Abstract
Objectives
The aim of this study was to investigate the effect of layering methods, flowable composite liner and use of low shrinkage silorane-based composite on the polymerization shrinkage stress of light cured composites.
Methods
Aluminum blocks were used to prepare MOD cavities and divided into four groups. A universal hybrid methacrylate-based composite (Z250), a flowable composite (Z350 flowable), and a silorane-based composite (P90) were used to fill the cavities. Cavities were restored using four different filling protocols. Group 1 was filled in bulk with Z250, group 2 was restored by an increment technique with the same composite, group 3 by an increment technique with Z250 and a Z350 flowable lining, and group 4 was restored by an increment technique with P90. The axial shrinkage strain and flexural modulus of the three composites were determined, and cuspal deflection of each group was measured with LVDT probes and compared among groups using ANOVA and Tukey’s post hoc test ( α = 0.05).
Results
The axial shrinkage strains of P90, Z250, and Z350 flowable were 1.09 (0.11), 2.29 (0.06), and 4.12 (0.08)%, respectively. The flexural modulus of P90 was 10.1 (0.9), Z250 was 13.6 (2.0), and that of Z350 flowable was 7.6 (0.9) GPa. The cuspal deflections at 33 min in groups 1–4 were 18.2 (1.54), 14.5 (0.47), 16.2 (1.10), and 6.6 (0.44) μm, respectively. The incremental filling technique yielded significantly lower cuspal deflection than the bulk filling technique. Flowable composite lining under universal composite (Z250) layering showed higher cuspal deflection than that without flowable composite lining. Silorane-based (P90) composite exhibited lower cuspal deflection than metacrylate based (Z250) composite.
Significance
Cuspal deflection resulting from polymerization shrinkage stress may be reduced by an incremental filling technique and by the use of low shrinking composite to obtain optimal clinical outcomes. Flowable composite lining under conventional composite layering did not reduce polymerization shrinkage stress as assessed by cuspal deflection.
1
Introduction
Composite restoration has become an essential part of everyday dental practice with the improvement in dental adhesive systems, the increase in patients’ demand for esthetics and more emphasis on preservation of tooth structure. The abrasion resistance of dental composites has continued to improve since their introduction as dental restoratives, enabling expanded use in posterior restorations with good longevity. However, the polymerization shrinkage and its associated stress still remains a major drawback of dental composite materials, and numerous studies have been performed to assess and reduce the polymerization shrinkage stress .
Polymerization shrinkage causes stress at the interface between a tooth and a restoration as the elastic modulus of the composite increases during curing. This stress manifests as bond failure, cuspal flexure, enamel microcracking, pulpal irritation and secondary caries due to bacterial infiltration, and post operative sensitivity, which in turn can lead to restoration failure requiring re-restoration .
Efforts have been made to increase inorganic filler loading and to develop a new resin matrix to reduce polymerization shrinkage of composites. However, increasing inorganic filler loading is limited to a level that the surface of fillers can be harmoniously combined physico-chemically with the resin matrix. Polymerization shrinkage can also be reduced by decreasing reactive sites per unit volume through increasing molecular weight per reactive groups. But this strategy also has its limitations because the use of high molecular weight monomers produces increased viscosity, resulting in poor handling characteristics , as well potentially reducing strength . Therefore, attempts to develop composites with completely new resin matrices that do not shrink or shrink considerably less, have been ongoing, and recently a composite with silorane resin matrix containing siloxane and oxirane has been introduced .
Clinical strategies suggested to minimize shrinkage stress of composites include incremental filling technique to decrease C -factor (configuration factor = bonded surface area/non-bonded surface area) , soft-cure or pulse-delay cure methods to slow polymerization by more gradually increasing light intensity from the curing units , and the use of low-modulus intermediate liner material such as flowable composites to absorb shrinkage stress .
Conflicting results have been reported regarding the efficacy of incremental filling technique. Studies using the finite element analysis method , and a study measuring cuspal flexure in premolar teeth reported incremental filling of composites produces higher shrinkage stress and cuspal deflection. In contrast, other studies have shown considerably reduced cuspal deflection with incremental filling compared to the bulk filling technique . It has also been reported that the incremental filling technique resulted in higher resin–dentin micro-tensile bond strength compared to bulk filling in large cavities whereas there was no significant difference in small cavities . The controversy over incremental and bulk filling techniques can be ascribed to the difficulty in exactly simulating the transitional changes of resin flow during polymerization, to the different testing methods, and to the difficulty in standardizing tested specimens .
Measurement of cuspal deflection is a useful way for evaluating polymerization shrinkage stress, but the use of extracted teeth for cuspal deflection measurement can produce significant discrepancies among specimens due to the lack of standardizing the anatomical and histochemical characteristics of each individual tooth . Park et al. fabricated aluminum blocks with identical shape and dimension instead of using extracted teeth and measured cuspal deflections of the aluminum blocks. The cuspal deflection in the incremental filling technique was shown to be considerably lower than for the bulk filling technique, and there was no significant difference between horizontal and oblique incremental filling techniques.
Flowable composite has been recommended as a stress-absorbing liner or base owing to its relatively low modulus of elasticity and greater ability to deform to contribute to reduction of polymerization shrinkage stress from the overlying composite restorative . Cuspal deflection has been shown to be significantly lower with the use of a flowable composite as an intermediate layer than without a flowable composite . In contrast, a study using a photoelastic model reported that the use of flowable composite increased shrinkage stress at the adhesive interface .
Silorane-based composite shows lower polymerization shrinkage compared to conventional methacrylate-based composite , however studies using a stress–strain analyzer and a universal testing machine reported that simply reducing the shrinkage does not ensure reduced stress development in composites .
Most studies have used indirect methods, such as microleakage and micro-tensile bond strength tests, to evaluate the effects of various clinical methods to reduce polymerization shrinkage stress. Measuring cuspal deflection of teeth provides a more direct representation of contraction stress effects, but is made difficult by the morphological and histochemical differences of natural tooth substrates. This study measured cuspal deflection in real time during composite curing, using standardized, uniform aluminum blocks with MOD cavity preparations. The aim of this study was to investigate the effects of layering methods, the use of flowable composite liner, or the use of low shrinkage silorane-based composite on polymerization shrinkage stress effects of composites.
2
Materials and methods
2.1
Cuspal deflection measurement instrument
Two LVDT (linear variable differential transformer) probes (AX-1, Solartron Metrology, West Sussex, UK) were set on two XYZ tables (Micro Motion Technology, Bucheon, Korea) with three attached micrometers (Mitutoyo, Kawasaki, Japan) ( Fig. 1 ). Cuspal deflection was detected by LVDT probes and the measured value was collected using a data acquisition board (PCI-6024, National Instruments, Austin, TX, USA) and data acquisition and analysis software (Labview, National Instruments). The sensitivity of the LVDT probes exceeded 0.1 μm in the range of ±1 mm.

2.2
Specimen preparation
Twenty four aluminum blocks (10 mm × 8 mm × 30 mm) with a MOD cavity [6 ( W ) mm × 8 ( L ) mm × 4 ( D ) mm] were fabricated using a milling machine, creating two remaining cusps [2 ( T ) mm × 8 ( L ) mm × 4 ( H ) mm] ( Fig. 2 a). The inside of the cavity was air-abraded with 50 μm Al 2 O 3 powder and thoroughly rinsed with water using a three-way syringe.

Composites used for filling the MOD cavities were a methacrylate-based universal hybrid composite (Z250: 3 M ESPE, St. Paul, MN, USA), a flowable composite (Z350 flowable: 3 M ESPE), and a silorane-based composite (P90: 3 M ESPE) ( Table 1 ). Scotchbond multipurpose adhesive (3 M ESPE) was applied prior to placement of methacrylate-based composites (Z250 and Z350 flowable) and P90 system adhesive was applied prior to silorane-based composite (P90) as recommended by the manufacturer. The adhesive was light cured for 10 s using a LED light curing unit (S10: 3 M ESPE), and the light intensity was measured as 1160 mW/cm 2 (EPM 1000 power meter, Molectron Detector Inc., Oregon, USA). The radius of light guide was 10 mm, and the light guide was positioned at approximately 2 mm from the irradiated surface. An acrylic cap with two notches on the cuspal wall sides was fabricated and placed on the aluminum blocks to prevent the composite from being pushed out of the cavity during layering, and to position the LVDT probes precisely 1 mm from the cusp tips ( Fig. 2 b). The internal surface of the acrylic cap was lubricated with petroleum jelly to prevent the composite from being adhered and to ensure free surfaces of composites on the sides facing the acrylic cap. The acrylic cap also had sufficient compliance to allow the expansion or contraction of composites and aluminum molds.
Composite | Lot no. | Resin matrix | Filler (wt%) | Manufacturer |
---|---|---|---|---|
Filtek Z250 Universal hybrid |
8LXJ | Bis-GMA, Bis-EMA, TEGDMA, UDMA | 0.01–3.5 μm Zr/silica particles (82 wt%) | 3 M ESPE St. Paul, MN, USA |
Filtek Z350 Flowable |
7FX | Bis-GMA, Bis-EMA, TEGDMA | 5–20 nm Zr/silica nanoparticles + 0.6–1.4 μm nano-clusters (65 wt%) | 3 M ESPE |
Filtek P90 Silorane |
N276998 | Silorane | 0.01–3.5 μm quartz particles, yttrium fluoride (76 wt%) | 3 M ESPE |
2.3
Composite filling and measurement of cuspal deflection
The required amount of composite to fill the cavity was calculated from the density of the composites and the volume of the cavity, and equal amount of composites for each cavity was ensured by weighing the material before use. The aluminum blocks were randomly divided into four groups and filled with composites by one of following protocols ( Fig. 3 ).

Group 1 (bulk filling): Z250 was placed in bulk and light cured from the upper surface for 20 s, the mesial side for 20 s, the distal side for 20 s, and the upper surface for 20 s again (total 80 s).
Group 2 (incremental filling): Z250 was placed in four incremental layers. The thickness of first horizontal increment was 1 mm and it was irradiated at a right angle from occlusal surface. The second and third increments were obliquely layered. The light guide was slightly tilted perpendicular to the irradiated surfaces of second and third oblique layers for optimum irradiation. The fourth horizontal layer was irradiated from occlusal direction. Therefore, the maximum thickness of composite layer for light curing was less than 2.5 mm at the diagonal direction. Each increment was light cured for 20 s (total 80 s).
Group 3 (incremental filling with flowable liner): The first layer was filled with Z350 flowable composite in 1 mm thickness, followed by three incremental layers with Z250. Each increment was light cured for 20 s as done in group 2 (total 80 s).
Group 4 (incremental filling with silorane-based composite): P90 was placed in four incremental layers. Each increment was light cured for 20 s as done in group 2 (total 80 s).
In the incremental placement groups (groups 2–4), the composite was equally divided into four portions with each portion representing a single increment. The composite for the bulk filling group and the first layers of incremental filling groups were filled before installing the aluminum block on the cuspal deflection measurement instrument. After setting the block onto the metal vise and positioning the two LVDT probes on the cusp tips, light curing and subsequent layering were performed.
Measurement of cuspal deflection was initiated 30 s prior to light curing to obtain a base line and continued up to 2000 s at a rate of 2 data points/s. The amounts of cuspal displacement measured from both cusps were added to produce total deflection. Six measurements were performed for each group at temperature of 25 ± 0.5 °C. The data was analyzed by ANOVA and Tukey’s post hoc test ( α = 0.05).
2.4
Measurement of the axial shrinkage strain and flexural modulus of composites
In order to investigate the effect of polymerization shrinkage and elastic modulus of the composites on the cuspal deflection, the axial shrinkage strain and flexural modulus of the composites were measured using a “modified bonded disc method” and a universal testing machine, respectively ( Fig. 4 ). To measure axial strain, a fixed amount of composite was pressed between a slide glass and a flexible cover glass (Marienfeld, Germany) using a metal wire with 0.5 mm diameter as a spacer, producing a disc-shaped specimen 0.5 mm in thickness and 6.0 mm in diameter (aspect ratio = 12). The tip of a LVDT probe was placed on the center of the cover glass and set to zero. A base line was obtained for 20 s, and then the curing light was irradiated for 40 s. The output voltage from the LVDT was stored on a computer using a data acquisition device (PCI-6024, National instruments) at a rate of 10 data points/s for 10 min to determine the axial shrinkage of the composites.

Bar type specimens for flexural modulus tests were prepared by placing the composites into stainless steel mold with 2 mm × 2 mm × 30 mm space, and light cured in three portions for 40 s each, and stored in distilled water at 37 °C for 24 h. The width and thickness of the specimens were measured, and flexural modulus was obtained by performing 3 point flexural test. Specimens were installed on a universal testing machine (4465, Instron, USA), load was applied at the rate of 0.5 mm/min (distance between the two supporting bases = 20 mm), and the load–displacement curve was measured. The flexural modulus of elasticity was calculated from the equation:
E = L 3 P 4 W T 3 D ,
where E is the flexural elastic modulus (Pa), L is the support span (m), P is the load (N), W is the specimen width (m), T is the specimen thickness (m), and D is the displacement at the center of the beam (m). Five specimens were tested for each composite.
2.5
Measurement of the compliance of the cusp of aluminum block
Weights of 15.0–16.0 kg at an interval of 200 g were applied at a point 1 mm from the cusp tip of the aluminum block and displacement of the cusp was measured using a LVDT probe ( Fig. 5 ). The cusp compliance was obtained from the measured load–displacement relationship ( n = 5).

2
Materials and methods
2.1
Cuspal deflection measurement instrument
Two LVDT (linear variable differential transformer) probes (AX-1, Solartron Metrology, West Sussex, UK) were set on two XYZ tables (Micro Motion Technology, Bucheon, Korea) with three attached micrometers (Mitutoyo, Kawasaki, Japan) ( Fig. 1 ). Cuspal deflection was detected by LVDT probes and the measured value was collected using a data acquisition board (PCI-6024, National Instruments, Austin, TX, USA) and data acquisition and analysis software (Labview, National Instruments). The sensitivity of the LVDT probes exceeded 0.1 μm in the range of ±1 mm.
2.2
Specimen preparation
Twenty four aluminum blocks (10 mm × 8 mm × 30 mm) with a MOD cavity [6 ( W ) mm × 8 ( L ) mm × 4 ( D ) mm] were fabricated using a milling machine, creating two remaining cusps [2 ( T ) mm × 8 ( L ) mm × 4 ( H ) mm] ( Fig. 2 a). The inside of the cavity was air-abraded with 50 μm Al 2 O 3 powder and thoroughly rinsed with water using a three-way syringe.
Composites used for filling the MOD cavities were a methacrylate-based universal hybrid composite (Z250: 3 M ESPE, St. Paul, MN, USA), a flowable composite (Z350 flowable: 3 M ESPE), and a silorane-based composite (P90: 3 M ESPE) ( Table 1 ). Scotchbond multipurpose adhesive (3 M ESPE) was applied prior to placement of methacrylate-based composites (Z250 and Z350 flowable) and P90 system adhesive was applied prior to silorane-based composite (P90) as recommended by the manufacturer. The adhesive was light cured for 10 s using a LED light curing unit (S10: 3 M ESPE), and the light intensity was measured as 1160 mW/cm 2 (EPM 1000 power meter, Molectron Detector Inc., Oregon, USA). The radius of light guide was 10 mm, and the light guide was positioned at approximately 2 mm from the irradiated surface. An acrylic cap with two notches on the cuspal wall sides was fabricated and placed on the aluminum blocks to prevent the composite from being pushed out of the cavity during layering, and to position the LVDT probes precisely 1 mm from the cusp tips ( Fig. 2 b). The internal surface of the acrylic cap was lubricated with petroleum jelly to prevent the composite from being adhered and to ensure free surfaces of composites on the sides facing the acrylic cap. The acrylic cap also had sufficient compliance to allow the expansion or contraction of composites and aluminum molds.
Composite | Lot no. | Resin matrix | Filler (wt%) | Manufacturer |
---|---|---|---|---|
Filtek Z250 Universal hybrid |
8LXJ | Bis-GMA, Bis-EMA, TEGDMA, UDMA | 0.01–3.5 μm Zr/silica particles (82 wt%) | 3 M ESPE St. Paul, MN, USA |
Filtek Z350 Flowable |
7FX | Bis-GMA, Bis-EMA, TEGDMA | 5–20 nm Zr/silica nanoparticles + 0.6–1.4 μm nano-clusters (65 wt%) | 3 M ESPE |
Filtek P90 Silorane |
N276998 | Silorane | 0.01–3.5 μm quartz particles, yttrium fluoride (76 wt%) | 3 M ESPE |
2.3
Composite filling and measurement of cuspal deflection
The required amount of composite to fill the cavity was calculated from the density of the composites and the volume of the cavity, and equal amount of composites for each cavity was ensured by weighing the material before use. The aluminum blocks were randomly divided into four groups and filled with composites by one of following protocols ( Fig. 3 ).
Group 1 (bulk filling): Z250 was placed in bulk and light cured from the upper surface for 20 s, the mesial side for 20 s, the distal side for 20 s, and the upper surface for 20 s again (total 80 s).
Group 2 (incremental filling): Z250 was placed in four incremental layers. The thickness of first horizontal increment was 1 mm and it was irradiated at a right angle from occlusal surface. The second and third increments were obliquely layered. The light guide was slightly tilted perpendicular to the irradiated surfaces of second and third oblique layers for optimum irradiation. The fourth horizontal layer was irradiated from occlusal direction. Therefore, the maximum thickness of composite layer for light curing was less than 2.5 mm at the diagonal direction. Each increment was light cured for 20 s (total 80 s).
Group 3 (incremental filling with flowable liner): The first layer was filled with Z350 flowable composite in 1 mm thickness, followed by three incremental layers with Z250. Each increment was light cured for 20 s as done in group 2 (total 80 s).
Group 4 (incremental filling with silorane-based composite): P90 was placed in four incremental layers. Each increment was light cured for 20 s as done in group 2 (total 80 s).
In the incremental placement groups (groups 2–4), the composite was equally divided into four portions with each portion representing a single increment. The composite for the bulk filling group and the first layers of incremental filling groups were filled before installing the aluminum block on the cuspal deflection measurement instrument. After setting the block onto the metal vise and positioning the two LVDT probes on the cusp tips, light curing and subsequent layering were performed.
Measurement of cuspal deflection was initiated 30 s prior to light curing to obtain a base line and continued up to 2000 s at a rate of 2 data points/s. The amounts of cuspal displacement measured from both cusps were added to produce total deflection. Six measurements were performed for each group at temperature of 25 ± 0.5 °C. The data was analyzed by ANOVA and Tukey’s post hoc test ( α = 0.05).
2.4
Measurement of the axial shrinkage strain and flexural modulus of composites
In order to investigate the effect of polymerization shrinkage and elastic modulus of the composites on the cuspal deflection, the axial shrinkage strain and flexural modulus of the composites were measured using a “modified bonded disc method” and a universal testing machine, respectively ( Fig. 4 ). To measure axial strain, a fixed amount of composite was pressed between a slide glass and a flexible cover glass (Marienfeld, Germany) using a metal wire with 0.5 mm diameter as a spacer, producing a disc-shaped specimen 0.5 mm in thickness and 6.0 mm in diameter (aspect ratio = 12). The tip of a LVDT probe was placed on the center of the cover glass and set to zero. A base line was obtained for 20 s, and then the curing light was irradiated for 40 s. The output voltage from the LVDT was stored on a computer using a data acquisition device (PCI-6024, National instruments) at a rate of 10 data points/s for 10 min to determine the axial shrinkage of the composites.
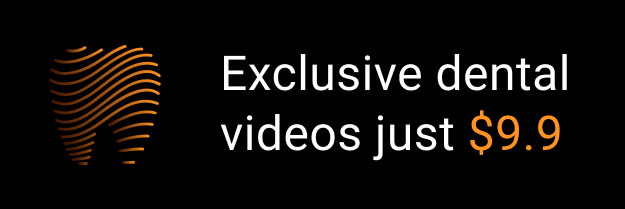