Stainless steel
Introduction
Most of us are familiar with stainless steel as a widely used quality product for both domestic and industrial applications. However, it is also extensively used in medical and dental applications, such as for the production of dental instruments, e.g. scalpel blades and forceps, orthodontic wires, denture bases and partial denture clasps, endodontic posts and as stainless steel crowns for the treatment of severely decayed primary molars. The material has generally been heavily worked to give it the desired shape and is therefore defined as a wrought alloy.
A wrought alloy distinguishes itself from the many casting alloys used for the construction of crowns and bridges in that it is a cast alloy which has been formed by mechanical processing such as rolling, extrusion or drawing to give it a new desired shape. When this is done at a low temperature, the mechanical processing is known as cold working, by which the metal is simultaneously shaped and strengthened (Figure 3.9.1). If the process is carried out at high temperatures, this is called hot working and generally involves shaping without strengthening. No strengthening occurs because the metal continually recrystallizes and the amount of deformation that can be performed is virtually limitless.
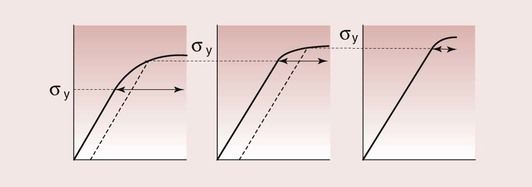
Many alloys besides stainless steel are available in wrought form, such as gold alloys for posts and denture clasps, Ni–Ti alloys for orthodontic wires and endodontic files, and Co–Cr–Ni alloys for denture clasps and orthodontic wires. However, only stainless steel will be considered in detail in this chapter.
Steels are available in a wide variety of compositions, with each having very specific properties that are carefully tailored to suit their particular application. One feature of steels that makes them such popular materials is the enormous range of mechanical properties that can be obtained with only small changes in composition. A comparison of steel to other products is shown in Table 3.9.1. The steel wires show a wide range of strengths, which the other materials cannot match.
Table 3.9.1
A comparison of fracture or yield strengths of steels with other materials
Material | Fracture or yield strength (MPa) |
Steel wire | 300–2800 |
Bulk steel | 300–800 |
Iron | 150–200 |
Brass | 200–400 |
Aluminium alloys | 200–600 |
Copper alloys | 300–600 |
Titanium alloys | 600–1100 |
Glass | 50–150 |
Carbon fibre | 2200–2800 |
Before the introduction of stainless steels in dentistry (generally in the early 1930s), the only metal that was felt to have good enough corrosion resistance to allow it to be used in the mouth was gold. Stainless steel possesses a high tensile strength, and is used to form springs in removable orthodontic appliances. It is also used in fixed appliances for construction of bands, brackets and arch wires. In fact, virtually all the components for fixed appliances used in orthodontics can be constructed out of stainless steel.
Orthodontic wire is made from what is known as austenitic stainless steel. This is a form of steel that can be readily shaped into a wire by rolling and subsequent extrusion through dies. This elongates the grains into long fibrous structures which run in the direction of the wire.
More specifically, the material used for orthodontic wires is known as a stabilized austenitic stainless steel. The best way of describing this material is to take the raw material, iron, and develop it, step by step, into the final product. Along the way, the different types of steel will be explored and their particular applications considered.
Iron
Iron is an allotropic material, i.e. it undergoes two solid-state phase changes with temperature. At room temperature, pure iron has a body-centred cubic (BCC) structure, known as the α-phase. This structure is stable up to a temperature of 912°C, where it transforms to a face-centred cubic (FCC) structure, the γ-phase.
At 1390°C the FCC iron reverts back to BCC, and retains this structure until it melts at 1538°C. These changes are accompanied by changes in the volume of the iron (Figure 3.9.2).
Steel
Steel is an alloy of iron and carbon, in which the carbon content must not exceed 2%. Iron with a carbon content greater than 2% is classified as a cast iron and will not be considered here.
Carbon steels
Carbon steel is an alloy of only iron and carbon. In its BCC form, when small amounts of carbon are dissolved in the iron, the material is known as α-iron or ferrite.
The solubility of the carbon in this BCC structure is very low compared with that in the FCC structure, being a maximum of 0.02 wt % at 723°C and only 0.005 wt % at room temperature. This is despite the greater unoccupied volume in BCC (packing factor 68%) compared to FCC (74%).
The FCC form of the material has a considerably higher solubility of carbon, of up to 2.11%. The reason for this is that the largest interstitial holes in BCC iron (diameter 0.072 nm) are smaller than those in FCC iron (diameter 0.104 nm). This FCC form of the steel is known as austenite.
Both of these forms of steel are relatively soft and ductile; in particular, the austenite is readily shaped at elevated temperatures by hot forging and rolling operations.
When the limit of solubility for the carbon is exceeded for either of these forms of steel, the excess carbon precipitates out as Fe3C, which is a hard and brittle phase, given the name cementite. The various phases in the iron–cementite system are presented in the partial equilibrium phase diagram in Figure 3.9.3.
Hyper- and hypo-eutectoid steels
At a carbon concentration of 0.8%, the alloy shows a transformation at 723°C from the single-phase austenite to a two-phase structure consisting of ferrite and cementite:
austenite → ferrite + cementite
This solid transformation is defined as a eutectoid, as distinct from a eutectic, which is a transformation of a single liquid phase directly into two solid phases (see Chapter 1.4).
Steels with a carbon content of exactly the eutectoid composition are called eutectoid steels. Those with a carbon content of greater than 0.8% are hyper-eutectoid steels, and are used in the manufacture of burs and cutting instruments, while those with a carbon content of less than 0.8% are hypo-eutectoid steels, and are used in the manufacture of dental instruments such as forceps.
The eutectoid transformation is very important in the production of steels because a number of interesting things can happen when a carbon steel is cooled from its austenitic high-temperature condition to room temperature.
Slow cooling
On slow cooling, the changes in structure for a 0.8% carbon steel are as predicted from the equilibrium phase diagram. The austenite is converted into a mixture of ferrite and cementite, which is described as pearlite (Figure 3.9.4). However, cooling is not usually carried out slowly, but involves rapid cooling by immersing the object into cold water in a process that is known as quenching.
Rapid cooling
When austenite is quenched in water, the ferrite and cementite cannot form because there is not enough time for diffusion and rearrangement of the atoms. Instead, a very rapid transformation occurs to a body-centred tetragonal structure, which is rather like a distorted BCC. This form of steel is desc/>
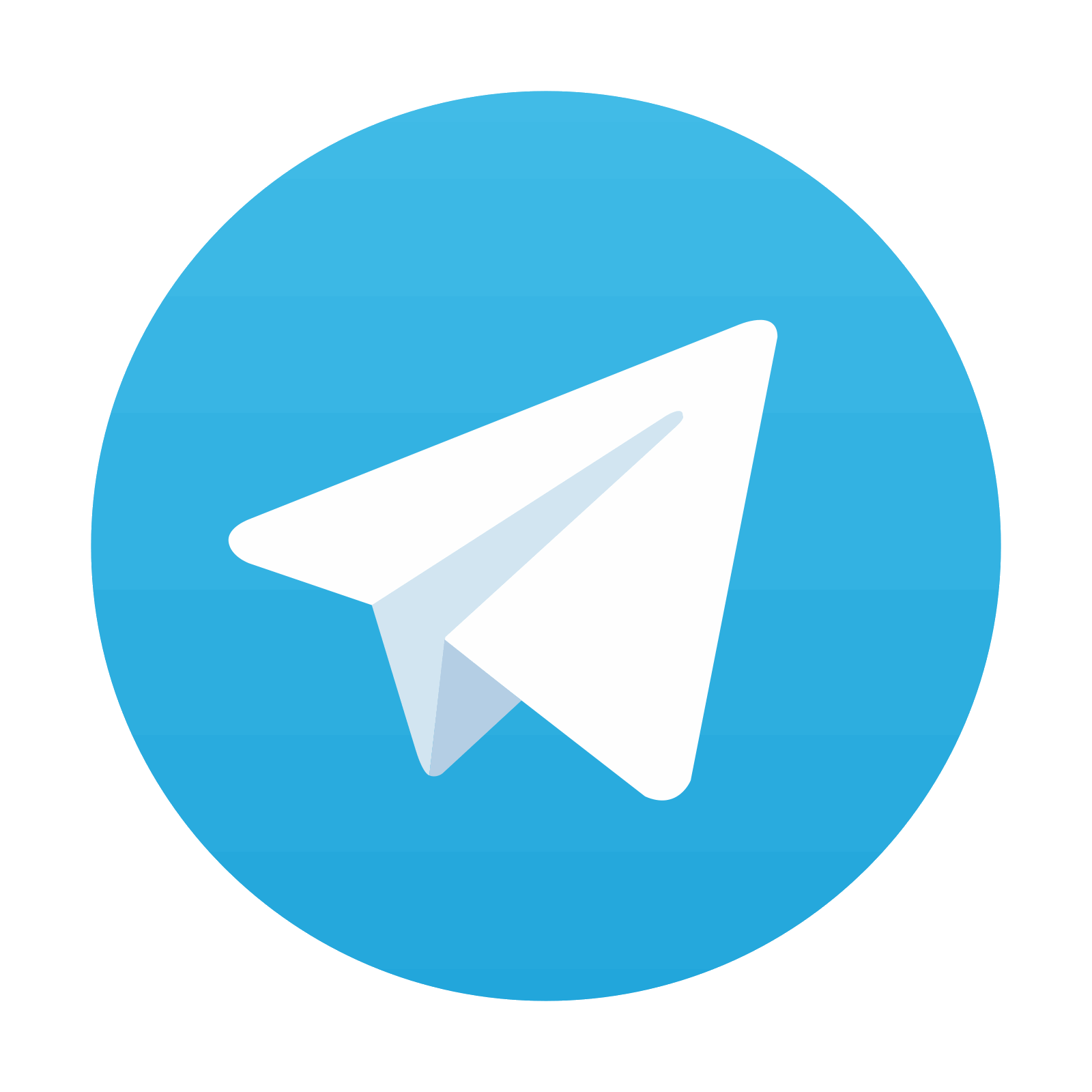
Stay updated, free dental videos. Join our Telegram channel

VIDEdental - Online dental courses
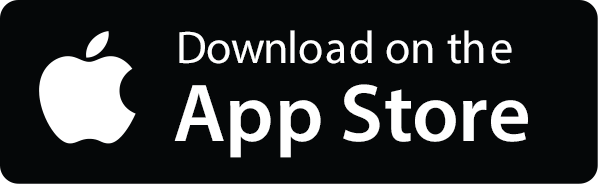
