Abstract
Objective
The aim of this study was to assess the influence of surface treatments on the surface characteristics of different zirconia cores and the adhesion of the zirconia-veneering ceramic systems by means of strain energy release rate ( G -value, J/m 2 ).
Methods
Three types of zirconia cores (NANOZR (NZ), Vita In-Ceram YZ (VZ), and IPS e.max ZirCAD (IZ)) were used. The specimens were divided into four groups in each test according to the surface treatment used; Gr 1 (control; no treatment), Gr 2 (sandblasted), Gr 3 (CH 2 Cl 2 for 60 min), and Gr 4 (experimental hot etching solution for 60 min). AFM, SEM, EDS, and XRD were carried out. Two types of veneering ceramics (Vita VM9 (V9) and IPS e.max Ceram (IC)) were used for testing the adhesion. The G -value (J/m 2 ) was measured with a four-point bending configuration. Following fracture testing specimens were examined with SEM. Data were analyzed using ANOVA and Tukey’s test.
Results
NZ treated with the experimental hot etching solution showed the highest R a values (206.06 ± 9.98 nm) compared with the other groups ( P < 0.05). The greatest amount of monoclinic phase is measured after sandblasting (19.59%) for NZ, followed by VZ (9.3%) and IZ (6.6%). The NZ/V9 (etching for 60 min) group showed the highest G -value (36.02 ± 2.80 J/m 2 ) among the groups. Mode of failure was mostly cohesive failure within all the bonded veneering ceramic systems.
Significance
The experimental hot etching solution could be considered as alternative treatment modality to sandblasting for zirconia cores to avoid phase transition at the surface from tetragonal to monoclinic that may be detrimental for the longevity of the zirconia-veneering ceramic restoration.
1
Introduction
In the last 10–15 years, ongoing developments over the ceramic materials science for dental applications have result in a class of high strength materials; zirconia-based ceramics, which potentially provide enhanced fracture resistance and long-term viability as compared to porcelain and other silica-based materials . These properties have promoted the use of zirconia in a variety of dental applications; such as frameworks for all-ceramic posterior crowns and fixed partial dentures (FPDs) .
Utilization of zirconia, as a core material, has improved the mechanical strength and fracture toughness of all-ceramic restorations, allowing them to withstand intermittent forces that arise throughout mastication . On the other hand, zirconia copings for crowns or multi-unit frameworks still require application of veneering ceramics, typically specialized porcelain, to accomplish appropriate esthetics . Clinical failures of veneered zirconia FPDs due to veneer debonding, chipping, and/or fracture are reported to be 15% after an observation period of 2–5 years . Adhesion between zirconia core-veneering ceramic depends on several factors related to the two different material phases, including chemical bonding, mechanical interlocking, wetting properties and the degree of interfacial stress generated via thermal expansion mismatch and glass transition temperature differences . Continuous searching and developing of zirconia core materials along with appropriate veneering ceramics are required.
Yttria-partially-stabilized zirconia (Y-TZP) has been increasingly applied for FPDs. Y-TZP presented with high flexural strength; however, its fracture toughness is low along with low mechanical durability . A significant improvement in fracture toughness occurred by replacing yttria with ceria (Ce-TZP); however, the flexural strength is reduced . Ce-TZP alloyed with alumina (Al 2 O 3 ) (Ce-TZP/Al 2 O 3 ) in order to improve its low flexural strength whereas the fracture toughness remains high . It is composed of zirconia matrix with 10 mol% ceria and 30 vol% of nanoscale Al 2 O 3 as a second phase, called NANOZR. Ce-TZP/Al 2 O 3 nanocomposite has been suggested as a material for FPDs frameworks; as it could be processed on dental CAD/CAM machines like Y-TZP in the white state .
Up to now, there is no agreement regarding the efficient surface treatment method for achieving optimum bond strength between zirconia cores and veneering ceramics. It is essential to enhance the quality and bond strength between the veneer and the core ceramic; as they are the key factors in the success of bilayered restorations . It has been reported that surface treatments of zirconia, such as airborne-particle abrasion or the application of a liner, had a significant effect on bond strength . On the other hand, it is necessary to consider that airborne-particle abrasion may promote a phase transition at the surface, altering the crystal structure from tetragonal to monoclinic . The two different crystal structures reveal different coefficients of thermal expansion (CTE) ; accordingly, affecting the mechanical strength and most probably, the bonding capability of the material . In addition, liner application has been reported to weaken the bond strength between zirconia and veneering ceramics .
The nature of bonding between zirconia core materials and veneering ceramics still requires further investigation. The development of adequate surface treatment of zirconia core will enhance the adhesion and the success rate of FPDs . Consequently, the aim of this study was to determine the effect of different surface treatments on the surface properties of Y-TZP and Ce-TZP/Al 2 O 3 core materials and to investigate the outcomes of these treatments on the adhesion of different zirconia-veneering ceramic systems. The null hypotheses tested were that the use of surface treatments would not influence the surface properties of Y-TZP and Ce-TZP/Al 2 O 3 cores and would not affect the adhesion of different zirconia-veneering ceramic systems.
2
Materials and methods
2.1
Specimen preparation
Vita In-Ceram YZ (VZ; Vita Zahnfabrik, Bad Säckingen, Germany) and IPS e.max ZirCAD (IZ; Ivoclar-Vivadent, Schaan, Liechtenstein) plates were cut from pre-sintered blocks using water cooled low-speed diamond saw (Isomet, Buehler GmbH, Düsseldorf, Germany) to produce zirconia specimens with the required dimensions for each test. The zirconia plates were cut 20% bigger than the desired dimension considering its shrinkage and sintered at 1530 °C for 2 h in the Vita ZYrcomat furnace (Vita Zahnfabrik, Bad Säckingen, Germany). NANOZR (NZ; Panasonic-Denko, Osaka, Japan) specimens were received as plates from the manufacturer with the dimensions required for each test. The NZ was prepared by sintering mixed powders of Ce-TZP and Al 2 O 3 at 1440 °C for 4 h. The details of fabrication procedures have been described previously . The specimens from each zirconia core material were wet ground on one surface only, using 600-grit silicon carbide (SiC) paper (Leco Co., St. Joseph, MI, USA) and then cleaned in a sonic (Bandelin, Sonorex, Germany) bath filled with ethanol for 5 min. Then, the specimens in each test were divided into four groups according to the surface treatment that was performed as follows:
-
Group (1) : No treatment (control); the specimens were exposed only to grinding and cleaning as mentioned above.
-
Group (2) : Sandblasted; the specimens were abraded with Al 2 O 3 particles (110 μm) with a dental airborne-particle abrasion unit (Micro-Blaster; Daedong Industrial Co., Ltd., Daegu, Korea) that was applied for 20 s at a pressure of 2 bar with a distance of 15 mm between the nozzle and the surface.
-
Group (3) : The specimens were immersed in methylene chloride (CH 2 Cl 2 , formula weight: 84.13 g/mol, El Nasr Pharmaceutical Chemicals Co., Egypt) for 60 min.
-
Group (4) : Experimental hot etching solution; a solution with 800 mL of methanol, 200 mL of 37% HCl, and 2 g of ferric chloride (FeCl 3 ) was heated up to 100 °C in a water bath during the etching process . The zirconia specimens were immersed in the solution for 60 min .
Treated specimens were rinsed with distilled water and then cleaned in a deionized water bath for 10 min and gently air-dried.
2.1.1
Atomic force microscopy (AFM) evaluation
The surface microtopography of the sintered treated zirconia plates (10 mm × 10 mm × 1 mm) ( n = 5) was characterized by contact-mode AFM (Autoprobe CP-II, Veeco, CA, USA). The radius of curvature of the scanning tip was 10 nm. Images were recorded with a scan rate of 1 Hz at a resolution of 512 × 512 pixels per image and scanning area of 10 μm × 10 μm. The average surface roughness ( R a ) of the zirconia specimen after different treatments was recorded in nanometers (nm). R a for each specimen was measured at three different sites and the mean roughness average was then calculated. Surface roughness mean values were compared with two-way ANOVA considering two factors (surface treatment and type of zirconia core) and their interactions. Multiple comparisons were made by Tukey’s test. Statistical significance was set at the 0.05 probability level.
2.1.2
Scanning electron microscopy (SEM) evaluation
Three representative specimens from each group of the sintered treated zirconia plates (10 mm × 10 mm × 1 mm) were rinsed with 96% ethanol and air-dried, mounted on metallic stubs, sputtered (Sputter Coater S150A, Japan) with a gold layer and then examined under a SEM (JEOL, JXA-840A, JEOL Ltd., Tokyo, Japan) at 10,000× magnification, to observe the features of the treated surfaces.
2.1.3
Elemental composition
The elemental composition of the sintered treated zirconia plates (10 mm × 10 mm × 1 mm) ( n = 3) from each group was analyzed using energy dispersive X-ray spectroscopy (EDS; INCA, Oxford Instruments, Abingdon, England). Three different areas were selected for each specimen.
2.1.4
Phase composition
The zirconia surface (10 mm × 10 mm × 1 mm) ( n = 3) was analyzed by X-ray diffractometer (XRD; X’Pert Pro, Panalytical, The Netherlands) to determine the crystal phases of the sintered zirconia grains to quantify the monoclinic and tetragonal phases. Specimen surfaces were scanned with Cu Kα X-ray over an angular range of 20–65° in 2 θ degrees with a step size of 0.05° and 5 s step interval. The relative amount of the monoclinic phase ( X M ) was calculated as suggested by Garvie and Nicholson :
X M = I M ( 1 1 1 ) + I M ( 1 1 1 ¯ ) I M ( 1 1 1 ) + I M ( 1 1 1 ¯ ) + I T ( 1 0 1 )
where I is the intensity of the peak, M(1 1 1) corresponds to the monoclinic phase referring to the crystallographic plane (1 1 1), T(1 0 1) corresponds to the tetragonal phase referring to the crystallographic plane (1 0 1) and <SPAN role=presentation tabIndex=0 id=MathJax-Element-2-Frame class=MathJax style="POSITION: relative" data-mathml='M(111¯)’>M(111¯)M(111¯)
M ( 1 1 1 ¯ )
corresponds to the monoclinic phase referring to crystallographic plane <SPAN role=presentation tabIndex=0 id=MathJax-Element-3-Frame class=MathJax style="POSITION: relative" data-mathml='(111¯)’>(111¯)(111¯)
( 1 1 1 ¯ )
.
2.1.5
Strain energy release rate test
2.1.5.1
Specimen preparation
A total number of forty rectangular sintered specimens from each zirconia core material (30 mm × 8 mm × 1.5 mm) were prepared and divided into four test groups, according to the surface treatments that were applied ( n = 10). After that, the core specimens were veneered with the respective veneering ceramics as follows: NZ and VZ cores were veneered with Vita VM9 (V9; Vita Zahnfabrik, Bad Säckingen, Germany), while IZ core was veneered with IPS e.max Ceram (IC; Ivoclar-Vivadent, Schaan, Liechtenstein) using a specially designed split Teflon mold (30 mm × 8 mm × 1.5 mm) that allowed for veneer thickness (1.5 mm) control with a total specimen thickness of 3 mm. Then, the specimens were extruded from the mold and sintered following the respective manufacturer’s recommendations ( Table 1 ).
Veneering ceramic | Pre-drying | Heating rate (°C/min) | Firing temperature (°C) | Holding time (min) | |
---|---|---|---|---|---|
Temperature (°C) | Time (min) | ||||
Liner (vacuum during heating) | |||||
V9 | 500 | 6 | 55 | 930 | 1 |
IC | 400 | 4 | 60 | 960 | 1 |
First dentin firing (vacuum during heating) | |||||
V9 | 500 | 6 | 55 | 910 | 1 |
IC | 400 | 4 | 50 | 750 | 1 |
Second dentin firing (vacuum during heating) | |||||
V9 | 500 | 6 | 55 | 900 | 1 |
IC | 400 | 4 | 50 | 750 | 1 |
Glazing (no vacuum) | |||||
V9 | 500 | 0 | 80 | 900 | 1 |
IC | 400 | 6 | 60 | 725 | 1 |
2.1.5.2
Notching the specimen
The test specimens were notched across the width and entirely through the depth of the porcelain layer at the middle of the specimen using water cooled low-speed diamond saw on which a micrometer is attached which gave an accurate notch of width 0.4 mm and a depth of 1.5 mm (the thickness of porcelain). A small pre-crack was created at the zirconia-veneering ceramic system interface at the base of the notch then stored in kerosene to minimize the influence of water vapor on crack growth during testing . The specimens were tested in a four-point-bending jig mounted in a universal testing machine (Model TT-B, Instron Corp., Canton, MA, USA) with the inner rollers 14 mm and the outer rollers 26 mm. They were subjected to 2–3 load and partial unload reload cycles at a crosshead speed of 0.05 mm/min until the crack reached the inner rollers, beyond which the load increased. This approach measures the strain energy release rate associated with stable crack extension at the interface between bi-material plates .
The load at which stable crack extension occurred was collected for calculation of the strain energy release rate, G . The testing configuration shown in Fig. 1 illustrates the relationship between the specimen and the rollers of the four-point bending jig. The strain energy release rate, G , is given by :
G = η [ P 2 l 2 ( 1 − ν z 2 ) ] E z b 2 h 3
where P is the load to stably propagate the crack, l the moment arm or distance between inner and outer load line (rollers) on the same side, ν z and E z are Poisson’s ratio and elastic modulus of zirconia substrate (NZ; 0.3, 269 GPa, VZ; 0.32, 210 GPa, and IZ; 0.3, 200 GPa) respectively, and b and h are the specimen width and total thickness, respectively.

The non-dimensional parameter η is calculated with the all-dimensional parameters by:
η = 3 2 1 ( h z / h ) 3 − λ { ( h c / h ) 3 + λ ( h z / h ) 3 + 3 λ ( h c h z / h 2 ) [ ( h c / h ) + ( λ h z / h ) ] − 1 }
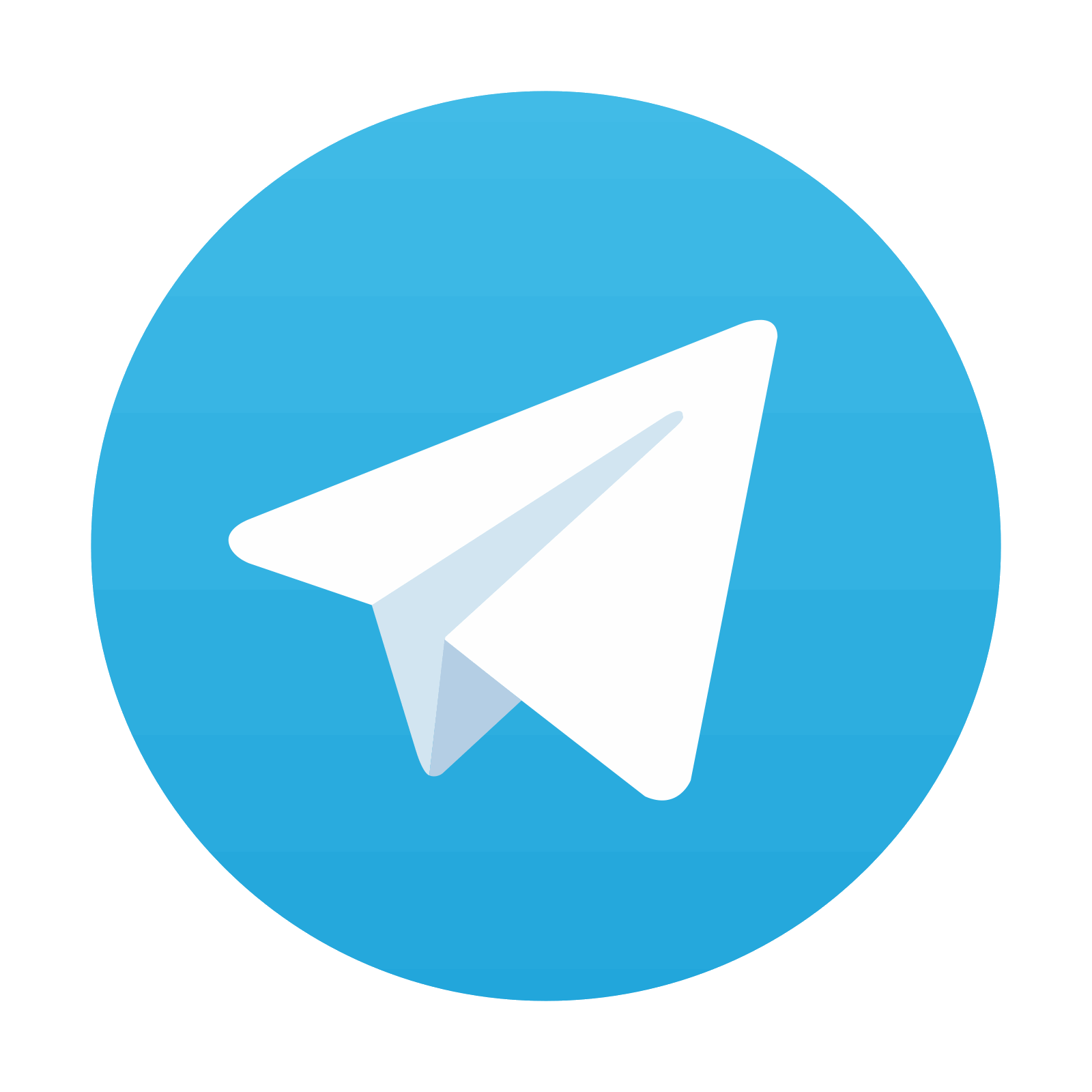
Stay updated, free dental videos. Join our Telegram channel

VIDEdental - Online dental courses
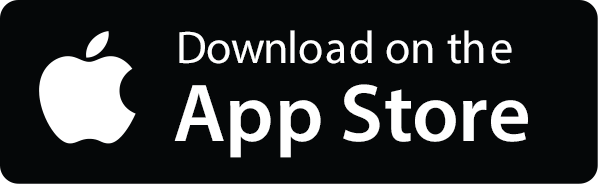
