Chapter 2
Properties used to Characterise Materials
2.1 Introduction
Many factors must be taken into account when considering which properties are relevant to the successful performance of a material used in dentistry. The situation in which the material is to be used and the recommended technique for its manipulation define the properties which characterise the material. Laboratory tests used to evaluate materials often duplicate conditions which exist in situ. This is not always possible and sometimes not desirable since one aim of in vitro testing is to predict in a rapid laboratory test what may happen in the mouth over a number of months or years. Many tests used to evaluate dental materials involve the measurement of simple properties such as compressive strength or hardness which have been shown to correlate with clinical performance.
Many materials used in dentistry are supplied as two or more components which are mixed together and undergo a chemical reaction, during which the mechanical and physical properties may change dramatically. For example, many impression materials are supplied as fluid pastes which begin to set when mixed together. The set material may be a rigid solid or a flexible rubber depending upon the chemical nature of the product.
The acceptance of such a product by the dentist depends upon the properties of the unmixed paste, the properties during mixing and setting and the properties of the set material (Table 2.1). This classification of properties applies to virtually all groups of materials.
Properties of unmixed materials: Manufacturers formulate materials which give optimal performance as evaluated by their quality assurance programme and clinical trials. It is known however, that certain products deteriorate during storage and as a result may perform poorly. Such materials are said to have limited shelf life. Some materials have an extended shelf life if refrigerated during storage. One technique commonly employed to predict stability is to carry out accelerated ageing by storing samples at elevated temperature, commonly 60°C, followed by evaluation of material properties.
Containers used for materials generally have a batch number stamped or printed onto them from which the date of manufacture can be obtained. Thus, for materials with limited shelf life it is possible to ascertain the date at which one would expect the properties to deteriorate.
Properties of materials during mixing, manipulation and setting: Properties of materials during mixing, manipulation and setting are considered together since they mainly involve a consideration of rheological properties and the way in which these change as a function of time during setting.
For materials of two or more components which set by a chemical reaction, thorough mixing is essential in order to achieve homogeneous distribution of properties throughout the material. The ease of mixing depends on factors such as the chemical affinity of the components, the viscosity, both of the components and the mixed material, the ambient temperature, the method of dispensation and the method of mixing.
Several methods of dispensation exist among materials used in dentistry. Some involve the mixing of powder and liquid components, others the mixing of two pastes, while others involve paste and liquid components. When the mixing of two pastes is required, the manufacturer often gives a good colour contrast between the two pastes. The achievement of a thorough mix of the two components can be judged by the attainment of a homogeneous colour with no streaks. When powder and liquid or paste and liquid are mixed, the achievement of a thorough mix is less certain. The components are mixed for a recommended time and/or until a recommended consistency is reached.
Table 2.1 Illustrating the different requirements and associated tests used for materials at different stages during their storage and use.
Stage of use | Practical issues | Tests required |
During storage Before use in surgery or laboratory. | Require material to keep fresh and last a long time. Wastage is minimised and bulk purchases can be made. | Shelf life, expiry date or date of manufacture given by manufacturer. Test that certain key properties are within acceptable limits after a period of storage. |
During proportioning, mixing and manipulating. | Easy and accurate to proportion, mix and use. Should not ‘drip’ off instruments. Should not stick to instruments. | Test reproducibility of proportioning. Test effect of proportions on properties. Test speed and completeness of mix. Test rheological properties and ‘tackiness’. |
During setting. | Material should have a convenient rate of set. Dimensional and temperature changes on setting should not cause problems with accuracy or irritation. | Measure working time and setting time using meaningful tests. Measure dimensional change during setting. Measure heat absorbed or evolved using thermometry. |
Set material | Material should have an acceptable appearance and sufficient durability to serve its function. Should be safe and harmless. | Measure mechanical properties such as strength, hardness, abrasion resistance. Evaluate resistance to fluids such as saliva and dietary liquids. Evaluate colour, translucency and gloss. |
A growing number of materials are mixed mechanically. This method removes uncertainty and gives a more reproducible result.
The use of encapsulated materials which are mixed mechanically is becoming very popular. These offer the dual advantages of easier and more reproducible mixing coupled with pre-set proportions of components within the capsules.
Certain products have specified manipulative requirements which will be referred to later. For many applications, materials should be in a relatively fluid state at the time they are introduced into the patient’s mouth but should undergo rapid setting involving a change to a more rigid or rubbery form. From the commencement of mixing, two important times can be defined which have an important bearing on the acceptability of materials. The first is the working time, defined as the time available for mixing and manipulating a material. For example, an impression material should be seated in the mouth before the end of the working time otherwise setting will have proceeded sufficiently for the viscosity to have increased considerably. The other time which characterises setting is the setting time. This, like working time, is to some extent arbitrary since it is defined as the time taken for a material to have reached a certain level of rigidity or elasticity. It is known that many materials continue setting for a considerable time after the apparent setting and optimum properties may not be achieved until several hours later.
Properties of the set material: The properties of the unmixed material and those during mixing and setting are important and may influence the practitioner’s selection. Generally, it is the properties of the set material which indicate the suitability of a product for any application. For example, in the case of a filling material, the method of dispensation, viscosity of the mixed material, working time and setting time control the ease of handling of the product, but the durability of the material in the oral environment depends on factors such as strength, solubility, abrasion resistance, etc. The properties of the set material can be conveniently divided into the following categories: mechanical properties, thermal properties, chemical properties, biological properties and miscellaneous other physical properties. Naturally, the properties relevant to any one material will depend on the application.
2.2 Mechanical properties
Most applications of materials in dentistry have a minimum mechanical property requirement. For example, certain materials should be sufficiently strong and tough to withstand biting forces without fracture. Others should be rigid enough to maintain their shape under load. Such properties of materials are generally characterised by the stress–strain relationship which is readily obtained by using a testing machine of the type shown in Fig. 2.1.
Before considering the various types of experiment which can be carried out and the relevance of the data obtained, it is necessary to define the terms stress and strain.
Stress: When an external force is applied to a body or specimen of material under test, an internal force, equal in magnitude but opposite in direction, is set up in the body. For simple compression or tension the stress is given by the expression, Stress = F/A, where F is the applied force and A the cross-sectional area (Fig. 2.2). A stress resisting a compressive force is referred to as a compressive stress and that resisting a tensile force a tensile stress.
Tensile and compressive stresses, along with shear, are the three simple examples of stress which form the basis of all other more complex stress patterns. The unit of stress is the pascal (Pa). This is the stress resulting from a force of 1 Newton (N) acting upon one square metre of surface. Whereas the tensile stress can be visualized as a purely uni-axial stress set up within a material, the compressive stress is more complex and comprises force vectors which act to introduce elements of shear within the specimen under compression.
Fig. 2.1 (a) Mechanical properties testing equipment. This shows the equipment used in determining mechanical properties of materials. The test being performed is a tensile test on a sample of impression material. Note the shape of the sample which is shown in the inset (b). This shape is referred to as a dumb bell shaped specimen and it is designed so that the specimen can be gripped at each end and stretched. The shape of the specimen will ensure that fracture occurs in the middle region and not at the ends of the specimen where the specimen is gripped. The results are given on the computer screen in the form of a plot of force against displacement, which can easily be converted into stress against strain.
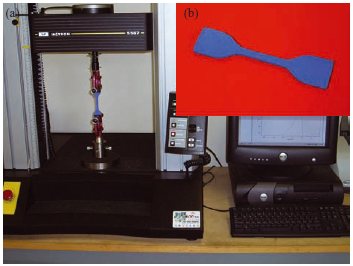
One test method commonly used for dental materials is the three-point bending test or transverse test (Fig. 2.3).
When an external force is applied to the mid-point of the test beam the stresses can be resolved as shown. The numerical value of stress is given by the expression
where L is the distance between the supports, b is the width of the specimen and d its depth.
When a cylinder of a brittle material is compressed across a diameter as shown in Fig. 2.4a, a tensile stress is set up in the specimen, the value of the stress being given by
where F is the applied force, D the diameter of the cylinder and T the length of the cylinder. This type of test is referred to as a diametral compressive tensile test and is commonly used when conventional tensile testing is difficult to carry out due to the brittle nature of the test material. For non-brittle materials the equation used to calculate stress breaks down due to the increased area of contact between the testing machine platen and the material under test (Fig. 2.4b).
Fracture stress – strength: There is a limit to the value of applied force which a body, or specimen of material, can withstand. The maximum stress is normally used to characterise the strength of a material. In a tensile test, the fracture stress is referred to as the tensile strength of a material whilst a compression test gives a value of compressive strength. The diametral compressive tensile test gives a value for tensile strength.
Fig. 2.2 Diagram indicating how the magnitudes of (a) compressive and (b) tensile stresses and strains are calculated.
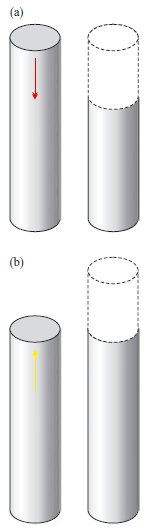
Fig. 2.3 Diagrammatic representation of a 3-point bending test or transverse test (a). Bending of the beam introduces both tensile and compressive stresses (b).
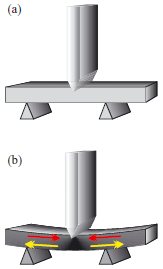
Fig. 2.4 Diametral compressive test for (a) a brittle material and (b) a ductile material.
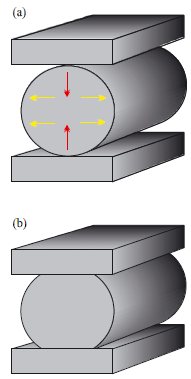
In the case of a bending test, fracture is normally initiated from the side of the specimen which is in tension. The bending stress at fracture, often called the flexural stress, is closely related to the tensile strength.
For brittle materials, the flexural strength can be significantly influenced by the presence of surface defects, voids or other imperfections which may cause stress concentrations at the surface in tension. These stress concentrations may cause a material to fracture at a force lower than that which would otherwise be expected, a fact which has obvious implications for engineering design as well as dentistry.
Strain: The application of an external force to a body or test specimen results in a change in dimension of that body. For example, when a tensile force is applied the body undergoes an extension, the magnitude of which depends on the applied force and the properties of the material. The numerical value of strain is given by the expression
Thus strain, which has no physical dimensions, can be seen as a measure of the fractional change in length caused by an applied force (Fig. 2.2). When strain becomes large, the dimensions of test specimens may change in a direction at 90° to that of the applied force. For example, a cylinder of material may undergo barrelling in addition to uni-axial compression, whilst a specimen subjected to tensile stress may become thinner in cross-section as the extension occurs. In order to monitor the way in which the stress changes with these alterations in specimen shape we need to take account of the poissons ratio of the material. This gives an indication of the ratio of strain occurring at 90° to the direction of the applied force to that occurring in the direction of the force.
The strain may be recoverable, that is the material will return to its original length after removal of the applied force, or the material may remain deformed, in which case the strain is non-recoverable. A third possibility is that the strain may be partially recoverable or that the recovery is time-dependent. The extent of recovery and/or rate of recovery is a function of the elastic properties of materials.
Stress-strain relationship: Stress and strain, as defined in the previous sections, are not independent and unrelated properties, but are closely related and may be seen as an example of cause and effect. The application of an external force, producing a stress within a material, results in a change in dimension or strain within the body.
The relationship between stress and strain is often used to characterise the mechanical properties of materials. Such data are generally obtained using a mechanical testing machine (Fig. 2.1) which enables strain to be measured as a function of stress and recorded automatically. Modern machines are capable of either increasing strain at a given rate and measuring the stress or increasing stress at a given rate and measuring the strain.Other applications, including fatigue testing, will be covered later.
For the simplest type of tensile or compression test, the graph displayed on the pen recorder would be as shown in Fig. 2.5.
It can be seen that in this example there is a linear relationship between stress and strain up to the point P. Further increases in stress cause proportionally greater increases in strain until the material fractures at point T. The stress corresponding to point T is the fracture stress. In a tensile test this gives a value of tensile strength, whilst in a compression test a value of compressive strength is obtained. The value of stress which corresponds to the limit of proportionality, P, is referred to as the proportional limit.
Point E is the yield stress. This corresponds to the stress beyond which strains are not fully recovered. Hence, it is the maximum stress which a material can withstand without undergoing some permanent deformation. The yield stress is difficult to characterise experimentally since it requires a series of experiments in which the stress is gradually increased then released and observations on elastic recovery made.
As a consequence of these experimental difficulties the proportional limit is often used to give an approximation to the value of the yield stress. Hence, when a material is reported as having a high value of proportional limit it indicates that a sample of the material is more likely to withstand applied stress without permanent deformation.
A practical example of a situation in which a high proportional limit is required is in connectors of partial dentures. Such connectors should not undergo permanent deformation if they are to retain their shape. A material such as cobalt–chromium (Co/Cr) alloy which has a high value of proportional limit is popular for this application since it can withstand high stresses without being permanently distorted. Another way of gauging the level of stress required to produce permanent deformation is to measure the proof stress. This indicates the value of stress which will result in a certain degree of permanent deformation upon removal of the stress. For example, the 0.1% proof stress (commonly used for alloys) is the level of stress which would result in a 0.1% permanent deformation.
Fig. 2.5 Typical stress-strain graph obtained from a simple compressive or tensile test.

The slope of the straight-line portion of the stress–strain graph gives a measure of the modulus of elasticity defined as:
This has units of stress. The choice of nomenclature for this property is somewhat unfortunate since it, in fact, gives an indication of the rigidity of a material and not its elasticity. A steep slope, giving a high modulus value, indicates a rigid material, whilst a shallow slope, giving a low modulus value, indicates flexible material. Whereas it may be advantageous for an impression material to be flexible it is essential for a restorative material to be rigid.
The value of strain recorded between points E and T indicates the degree of permanent deformation which can be imparted to a material up to the point of fracture. For a tensile test this gives an indication of ductility whilst for a compressive test it indicates malleability. Hence, a ductile material can be bent or stretched by a considerable amount without fracture whereas a malleable material can be hammered into a thin sheet. A property often used to give an indication of ductility is the elongation at fracture. Alloys used to form wires must show a high degree of ductility since they are extended considerably during the production process. In addition, clasps of dentures constructed from ductile alloys can be altered by bending.
The malleability of stainless steel is utilized when forming a denture base by the swaging technique. This involves the adaptation of a sheet of stainless steel over a preformed cast.
The area beneath the stress-strain curve yields some important information about test materials (Fig. 2.6). The area beneath the curve up to the elastic limit, Fig. 2.6a, gives a value of resilience, the units being those of energy. Resilience may be defined as the energy absorbed by a material in undergoing elastic deformation up to the elastic limit. A high value of resilience is one parameter often used to characterise elastomers. Such materials which may, for example, be used to apply a cushioned lining to a hard denture base are able to absorb considerable amounts of energy without being permanently distorted. The energy is stored and released when the material springs back to its original shape after removal of the applied stress.
Fig. 2.6 The area under a stress-strain graph may be used to calculate either (a) resilience or (b) toughness.
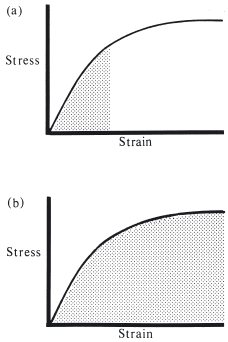
The total area under the stress-strain graph, Fig. 2.6b, gives an indication of toughness. This again has units of energy and may be defined as the total amount of energy which a material can absorb up to the point of fracture. A material capable of absorbing large quantities of energy is termed a tough material. The opposite of toughness is brittleness. This is, naturally, an important property for many dental materials. Its measurement, for example in a transverse test, depends on factors such as the speed with which the stress is increased and the presence of small imperfections in the specimen surface from which cracks can propagate.
Fracture toughness and impact strength: For brittle materials fracture may occur suddenly at a stress which is apparently well below the ideal fracture stress. This observation led to the development of theories on fracture toughness which takes account of the fact that small cracks can concentrate the stress at their tips. Griffith developed the theory of fracture toughness which led to the use of equations used for the calculation of stress intensification factor K. When K becomes great enough for crack propagation to occur it is termed the critical stress intensification factor Kc. This is calculated using the applied force, the specimen dimensions and the size and shape of the notch causing stress intensification. K has the units MNm-1.5. In order to calculate K or Kc specimens of the type shown in Fig. 2.7 are most commonly used. The notch is moulded or machined into the specimen and has very well defined dimensions of notch depth and notch tip radius. This type of specimen is known as a single-edge-notched specimen (SEN). It is likely that fracture toughness is more meaningful than strength for brittle materials as the critical effect of surface defects is accounted for by the presence of a notch. The equations used to calculate fracture toughness should strictly only be applied to materials which fail by a purely brittle mechanism. When plastic deformations occur before fracture misleading results can be obtained. The speed at which testing is carried out may affect the extent to which plastic deformation may occur. It is more likely to occur when the strain is increased slowly than when the strain is increased rapidly.
Fig. 2.7 Notched specimens are often used in tests of toughness in order to overcome the effects of surface imperfections in specimens.
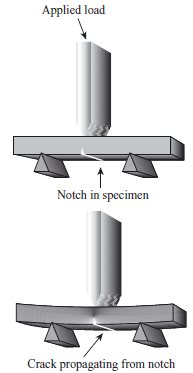
Hence materials are more likely to behave in a more brittle fashion when stress or strain are increased rapidly. When the stress is increased very rapidly it may be termed an impact test and the important practical property obtained is the impact strength which is normally quoted in units of energy. For this type of test the machine shown in Fig. 2.1 is often not capable of increasing stress rapidly enough and a swinging pendulum impact testing device is commonly used (Fig. 2.8). This type of instrument is known as a Charpy Impact tester. The position reached by the pendulum after fracturing the specimen gives a measure of the energy absorbed by the specimen during fracture. The absorbed energy can be resolved into several components which include friction and air resistance in the equipment. These minor components can be calculated by doing a dummy run with no specimens. The major components of energy are used in initiating and propagating cracks in the material. The relative magnitudes of these two components can be investigated by testing specimens with and without preformed cracks or notches. When the presence of a small notch or crack in the surface of a material has a marked effect on impact strength the material is said to be notch sensitive. Specimens of the type shown in Fig. 2.7 are often used in impact testing. Impact strength is not a fundamental material property (as is modulus of elasticity, for example) and it is not possible to fully account for differences in specimen size and shape. Values of impact strength measured in this way may only be considered of limited use in making direct comparisons with other materials of the same specimen size tested on the same instrument. For this reason the method is of limited scientific use, but is widely used in industry for quality control and development. Impact strength is an important property for acrylic denture base materials which have a tendency to fracture if accidentally dropped onto a hard surface.
Fig. 2.8 Test equipment for the Charpy impact test. This shows the equipment used to determine impact strength. The essential part of this equipment consists of a pendulum which swings from the position shown, down and then up again to the equivalent position on the other side. If a specimen is located at the bottom of the swing, as the pendulum swings through, it fractures the specimen and as energy will be absorbed in this process the pendulum swings up to a lower position on the other side. Hence, the energy absorbed in fracturing the specimen is shown on the gauge. Since this equipment gives a direct measure of energy absorbed during fracture this is strictly speaking a measurement of toughness rather than strength.
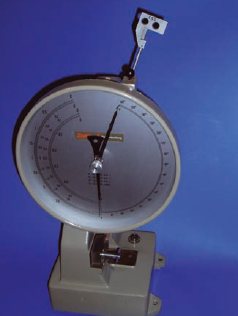
Figure 2.9 gives examples of various types of stress-strain graphs which may be encountered, along with an explanation of the way in which the graphs can be used to characterise materials.
Fig. 2.9 Six different types of stress-strain graphs. These may be used to characterise materials as follows: (a) rigid, strong, tough, ductile; (b) flexible, tough; (c) rigid, strong, brittle; (d) rigid, weak, brittle; (e) flexible, weak, brittle; (f) flexible, resilient.
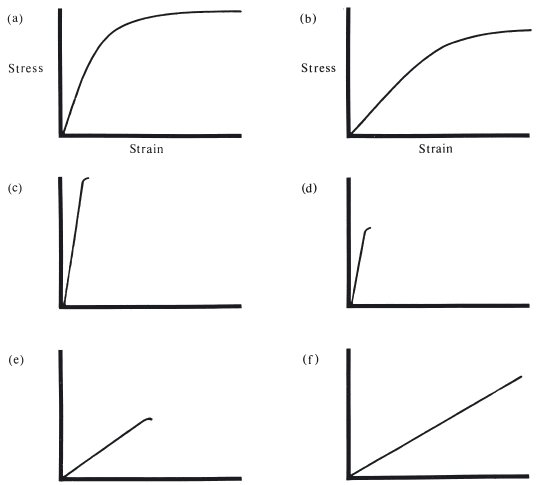
Fatigue properties: Many materials which are used as restoratives or dental prostheses are subjected to intermittent stresses over a long period of time – possibly many years. Although the stresses encountered may be far too small to cause fracture of a material when measured in a direct tensile, compressive or transverse test it is possible that, over a period of time, failure may occur by a fatigue process. This involves the formation of a microcrack, possibly caused by stress concentration at a surface fault or due to the shape of the restoration or prosthesis. This crack slowly propagates until fracture occurs. Final fracture often occurs at quite a low level of stress, a fact which often surprises patients who claim that their denture fractured when biting on soft food.
Fatigue properties may be studied in one of two ways. Firstly, it is possible to apply a cyclic stress at a given magnitude and frequency and to observe the number of cycles required for failure. The result is often referred to as the fatigue life of a material. Another approach is to select a given number of stress cycles, say 10 000, and determine the value of the cyclic stress which is required to cause fracture within this number of cycles. The result in this case is referred to as the fatigue limit. Both methods play an important part in materials’ evaluation. The most rigorous approach is to test many specimens at different cyclic stress levels and to determine the number of cycles to failure in each case. The result is then given in the form of a graph as shown in Fig. 2.10. As the applied cyclic stress increases, the number of cycles to failure decreases.
Fig. 2.10 Fatigue testing. Results are often given as a graph of cyclic stress versus number of cycles to failure. At smaller stress levels a greater number of cycles are required to cause fracture.
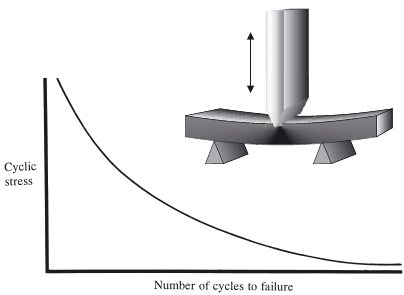
One of the most important factors involved in such tests is the quality of the specimen used in the test since faults introduced during preparation can drastically reduce both fatigue life and fatigue limit.
Fatigue failure has often received only scant consideration in the past as a possible mode of failure for dental materials. It is now recognized that stress concentrations within materials can occur to an extent where cracks can propagate to cause failure within the normal lifetime of the material. Where fatigue cracks occur near the surface of a material and result in/>
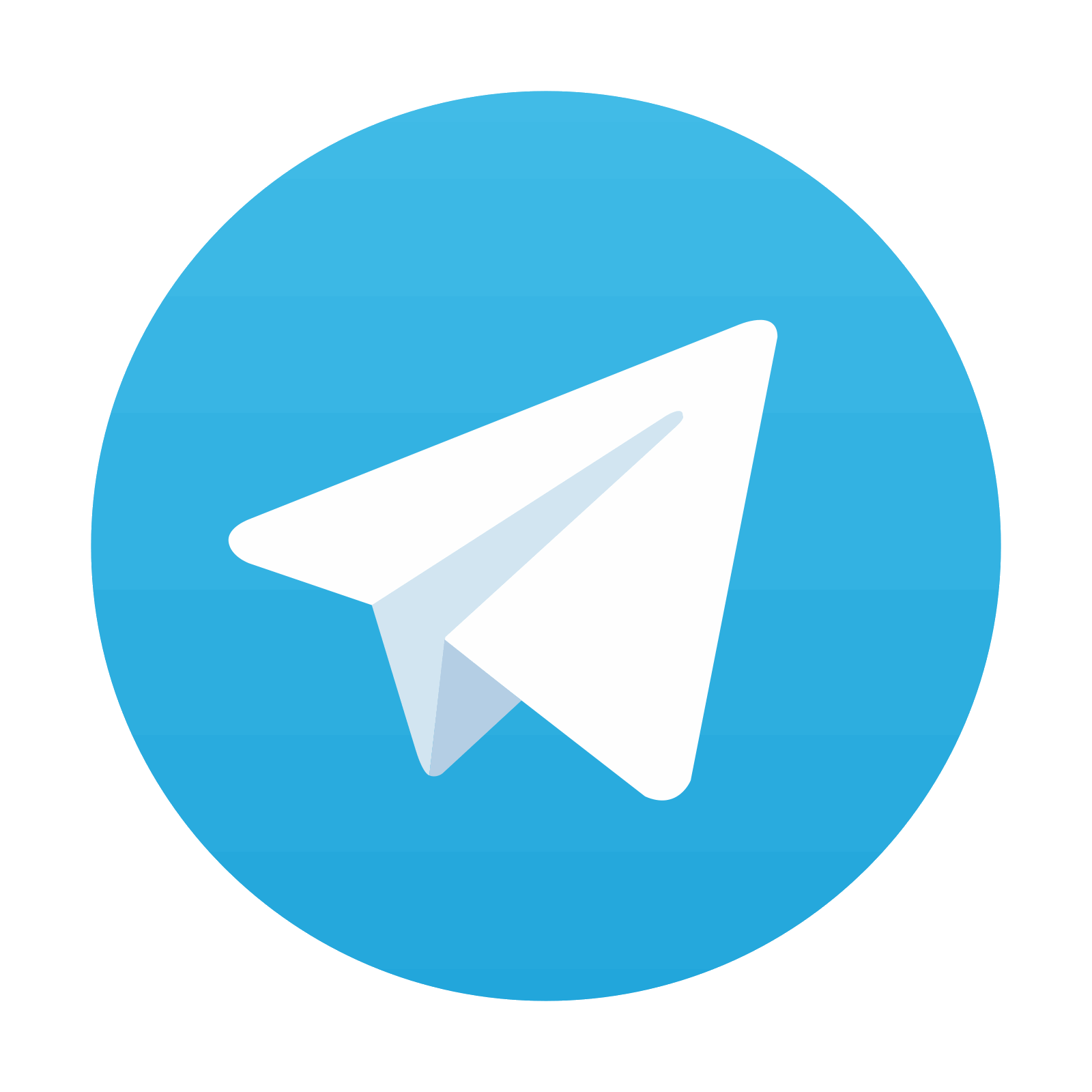
Stay updated, free dental videos. Join our Telegram channel

VIDEdental - Online dental courses
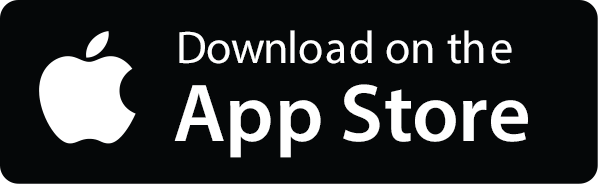
