Abstract
Objective
To study the role of the various components of alginate dental impression materials.
Methods
Experimental materials were formulated and their physical properties characterized and compared to commercially available counterparts (Neocolloid, Palgat Plus and Blueprint Cremix). Properties examined were: dimensional stability and weight change in water and artificial saliva; setting behavior; Shore A hardness and tear energy. The role of magnesium oxide was also investigated.
Results
Weight changes in water and artificial saliva can be attributed to an initial thermodynamic potential owing to the ionic content of the alginate, causing water to diffuse into the material. Water is then driven back out following a reversal of this potential.
Hardness results for experimental materials were within the range obtained from the commercial materials. The hardness value for an experimental formulation that did not contain magnesium oxide was lower than values from the other experimental materials that did.
Tear energies for all three experimental materials were greater than those of the commercial products. There were statistically significant differences between the two experimental materials that contained magnesium oxide and one that did not.
With regard to setting time, statistically significant differences were seen between commercial materials and two of the experimental materials. The experimental material that did not contain magnesium oxide had a considerably longer setting time than all of the other materials tested.
Significance
The key role of magnesium oxide in the setting reaction and the effect on hardness have been demonstrated and discussed.
1
Introduction
Alginate dental impression materials were introduced in 1940 . Since then they have been used extensively in Dentistry as one of the group of so-called ‘elastic’ impression materials, with well documented advantages and disadvantages . They have also found application in ophthalmic surgery and in measuring wound size in general surgery .
The term ‘elastic’ however is something of a misnomer; alginates are visco-elastic materials with rubber-like compliance. Marketed products must conform to ISO 1563:1990.
Since their inception, there have been a number of publications on a range of properties . However, understandably these have been almost exclusively on commercial products. Cook investigated the effect of some ingredients on properties, by using commercial impression materials and analyzing them for components to explain the results of a number of physical tests. Morris studied the chemical structure of alginate polymers. In order to investigate the role of individual components in alginate impression materials and the effect on physical properties, formulations have to be produced ab initio .
Disinfection of dental impressions is necessary to avoid cross-infection consequent on the presence of micro-organisms from blood and saliva on the impression surface . Micro-organisms have also been recovered from stone casts made from contaminated impressions . Spray and immersion disinfectants are widely used to disinfect alginate impressions. However, these processes are likely to cause dimensional changes or adversely affect surface quality . Clearly the availability of a self-disinfecting alginate would be a distinct advantage.
In this contribution, experimental alginate formulations have been prepared using sodium alginate and individual components varied to determine the consequent effects on setting time, dimensional stability, Shore A hardness and tear strength. The role of magnesium oxide in alginate formulations has also been examined. Commercial materials have been used for comparison.
2
Materials and methods
2.1
Materials
The commercial materials used were: Neocolloid, Zhermack; Palgat Plus, 3M ESPE (both sodium alginates) and Blueprint Cremix, Dentsply DeTrey (potassium alginate). Approximate compositions are given in Table 1 . Each material was mixed according to the manufacturer’s instructions. Neocolloid was the only commercial material used for experiments on dimensional and weight changes after setting. For all other tests, all three materials were used.
Neocolloid (Zhermack) | Palgat Plus (3M ESPE) | Blueprint Cremix (Dentsply) |
---|---|---|
Sodium pyrophosphate | Trisodium phosphate | Disodium orthophosphate |
Zinc oxide | Magnesium oxide | Magnesium oxide |
Diatomaceous earth | Diatomaceous earth | Inorganic filler |
Cristobalite | Sodium alginate | Potassium alginate |
Potassium fluorotitanate | Dipotassium hexafluorotitanate | Potassium hexafluorotitanate |
Calcium sulfate | Calcium sulfate dihydrate | |
Polypropylene glycol | ||
Sodium aluminosilicate |
Three experimental materials were developed and tested. The formulations and source of constituents for the experimental materials are given in Tables 2 and 3 . ExI is the formulation recommended by the alginate manufacturer ISP Alginates (UK) Ltd. ExII was formulated with an increased sodium pyrophosphate content to investigate the effect on setting time. It should be noted that the formulations contain magnesium oxide (MgO); not shown in most dental material textbooks . Its role will be demonstrated subsequently. A third experimental material (ExII F1) was formulated without MgO. All three materials were used for all tests, except the dimensional and weight changes, where ExII F1 was not tested.
Ingredient | Supplier | Function |
---|---|---|
Manugel ® DJX | ISP Alginates (UK) Ltd, Ayreshire, UK | Soluble alginate |
Crystacast plaster | CFS Partnership, Cornwall, UK | Cross-linking agent |
Potassium fluorotitanate | Rose Chemicals Ltd, London, UK | pH modifier |
Tetrasodium pyrophosphate | Sigma–Aldrich Co. Ltd, Dorset, UK | Sequestrant |
Diatomaceous earth | Sigma–Aldrich Co. Ltd, Dorset, UK | Filler |
Magnesium oxide | Sigma–Aldrich Co. Ltd, Dorset, UK | Cross-linking agent |
Ingredient | Ex1 | ExII | ExII F1 |
---|---|---|---|
Manugel ® DJX | 14.00% | 14.00% | 14.00% |
Crystacast plaster | 9.00% | 9.00% | 9.00% |
Potassium fluorotitanate | 0.42% | 0.84% | 0.84% |
Tetrasodium pyrophosphate | 3.00% | 3.00% | 3.00% |
Diatomaceous earth | 63.58% | 73.16% | 73.16% |
Magnesium oxide | 10.00% | 10.00% | – |
2.2
Methods
2.2.1
Sample preparation
For commercial materials, the equivalent to one level scoop of powder and one measure of water were mixed in a rubber bowl. For all experimental materials, 10 g powder was mixed with 23 ml water for 45 s. In all cases, the water temperature was 23 °C. Wax molds were used to make rectangular samples measuring 10 mm × 60 mm that were either 1.5 mm or 3 mm thick. In all cases, one mix was used to make one sample only. To make a sample, a wax mold was placed onto a glass plate, and the rectangular cavity of the wax was filled with the mixed alginate then covered with a glass slide. Once the material had set, the glass slide was removed and the alginate sample was carefully cut out of the mold using a scalpel. Similar procedures were used to make specimens for hardness and tear testing.
2.2.2
Measuring dimensional changes
A Chesterman traveling microscope was used to measure dimensional changes in water and artificial saliva (Orthana, A.S. Pharma Ltd, UK). Corresponding studies in air are described elsewhere .
Immediately after preparation, the sample was placed in a polytetrafluoroethylene (PTFE) trough and secured at one end on a fixed pin. A movable pin was inserted into the other end of the sample. The distance (±0.0001 cm) between the fixed pin and the sample edge closest to the movable pin was measured at the following intervals during an 8 h period:
- •
every 5 min for the first hour;
- •
every 15 min for the second hour;
- •
every 30 min for the remaining 6 h.
Five samples of each material (Neocolloid, ExI and ExII) were tested.
2.2.3
Determination of setting behavior
An oscillating rheometer was used to determine setting times. The rheometer was a modification of the instrument first described by Bovis et al. . This instrument subjects the specimen to an oscillating stress of constant amplitude and frequency and measures the resulting oscillating strain profile. The well known ‘wine glass’ profile is obtained as the material sets.
Before starting the experiment, the incubator was set to 37 °C and allowed to stabilize. A flask of ice water connected to the chart recorder by a copper-constantan wire was used as a 0 °C reference point. The chart speed was set at 5 mm/min and the rheometer left to oscillate for 2 min prior to testing the sample, to record the original trace length.
Each commercial alginate was mixed according to the manufacturer’s instructions (experimental materials mixed as specified previously), using tap water at 23 °C. Recording of the oscillations began simultaneously with the time of mixing, to give a true indication of setting time. The mixed alginate was then loaded onto the bottom plate of rheometer, ensuring that the 1.1 mm gap was filled. The top plate was then placed back onto the rheometer and fastened with two bolts. The experiment was terminated after sufficient time had elapsed for the material to set completely. The same procedure was adopted for the experimental materials and five samples of each material were tested. Setting time was defined as the length of time taken for a 40% reduction in chart width.
2.2.4
Shore A hardness
A Congenix Wallace Shore A hardness durometer (Wallace Instruments, UK) was used to determine hardness in accordance with the method specified by the American Society for Testing Materials (ASTM) , over a period of 15 min. A load of 10 N was applied to test specimens.
The sample preparation was essentially that given previously, except that quantities were doubled in order to give sheets of 100 mm × 80 mm × 2 mm. On setting, samples were removed from the mold and cut into three equal strips of 100 mm × 25 mm × 2 mm. For testing, three strips were placed on top of each other to give the required sample thickness of 6 mm. Six readings were taken for each sample at each time point and the mean was used as the reading. Three samples of each material were tested.
Gent has shown that the following relationship exists between Shore hardness and Young’s modulus ( E ) (also referred to as modulus of elasticity), a measure of stiffness:
2.2.5
Tear strength measurement
Tear testing was carried out at room temperature using a 5567 model testing machine by Instron (UK). Sheets of alginate materials were prepared as described above and specimens of 75 mm × 25 mm × 2 mm were cut out using a scalpel. An incision measuring 50 mm was made down the middle of specimen to make a ‘trouser test’ piece . The sample was held in place with clamps and extended at a constant rate of 100 mm/min using a 5 N load cell. Seven samples of each material were tested and the tear energy ( Г ) calculated from:
where Г is the tearing energy (J/m 2 ), F the force (N), and t the thickness (m).
Eq. (2) ignores energy expended to extend and stretch the ‘legs’.
2.3
Statistical analysis
Statistical analysis of the results was carried out using the Mann–Whitney U test.
2
Materials and methods
2.1
Materials
The commercial materials used were: Neocolloid, Zhermack; Palgat Plus, 3M ESPE (both sodium alginates) and Blueprint Cremix, Dentsply DeTrey (potassium alginate). Approximate compositions are given in Table 1 . Each material was mixed according to the manufacturer’s instructions. Neocolloid was the only commercial material used for experiments on dimensional and weight changes after setting. For all other tests, all three materials were used.
Neocolloid (Zhermack) | Palgat Plus (3M ESPE) | Blueprint Cremix (Dentsply) |
---|---|---|
Sodium pyrophosphate | Trisodium phosphate | Disodium orthophosphate |
Zinc oxide | Magnesium oxide | Magnesium oxide |
Diatomaceous earth | Diatomaceous earth | Inorganic filler |
Cristobalite | Sodium alginate | Potassium alginate |
Potassium fluorotitanate | Dipotassium hexafluorotitanate | Potassium hexafluorotitanate |
Calcium sulfate | Calcium sulfate dihydrate | |
Polypropylene glycol | ||
Sodium aluminosilicate |
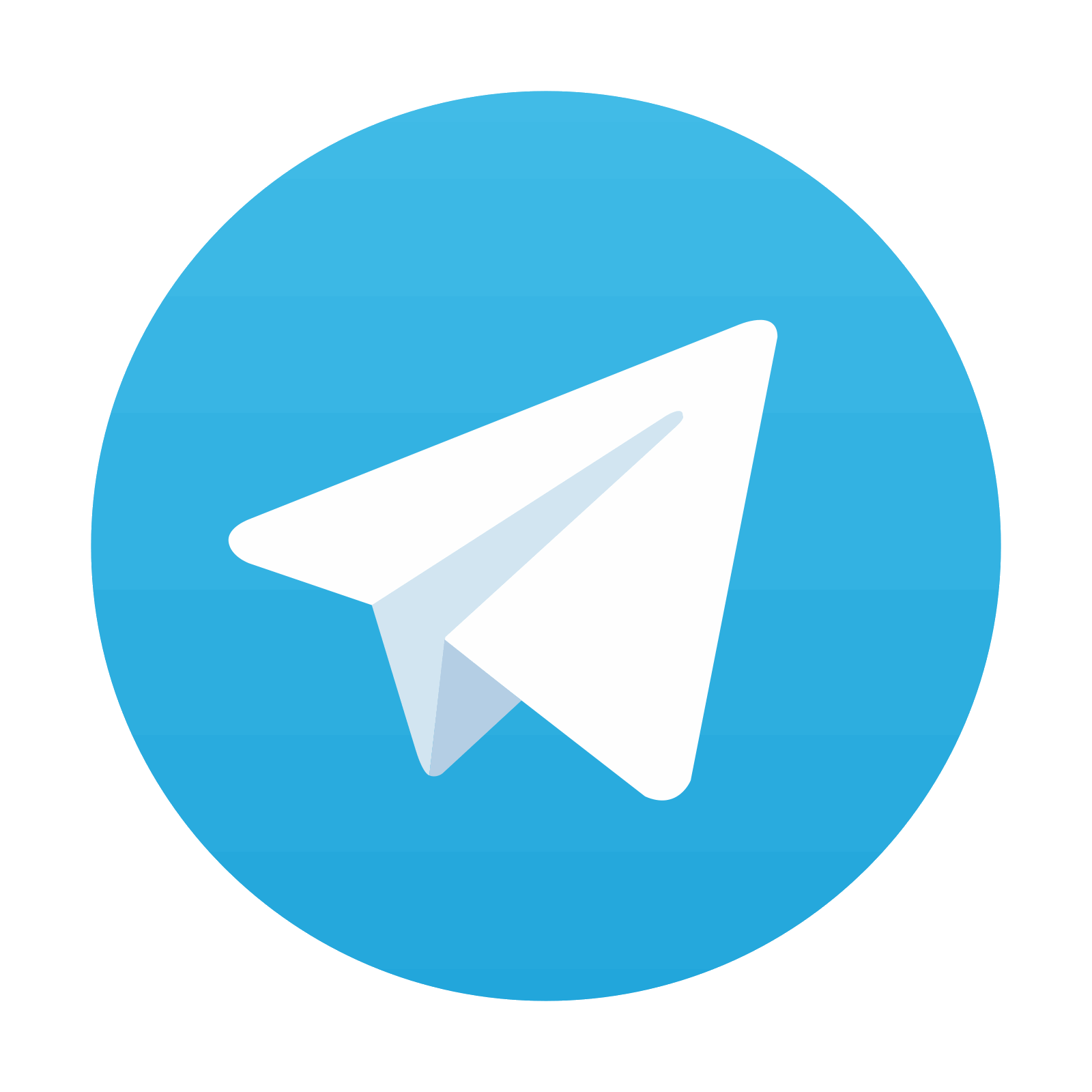
Stay updated, free dental videos. Join our Telegram channel

VIDEdental - Online dental courses
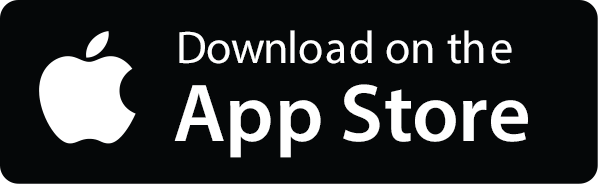

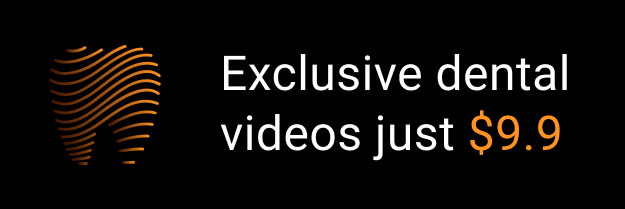