7 Orthodontic Brackets
Biofilm formed intraorally after an hour on polycarbonate bracket raw material (polarized light image) Original magnification × 50
Introduction and Early Research
Wettability and Potential for Plaque Accumulation
Bracket Slot-Archwire Friction
Experimental Approaches and Instrumentation
Introduction
Orthodontic brackets bonded to enamel provide the means to transfer the force applied by the activated archwire to the tooth. The evolution of this appliance, originally manufactured from stainless steel, has demonstrated a unique progress curve characterized by extended quiescent periods interspersed with notably active periods.
The original treatment approach utilized a slot attached to a stainless steel band that was cemented to the tooth, and early attempts to modify this attachment resulted in wide base surfaces onto which a slot was soldered. This appliance was then bonded to the tooth with the use of epoxy resin. Although some reports list these advances as occurring in the 1960s, it was not until the late 1970s that direct bonding to enamel (Chapter 5) was widely accepted as a standard procedure to replace banding. The reasons for this significant delay arose from the initial reluctance of the orthodontic community to adopt the concept of etching tooth enamel. While the advances in bracket design and manufacturing include the three general aspects of base morphology, base-slot connection, and slot size characteristics, this chapter is concerned with the materials science of brackets, i.e., mainly the first two general aspects. Slot prescriptions are named for their inventors who advocated a variety of angular values, depending upon treatment philosophy and mechanotherapeutic approaches.
The next stage of bracket evolution included modification of the base design to provide higher bond strength with adhesives, while concurrent efforts focused on decreasing the base surface, which at that time covered almost the entire labial mesiodistal tooth surface. While bracket manufacturing had traditionally employed mechanical deformation or wrought processing techniques to fabricate these appliances, further research led to the additional use of injection molding to fabricate cast brackets. A variety of standardized bracket types, such as twin, mini, and single appliances, were offered to the profession.
Subsequent research resulted in the introduction of brackets that had greatly improved aesthetic appearances compared to the metal brackets. These brackets have become popular with the greatly increased number of adult orthodontic patients. The percentage of adult patients increased dramatically in the mid 1980s to 25% of the total number of orthodontic patients, compared to very low percentages during the 1970s. Early commercially available aesthetic products included both plastic brackets and ceramic brackets fabricated from either polycrystalline or single-crystal alumina. While extensive commercial marketing of these products initially occurred during the mid 1980s, the first transparent bracket materials date back to the 1960s and the novel approaches and pioneering work of Newman and his coworkers.
The thicker profile of the initial ceramic brackets caused slight discomfort for some patients. However, the most serious clinical problem was the incidence of enamel damage during debonding and the occasional occurrence of bracket tie-wing fracture during therapy and subsequent debonding. Enamel cracking was promoted by the use of silane coatings on the base to increase bond strength, as well as by the use of crystal projections on the base to increase the active bonding surface available. Bracket wing fracture arose from the completely brittle nature of alumina, with crack propagation occurring more readily in the single-crystal (sapphire) form of this ceramic, as discussed in Chapter 1.
Plastic orthodontic brackets have also presented problems with the transfer of forces from an activated archwire. The low elastic modulus of the plastic can result in distortion of the appliance when the bracket is subjected to substantial forces in vivo. Some absorption of colorants was also noted with the first generation of these appliances. During the 1990s the manufacturers developed brackets with essentially no adverse clinical effects by modifying the design of the appliance and by using new reinforced polycarbonate plastic brackets. Recently, a wide array of polycarbonate brackets, with or without a metal slot, has become available. In contrast, there appears to have been a significant decrease in the number of brands of ceramic brackets. Tables 7.1 and 7.2 list some currently available plastic and ceramic bracket products.
Product Name | Raw Material | Manufacturer/Country |
Aesthetic Line | Polycarbonate-glass fibers | Forestadent/Germany |
DB Fibre | Polycarbonate-composite | Leone/Italy |
Elan | Polycarbonate-composite | GAC International/USA |
Envision | Polyurethane-composite | Ortho Organizers/USA |
Image | Polycarbonate-glass fibers | Gestenco/Sweden |
Plastic | Polycarbonate | Dentaurum/Germany |
Quantum | Plastic | Masel/USA |
Value Line | Thermoplastic-polyurethane | OREC/USA |
Spirit |
Fiber-reinforced polycarbonate |
Ormco/USA |
In describing bracket evolution, it is important to include the introduction of the self-ligating bracket. This was the result of an effort to develop a reliable appliance that would maintain steady force levels during activation while providing decreased frictional resistance and optimum three-dimensional control of tooth movement. An important characteristic of these appliances documented through both in vitro and in vivo studies is the potential elimination of cross-contamination through the avoidance of elastomeric ligatures. Their use, however, has not become widespread, presumably because of the lack of interchangeable auxiliaries with conventional brackets and the necessity for maintaining an inventory of suitable utilities. From a materials science perspective, those materials are basically identical to their conventional counterparts, and thus these products will not be described in this chapter.
Product Name | Raw Material | Manufacturer/Country |
Allure NSB | Polycrystalline alumina | GAC International/USA |
Add another bracket: Contour | Polycrystalline alumina | Class One Orthodontics/USA |
Clarity | Polycrystalline alumina | 3M Unitek/USA |
Eclipse | Alumina-plastic base | Masel/USA |
Fascination | Polycrystalline alumina | Dentaurum/Germany |
Hi-Brace | Polycrystalline zirconia | Toray Ceram/Japan |
Intrigue | Polycrystalline aluminia | Lancer Orthodontics/USA |
Lumina | Polycrystalline alumina | Ormco/USA |
MXi | Polycrystalline alumina | TP Orthodontics/USA |
Signature | Polycrystalline alumina | RMO/USA |
Starfire TMB | Single-crystal alumina | “A” Company-Ormco/USA |
20/20 |
Polycrystalline alumina |
American Orthodontics/USA |
Metallic Brackets
Introduction and Early Research
Stainless steel brackets have been used for decades with highly successful clinical results. The morphology of the base, which is composed of a metal mesh, yields adequate adhesive bond strength values to enamel (discussed in Chapter 5) that meet the demands of in vivo orthodontic forces. Early studies, including research by Gwinnett and his colleagues, determined the optimum mesh size for increased bond strength. Extensive analyses of the rheo-logical properties of the adhesive pastes have been performed, and it has been found that viscosity is principally controlled by the filler content volume. Manufacturers have incorporated a variety of mesh designs in their currently marketed products. Recent investigations, however, were not able to identify any differences in bond strength between conventional bracket bases and bases with more condensed mesh configurations. This may be because the base sizes chosen exceeded the optimum range for clinical use.
Advances in Metallic Brackets
Despite the clinically sufficient bond strength provided by conventional metal brackets, some attempts have focused on increasing the strength of the bracket-adhesive interface. The goal is to achieve bond longevity and integrity throughout treatment for those special occasions where the currently available bond strength levels are insufficient. Droese and Diedrich have plasma-coated metal bracket bases having a variety of mesh designs as well as ceramic bracket bases. They reported that the enormously increased active surface area of the base resulted in much greater mechanical interlocking. For metal brackets, the non-mesh, plasma-sprayed bases had tensile adhesive bond strengths similar to those for un-sprayed mesh bases. However, plasma-sprayed ceramic brackets did not yield similar results, and it was concluded that these brackets are not good candidates for this procedure.
There have been some potentially alarming reports on the corrosion potential of the AISI type 316L austenitic stainless steel alloy currently used for bracket manufacturing. This alloy contains 16–18% Cr, 10–14% Ni, 2–3% Mo and a maximum of 0.03% C (values in wt%); the “L” designation refers to the lower carbon content compared to type 316 stainless steel, which contains a nominal maximum amount of 0.08 wt% C. The 316L stainless steel contains somewhat more nickel, somewhat less chromium, and substantially less carbon than the AISI types 302 and 304 stainless steel archwire alloys (Chapter 4), along with a small amount of molybdenum that is not present in the latter. (All of these stainless steel alloys also contain a nominal amount of 2 wt% Mn.) Although the 316L stainless steel bracket alloy has performed well clinically, some corrosion of this material may be identified in the form of discoloration of the underlying adhesive layer (Fig. 7.1). Maijer and Smith have attributed this effect to the diffusion of corrosion products from the bracket base to the adhesive, noting also the potential for enamel discoloration. As discussed in Chapter 4, the corrosion resistance of stainless steel is provided by a passive surface film of chromium oxide; the corrosion resistance of titanium and its alloys is provided by an analogous passive film of titanium oxide. While the addition of molybdenum to the 316L stainless steel alloy provides further protection from crevice and pitting corrosion, the chromium oxide passive films are not as stable as their titanium oxide counterparts.
Fig. 7.1 Corrosion attack of 316L stainless steel alloy identified following debonding where corrosion products have diffused into the adhesive layer, causing discoloration
Clinical interest in the in vivo corrosion attack of metal brackets derives from the potential adverse biological consequences, as discussed in Chapter 15. The chief concern is the release of nickel ions during corrosion of stainless steel. It was previously noted in Chapter 4 that nickel is incorporated in the compositions of all austenitic stainless steel alloys to stabilize the austenite phase.
Aesthetic Brackets
Many types of aesthetic brackets have been introduced during the past decade. Appliances fabricated from alumina and zirconia ceramics, as well as a variety of plastic brackets, have been marketed. Consideration of the compositions, manufacturing, and properties of these brackets may clarify several issues pertinent to their clinical performance.
A 2205 stainless steel alloy that contains half the amount of nickel found in the 316L alloy has recently been proposed by Oshida, Moore and their colleagues as an alternative for orthodontic brackets. The 2205 stainless steel alloy has a duplex microstructure consisting of austenitic and delta-ferritic phases, and is harder than the 316L alloy. Moreover, the 2205 alloy demonstrated substantially less crevice corrosion than the 316L alloy when coupled with NiTi, β-titanium, or stainless steel archwires in an in vitro immersion test using an aqueous NaCl solution at 37 °C.
Use of the 2205 stainless steel alloy for brackets also follows from recent research by Matasa, who measured the microhardness values (Chapter 1) of metallic brackets to obtain information about the relative strengths of the bracket alloys. It was found that the 316L alloy had much lower hardness compared to the PH (precipitation-hardening) 17–4 stainless steel bracket alloy, although the former had significantly higher corrosion resistance. Further research is needed to find the stainless steel alloy with an optimum combination of strength and corrosion resistance for orthodontic brackets.
Some recently reported evidence on the feasibility of manufacturing titanium brackets by metal injection molding (MIM) may open new horizons for the metallic appliances. The brackets tested exhibited mechanical properties and bond strengths equivalent to or better than that of stainless steel brackets, while the new alloy provides better corrosion resistance and absence of nickel leaching.
As the process of optimizing materials for orthodontic applications gains increasing interest, a new generation of metallic appliances may be developed minimizing the concerns about adverse biological reactions.
Plastic Brackets
The first plastic brackets were manufactured from unfilled polycarbonate and introduced during the early 1970s. Unfortunately, these brackets had a tendency to undergo creep deformation when transferring torque loads generated by archwires to the teeth. Ceramicreinforced, fiberglass-reinforced, and metal slot-reinforced polycarbonate brackets were subsequently introduced to alleviate this problem. Another problem was discoloration of the first-generation unfilled polycarbonate brackets during clinical aging.
The reinforced polycarbonate brackets were also introduced in response to reports of enamel damage by ceramic brackets. The primers that were used to prepare the base for bonding have gradually been eliminated so that this clinical step would be avoided during bracket placement on the etched enamel surface. These primers contain low-molecular-weight dimethacrylates and methyl methacrylate, producing a surface that facilitates micromechanical interlocking (Fig. 7.2).
While the metal slot-reinforced polycarbo-nate brackets appear to be capable of generating the desired torque on teeth under clinical conditions, problems have been reported with the integrity of the slot periphery. Some of the metal slots have a level of surface roughness that may significantly affect the archwire-bracket sliding friction (Fig. 7.3). A beneficial consequence of the relatively low elastic modulus of polycarbonate is that the load applied during debonding of the plastic brackets results in a peel-off effect, mimicking the debonding behavior of metal brackets (Figs. 7.4 and 7.5). Further research is needed on the bond strength, torque delivery, clinical aging, and creep properties of the currently available poly-carbonate brackets.
Fig. 7.2 Secondary electron images of the base of a polycarbonate bracket. (a) As-received. Original magnification ×60. (b) Following application of a methacrylate-based primer, depicting the dramatically increased roughness used to facilitate micromechanical interlocking with the adhesive. Original magnification ×60. The plasticity (flow) of the primer greatly increases the surface roughness and exposes some fibers from the poly-carbonate matrix
Fig. 7.3 Secondary electron images of a polycarbonate bracket with metallic slot, demonstrating increased roughness of the slot surface opposing the archwire. (a) Lateral view. Original magnification ×60. (b) Lateral view. Original magnification ×150. Note the incomplete adaptation of the metallic slot base to the bracket wall
Fig. 7.4 Polycarbonate bracket exhibiting bending distortion during debonding, where the pattern mimics the peel-off debonding of stainless steel brackets. Note the bending of the bracket wings
Fig. 7.5 Secondary electron images of the debonded poly-carbonate bracket shown in Fig. 7.4. Original magnification ×48. (a) Twisting-like bending of the tie-wing caused by application of the debonding forces. Note the breakage and projection of the fibers caused by twisting of the tie-wing following debonding. (b) Distortion of the slot width as a result of the compressive force applied during debonding
Ceramic Brackets
Composition, Structure and Manufacturing Process
Most ceramic brackets are made of high-purity aluminum oxide (alumina), and the brackets are available in both polycrystalline and single-crystal (sapphire) forms. Alumina brackets were first introduced in the late 1980s. Ceramic brackets fabricated from polycrystalline zirconium oxide (zirconia) were subsequently manufactured in Australia and Japan.
Polycrystalline alumina brackets are manufactured by first combining a suitable binder with aluminum oxide particles (average of 0.3 μm size) so that this mixture can be molded into the shape of a bracket. This molded mixture is then heated (fired) at temperatures in excess of 1800 °C to burn out the binder and achieve sintering of the particles. Diamond cutting tools are then used to machine the slot dimensions. Heat treatment is subsequently performed to relieve stresses caused by the cutting and to remove surface imperfections resulting from the manufacturing processes.
The sintering produces a polycrystalline alumina microstructure with grain boundaries (Chapter 1), resulting in some translucency. There is loss of light transmission through the ceramic because of a small variation in refractive index with crystallographic direction within grains and scattering processes at the grain boundaries. Optical properties and strength are inversely related for the poly-crystalline alumina ceramics: the larger the individual grains in the microstructure, the greater is the ceramic translucency. However, when the grain size approaches 30 μm, the material becomes substantially weaker. Heat treatment after machining the slots must be carefully controlled to prevent grain growth that would degrade the physical properties. While the manufacturing process readily allows alumina brackets to be molded to the desired geometry, structural imperfections at the grain boundaries or trace amounts of sintering aids (concentrations as low as 0.001%) can serve as sites of crack initiation under stress.
The first step in the manufacture of the single-crystal brackets is the slow cooling of molten high-purity aluminum oxide under controlled conditions from temperatures above 2100 °C. The resulting bulk single-crystal alumina in rod or bar form is then milled into brackets using diamond cutting, Nd:YAG lasers, or ultrasonic cutting. The single-crystal brackets are also subsequently heat treated to remove surface imperfections and stresses created by the milling process.
The single-crystal alumina brackets contain less impurities than are found in the poly-crystalline alumina brackets, which require the presence of sintering aids during manufacturing. Single-crystal brackets also have excellent optical clarity owing to the absence of internal grain boundaries, although there is a minor amount of birefringence resulting from variation of the refractive index with crystallo-graphic direction. Physical properties of single-crystal and polycrystalline alumina brackets are listed in Table 7.3. Once fracture initiation has occurred at Griffith flaws (Chapter 1) under sufficiently high local stresses, single-crystal alumina has lower resistance to crack propagation than does polycrystalline alumina, where the advancing cracks follow irregular paths along grain boundaries. Figures 7.6 and 7.7 are scanning electron microscope (SEM) photographs of fractured tie-wings, illustrating the difference in crack propagation behavior for single-crystal and polycrystalline alumina brackets.
Property | Single-Crystal Alumina (sapphire) | Polycrystalline Alumina (99.9% purity and sintered) |
Modulus of elasticity (GPa) | 430 | 390 |
Bending strength (MPa) | 630 | 280 |
Compressive strength (MPa) | 2100-4100 | 2400 |
Tensile strength (MPa) |
1800-2600 |
210-310 |
From Swartz, 1988. Reprinted with permission from JCO, Inc
Fig. 7.6 Secondary electron image of the tie-wing fracture site for compressive loading of a Starfire TMB single-crystal alumina bracket. Scale bar length = 10 μm. (From Sonneveld et al, 1993. An abstract describing this study is found in Sonneveld et al, 1994)
The strength of both single-crystal and poly-crystalline alumina can be increased by eliminating surface flaws that can serve as sites of stress concentration and fracture initiation. Decreasing the grain size will also increase the strength of polycrystalline alumina. The properties of surgical grade alumina are summarized in Table 7.4.
There has been interest in zirconia brackets because of the possibility of achieving much higher values of fracture toughness than are possible for polycrystalline alumina brackets, as discussed at length in a later section. The polycrystalline zirconia brackets are manufactured by impression molding, followed by hot isostatic pressing. Yttrium oxide-partially stabilized zirconia (YPSZ) can be obtained in bulk form by sintering (without pressure up to 95% of the theoretical density) a mixture of ultrafine zirconia powder (average starting particle size of 0.2 μm) and 5 wt% yttrium oxide. A polycrystalline microstructure with an average grain size of about 0.5 μm is obtained, and hot isostatic pressing is subsequently employed to remove residual porosity with limited additional grain growth. Table 7.3 compares the properties of surgical grade alumina and YPSZ in bulk form.
Fig. 7.7 Secondary electron image of the tie-wing fracture site for compressive loading of a Transcend 2000 polycrystalline alumina bracket. Scale bar length = 10 μm. (From Sonneveld, 1993. An abstract describing this study is found in Sonneveld et al, 1994)
Fig. 7.8 Secondary electron image of the base of a polycrystalline alumina bracket employing large recesses for mechanical interlocking with the adhesive resin. Original magnification ×160
Base Morphology
Several papers published during the mid-1990s dealt with the description of the ceramic bracket base design, structure, and composition, and the associated mechanisms for retention to the etched enamel. Microscopic and spectroscopic analyses employed for study of the structure and morphology of the bases have provided some clarification of the bracket manufacturing processes. The bonding mechanisms that have been identified may be classified into three major categories:
• Mechanical retention employing large recesses (Fig. 7.8)
• Chemical adhesion facilitated by the use of a silane layer (Fig. 7.9)
• Micromechanical retention through the utilization of a number of configurations, including protruding crystals, grooves, a porous surface, and spherical glass particles (Fig. 7.10).
Fig. 7.9 Incident polarized light image of the base of a single-crystal ceramic bracket covered with an island of a silane layer, illustrating a birefringence effect. Bright field image, crossed polarizers. Original magnification ×50
Fig. 7.10 Bases of polycrystalline brackets employing various protrusion d/>
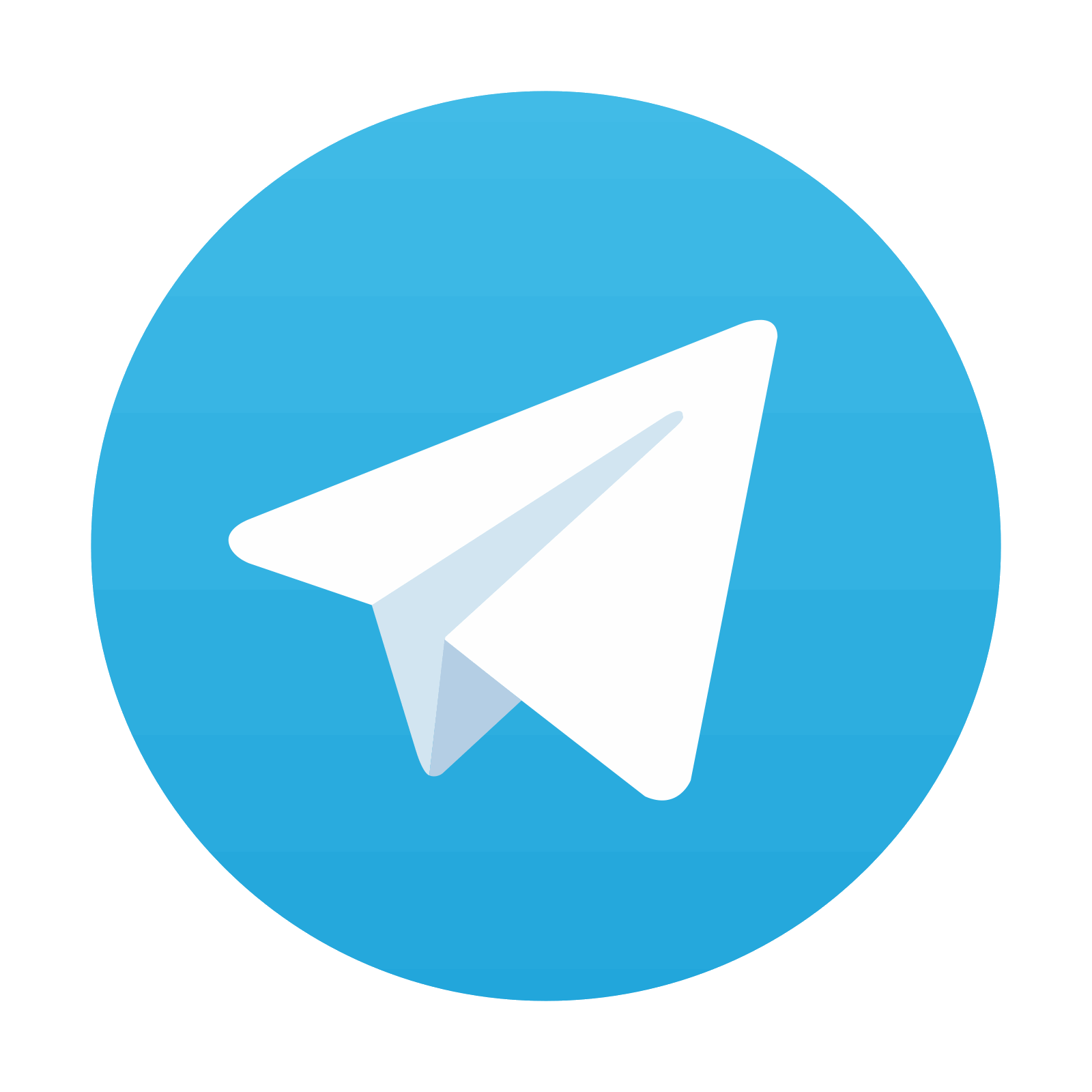
Stay updated, free dental videos. Join our Telegram channel

VIDEdental - Online dental courses
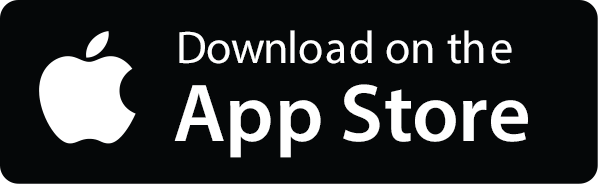
