22 INVESTING AND CASTING
The lost-wax casting technique has been used since ancient times to convert wax patterns to cast metal. It was first described1,2 at the end of the 19th century as a means of making dental castings.
PREREQUISITES
When the wax pattern has been completed and its margin has been reflowed (see p. 578), it is carefully evaluated for smoothness, finish, and contour (see Chapter 18). The pattern is inspected under magnification, and any residual flash (wax that extends beyond the preparation margin) is removed. A sprue is attached to the pattern, then removed from the die, and attached to a crucible former (Fig. 22-1). The wax pattern must be invested immediately because any delay leads to distortion of the pattern as a result of stress relief of the wax.3
Sprue
Sprue design (Fig. 22-2) varies depending on the type of restoration being cast, the alloy used, and the casting machine. There are three basic requirements, as follows:
If a metal sprue is used, it should be made of noncorroding metal to avoid possible contamination of the casting. Metal sprues are often hollow to increase contact surface area and strengthen the attachment between the sprue and pattern. They are usually separated from the investment at the same time the crucible former is. Special care must then be taken to examine the orifice for small particles of investment that may break off when such a sprue is removed, because these can cause an incomplete casting if undetected (see p. 701).
Diameter
In general, a relatively large-diameter sprue is recommended because this improves the flow of molten metal into the mold and ensures a reservoir during solidification.4,5
Location
The sprue should be attached to the bulkiest noncritical part of the pattern, away from margins and occlusal contacts. Normally, the largest nonfunctional cusp is used (Fig. 22-3). The point of attachment should allow a stream of metal to be directed to all parts of the mold without having to flow in an opposite direction to the casting force (Fig. 22-4).
The sprue must also allow for proper positioning of the pattern in the ring. This can be crucial because expansion within the mold is not uniform.6,7 For example, spruing on the cusp tip can give good results, but spruing on the proximal contact may produce a casting that is too wide mesiodistally and too short occlusocervically.
Attachment
The sprue’s point of attachment to the pattern should be carefully smoothed to minimize turbulence. For the centrifugal casting technique, the attachment area should not be restricted because necking increases casting porosity and reduces mold filling.8 Similarly, excessively widening the attachment can cause this part of the cooling melt to solidify last, causing a void on the internal aspect of the casting, known as shrink-spot porosity.
Crucible Former
The sprue is attached to a crucible former* (Fig. 22-6), usually made of rubber, which serves as a base for the casting ring during investing. The exact shape of the crucible former depends on the type of ring and casting machine used. With most modern machines, the crucible former is tall, to allow use of a short sprue and also to enable the pattern to be positioned near the end of the casting ring.
Casting Ring and Liner
The casting ring serves as a container for the investment while it sets and restricts the setting expansion of the mold. Normally a liner is placed inside the ring to allow for more expansion, because the liner is somewhat compressible. Use of two liners allows for additional compression and enables increased setting expansion of the investment material. At one time, asbestos was used as the liner, but this has been replaced by other materials to avoid the health risks associated with asbestos fibers. Like many other factors that come into play in achieving consistent casting with the proper quality of fit, changes in the liner are important. Wetting the liner increases the hygroscopic expansion of the mold and should be carefully controlled. An absorbent dry liner removes water from the investment and makes a thicker mix, which leads to increase in the total expansion.11,12 To prevent expansion restriction, care must be taken not to squeeze the liner against the ring. Increased expansion can be obtained by placing the mold in a water bath. This is because of hygroscopic expansion (Fig. 22-7). The position of the pattern in the casting ring also affects expansion. For consistent results, a single crown should be centered in the ring, equidistant from its walls. When fixed prostheses are cast as one piece, greater accuracy is achieved if the pattern is placed near the center of a large or special oval ring, rather than if a portion of a multiunit wax pattern is only partially centered and partially near the edge of a smaller ring.6
Ringless Investment Technique
With the use of higher strength, phosphate-bonded investments, the ringless technique has become quite popular (Fig. 22-8).13 The method entails the use of a paper or plastic casting ring and is designed to allow unrestricted expansion.14 This can be useful with higher melting alloys that shrink more because of a larger cooling trajectory.
Spruing Technique
Step-by-step procedure for a single casting
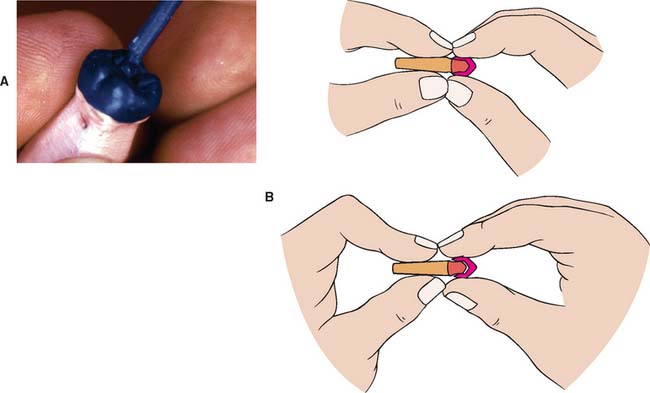
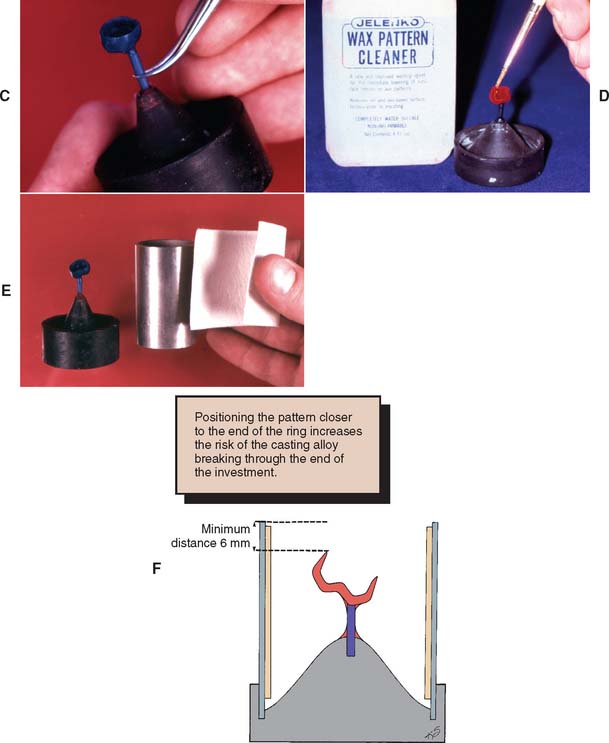
Fig. 22-10 Spruing technique for a single casting. A, Attaching the sprue to the pattern. B, Removing the pattern from the die (see p. 566 for a description of this technique). C, Positioning the pattern on the crucible former. D, Application of surfactant. E, A ring liner increases the setting expansion. F, The pattern must be positioned sufficiently away from the end of the ring.
MATERIALS SCIENCE
Gypsum-Bonded Investments
Expansion
Hygroscopic expansion
Hygroscopic expansion occurs when water is added to the setting gypsum investment immediately after the ring has been filled. Usually this is accomplished by submerging the ring in a water bath at 37°C (100°F) for up to 1 hour immediately after investing. A significant amount of additional setting expansion results, enabling the use of a slightly lower wax elimination temperature. A wet ring liner also contributes hygroscopic expansion to the portion of the mold with which it is in contact (see Fig. 22-7).
Thermal expansion
As the mold is heated to eliminate the wax, thermal expansion occurs (Fig. 22-12). The silica refractory material is principally responsible for this because of solid-state phase transformations. Cristobalite changes from the α to the β (high-temperature) form between 200°C (392°F) and 270°C (518°F); quartz transforms at 575°C (1067°F). These transitions involve a change in crystal form, an accompanying change in bond angles and axis dimension, and a decreased density, producing a volume increase in the refractory components.
Phosphate-Bonded Investments
The principal difference between gypsum-bonded and phosphate-bonded investments is the composition of the binder and the relatively high concentration of silica refractory material in the latter. The binder consists of magnesium oxide and an ammonium phosphate compound. In contrast to gypsum-bonded products, this material is stable at burnout temperatures above 650°C (1200°F) (Fig. 22-13), which allows for additional thermal expansion. Most phosphate-bonded investments are mixed with a specially prepared suspension of colloidal silica in water. (Some, however, can be mixed with water alone.)
Working time
Phosphate-bonded investments have a relatively short working time in comparison with gypsum materials. Their exothermic setting reaction accelerates as the temperature of the mix rises during manipulation. The filled ring feels warm to the touch even shortly after it has been filled. A longer mixing time significantly accelerates the setting reaction and temperature and thus reduces the working time even further. The addition of water to the colloidal silica suspension increases the working time, with some loss of setting expansion. Many technicians therefore vary the quantity of special liquid and water between batches and make trial mixes for each new shipment. This has been a reliable means of adjusting expansion.15
Gas is formed during the reaction and must be removed for a sufficiently long period to minimize nodules on the casting.16 Maintaining a vacuum for about 60 seconds appears to be adequate.
SELECTION OF MATERIALS
Selecting a Casting Alloy
The number and variety of alloys suitable for casting have expanded dramatically, largely because of changes in the price of gold. Many alloys are available, especially for metal-ceramic restorations (see Chapter 19). The dentist must be able to make a rational choice on the basis of current information.
Factors to be considered
Intended use
Alloys for casting were traditionally classified on the basis of their intended use, as follows:
Physical properties
Porcelain-type alloys with a high noble metal content were found to have hardness similar to that of type III alloys, and base metal alloys were found to be harder than type IV alloys (see Chapter 19).
Composition
To be accepted by the ADA as an alloy suitable for dental restorations,17 the manufacturer must list the percentage composition by weight of the three main ingredients and any noble metal percentage. The functional characteristics of corrosion resistance and tarnish resistance were traditionally predicted on the basis of gold content. In general, if at least half the atoms in the alloy are gold (which would be 75% by weight), good resistance to corrosion and tarnish can be predicted. Nevertheless, clinical evaluations have failed to show statistically significant differences in the tarnish resistance of high-gold (77%) and low-gold (59.5% to 27.6%) alloys.18 However, a poorly formulated alloy, even of high gold content, can rapidly tarnish intraorally.
Cost
When the intrinsic metal cost of a restoration is calculated, the volume of the casting, rather than its weight, should be determined. Dental casting alloys can vary considerably in density from below 8 g/mL to over 18 g/mL (see Table 19-1). An “average” restoration has a volume of 0.08 mL; an all-metal pontic may have a volume reaching 0.25 mL.19 Therefore, it is conceivable that the cost of a large pontic cast in a low-density alloy would be equal to or less than the cost of a complete cast crown fabricated from a high-density alloy. When noble metal prices are high, more sophisticated techniques of scrap recovery become economically attractive. These can range from installing conventional metal catchers in all areas where castings are finished to equipping all work stations with filtered suction machines.
Clinical performance
A risk in choosing a new alloy is that defective clinical performance may fail to appear in laboratory testing or in short-term animal and clinical trials. For example, manufacturers introduced copper-based casting alloys with very poor corrosion resistance20 when the price of gold was rapidly rising.* Although the clinically established alloys all have disadvantages, their performance is likely to have been well documented, and the prognosis of restorative treatment can be more accurately predicted.
Laboratory performance
Sound laboratory data are essential in the selection of a casting alloy. Important areas of consideration are casting accuracy, surface roughness, strength, sag resistance, and metal-ceramic bond strength. Currently available data suggest that nickel-chromium alloys have lower casting accuracy21 and greater surface roughness22 than do gold alloys (Fig. 22-14) but higher strength and sag resistance because of their higher melting ranges.23
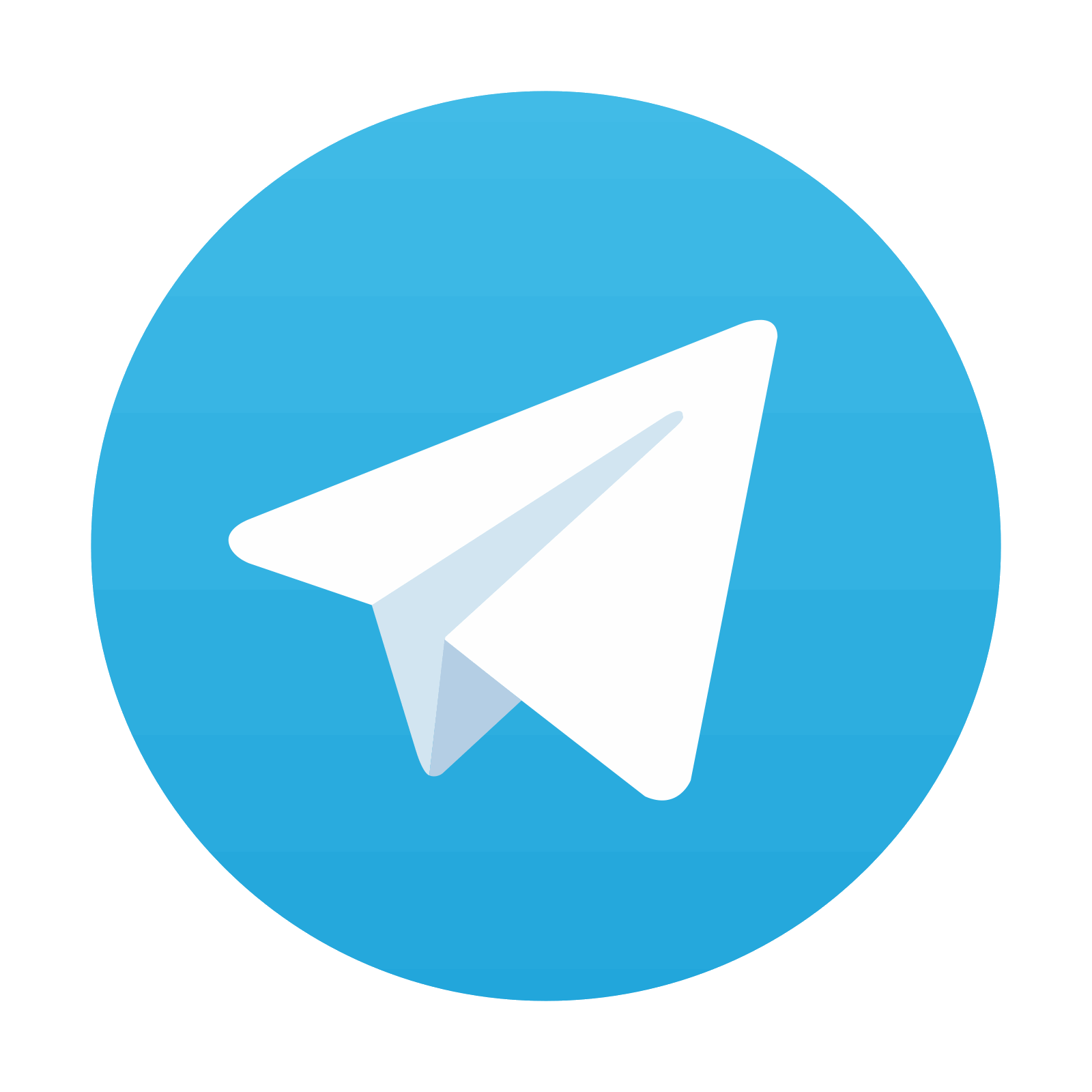
Stay updated, free dental videos. Join our Telegram channel

VIDEdental - Online dental courses
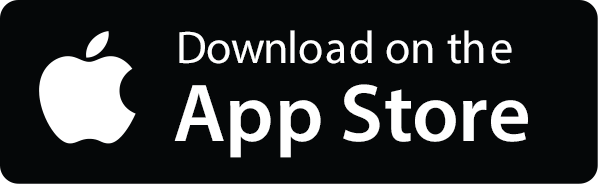
