Dental amalgams
Introduction
Dental amalgam had a fairly inauspicious beginning, early in the 19th century, when it was used as a restorative material, being made by mixing Spanish or Mexican silver coins with mercury. Dental amalgams have come a long way since then, and are still a part of everyday dental practice.
The development of dental amalgams is due, in no small way, to one of the most famous dentists ever, G.V. Black, who recognized the need to determine the properties of dental amalgams with some accuracy, if their performance was ever going to be predictable. At the beginning of the 20th century, because of his research work, amalgams could be produced with reasonably predictable handling characteristics.
Over the years, our understanding of these materials has advanced considerably, but up until the late 1960s, there was little change in this field and the composition was very much as it had been for the preceding 50 years.
During the last 50 years, it seems as though the developers of dental amalgams have tried to make up for this lack of activity, with new formulations appearing at frequent intervals. There has been an onslaught on the traditional applications of this material by new materials, such as the resin composites and the glass–ionomer cements. While this has led to some exciting new developments in dental amalgams, it has made the dentist’s job more difficult, as the selection of the best available product at the best possible price becomes more and more complicated.
In this section, the development of the amalgams from the late 1960s to their current status is charted, highlighting the important advances made.
The structure of traditional dental amalgams
Composition
An amalgam is formed when mercury is mixed with another metal or metals. Mercury is liquid at room temperature (solidifying at −39°C), and it reacts readily with metals such as silver, tin and copper, to produce solid materials. When the dentist selects a certain dental amalgam, it is effectively a selection of the alloy with which the mercury will be mixed and react.
Strictly speaking, the term dental amalgam cannot be used until one is referring to the material produced as a consequence of the reaction between the mercury and the alloy. This alloy can vary either in composition or in form, and dental amalgam manufacturers use this variability to produce a wide range of products.
Alloy
The alloy used in the traditional dental amalgams consists of a mixture of silver, tin, copper and sometimes zinc and/or mercury. A typical composition may be as shown in Table 2.1.1.
Table 2.1.1
Constituents of a typical dental amalgam alloy
Constituent | % of total |
Ag | 67–74 |
Sn | 25–28 |
Cu | 0–6 |
Zn | 0–2 |
Hg | 0–3 |
Silver is the main constituent, present in combination with tin as the intermetallic compound Ag3Sn, known commonly as the γ phase. The phase diagram for the Ag–Sn system is shown in Figure 2.1.1, and shows that the Ag3Sn phase is the third pure phase in the system, hence the Greek symbol γ.
This γ phase reacts readily with mercury to form the dental amalgam. Copper is present to increase the strength and hardness of the amalgam, and a more pronounced effect is produced when the copper content is increased beyond 6%, but this will be dealt with later. Zinc may be present as a result of the initial production of the alloy, and is not considered to serve any useful purpose in the amalgamation process. Mercury is sometimes added to provide a more rapid reaction, in what is referred to as pre-amalgamation.
The alloy is used in the form of a powder, and the size and shape of the particles in this powder are critical to the handling characteristics and the final properties of the restoration. The alloy powder is available as either lathe-cut particles or spherical particles, as shown in Figure 2.1.2.
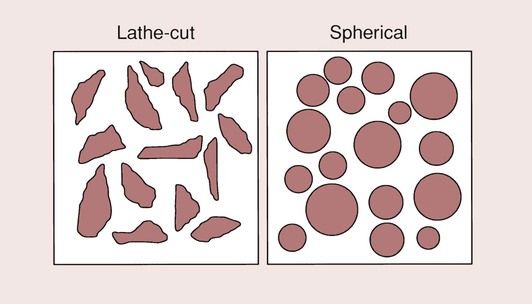
Lathe-cut
The lathe-cut particles are produced by machining a solid ingot of the alloy on a lathe. The chippings that are produced are graded, and only those in the right size range are used in the powder to be amalgamated with mercury.
The alloy is available as coarse-, medium- or fine-grained powder, and each will handle slightly differently. The individual chippings will have become highly stressed during the machining, and this makes their surfaces very reactive to mercury. A consequence of this is that the setting reaction is far too rapid unless heat treatment (which relieves the internal stresses) is applied. The heat treatment is usually carried out by placing the powder in boiling water.
Spherical particles
The production of the spherical particles is by a quite different route. The various ingredients of the alloy are melted together and then sprayed into an inert atmosphere, where the droplets solidify as small, spherical pellets of various sizes. This method of manufacture has the advantages that no further machining processes are required, and that the composition of the alloy can be readily altered. What is important to the manufacturer is that the yield of particles of the correct size is as high as possible, since this minimizes the cost of production. The particles that are rejected because they are either too big or too small are simply recycled.
Mercury
The mercury used in the preparation of an amalgam needs to be very pure; otherwise a surface layer of contaminants is formed that interferes with the setting reaction. For this reason, the mercury is triple-distilled. The purity can easily be checked by visual examination. If a dull surface is observed, as opposed to the usual highly reflective surface, the mercury is contaminated.
Setting reaction
The setting reaction between the Ag–Sn alloy and the mercury is initiated by a vigorous mixing of the two ingredients. This mixing causes the outer layer of the alloy particles to dissolve into the mercury, forming two new phases, which are solid at room temperature. The reaction is as follows:
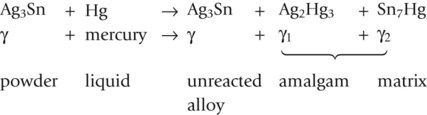
As can be seen from the reaction, not all of the alloy particles dissolve in the mercury. On the contrary, a considerable amount remains, so that the final structure is one of a core of γ held together by a matrix of predominantly γ1, which is interspersed with γ2. The structure of the set material is shown in Figure 2.1.3.
The copper in the lathe-cut alloy is present in the form of discrete areas of Cu3Sn, and remains mainly within the original alloy in its unreacted form.
In the case of the spherical particles, the copper is uniformly distributed, and the alloy could be more accurately regarded as a ternary alloy of silver, tin and copper. Hence, in the final structure of the spherical alloy amalgam, the copper is not present as a discrete phase but is widely distributed throughout the material. Although some voids will inevitably be present, in a well-condensed amalgam there will be very little porosity.
Properties of traditional amalgams
It is not the intention here to cover all aspects of the properties of dental amalgams, and only those properties of some importance to clinical use and development of new alloys will be considered.
Strength
The strength of an amalgam is extremely important, since the restoration has to be able to withstand the considerable loads generated during mastication, and any lack of strength is likely to lead to marginal ditching of the restoration or even gross fracture.
Although most attention has been paid to the final compressive strength of the set material, it is perhaps more important to consider the tensile strength and the rate at which the final strength is acquired.
As might be imagined, the final strength of the amalgam will be a function of the properties of the individual phases. It is not easy to determine the properties of the three main phases of an amalgam, but micro-hardness measurements suggest that the γ phase and the γ1 phase have a similar hardness, while the γ2 phase is considerably softer. The tensile strength of the γ2 phase has also been measured to be only a fraction of that of the original γ phase, with the γ1 phase falling in between (Table 2.1.2).
Table 2.1.2
Tensile strengths of phases of amalgam
Phase | Tensile strength (MPa) |
γ | 170 |
γ1 | 30 |
γ2 | 20 |
Amalgam | 60 |
This means that the weak link within the amalgam structure is the γ2 phase, and if its proportion in the final composition could be minimized, a stronger amalgam would result. The amount of γ1 and γ2 formed is strongly dependent on the amount of mercury in the final composition. The higher the mercury content, the weaker the material will be, because larger amounts of the weaker phases will be produced.
The final mercury content of the amalgam is dependent on the quality of the condensation technique more than anything else, with a properly condensed amalgam having a mercury content of just less than 50%. Besides the condensation technique, the size and shape of the alloy particles will also affect the final mercury content. The initial ratio of alloy to mercury is lower in amalgam made with spherical alloy particles than with lathe-cut alloy particles because the material is more easily condensed. With spherical alloy particles, a final mercury content of about 45% is readily achievable.
The particle size is also important. For a given amount of alloy that is to be amalgamated with mercury, choosing smaller alloy particles results in more of the alloy surface being exposed to the mercury. This means that more of the alloy will dissolve in the mercury, producing more of the mercury-containing phases. Consequently, too small a particle size is contraindicated.
Whatever the form of the alloy used, the conscientious removal of excess mercury during the placement of a restoration is vitally important.
Flow and creep
It has been postulated that the excessive flow of an amalgam, resulting from repeated occlusal loading, can cause flattening of contact points, overhanging margins, and protrusion of the restoration from the tooth surface at the margin. The latter has been implicated as a major source of marginal breakdown. Although flow is measured for amalgam in laboratory tests, the measurement is usually carried out over a short period very soon after mixing and is therefore of limited clinical relevance. A more appropriate measurement would be that of creep. This is the flow caused by loads acting over long periods. Creep is dependent on both the yield strength of the material and the temperature of the environment, and only becomes a serious problem when the environmental temperature is greater than half the melting temperature of the material.
Since the amalgam phases have very low melting temperatures (about 80°C) and the restorations are subjected to repeated loadings, there is the possibility of creep occurring. The phases most prone to creep will be the mercury-based γ1 and γ2 phases. Consequently, the lower the proportion of these phases present (as may be achieved by proper condensation), the less susceptible the amalgam will be to creep.
Corrosion
It is well recognized that amalgams corrode in the oral environment. Indeed, corrosion is often cited as an advantage, in that the corrosion products help to produce a good marginal seal. However, crevice corrosion, caused by the formation of an oxidation cell in the marginal gap, can cause a rapid deterioration in the properties of the amalgam. The corrosion process is especially associated with the γ2 phase.
The γ2 phase is considerably more electronegative than the γ and γ1 phases. This means that, in the presence of an electrolytic solution, the γ2 phase will act as the anode of the oxidation cell and will gradually dissolve. The reaction is as follows:
tin-mercury phase + oral fluids → tin salts + free mercury
Sn7Hg + oxygen → oxides & chlorides + Hg
Normally, the formation of oxides would help to slow down the corrosion process by forming a protective surface coating. However, in the gap between the amalgam and the tooth tissues, a surface oxide is not formed, as the reaction products from the corrosion process precipitate out. The process is also very insidious, since the production of free mercury allows further reaction with γ, and the formation of more γ1 and γ2. This process will severely weaken the amalgam structure, and is often cited as a cause of marginal breakdown.
High-copper-content dental amalgams
From the above discussion of the properties of the traditional dental amalgams, it can be deduced that an improvement in their performance may be possible if their strength could be increased. This strengthening is possible by reducing the amount of γ1 and γ2, or better still if the weak and corrosion-susceptible γ2 phase could be eliminated from the structure entirely, with the added benefit that creep could be reduced.
Dispersed phase amalgams
In the early 1960s, attempts were made to increase the strength of dental amalgams by increasing the copper content of the alloy.
The idea was that the copper would act as a dispersion-strengthening agent. A spherical alloy (basically silver and copper) with a high copper content was added to the conventional lathe-cut alloy. The choice of the spherical particles was made essentially because it was easier to alter the composition of spherical particles than lathe-cut particles on an experimental basis. The potential advantages, in terms of easier condensation, were also recognized at that time.
As it turned out, the increase in the copper content of the alloy resulted in a modification of the setting reaction, which proved to be highly beneficial.
The first reaction is the same as for the traditional alloys, but this is followed by a second reaction:

Thus, the final amalgam contains little or no γ2. The structure of this amalgam is shown in Figure 2.1.4.
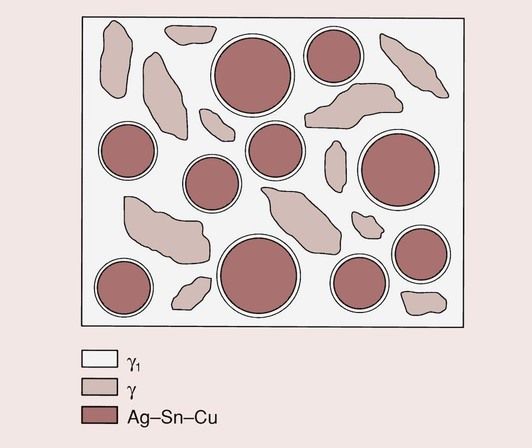
Initially, it was thought that all of the γ2 was eliminated by this reaction, but it has since been recognized that some γ2 will remain, although it is only a small and probably insignificant amount.
The modification in the setting reaction has resulted in a number of interesting and important changes in the properties of the amalgam, namely:
Other high-copper-content formulations
With these sorts of improvements, it was not long before the idea of the all-spherical high-copper amalgams came into being. These combine all of the advantages of easier condensation with those mentioned above, and a number of such products are now available.
The powder in these cases is a ternary spherical alloy of silver, tin and copper and has a setting reaction as follows:
Ag −− Sn −− Cu+Hg→Ag −− Sn −− Cu+γ1+Cu6Sn5

The reluctance of many dentists to convert from a lathe-cut alloy to a spherical alloy has led to the introduction of high-copper-content all-lathe-cut alloy formulations. The composition of these alloys is essentially the same as for all of the spherical alloys, except that there are wide differences in the total copper content, which can vary from 12 to 30%. As yet, it is not known what the optimum percentage of copper is.
For those dentists who prefer the dispersed-phase type of alloy, there are now a number available that have a mixture of spherical and lathe-cut particles, where both particle types have the same composition of ternary Ag–Sn–Cu alloy.
Selection and use of dental amalgams
In the selection of the appropriate dental amalgam, there are two major factors that need to be considered:
Both of these will have a profound effect on the properties of the dental amalgams, such as their handling characteristics and their clinical performance.
The clinical performance of an amalgam restoration is dependent as much on the correct choice of the alloy as it is on the use of a good operative procedure. The need for a good procedure involves all of the stages of amalgam placement, from the proportioning stage to the final polishing.
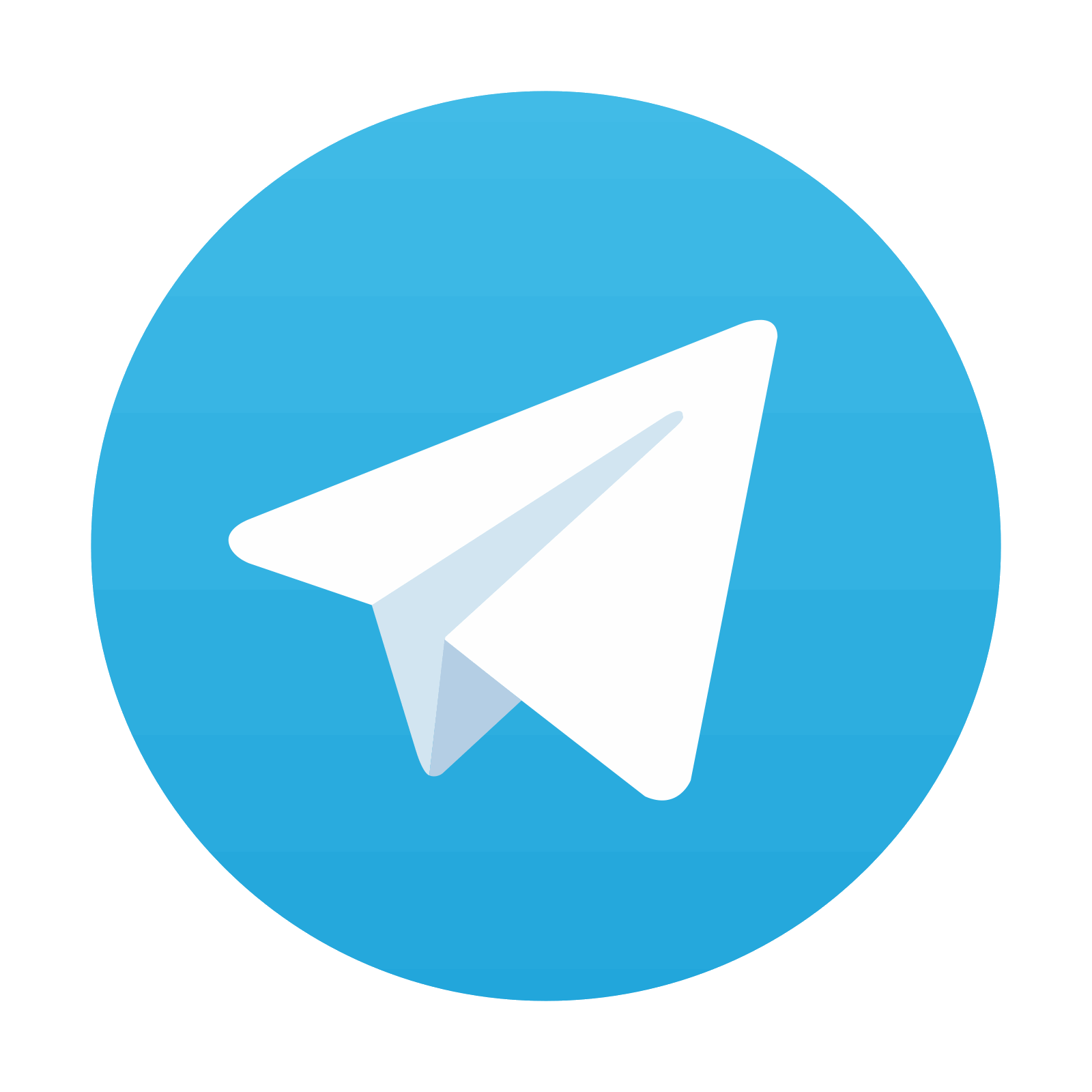
Stay updated, free dental videos. Join our Telegram channel

VIDEdental - Online dental courses
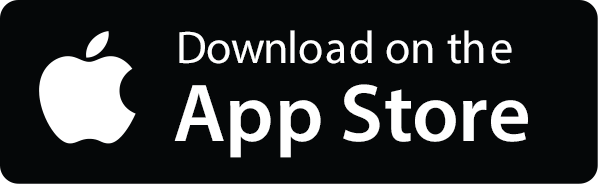
