Metal-bonded ceramics
Introduction
A major limitation of the aesthetic ceramics such as the feldspathic glasses was their lack of strength. For ceramic restorations, the presence of micro-cracks on the fitting surface is a major source of weakness, and their removal would significantly improve the strength of the crown. Glazing the internal fitting surface is one possibility but impractical. Another possibility is bonding the ceramic to a metal substrate, such that these microscopic cracks are effectively eliminated, with the consequence that the structure is considerably stronger. This is the basic premise behind the metal-bonded system (Figure 3.5.1). The significant breakthrough came with the publication of a patent by Weinstein, Katz and Weinstein in 1962, where they explained how it is possible to get a feldspathic glass to bond to an alloy surface by the inclusion of leucite crystals. The latter were added so as to ensure that the coefficient of thermal expansion of the ceramic closely matched that of the metal, as explained in more detail later.
The crown consists of a cast metal coping, on to which is fired a ceramic veneer. If a proper bond is created, then the internal cracks are eliminated, as the metal presents a barrier to the propagation of cracks by virtue of its high fracture toughness. One of the most likely modes of failure with this system is the separation of the ceramic from the metal due to an interfacial breakdown of the metal–ceramic bond. The success of the system depends on the quality of this bond.
An important contributory factor to the ability to bond the ceramic to the metal is the degree of mismatch between the coefficients of expansion of the ceramic and the metal. If the mismatch is too great, then stresses will build up during the cooling process after firing. These stresses can be sufficient to result in crazing or cracking of the ceramic. The issues of the bond and the coefficients of expansion both require careful consideration.
The bond
The nature of the bond between the metal coping and the ceramic has been extensively studied and it is agreed generally that there are three mechanisms involved:
Mechanical retention occurs as the ceramic flows into the microscopic spaces in the surface of the metal. The roughness of the surface is enhanced, often by applying an alumina-air abrasive or by grinding, so that the amount of interlocking is increased (Figure 3.5.2). This has the added benefit of producing a very clean surface that aids the wetting of the ceramic on to the metal.
Good bonding relies on an intimate contact between the ceramic and the metal coping, and any contaminants will jeopardize the quality of the bond. Before the ceramic is applied to the surface of the coping, the coping is subjected to a degassing cycle in the furnace, which burns off any remaining impurities and reduces the formation of bubbles due to trapped gases at the interface. The various stages in the surface preparation of the metal coping are described in more detail at a later stage. Most ceramics have a coefficient of thermal expansion that is considerably lower than that of metals (Table 3.5.1). On cooling, the metal will try to contract more than the ceramic due to its higher coefficient of expansion. This leaves the ceramic in a state of compression. Whilst this is potentially highly beneficial for this brittle material, it is important that the mismatch in the coefficients of thermal expansion is only small. If the mismatch is too big, internal stresses created during cooling could cause the ceramic to fracture, with the most likely place for failure being the interface between the metal and the ceramic.
Table 3.5.1
Typical values of the coefficient of thermal expansion (α) of metals and ceramics
Material | α (ppm/°C) |
Metals | |
Aluminium | 23.6 |
Gold | 13.8 |
Nickel | 13.3 |
Silver | 19.0 |
Ceramics | |
Alumina | 8.8 |
Spinel (MgAl2O4) | 7.6 |
Fused silica (SiO2) | 0.5 |
Soda–lime glass | 9.0 |
There is now considerable evidence that a strong chemical bond is created between the ceramic and the oxide coating on the metal. During firing, the ceramic is taken above its glass transition temperature such that it can flow and fuse with the oxides on the metal surface by migration of the metal oxides into the ceramic. In the case of gold alloy copings, small amounts of oxide-forming elements are added to the alloy because gold does not naturally form an oxide. As a consequence, the strength of the bond between the metal and the ceramic is increased manifold. This shows the importance of the presence of the surface oxides.
Preparation of the metal surface
In order to obtain a good bond between the metal coping and the ceramic veneer, it is important for the metal surface to be carefully prepared. This involves a number of technical stages that warrant closer examination. The main reasons for the surface preparation of the metal are to ensure the removal of any contaminants and to produce a surface oxide layer of the correct composition and character to which the ceramic will fuse. The various stages can be identified as:
Surface grinding
When the metal casting is removed from the investment, there is always residual investment bonded to the surface of the casting. The surface is also contaminated with unwanted oxides, small porosities and fine projections, especially if the investment is susceptible to fracture of the surface layer.
The grinding process is carried out to remove all of these imperfections, and the increased surface roughness is believed to aid the retention of the ceramic by micro-mechanical interlocking.
However, the grinding process can itself suffer from the problem of debris, such as oils, waxes, bits of skin tissue or gases becoming trapped in undercuts. Even though the ceramic may be very effective in wetting the surface of the metal, it cannot always penetrate deep fissures.
In general, methods of grinding that do not result in the formation of deep fissures, porosities or undercuts are preferred and, to this end, the use of fissure burs or carbide burs appears to be the recommended procedure.
Cleaning the casting in an organic solvent (e.g. carbon tetrachloride) in a sealed ultrasonic bath will remove surface contamination that has arisen during the handling of the casting.
Heating under partial vacuum
In the as-cast condition, the metal will not have the ideal oxide coating on its surface. Gold alloys will have virtually no oxide coating, given the noble nature of this metal. An oxide film can be formed by heating the casting at a temperature near to the firing temperature of the ceramic. This has the effect of allowing the metallic elements that are incorporated in the alloy (e.g. tin, indium, zinc or gallium) to migrate to the surface and form an oxide surface layer.
Great care must be taken to ensure that the correct heating cycle is used. Too brief a heat treatment could result in the formation of a thin or partial oxide coating, providing a poor substrate to which the ceramic can fuse. An excessively long heating cycle could result in the depletion of the oxidizing elements from the surface layer of the gold alloy.
No bond will form if all of the oxide formed is removed during the subsequent acid pickling process and none of the oxidizing elements are left sufficiently close to the surface to allow the formation of additional oxides.
Carrying out the heat treatment under reduced pressure aids the removal of gases that have been absorbed by the metal in great amounts during the casting process. The removal of these gases helps to prevent the formation of interfacial bubbles. For this reason, the heat treatment of the alloy prior to the ceramic firing cycle is often referred to as a degassing treatment.
In the case of base metal alloys, where nickel and chromium are commonly used, the metals oxidize very readily and the problem is generally the opposite of that for the gold alloys, in that too much of the oxide is formed.
Although oxides will naturally form during the firing of the ceramic, it has been found that it is better to preform the oxide coating, as this improves the wetting of the ceramic on the metal surface.
Acid pickling
The heat treatment of gold alloys will produce not only tin oxide but various other oxides on the surface as well.
The acid pickling procedure seeks to remove the unwanted oxides in preference to the tin oxide. There is the added advantage that the dark surface of the alloy is lightened from grey to white due to increased concentration of tin oxide on the alloy surface. Commonly used acids are 50% hydrofluoric acid or 30% hydrochloric acid, with the latter preferred because of the hazards associated with the use of hydrofluoric acid. Neither this nor the following procedure is generally required for base metal alloys.
Heating in air
A further heat treatment in air is frequently carried out in order to form an oxide coating of the correct thickness and quality.
The optimal oxide film on precious metal alloys should have a matt, greyish-white appearance, being composed mainly of base metal oxide. If the surface has a glossy appearance, this indicates a lack of oxide film and is usually the consequence of too many repeated surface treatments.
Importance of thermal expansion
The composition of the ceramic for metal–ceramic restorations needs to be different from that of the ceramic used for all-ceramic restorations.
The coefficient of thermal expansion (α) of the feldspathic glasses used in the construction of the porcelain jacket crowns is 7–8 ppm/°C. This is far too low to be compatible with the alloys, which are typically in the region of 14–16 ppm/°C. This mismatch would give rise to serious problems due to excessive differential shrinkage on cooling. Depending on their composition, the coefficient of thermal expansion of the alloys and the ceramics can differ quite considerably.
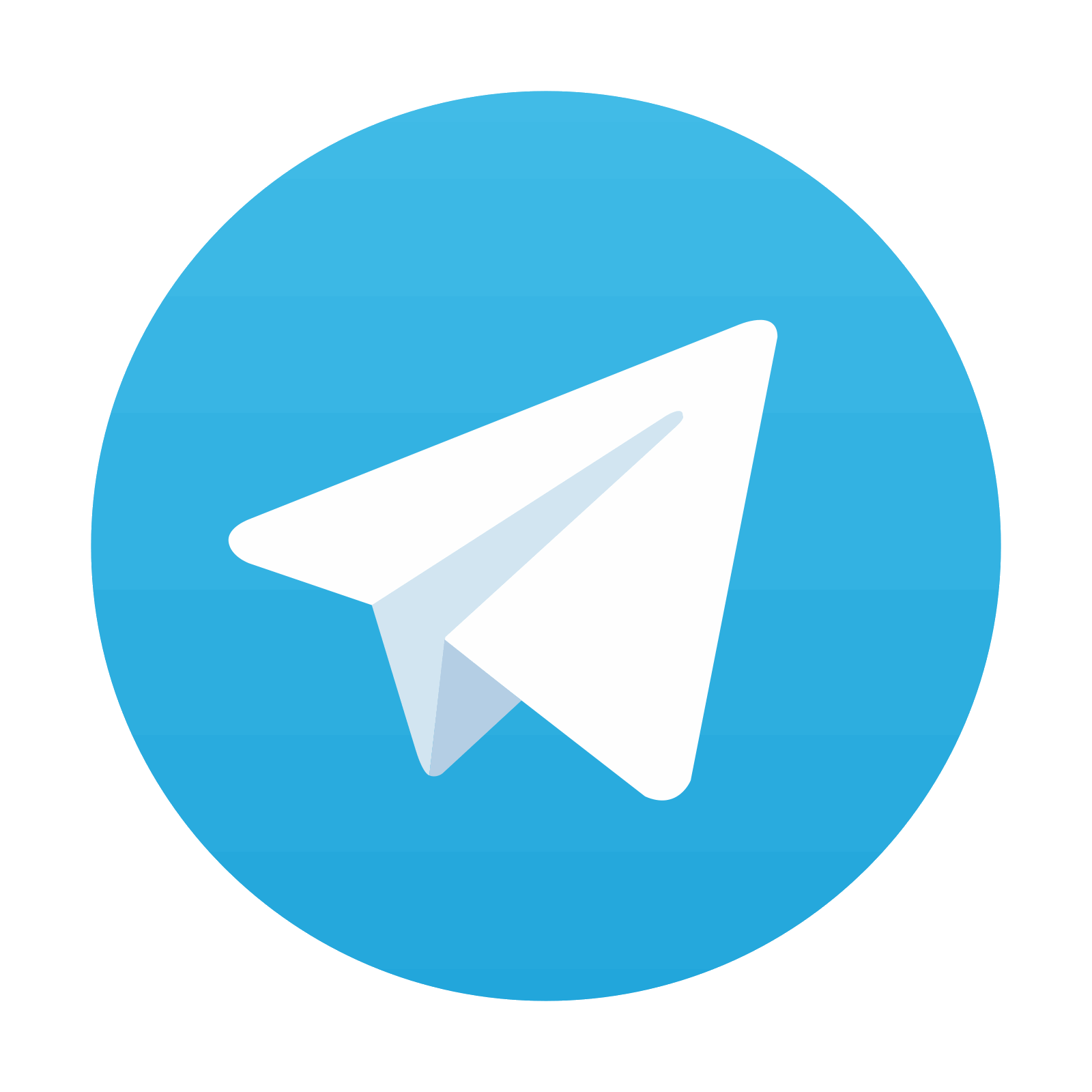
Stay updated, free dental videos. Join our Telegram channel

VIDEdental - Online dental courses
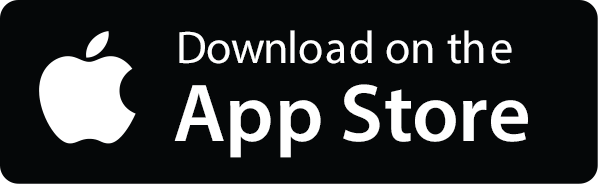
