All-ceramic restorations
Resin-bonded ceramics
Introduction
One way in which the traditional approach of cemented restorations has been challenged is with the development of new adhesive techniques. These have extended the use of ceramics to areas not previously thought possible. The concept of the resin-bonded ceramic restoration could not become reality until techniques for bonding the ceramic to enamel and dentine had been discovered. The idea of bonding ceramics to enamel using a combination of the acid-etch technique and resins began to be developed during the 1970s, which led, in the 1980s, to the ceramic veneers restoration. Then, still in the 1980s, major progress was made in the development of dentine-bonding agents, which opened up the possibility of resin-bonded crowns. The combination of adhesion to enamel, dentine and ceramic, and the improved strength characteristics of the ceramics, has produced restorations with excellent mechanical integrity. In fact, the adhesive bond has the effect of eliminating the internal surface flaws and thus reduces the potential for fracture. This has led to a growth in the use of resin-bonded ceramics for crowns, veneers and inlays.
Ceramic veneers
The concept of using ceramics as veneers is not new, and can be traced back to Dr Charles Pincus of Beverley Hills, who constructed porcelain veneers in the 1930s for actors in Hollywood, including Shirley Temple. The porcelain veneers were baked on platinum foil and retained on the teeth by denture powder. However, the veneers often broke because the thin porcelain was brittle and they were frequently removed from the teeth. When acrylic resin was introduced in 1937, Pincus switched to this material for the production of veneers for the acting profession. This eventually developed into the use of composite veneers, and ceramics were not used for a long time.
The advent of procedures for bonding resins to enamel using phosphoric acid etching of the enamel allowed the development of the resin-bonded ceramic veneer as a viable treatment option. This technique permitted bonding of resins to tooth enamel. In this situation, the fact that the thin ceramic material is bonded to the underlying tooth structure via a resin means that the tooth itself provides the support for the weak veneering material. An early reference to supporting a ceramic restoration by resin-bonding it to enamel was published by Rochette in 1975. This idea was then extended by Horn in 1983, who proposed the use of hydrofluoric acid as a glass etchant for veneers constructed from a leucite-containing feldspar, so as to enhance the bond between the ceramic and the resin. Thus, using the phosphoric acid-etch technique on enamel, he was able to bond the ceramic veneers permanently to the teeth with a resin-based composite. Bonding to ceramic has since been improved by the additional use of a silane coupling agent (see Chapter 3.8).
Ceramic veneers are considered superior to composites because of their improved aesthetics, colour stability, surface finish, abrasion resistance and tissue compatibility. They are also chemically very stable and have a coefficient of expansion similar to that of enamel. The finishing of porcelain veneers is more difficult than that of composites due to their high hardness. The thin feathered margins are more easily damaged than the margins of crowns, both in the laboratory and in the surgery. The ceramic veneers have the distinct advantage over crowns that improved aesthetics can be achieved with minimal tooth reduction, and the palatal surface of the tooth is unchanged so that incisal guidance is maintained. The material used for the construction of veneers is either a simple feldspathic glass or a leucite-containing feldspathic glass (see Chapters 3.4 and 3.5); these are the materials of choice for the construction of veneers due to their excellent aesthetics, especially from the point of view of colour and translucency, something which it is difficult for any other ceramic to match.
Although, in the time of Land and Pincus, the veneers were constructed on platinum foil, nowadays a variety of methods are available, which include:
Sintering process
In the sintering process, a slurry of the ceramic powder is applied to a refractory die (as opposed to a Pt-foil-coated die in the case of the porcelain jacket crown), dried and subsequently fired in a porcelain furnace. Multiple layers can be built up to develop characterization. Great skill is required by the dental laboratory technician to get the best aesthetics and appropriate contour. Examples of commercial leucite-reinforced ceramics using the sintering processing route are Fortress (Mirage Dental Systems, Kansas City, USA) and Optec-HSP (Jeneric/Pentron Inc, Wallingford, USA).
Hot-pressing
In order to surmount the problems of the inherent inaccuracies of fit of the sintered ceramics, which are due to the high firing shrinkage, attention has recently been paid to the possibility of using glass ceramics, which employ a casting process for the manufacture of crowns, veneers and inlays. Hot-pressing is one such approach and is a technique that involves the heating up an ingot of the ceramic. The ingot is a solid block of the material, which is made of a leucite-reinforced feldspar, as is the case with Empress I (Ivoclar-Vivadent, Schaan, Liechtenstein). This method utilizes parts of the lost wax casting technique. As in lost wax casting, a wax pattern is produced, which is then invested in a refractory die material. The wax is burnt out to create the space to be filled by the leucite-reinforced glass–ceramic. A specially designed pressing furnace is then used to fill the mould space from a pellet of the glass–ceramic using a viscous flow process at a temperature of 1180°C (Figure 3.7.1). When the ingot is heated to a sufficiently high temperature, it will become a softened mass such that under pressure it will flow into a refractory mould. This process is also often described as transfer moulding. It is distinctly different from the sintering technique since it does not rely on the fusion of powder particles.
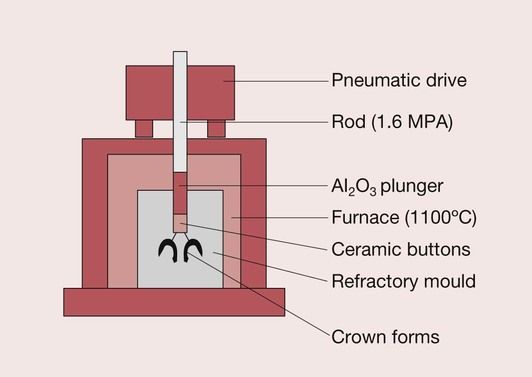
The final shading may be done by applying surface stains. For anterior restorations, the veneer is cut back and a powdered form of the leucite-reinforced glass–ceramic is bonded using the conventional sintering technique.
CAD–CAM
Since the feldspathic glasses and the leucite-containing feldspathic glasses can be prefabricated into blocks, the veneers can also be constructed using CAD–CAM technology. This can be done at the chair side with the CEREC system from Sirona using Vitablocks (Vita Zahnfabrik, Germany) or Procad (Ivoclar-Vivadent, Liechtenstein). The dental laboratory also has CAD–CAM technology for the construction of veneers, inlays and crowns.
Properties
The aesthetic results with the feldspathic glasses and the leucite-containing feldspathic glasses are excellent due to their high translucency, fluorescence and opalescence. When used in combination with resin bonding to enamel and dentine, these materials are very good for veneers and inlays and are also used for anterior crowns. However, the mechanical strength is insufficient for this class of ceramic to be used in the construction of posterior crowns and all-ceramic bridges.
Due to these limitations and a desire to produce ceramics suitable for use in the posterior part of the mouth, linked to a wish to extend their use to the construction of small three-unit bridges, there has been a major drive to develop new ceramics suitable for use as resin-bonded all-ceramic restorations. The focus of this development has been a class of materials known as glass–ceramics.
Glass–ceramics
The majority of materials available for resin-bonded ceramic restorations are, in essence, varieties of a special group of ceramics known as glass–ceramics. The various dental glass–ceramics that have been developed for resin-bonded ceramic restorations will be described, along with some of the new processing techniques that have evolved at the same time.
Glass–ceramics were first developed by Corning Glass Works in the late 1950s. In principle, an article is formed while liquid, and a metastable glass results on cooling. During a subsequent heat treatment, controlled crystallization occurs, with the nucleation and growth of internal crystals. This conversion process from a glass to a partially crystalline glass is called ceraming. Thus, a glass ceramic is a multiphase solid containing a residual glass phase with a finely dispersed crystalline phase. The controlled crystallization of the glass results in the formation of tiny crystals that are evenly distributed throughout the glass. The number of crystals, their growth rate and thus their size are regulated by the time and temperature of the ceraming heat treatment.
There are two important aspects to the formation of the crystalline phase: crystal nucleation and crystal growth. The schematic in Figure 3.7.2 shows that the rate of crystal nucleation and the rate of crystal growth are at a maximum at different temperatures. The ceraming process consequently involves a two-stage heat treatment. The first heat treatment is carried out at the temperature for maximum nucleation of crystals, so as to maximize the number of crystals formed. The material temperature is then raised, after a suitable period of time, to the higher temperature to allow crystal growth. It is held at the higher temperature until the optimum crystal size is formed.
To ensure a high strength for the glass–ceramic, it is important that the crystals are numerous and are uniformly distributed throughou/>
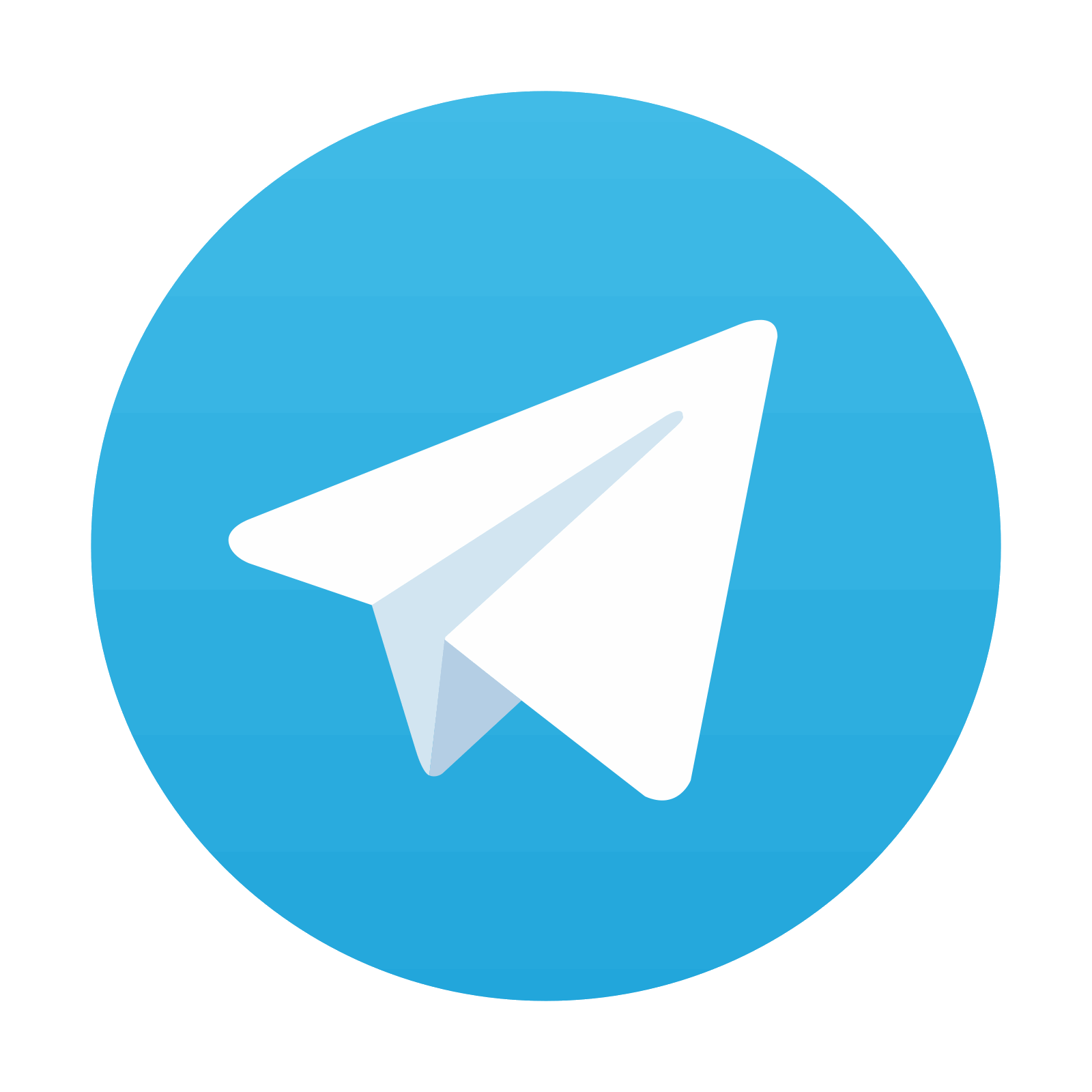
Stay updated, free dental videos. Join our Telegram channel

VIDEdental - Online dental courses
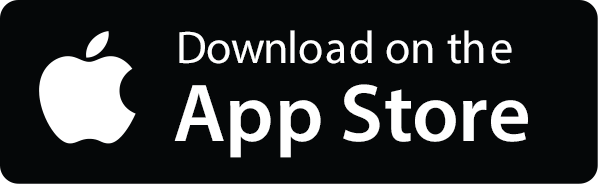
