Highlights
- •
Cusp angle of the dental crown is directly proportional to the load-carrying capacity.
- •
Failure always initiated at the centre of the midline of the occlusal surface.
- •
AE activity is significantly pronounced for low cusp angles.
Abstract
Objective
The effect of cusp angle on the load-carrying capacity and failure behaviour of BionZ Diamond zirconia crowns is carried out using experimental and numerical investigations.
Methods
The experimental program using monolithic crowns were divided into three groups (n = 14) for three cusp angles, 60, 80 and 120 degrees and were tested to failure under the static load. A 2-channel acoustic emission (AE) system was used to monitor the failure process while the piezo sensors were attached to the rigid stainless-steel jig for recoding the AE events. Load-displacement and AE response were simultaneously monitored until failure of specimens. Parametric AE analysis was conducted for the factors such as amplitude, energy released, signal duration and cumulative counts, for each AE signal. Fast Fourier transform (FFT) was conducted to assess the frequency at failure. Linear finite element analysis (FEA) was carried out using commercial software Ansys Workbench 19.1 to present the stress distribution and failure modes. Post-failure surface morphology study was carried out using scanning electron microscopy (SEM) and statistical analysis was performed using Weibull analysis.
Results
All the samples in three different groups have failed at the mid-line, splitting the zirconia crowns into two equal pieces. The load to failure was directly proportional to the cusp angle in crowns; 120° group had the highest load-carrying capacity of 2.93 ± 0.26 kN while 60 and 80° groups had a failure load of 2.46 ± 0.53 and 2.52 ± 0.16 kN, respectively. Parametric AE analysis revealed that the failure was instantaneous and 60-degree samples had higher AE signature. FE analysis showed the crack initiation at the occlusal surface of the crown which is in agreement with the SEM images. A close agreement of results for the load and stress distribution from FEA complemented with the experimental study.
Significance
Optimisation of cusp-angle could help clinicians to accurately design the monolithic zirconia crown focussing on maximum load-carrying capacity, increasing the restoration life.
1
Introduction
Computer-aided design (CAD) and computer-aided manufacturing (CAM) monolithic zirconia restorations are becoming more popular in restoring posterior dentition due to their high mechanical characteristics and improvement in their optical properties. To minimise the formation of microscopic flaws during conventional manufacturing which could lead to premature failure, CAD/CAM-based materials were developed in the last two decades to enhance the load-carrying capability and fracture resistance. CAD/CAM technique enabled the development of better structures wherein all the production steps of manufacturing are electronically stored with a higher degree of precision, accuracy and reproducibility [ ]. Monolithic restorations which were introduced to replace multilayer restorations that had experienced challenges such as cracking, fragmenting (chipping) or veneer splitting (delamination). This type of failures could be explained by poor interfacial adhesion between the layers. It was concluded that zirconia-based monolithic crowns offered the best performance (split resistance) in comparison with lithium disilicate and resin-based composite crowns [ ]. Nevertheless, sufficient care needs to be exercised during the manufacturing process using the CAD/CAM technique as the material is highly sensitive to fabrication defects (imperfection/impurity/stress concentration) [ ]. Zirconia is one of the highly preferred ceramics due to its excellent mechanical properties, superior biocompatibility, translucency and minimal adhesion to bacteria [ ]. However, they also come with challenges such as high cost, very high toughness (could cause high wear on opposing occlusal surface, reducing the vertical distance), limited clinical performance data, low-temperature degradation and difficulty to assess any decay under the crown [ , ]. Zirconia is generally used as veneers, posts, fixed partial dentures, implants, abutments, and full or partial crowns. Zirconia crowns are found to have a higher survival rate of up to 97.6% after 7 years [ ].
Cusp angle is the angle made by the slopes of the cusp in buccolingual or mesiodistal directions. In a dental crown, the cusp angle is one of the primary influencing factors for the intricate stress distribution at crown fissure due to complex repetitive external occlusal loads [ ], especially on the crown surface of a monolithic structure [ ]. Several studies have shown that the cusp angle influences the local stress patterns and fracture of the tooth and the root [ ]. Based on the various failure modes of dentin supported zirconia structures, Zhang and Lawn [ ] concluded that the fracture could occur due to intaglio radial cracks initiated below the contact zone or from the occlusal surface.
Acoustic emission (AE) is a proven structural health monitoring (SHM) technique which analyses the transient elastic waves generated during rapid strain energy release when the material structure is changed (failure) [ ]. When a structure is loaded, elastic energy is stored in the material and when the magnitude of stresses exceeds the limiting value, cracks initiate, and the elastic energy is suddenly released and transmitted within the material in the form of stress waves. Piezo-electric based sensing is one of the reliable techniques over several decades for the evaluation of structural failure using AE. In this technique, the mechanical (elastic) energy from the material is converted into an electrical pulse by a piezo-electric surface mounted sensor and suitable for in-situ SHM [ ]. Many studies have been conducted in the past on both metals and non-metals to assess the location of the failure, the intensity of failure, type of failure and residual strength of the structure [ , ] using piezoelectric sensors. Time-domain analysis of individual AE signal yields several parameters such as amplitude, the energy released, signal duration, signal rise time and the number of counts (threshold crossings). Time-frequency analysis provides enhanced noise discrimination and superior source characterisation. AE technique has been used to assess the interfacial debonding and failure behaviour of various dental materials such as ceramics [ , ], resin-based composites [ , ], and fibre reinforced composites [ , ]. Many studies are focussed on the signal amplitude and the number of counts at failure. However, for high strength materials, the amplitude is always around 99 dB (peak value) which deters failure characterisation (initiation, propagation, and failure). Hence, other AE parameters such as energy released, signal duration and counts provide the required scientific insight into the failure analysis [ ].
Though many in-vitro investigations have been performed in the past to assess the failure strength of ceramic crowns [ , , ] and the location of failure initiation [ , ], no study has been conducted covering broad scatter of 60 to 120-degree cusp angles and using acoustic emission to analyse the failure process. The aims of this study are (a) to find an optimised cusp angle with maximum load-carrying capacity subjected to quasi-static compression load till failure of zirconia crowns (b) to understand the state of stress distribution at failure using finite element analysis and (c) to understand the failure behaviour of zirconia crowns using acoustic emission analysis.
2
Materials and methods
2.1
Fabrication of premolar zirconia crowns
Premolar crowns were created for 42 samples on titanium abutment using pattern resin (GC Corporation, Tokyo, Japan) with a buccolingual and mesiodistal diameter of the crown set at ∼8.80 mm while the height of palatal and buccal cusp for all samples was set to 3 mm. Heated angled brass indenters of were used to create the three cusp angle (60°, 80° and 120°) impressions on the resin crown between buccal and palatal cusps. Once cooled, the three resin crowns were scanned with 3Shape D 900 (3Shape, Copenhagen, Denmark) to digital samples both buccolingual and occlusogingival directions. Total of 42 zirconia crowns with 0.8 mm thickness (n = 14 for each cusp angle) were dry milled using a computer-controlled milling machine (Roeders RXD 5, Roeders) from BionZ Diamond (Boinah, Italy) monolithic zirconia discs (98 mm diameter X18 mm thickness) and subsequently, the crowns were sintered (HT-S Speed, MiHM-VOGT, Germany). To confirm the cusp angles of the tested crowns, a profile projector (Nikon) was used and the measured mean and standard deviation values of the three cusp angle are presented in Table 1 (groups A, B and C) along with the measured crown dimensions.
Group | Cusp angle (º) | Buccal length of crown (mm) | Cusp midline to crown base (mm) | Mesiodistal diameter (mm) |
---|---|---|---|---|
A | 58.93 ± 1.88 | 11.78 ± 0.04 | 10.28 ± 1.1 | 8.77 ± 0.06 |
B | 79.92 ± 3.04 | 11.82 ± 0.04 | 9.81 ± 0.07 | 8.87 ± 0.08 |
C | 119.92 + 3.23 | 11.35 ± 0.09 | 10.09 ± 0.25 | 8.74 ± 0.05 |
2.2
Finite element analysis
Models of the tooth corresponding to the cusp angles 60, 80 and 120 degrees were designed in SolidWorks 2016. The geometric models suffice the requirement as the stress concentration is at the midline of the crown. The 3D geometric models were then exported to commercially available finite element (FE) software, ANSYS Workbench v19.1 and meshed using tetrahedron elements and a mesh convergence study was carried out for the developed model. Assumptions are made such as the structure is free from all inherent defects and the bonding between crown-cement and cement-base are perfect. Boundary conditions such as; base nodes of the crown are fixed in all directions and a static compressive load is applied to each of the cusp surfaces. Mohr-Coulomb failure theory suitable for brittle materials such as glass and ceramics was used to determine the failure load which states that the failure in brittle material occurs when <SPAN role=presentation tabIndex=0 id=MathJax-Element-1-Frame class=MathJax style="POSITION: relative" data-mathml='σ1Sut+σ3Suc<1.0′>(?1???+?3???)<1.0σ1Sut+σ3Suc<1.0
σ 1 S u t + σ 3 S u c < 1.0
[ ], where <SPAN role=presentation tabIndex=0 id=MathJax-Element-2-Frame class=MathJax style="POSITION: relative" data-mathml='σ1′>?1σ1
σ 1
= maximum principal stress, <SPAN role=presentation tabIndex=0 id=MathJax-Element-3-Frame class=MathJax style="POSITION: relative" data-mathml='σ3′>?3σ3
σ 3
= minimum principal stress, <SPAN role=presentation tabIndex=0 id=MathJax-Element-4-Frame class=MathJax style="POSITION: relative" data-mathml='Sut’>???Sut
S u t
= ultimate tensile strength and <SPAN role=presentation tabIndex=0 id=MathJax-Element-5-Frame class=MathJax style="POSITION: relative" data-mathml='Suc’>???Suc
S u c
= ultimate compressive strength. The material properties used for the FE analysis are presented in Table 2 . This failure theory defines a linear relationship between the normal stress (maximum principal) and shear stress (minimum principal) at failure, which is more suited for materials with a high value of compressive strength in comparison with tensile strength. Maximum principal stresses and corresponding load were recorded when the Mohr-Coulomb safety factor is 1.0 (stress = material strength).
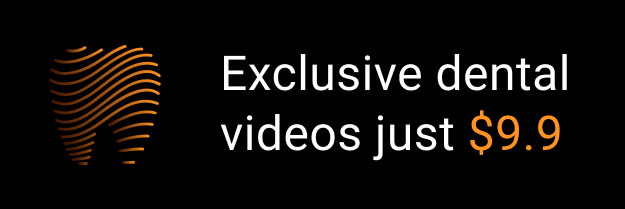