Abstract
Objective
To determine the mechanical properties of a newly-developed CAD/CAM resin composite block and compare with other resin composite blocks and a polymer-infiltrated ceramic block.
Methods
Experimental composite block was formulated by our proprietary resin and filler technologies and cured via Hot Isostatic Pressing (HIP). Bar-shaped specimens (1 × 4×12 − 13 mm, n = 10) for flexural strength, flexural modulus and modulus of resilience were sectioned from block materials and measured in accordance to modified ISO-6872. Cylinder specimens for compressive strength (2 × 4 mm, n = 8) and for diametral tensile strength (6 × 3 mm, n = 8) were milled from the block materials and tested according to ASTM-D695 and ANSI/ADA-Specification #27, respectively. Block specimens (5 mm, n = 3) for Vickers hardness were polished and measured for five indentations on each specimen. The data was analyzed by one-way ANOVA and post-hoc Tukey tests (p ≤ 0.05).
Results
Experimental composite block showed higher or significantly higher flexural strength, flexural modulus, modulus of resilience, compressive strength, diametral tensile strength and Vickers hardness than the other commercially available block materials except Vita Enamic for flexural modulus and hardness and Cerasmart for modulus of resilience. Some positive correlations were observed among the different mechanical properties.
Significance
New composite block exhibited higher mechanical properties as compared to commercially available composite block materials. Superior mechanical properties for resin composite block materials were obtained by composite and curing processing technologies. Resin composite blocks with higher mechanical properties are good options for the fabrication of CAD/CAM indirect restorations.
1
Introduction
The application of computer-aided design and manufacturing (CAD/CAM) in dentistry for indirect dental restorations has remarkably increased during the last decade. Dental restorations generated by CAD/CAM can meet standardized manufacturing processes, provide good reproducibility and reduce production cost. Moreover, CAD/CAM technology can process a variety of restorative materials such as glass–ceramics/ceramics, composite and acrylic resins due to the introduction of new digitalization technologies and tools [ , ].
Glass–ceramics/ceramics and resin-based composites currently are two major categories of the machinable esthetic materials used in the production of CAD/CAM restorations. Glass–ceramics/ceramics are strong and stiff due to their higher elastic modulus [ ], and generally exhibit good mechanical and esthetic properties, but they are brittle and susceptible to chipping during the milling process [ ].
Over the past decade, resin-based composites have been significantly improved due to advances in composite technology and have been expanded to CAD/CAM systems for the fabrication of indirect restorations such as inlays, onlays, veneers, crowns and bridges [ ]. The first resin composite block for CAD/CAM systems was Paradigm MZ100 (3M ESPE, USA) launched in 2000. Paradigm MZ100 block was made based on 3M™ Z100™ direct resin composite and contains 85 wt.% ultrafine zirconia–silica ceramic fillers [ ]. It is reported that, flexural strength, flexural modulus, compressive strength and diametral tensile strength are 146 MPa, 12.7 GPa, 524 MPa and 114 MPa, respectively [ ]. Later, 3M ESPE developed the Lava Ultimate block by utilizing a so-called resin nano ceramic material, which contains about 80 wt.% of zirconia–silica nano ceramic fillers [ ]. Flexural strength (204 MPa) was significantly improved compared to Paradigm MZ100. Similar to Lava Ultimate block, GC (GC Corporation, Japan) marketed Cerasmart as a hybrid ceramic block that contains 75 wt.% of nano ceramic particles in a highly cross-linked resin matrix [ ]. It showed a high flexural strength (231 MPa). Although these new composite block materials are different in composition and curing condition, they are actually made by conventional filler-resin mixing composite technology. VITA (VITA Zahnfabrik, Germany) launched Vita Enamic, a truly hybrid ceramic for CAD/CAM restorations, by introducing the Polymer-Infiltrated-Ceramic Network (PICN) technology. A porous ceramic network (86 wt.%) was first formed and then infiltrated by polymeric resins [ ], which provides a new way to increase filler loading capacity. Vita Enamic exhibited significantly higher modulus of elasticity (30 ± 2 GPa) and hardness (2.5 GPa) [ ] than composite block materials made by mixing fillers and polymeric resins.
Compared to glass–ceramics/ceramics, CAD/CAM composites blocks are easily fabricated and repaired [ , ], they have better machinability and thus lower tendency to marginal chipping [ , , ]. Although mechanical properties have been improved due to new formulation developments, optimized polymerization processes and new innovations, composite blocks generally are still not as strong as glass–ceramics/ceramics materials based on mechanical properties. The ideal composite block restorative material for CAD/CAM system is a combination of certain properties of ceramics such as durability with properties of resin composite such as an elastic modulus similar to dentin. The objective of this study is to report on the development of a new CAD/CAM resin composite block with favorable mechanical properties and compare it with other commercially available composite block materials. The hypothesis is that this new CAD/CAM composite block has more favorable mechanical properties than conventional CAD/CAM resin composite blocks.
2
Materials and methods
2.1
Materials
Experimental composite block was formulated by our proprietary resin and filler technologies and cured via Hot Isostatic Pressing (HIP) process. Homogeneous resin mixtures were made by stirring resin monomers with a thermal initiator and additives until dissolved. The resulting resin mixtures were further mixed with fillers until a uniform paste was formed. Composite pastes were cured under high temperature and high pressure via hot isostatic pressing (HIP) (180 °C and 300 MPa). Six commercially available CAD/CAM blocks, including five resin composite blocks (Paradigm MZ100, Lava Ultimate, Grandio blocs, Cerasmart and Shofu Block HC) and one hybrid ceramic block (Vita Enamic), were selected for comparison in this study. Further information about the block materials studied is shown in Table 1 .
Material | Manufacturer | Type | Resin | Filler | Filler content (%) |
---|---|---|---|---|---|
Exp | Glidewell | Resin composite | BisGMA, UDMA, TEGDMA | Silica and barium micro/nanoparticles | 82.5 |
Paradigm MZ100 | 3M ESPE | Resin composite | BisGMA, TEGDMA | ultrafine zirconia–silica ceramic particles | 85 |
Lava Ultimate | 3M ESPE | Resin composite | BisGMA, UDMA, BisEMA, TEGDMA | Silica and zirconia nanoparticles and nanoclusters | 80 |
Cerasmart | GC | Resin composite | BisMEPP, UDMA, DMA | Silica and barium nanoparticles | 75 |
Grandio blocs | VOCO | Resin composite | UDMA,DMA | Nanosilica and barium glass | 86 |
Shofu Block HC | Shofu | Resin composite | UDMA, TEGDMA | Silica, fumed silica and zirconium silicate | 75 |
Vita Enamic | Vita | Hybrid ceramic | UDMA, TEGDMA | Feldspar ceramic enriched with aluminum oxide | 86 |
2.2
Flexural strength, flexural modulus and modulus of resilience
Flexural strength, flexural modulus and modulus of resilience were determined by three-point bending method in accordance with ISO-6872 [ ] modified. The bar-shaped specimens (thickness × width × length = 1 mm × 4 mm × 12 – 13 mm, n = 10) were sectioned from block materials using saw machine (IsoMet High Speed Pro, Buehler) and tested under crosshead speed of 0.75 mm/min by using a test fixture with a 10 mm support span on an Instron 5564 universal testing machine. Flexural modulus was determined from the slope of the linear region of the stress-strain curve. Modulus of resilience was determined from the area under the elastic portion of the stress-strain curve. The following formulas were used to calculate the flexural strength, flexural modulus and modulus of resilience:
where P is the maximum load (N), l is the test span (mm), w is the width of the specimen (mm), b is the thickness (mm) of the specimen, and s is the slope of the linear portion of the stress-strain curve (N/mm).
2.3
Compressive strength
The cylinder specimens (diameter × height = 2 × 4 mm, n = 8) were milled from block materials on a Glidewell Laboratories TS150™ mill system. Compressive strength was tested according to the ASTM-D695 [ ] under the testing speed of 0.75 mm/min. on an Instron 5564 universal testing machine.
2.4
Diametral tensile strength
The disk specimens (diameter × height = 6 × 3 mm, n = 8) were milled from block materials on a Glidewell Laboratories TS150™ mill system. Diametral tensile strength was tested according to the ANSI/ADA- Specification #27 [ ] under the testing speed of 1.0 mm/min. on an Instron 5564 universal testing machine.
2.5
Vickers hardness
Test specimens (5 mm thickness, n = 3) were prepared by sectioning from the block materials and were embedded in acrylic resin mixed with powder. All specimens were wet polished sequentially with 80, 500, and 1200 grit SIC, followed by 3 μm diamond suspension on Grinder-Polisher (EcoMet 300 Pro, Buehler). Vickers Hardness was measured for five indentations made on each test specimen with a load of 19.61 N and a dwell time of 10 s under a micro Vickers hardness tester (HMV-G, Shimadzu) based on ASTM C1327 modified [ ], and calculated based on the formula:
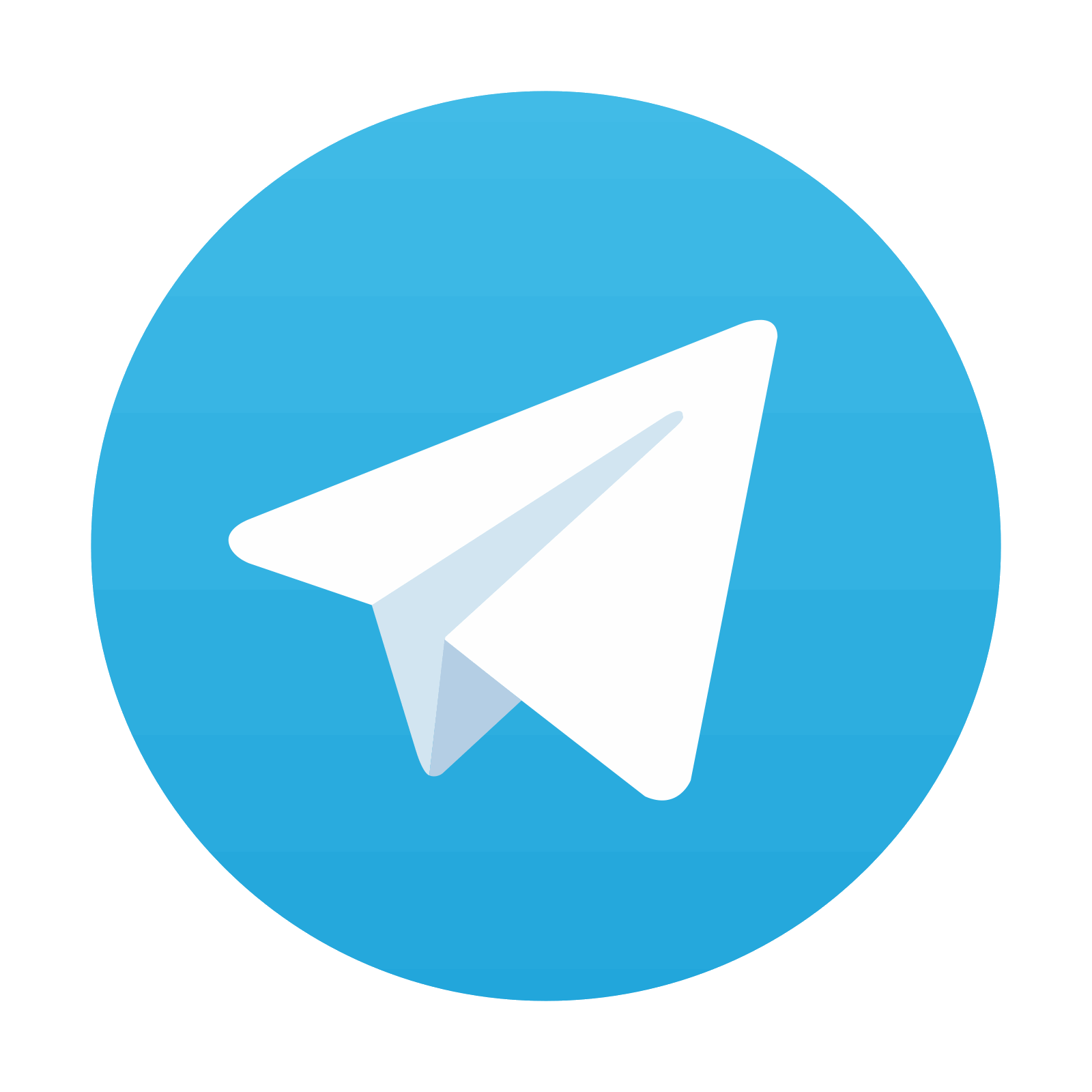
Stay updated, free dental videos. Join our Telegram channel

VIDEdental - Online dental courses
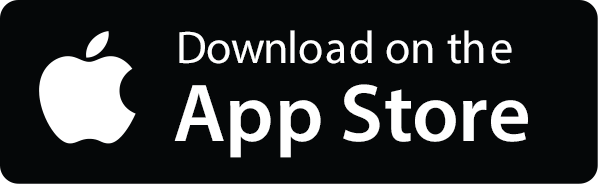

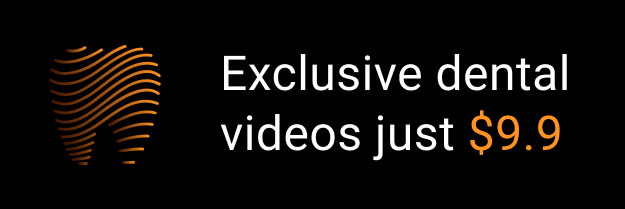