 3 ) at the different time intervals:
2.3
Fracture toughness testing ( K Ic )
The compact tension C(T) test was used for the determination of fracture toughness, according to the ASTM E1820-13 [ ]. The notch length a i was measured in a stereomicroscope and corresponded to the distance between the center of the holes and the notch tip ( Fig. 1 A). Half of the specimens of each material (n = 10) was aged in distilled water at 37 °C for 60 days, whereas the other half was stored overnight in a desiccator at 37 °C. Testing was conducted in a universal testing machine (Model Z2.5, Zwick/Roell, Ulm, Germany) at a 1 mm/min loading rate. The alignment of the specimens was carefully controlled through a camera system coupled to the machine axis, to avoid tilting during pre-loading. The maximum load at failure P was used to calculate fracture toughness using [ ]:
KIc=PBW1/2fai/W
with B the specimen width, W the distance between the center of the holes and the back edge of the specimen ( Fig. 1 A) and:
fai/W=2+aiW0.886+4.6aiW-13.32aiW2+14.72aiW3-5.6aiW41-aiW3/2
2.4
Inert strength and fatigue testing
Biaxial strength and fatigue tests were conducted using the ball-on-three-balls (B3B) test ( Fig. 1 B) with a specially designed assembly for the plate geometry of the specimens [ ]. The thickness ( t ) at the sample’s center was measured with a digital rounded-tip dial gage with resolution 0.002 mm (ID-C112XB, Mitutoyo Corp, Japan). Half of the specimens for strength and fatigue (n = 30) was tested after 24 h storage in a desiccator at 37 °C. The other half was stored in distilled water at 37 °C for 60 days prior to mechanical testing.
Biaxial strength tests were carried out in the universal testing machine at a cross-head speed of 1.2 mm/min, with the specimen’s polished surface loaded in tension. The maximum load at fracture ( P ) was used to calculate the biaxial strength ( σ ) according to [ ]:
σ=fτ,νPt2
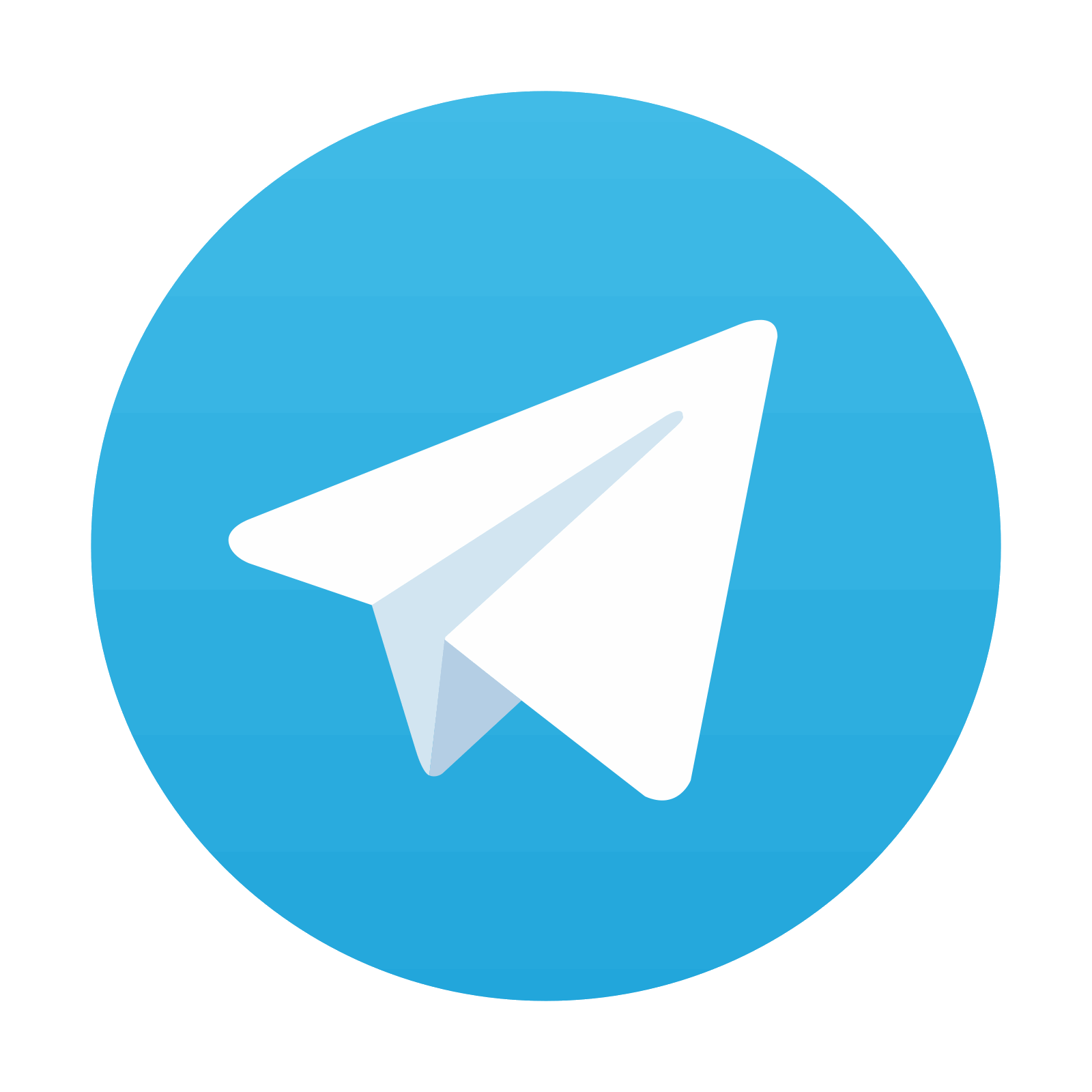
Stay updated, free dental videos. Join our Telegram channel

VIDEdental - Online dental courses
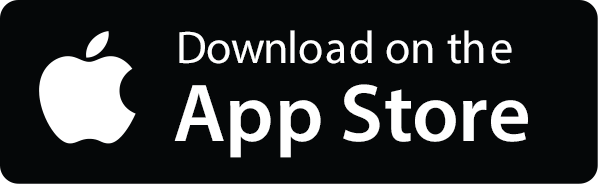

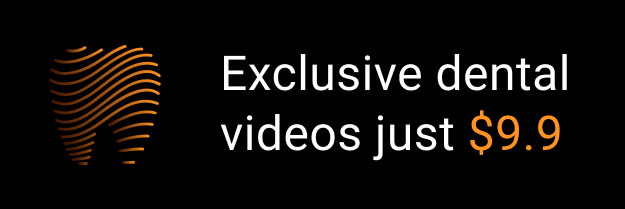