Abstract
Objectives
To test the null hypothesis that polymerization-induced stress was not influenced by cavity dimensions and geometries.
Methods
Four experimental groups, with different C-factors and specimen volumes were defined using bottom-less glass disks (height: 1 or 2 mm) with a central hole 3 or 6 mm in diameter, and 3 mm wall thickness. Another four groups were created by bonding a glass plate to the bottom of the disks. Additionally, disks with 2-mm height, 3 mm in cavity diameter, and 4.5-mm thick walls were prepared. Vickers indents (9.8 N, 20 s) were made at the top surface at 600 μm from the cavity margin. The lengths of the indentation diagonal and the corner cracks parallel to the cavity margin were measured. Ten minutes after restoration (Majesty Esthetic, Kuraray), cracks were re-measured. Stresses at the indent site were calculated based on glass fracture toughness and increase in crack length. Data were subjected to ANOVA/Tukey or Kruskal–Wallis/Mann–Whitney tests (alpha: 5%, n = 8). Finite element analysis (FEA) was used to estimate stress at the interface and the effective structural rigidity of the substrate.
Results
Overall, for experimental and FEA results, cavities developed higher stress than bottom-less disks. Increasing wall thickness did not affect stress. When similar geometries and C-factors were compared, higher volumes developed higher stress and had greater incidence of margin cracking.
Clinical significance
C-factor is a suitable predictor for polymerization stress in low compliance environments, particularly due to its simplicity. However, the influence of cavity size cannot be disregarded especially for the development of marginal cracking. The interaction between size, geometry and stiffness is likely to become more complex according to the complexity of the cavity shape.
1
Introduction
Among the many factors involved in the longevity of restorative procedures using resin composites, the size and the complexity of the restored cavity is often quoted as one of the most important . Clinical data show that the survival rate of composite restorations placed in posterior teeth is inversely related to the number of restored surfaces , with composite bulk fracture and secondary caries being the most frequent causes of failure . Indeed, it is intuitive to assume that larger restorations are more exposed to masticatory forces, which increases the risk of composite fracture, and also intensifies the stress at the bonded interface and/or the tooth structure.
Besides occlusal loading, there are other concurrent aspects that may justify why the bonded interface of composite restorations fails and allows the development of secondary caries, particularly in high-caries risk patients . One aspect refers to the degradation of the adhesive layer due to hydrolysis of the resin component and/or the degradation of the collagen fibers in the hybrid layer due to enzymatic attack by metalloproteinases . Also, there are other sources of stress that must be withstood by the bonded interface, including those that originate from the coefficient of thermal expansion mismatch between the tooth structure and the restoration , and composite polymerization stress.
Polymerization-induced interfacial stress is created during the early stages of the restorative procedure due to the shrinkage and development of the elastic modulus of the restorative taking place under restricted conditions, i.e., while bonded to a substrate . Polymerization stress is not a basic material property and, as such, its magnitude and distribution is determined by the interplay of several variables that can be related to either the material or the bonding substrate. As an example of how complex the interaction between the composite and the local conditions is, highly filled composites were shown to develop high stress values when bonded to low compliance (more rigid) substrates (due to a stronger influence of the elastic modulus), and low stresses when tested in a more compliant system (due to their relatively low polymerization shrinkage) .
While the material-related variables that influence polymerization stress magnitude have been extensively studied over the last decade the environmental factors have received considerably less attention. Specific information gathered from mechanical tests and finite element analysis (FEA) indicates that polymerization stress is determined by the interaction between the compliance of the bonding substrate, the size, and the configuration of the restoration (or specimen) .
In broad terms, compliance can be defined as the amount of deformation of the structure when subjected to shrinkage forces . A particular composite will generate lower stress levels during setting when tested in a high compliance system, and vice versa . For a similar geometry (a class I, for example), a large cavity with thin walls represents a high compliance situation, as shrinkage forces will deform the remaining tooth structure more easily. This deformation reduces the stress in the restoration and at the bonded interface, but increases the stress in the substrate .
Restoration size (or volume) and configuration has been the subject of debate in the literature. The idea that polymerization stress increases in tandem with the confinement imposed on the composite was first suggested by Bowen, half a century ago . Later, the concept of cavity “configuration factor” (C-factor) was defined as the restoration’s ratio of bonded to unbonded surface area . Indeed, it is true that in rigid mechanical testing systems, uniaxial stress increases with C-factor and is not influenced by the specimen’s volume . However, this is not necessarily the case with more compliant substrates, where the mass of shrinking composite also determines the stress magnitude and an inverse relationship between C-factor and stress has been observed . It is undeniable that the idea of having an index such as the C-factor to estimate the risk of interfacial failure due to polymerization stress is appealing, explaining why it has gained such widespread popularity. However, in vitro investigations evaluating the influence of cavity dimensions on microleakage and bond strength as an indirect way to assess the effect of polymerization stress show an interaction between confinement and volume . Therefore, rather than trying to establish beyond doubt which environmental factor is the most important, effort should focus on gaining a deeper understanding of how the these conditions influence polymerization stress development.
A new method to quantify polymerization-induced stress in the bonding substrate was developed, based upon indentation fracture mechanics principles . The “crack analysis method” uses the increase in length of indentation cracks and the fracture toughness of the substrate to estimate residual tensile stresses around the crack tip . Vickers indents are introduced close to the margin of a cavity prepared in glass or ceramic disks, prior to restoration with a bonded composite. Immediately after restoration, the corner cracks increase in length according to the stress level in the substrate resulting from composite polymerization. So far, crack analysis has been used to calculate residual stresses in the bonding substrate obtained with different photoactivation methods and at different distances from the restoration margin . Because the specimen geometry is more akin to an actual restoration than the uniaxial mechanical test, it would be interesting to verify if this method is capable of distinguishing stress levels among restorations with different dimensions and geometric configurations. Also, it is possible to modulate the compliance of the cavity, to some extent, by varying the thickness of the disk wall.
Therefore, this study tested the null hypothesis that, for cylindrical cavities, polymerization-induced stress in a glass substrate was not influenced by cavity dimensions and geometries.
2
Materials and methods
2.1
Polymerization stress determination by crack analysis
Different C-factors and cavity volumes were defined by using soda-lime glass disks 1 or 2 mm in height with a central cylindrical hole 3 or 6 mm in diameter. The disks were prepared by drilling 2-mm thick glass plates and 1-mm thick microscope glass slides with similar composition using sintered diamond core drills (Ukam Industrial Superhard Tools, Valencia, CA, USA) mounted on a drill press. The external diameter of the disks was matched to keep the wall thickness constant at 3 mm. A mixture of water and water-soluble lubricant (Safetycool 407, Castrol, Sydney, Australia) running through a water swivel adapter was used for cooling. Drilling speed was approximately 300 rpm. Another four experimental groups were created by bonding a glass plate to the bottom of the disks using a cyanoacrylate adhesive (UHU GmbH, Bühl, Germany). Finally, in order to assess the effect of cavity compliance on polymerization induced stress an extra set of disks with 2-mm height, 3 mm in cavity diameter, and 4.5-mm thick walls was prepared. The experimental groups, with the respective C-factors and cavity volumes are presented in Table 1 .
Groups | Geometry | Height (mm) | Diameter (mm) | C-factor a | Volume (mm 3 ) |
---|---|---|---|---|---|
I | Cavity (3-mm thick wall) | 2 | 3 | 3.7 | 14 |
II | 6 | 2.3 | 57 | ||
III | 1 | 3 | 2.3 | 7 | |
IV | 6 | 1.7 | 28 | ||
V | Disk (3-mm thick wall) | 2 | 3 | 1.3 | 14 |
VI | 6 | 0.7 | 57 | ||
VII | 1 | 3 | 0.7 | 7 | |
VIII | 6 | 0.3 | 28 | ||
IX | Disk (4.5-mm thick wall) | 2 | 3 | 1.3 | 14 |
a Disks: C = h / r ; cavities: C = (2 h + r )/ r , where h is the height and r is the radius of the cavity.
In order to relieve any residual stresses that may interfere with crack growth, the glass disks were annealed at 510 °C for 2 h, followed by slow cooling. Then, they were sonicated in ethanol for 15 min. Four Vickers indents, one per quadrant, were made at the top surface at approximately 600 μm from the cavity margin using a 9.8 N load for 20 s (Shimadzu Corp., Kyoto, Japan). The disks were kept in a desiccator for 24 h (relative humidity lower than 30%) at room temperature to allow for the corner cracks to grow due to stress corrosion cracking and residual indentation stress. Digitized images of the indents were obtained on an optical microscope, at 500× magnification under reflected light (Metallux II, Leitz, Westzlar, Germany). The lengths of the indentation diagonal ( d ) and the corner cracks parallel to the cavity margin ( c ) were measured using the ImageJ software (National Institute of Health, Bethesda, MD, USA) ( Fig. 1 ). Based on these initial measurements, the fracture toughness of the soda-lime glass ( K c ) was calculated using the formula:
K c = 0.026 × ( EP ) 1 / 2 d 2 c − 3 / 2
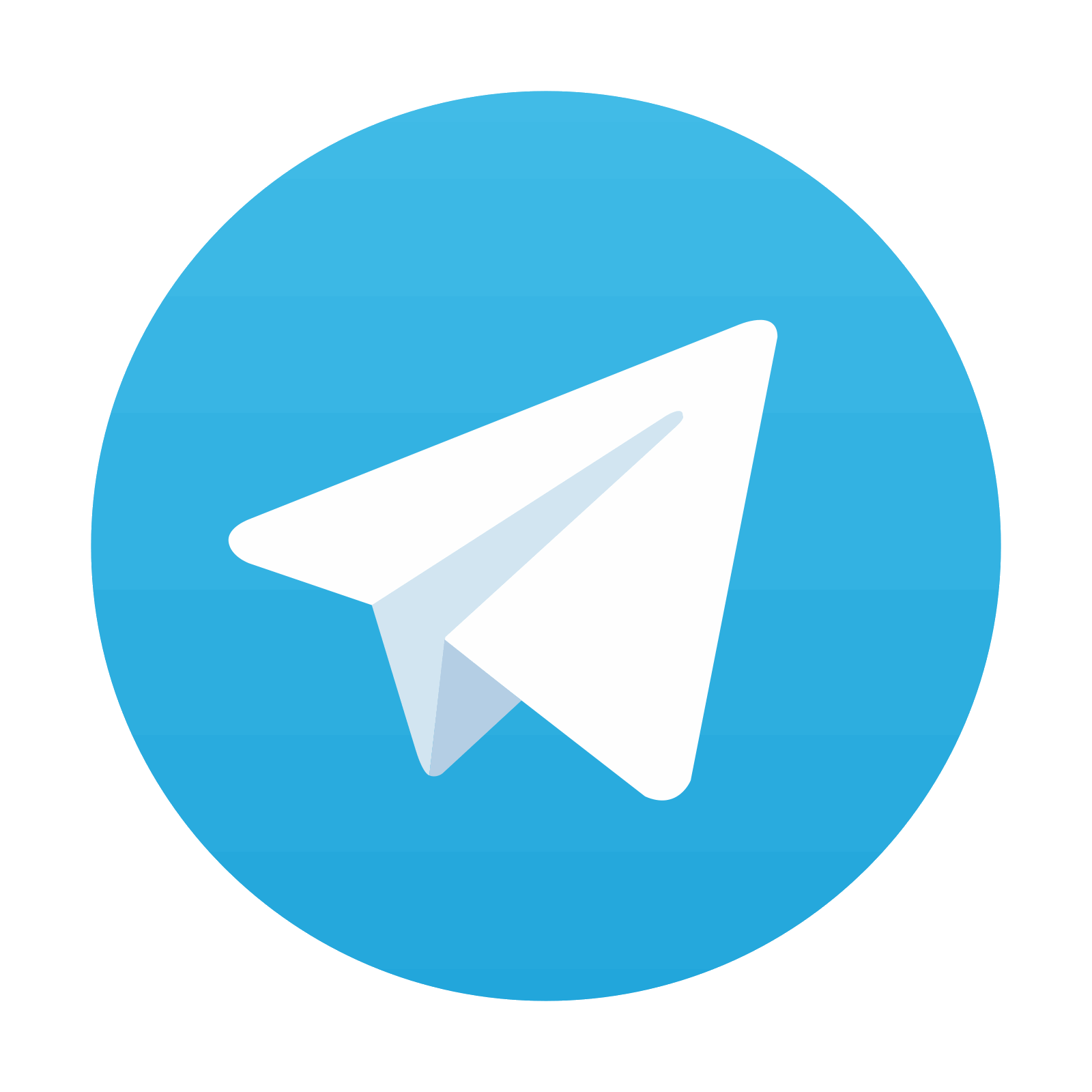
Stay updated, free dental videos. Join our Telegram channel

VIDEdental - Online dental courses
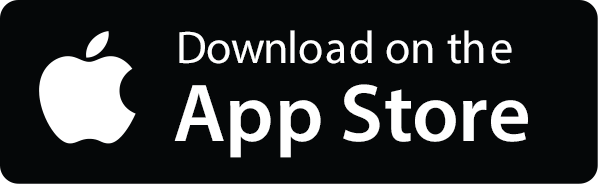
