Chapter 7
Gold and Alloys of Noble Metals
7.1 Introduction
In the ‘as cast’ condition, pure gold is too soft to maintain its shape under the forces of mastication. Its strength and hardness can be greatly improved by either cold working or alloying.
Gold is very malleable and ductile and can be readily cold worked. This characteristic is utilized in the restoration of teeth using pure gold fillings. Alloys of gold are commonly used for cast restorations. The use of wrought gold wires is dealt with in a separate chapter dealing with wrought alloys.
7.2 Pure gold fillings (cohesive gold)
When two pieces of pure gold are pressed together, metallic bonds are formed at their point of contact and the gold is welded together, without the application of heat. This property of cold welding is utilized when building up a pure gold filling. The surfaces of the two pieces of gold must be perfectly clean to allow intimate contact and the applied force must be great enough to encourage the formation of bonds.
Cohesive gold is normally used in the form of a very thin gold sheet or ‘foil’, approximately 0.001 mm thick. On condensation into the prepared cavity, each layer of foil becomes welded to the material already condensed. It is normal practice to heat the gold foil to about 250°C in an electric furnace or a gas flame before use to remove any adsorbed grease or gases which would prevent efficient welding. The tooth to be filled must be isolated from the saliva using rubber dam and thoroughly dried to avoid contamination during condensation.
Condensation or ‘plugging’ of the gold may be carried out by hand, with an automatic mallet, orby the application of a mechanical vibrator. The use of an automatic mallet involves the application of a relatively large force at infrequent interdelivers much lighter, butvals, whereas a pneumatic or electrically driven condenser delivers much lighter, but more frequent blows. Care must be taken not to overheat the filling during the finishing procedures where the occlusal contour of the tooth is ‘carved’ using rotary finishing instruments then polished. Marked heating can cause damage to the pulp. The tooth and its supporting structures must withstand the fairly harsh treatment they receive during condensation without becoming damaged. Fortunately, both the dentine and periodontal membrane are fairly resilient.
The mechanical properties of the pure gold filling depend on the amount of cold working carried out on the material. The degree of work hardening depends on the pressure applied during condensation and the length of time for which the material is condensed. Practical limitations of time and the pressure which can be tolerated by the patient restrict the hardness of the pure gold filling to values similar to those for the softer (type I) casting gold alloys. Sandwich foils of gold and platinum are also available which produce a condensed restoration with better physical characteristics. These can be used to produce small class II restorations using a similar approach.
The advantages of the gold foil filling are that it is perfectly corrosion resistant and does not rely on a relatively soluble cement lute for retention. In cavities where the filling is surrounded by tooth substance, or where there is little or no opposing force, the mechanical properties are adequate and the pure gold filling offers a very durable restoration. In high load bearing areas, certain properties of pure gold such as rigidity and elastic limit are insufficient to resist distortion. Apart from this, the high cost of these restorations in terms of material used and the time taken to produce the restoration precludes their use in all but a minimal number of cases.
7.3 Traditional casting gold alloys
An indication of the composition of the traditional casting gold alloys is given in Table 7.1. The descriptions of the four types of dental casting gold alloy (types 1 to 4) are given in ISO 1562:1995 as follows:
Type 1 | low strength – for castings subject to very slight stress, e.g. inlays. |
Type 2 | medium strength – for castings subject to moderate stress, e.g., inlays and onlays. |
Type 3 | high strength – for castings subject to high stress, e.g. onlays, thin cast backings, pontics, full crowns and saddles. |
Type 4 | extra high strength – for castings subject to very high stress and thin in cross section, e.g. saddles, bars, clasps, crowns, bridges and partial denture frameworks. |
Standards for ‘dental gold casting alloys’ require a noble metal content of at least 75%. It can be seen that the gold content or nobility decreases on going from the type 1 (soft) alloy to the type 4 (extra hard) alloy. Nobility of gold alloys is often indicated by either a carat value or a fineness value. The carat value indicates the number of parts by weight of gold in 24 parts of alloy. Thus, a type 2 alloy containing 75% gold has a carat value of 18. The fineness value indicates the number of parts by weight of gold in 1000 parts of alloy. The type 2 alloy would have a fineness value of 750.
ISO 1562:1995 for dental casting gold alloys requires that of the minimum noble metal content of 75%, at least 65% shall be gold whilst the remaining noble metal components shall be platinum group metals such as platinum, palladium, iridium, ruthenium or rhodium. The most commonly used is palladium. The use of potentially hazardous constituents is discouraged as the manufacturer is required to list all the components along with the percentage of each.
Table 7.1 Typical compositions of casting gold alloys.

The increase in hardness observed when nobility decreases is primarily due to the solution hardening effect of the alloying metals which all form solid solutions with gold. The types 3 and 4 alloys can be further hardened by heat treatments.
The presence of significant quantities of platinum and palladium, as in the type 4 alloys, not only causes considerable solution hardening but also leads to a widening of the separation between the solidus and liquidus lines of the solid solution phase diagram. The results of this is an increase in coring as explained on p. 59. The cored structure can be removed by carrying out a homogenization heat treatment. Platinum and palladium also significantly increase the melting point and recrystallization temperature of gold alloys, a fact which can be used to advantage when selecting alloys for components which may require soldering.
Zinc, which is present to a concentration of about 1% in most alloys, acts as a scavenger during casting. It is the most chemically reactive of all the metals used and becomes preferentially oxidized at the high temperatures of casting. The resulting zinc oxide slag can be removed from the molten alloy. It is normal to re-use any excess alloy which is left after a casting has been produced (e.g. the alloy from the sprue). Care should be taken when doing this to ensure that sufficient zinc remains to have an effective scavenging action. When all the zinc has been oxidized the other metals of the alloy, particularly copper, become prone to attack. In order to minimize the chances of this occurring it is good practice to always include some fresh alloy in each alloy melt prepared for casting.
Table 7.2 Comparative properties of casting gold alloys.

Table 7.3 Properties of casting gold alloys.

Table 7.2 gives an indication of the comparative properties of the four types of casting gold alloys. Moving through the series from type 1 to type 4, there is an increase in hardness, strength and proportional limit. The corrosion resistance decreases as the gold content is reduced, although for practical purposes all of the alloys may be considered adequate from this point of view. Ductility and malleability also decrease when the gold content is reduced. Table 7.3 gives more detailed information regarding the properties of the alloys. It is interesting to note that the ability to withstand stress within the elastic range is given by the 0.2% proof stress as opposed to the proportional limit (see Chapter 2). The proof stress is more readily determined and arguably more meaningful than the proportional limit. It represents the stress required to cause a permanent deformation of a particular value (0.2% in this case). Table 7.4 gives the ISO specification limits which apply to the materials.
The variation in alloy properties with composition is reflected in the applications for which the materials are chosen. The relatively soft, type 1 alloys are used for inlays which are well supported by tooth substance and which do not have to resist large masticatory forces. The high values of ductility of these alloys enables them to be burnished – a process which improves the marginal fit of the inlay and increases surface hardness. The need to improve the fit of inlays by burnishing has decreased with improvements in casting accuracy.
The type 2 alloys are the most widely used alloys for inlays. They have superior mechanical properties when compared with the type 1 materials, though at the expense of a slight decrease in ductility.
The type 3 (hard) alloys are used where there is less support from tooth substance and when opposing stresses are likely to be relatively high. Examples of the use of these materials include the production of crowns and inlays for high stress areas such as class II cavities in molars. Type 3 alloys with a high copper content (>8%) can be heat treated in air at 400°C for 10 minutes to produce a stable copper oxide layer on their surface. Chemically active adhesive luting resins can then be used to bond such structures to tooth tissue rather than relying upon mechanical retention form and a conventional luting cement for retention. The high platinum and/or palladium content of the type 3 alloys, leading to a higher melting point, is beneficial when constructing components for bridges which are joined by soldering.
Type 4 alloys are used in high stress areas and for constructing components of partial dentures and for this reason are normally referred to as partial denture casting alloys. Partial dentures normally have clasps or other devices for retaining the denture. These must be flexible enough to engage undercuts in standing teeth but have sufficiently high values of proportional limit such that they do not become distorted. The type 4 gold alloys possess th/>
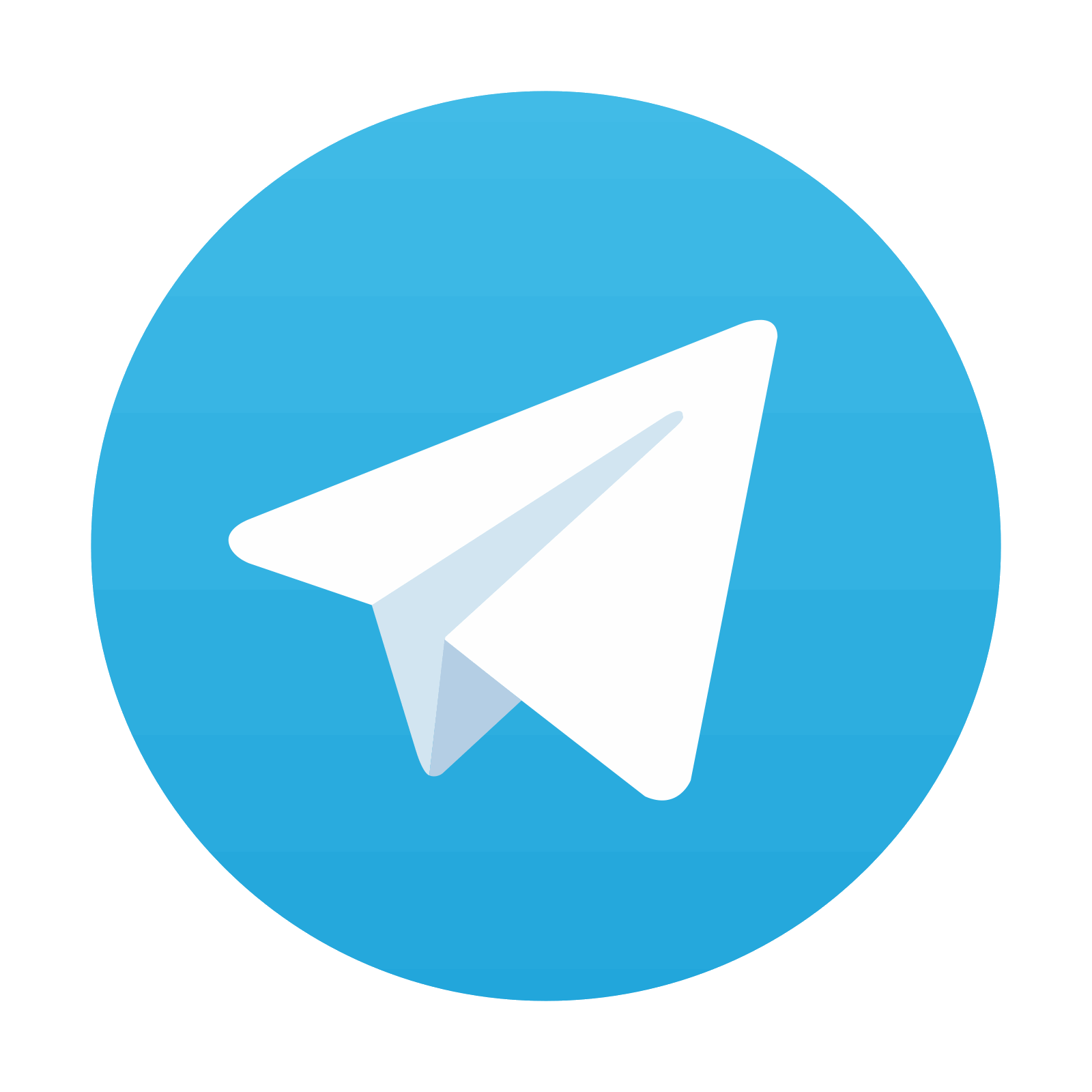
Stay updated, free dental videos. Join our Telegram channel

VIDEdental - Online dental courses
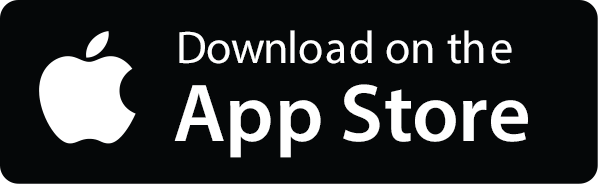
