Introduction
Fabrication of orthodontic aligners directly via 3-dimensional (3D) printing presents the potential to increase the efficiency of aligner production relative to traditional workflows; however tunable aspects of the 3D-printing process might affect the dimensional fidelity of the fabricated appliances. This study aimed to investigate the effect of print orientation on the dimensional accuracy of orthodontic aligners printed directly with a 3D printer.
Methods
A digitally designed aligner of 500 μm thickness was printed in 3D in Grey V4 (Formlabs, Somerville, Mass) resin at 8 angulations at 45° intervals (n = 10 per angulation) using a stereolithography 3D printer. Each aligner was scanned with an optical scanner, and all but the intaglio surface of each scan was digitally removed. Each resultant scan file was superimposed onto the isolated intaglio of the designed master aligner file. The dimensional deviation was quantified with Geomagic Control software (3D Systems, Rock Hill, SC), and data were analyzed using R statistical software (version 2018; R Core Team, Vienna, Austria) ( P <0.05).
Results
Print angle showed a statistically significant effect on standard deviation, average positive deviation, absolute average negative deviation, and percentage of points out of bounds (tolerance bounds defined as ±250 μm) ( P <0.05). Qualitative analysis of the 3D surface deviation maps indicated that the 0° and 90° groups showed less deviation and appeared to be the most accurate in the anterior regions. Overall, the majority of the print angle groups studied were not printed within clinically acceptable tolerance ranges, with the major exception being the 90° group, which printed nominally within clinically acceptable tolerance ranges.
Conclusions
With the workflow applied, print orientation significantly affects the dimensional accuracy of directly 3D-printed orthodontic aligners. Within the limitations of this study, printing at the 90° angulation would be advised as it is the group with the most accurate prints relative to the 7 other orientations investigated, although not all differences were statistically significant.
Highlights
- •
Orthodontists should understand the best print orientation for 3D printed aligners.
- •
Deviations observed in 3D-printed aligners can affect fit.
- •
Print orientation affects the dimensional accuracy of directly 3D-printed aligners.
- •
A 90° angle resulted in the highest dimensional accuracy.
Because of the ever-increasing demand for clear aligner therapy as a treatment option for orthodontic patients and the recent desire for orthodontists to transition to in-house 3-dimensional (3D) printing of clear aligners, a need exists for research to optimize 3D printing workflows to achieve treatment goals. Traditionally, the fabrication of in-house aligners is performed via 3D printing of a resin dental model from input stereolithography (STL) file, followed by thermoforming a plastic sheet on top of the printed model to create the aligner. The accuracy of 3D printed orthodontic models has been investigated at length in the literature and generally has been found to be within clinical tolerance ranges. Recently, new resins have emerged that may enable practitioners to directly 3D-print aligners and forgo the steps of printing models and thermoforming the plastic, thereby increasing office efficiency. However, models and aligners have inherent geometric differences, most notably the shell-like morphology of aligners compared with models, which may affect the fidelity with which the respective parts are produced through 3D printing. Thus, the need for research on print accuracy of directly 3D-printed aligners has arisen, most importantly the accuracy of the intaglio (inside) surface of the aligners, which is functionally the clinically working side of aligners that moves the teeth. Deviations in the accuracy could alter clinical force vectors and jeopardize desired clinical results when it comes to desired tooth movement.
The thickness of thermoformed aligners has been shown to affect force generation in orthodontic applications. Accordingly, deviations from intended aligner thickness, whether the aligner is produced by thermoforming or directly by 3D printing, may affect the clinical performance of the appliance. A recent study investigated the effect of the thickness of an aligner design on the thickness of the aligner when produced by 3D printing. Typical thicknesses of thermoformed aligners range from 400 μm to 1500 μm, which led to the selection of 3 aligner thicknesses: 250 μm, 500 μm, and 750 μm. In each case, the average thickness of the 3D-printed aligner was significantly thicker than designed, and the deviations were found to affect the intaglio and cameo surfaces of the aligners. The thickness deviations observed in the 3D-printed aligners can negatively affect the fit of the appliance as well as the prescribed orthodontic tooth movement.
Another variable in the 3D-printing workflow of directly printed aligners is print orientation relative to the print platform. A recent study analyzing the effects of aligner print orientation on dimensional accuracy looked at 3 print orientations: one with the aligner oriented such that the occlusal surface was perpendicular to the print platform with the anterior portion away from the print platform, a second oriented at a 45° angle with the anterior portion and intaglio surface away from the print platform, and the third oriented with the occlusal surface parallel to the print platform with the intaglio surface away from the print platform. The authors found that the average positive and negative dimensional deviations of the aligners printed at all orientations investigated fell within a clinical tolerance range of ± 250 μm, but the authors suggested that localized areas of dimensional deviation observed might affect the clinical utility of the aligners. However, it becomes apparent that other possible print orientations exist, such as orientations in which the cameo surface rather than the intaglio surface is positioned away from the print platform, as well as if the posterior portion of the aligner were to be oriented away from the print platform instead of the anterior. As the orientation of a part during 3D printing can affect the efficiency of the workflow, it is important to characterize the effects of different orientations on the dimensional fidelity of the appliances produced. Accordingly, this study aimed to evaluate the effect of the orientation of the aligner during printing on the dimensional accuracy of orthodontic aligners fabricated directly via 3D printing using an opaque resin (Grey V4; Formlabs, Somerville, Mass). The null hypothesis was that there is no effect of the print orientation on the dimensional accuracy of 3D-printed orthodontic aligners.
Material and methods
An aligner of uniform thickness (500 μm) was digitally designed on the basis of a typodont archform (Nissin, Kyoto, Japan), and an STL file was generated. The archform included a full adult dentition except for third molars. This STL file was imported into PreForm software (PreForm software, version 2.19.3; Formlabs) and was prepared for 3D printing. The aligner print angle was varied at 8 different orientations at 45° intervals relative to the print platform, and the angles were labeled as 0°, 45°, 90°, 135°, 180°, 225°, 270°, and 315° ( Fig 1 ).

All files were digitally prepared for the printing of the aligners (n = 10) for each angle for a total of 80 printed aligners. Print supports were added only to the cameo (outside) surface of the aligners in an attempt to preserve the accuracy of the intaglio surfaces; however, for orientations with the cameo surface oriented away from the print platform, it was necessary for some supports to be located on the gingival margins of the aligner, but not extending into the intaglio surface. The aligners were printed with an opaque grey resin (Grey V4; Formlabs) with a Form 2 (Formlabs) printer using a 405 nm wavelength laser light source. Although the opaque Grey V4 resin is not approved for intraoral use, it was selected for use in the present study as previous studies found the translucency of clear materials to present difficulty in optically scanning 3D-printed clear aligners for superimposition analysis. , The aligners were printed using a 100 μm print layer height. After printing, postprocessing was performed according to the manufacturer’s instructions for the resin. Briefly, the aligners were removed from the print platform and washed in 2 successive baths of >99% isopropyl alcohol, the first for 1 minute to remove excess resin and the second for 10 minutes under agitation (Form Wash; Formlabs). After washing, the aligners were aggressively sprayed with compressed air to remove isopropyl alcohol and left to air-dry for 30 minutes at room temperature (23°C). The aligners were then cured for 30 minutes at 60°C in a curing chamber equipped with 405 nm wavelength light-emitting diodes (Form Cure; Formlabs). All print supports were then removed carefully in preparation for scanning. To facilitate the optical scanning of the aligners, a custom 3D-printed jig was created to position the aligner on the scanner platform at a 45° angle, with the jig fitting securely within the intaglio surface of the right second molar portion of the aligner ( Supplementary Fig ). All aligners were scanned with a desktop scanner (E3; 3Shape, Copenhagen, Denmark). The STL files produced from the scans were transferred to Geomagic Control metrology software (version 2015.1.1; 3D Systems, Rock Hill, SC), and the intaglio surface of each scan file was isolated by manually selecting and digitally removing all other surfaces within the software. The right second molar, which was attached to the jig, was also removed digitally. With the same software, the intaglio surface of each scan was then superimposed with the selected intaglio surface of the original aligner STL input file to analyze 3D-surface deviations. The superimposition involved an automated iterative closest point algorithm in achieving the best fit between the 2 surfaces. The 3D-comparison feature of the software was then used to calculate surface deviations across all points of the intaglio surface, and color maps illustrating 3D-surface deviations were generated. A 250 μm tolerance level was used as the upper and lower bounds of clinical acceptance in accordance with previous studies. , , , A generalized linear mixed model and post-hoc Tukey contrasts were employed for statistical analysis using R statistical software (version 2018; R Core Team, Vienna, Austria). The effects of the explanatory variables of the print orientation angle, positioning of the intaglio surface of the aligner away from the build platform, and the positioning of the anterior portion of the aligner away from the build platform on the response variables of standard deviation, average positive deviation, absolute average negative deviation, and percentage of points out of bounds were analyzed. The level of significance was set at P <0.05 for all analyses. For this study, with an α = 0.05 and sample size of 10, and on the basis of observed effect sizes of F values 11-14, we were able to detect very small effect sizes with a power of 0.99. ,
Results
Three of the 80 aligners (3.75%) were fractured during the postprint processing stages and were excluded from the study (1 sample from each of the 45°, 135°, and 225° groups). Overall, print angle showed a statistically significant effect on standard deviation ( Fig 2 ), average positive deviation ( Fig 3 ), average negative deviation ( Fig 4 ), and percentage of points out of bounds ( Table ).



Angle | % out of bounds (mean ± SD) | Post-hoc Tukey contrast results ( P values) | |||||||
---|---|---|---|---|---|---|---|---|---|
0° | 45° | 90° | 135° | 180° | 225° | 270° | 315° | ||
0° | 23.2 ± 12.0 | – | 0.188 | 0.884 | <0.001 ∗ | 0.441 | <0.001 ∗ | 0.987 | 0.459 |
45° | 33.9 ± 8.6 | 0.188 | – | <0.001 ∗ | 0.204 | 0.999 | 0.746 | 0.721 | >0.999 |
90° | 17.9 ± 9.9 | 0.884 | <0.001 ∗ | – | <0.001 ∗ | 0.020 ∗ | <0.001 ∗ | 0.348 | 0.021 ∗ |
135° | 46.2 ± 7.8 | <0.001 ∗ | 0.204 | <0.001 ∗ | – | 0.051 | 0.987 | <0.001 ∗ | 0.043 ∗ |
180° | 31.8 ± 7.6 | 0.441 | 0.999 | 0.020 ∗ | 0.051 | – | 0.389 | 0.940 | >0.999 |
225° | 41.8 ± 3.6 | <0.001 ∗ | 0.746 | <0.001 ∗ | 0.987 | 0.389 | – | 0.025 ∗ | 0.359 |
270° | 26.7 ± 12.1 | 0.987 | 0.721 | 0.348 | <0.001 ∗ | 0.940 | 0.025 | – | 0.948 |
315° | 31.4 ± 8.7 | 0.459 | >0.999 | 0.021 ∗ | 0.043 ∗ | >0.999 | 0.359 | 0.948 | – |
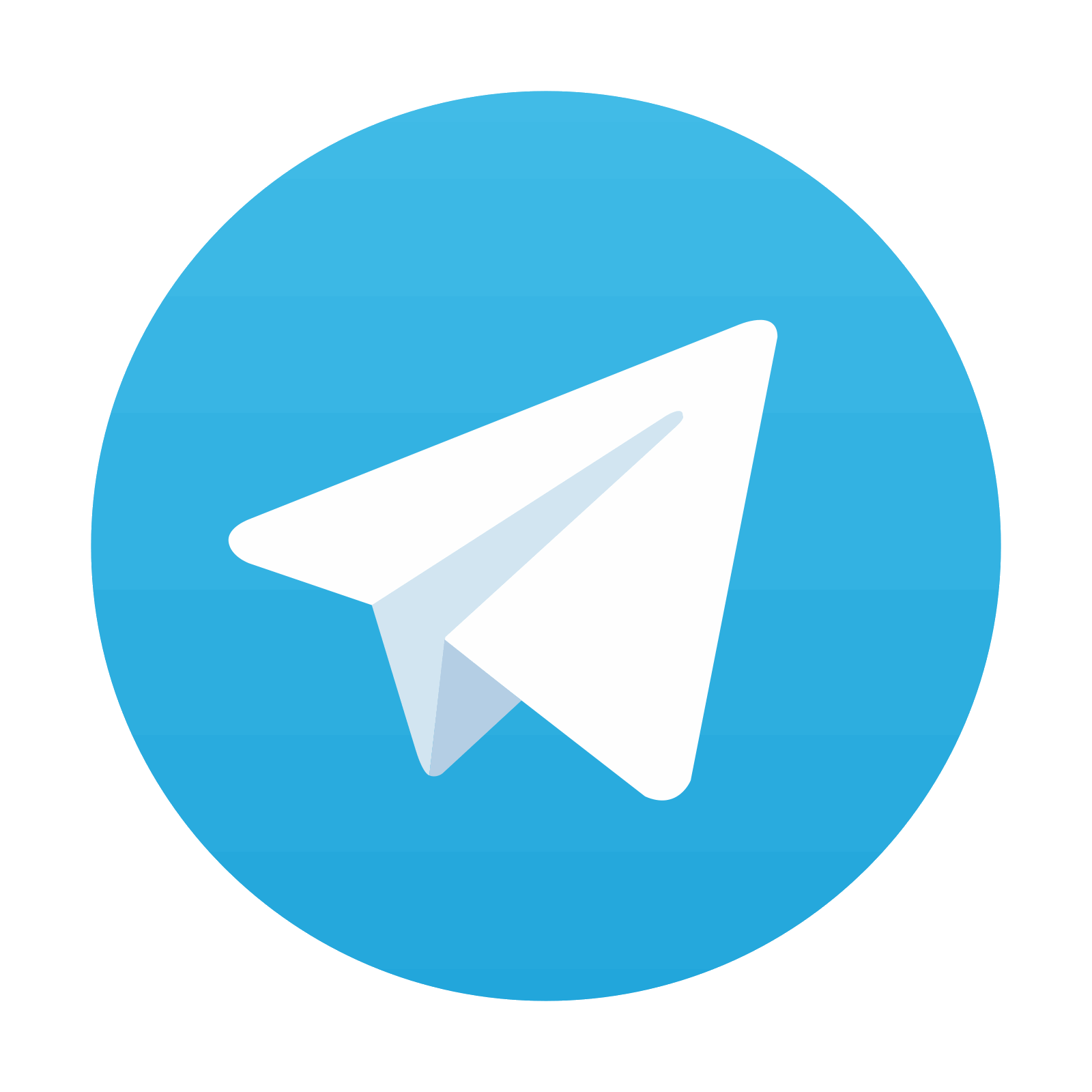
Stay updated, free dental videos. Join our Telegram channel

VIDEdental - Online dental courses
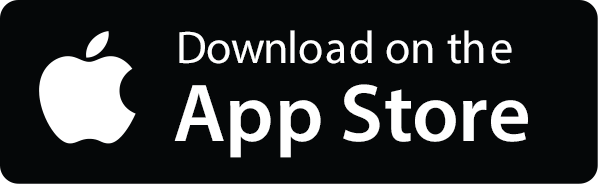

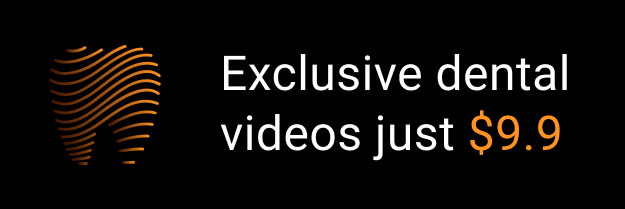