Chapter 19
Elastic Impression Materials: Synthetic Elastomers
19.1 Introduction
Synthetic elastomers were developed mainly for industrial applications but their potential in medicine and dentistry was quickly realized and they are now widely used as impression materials. They were quick to gain acceptance in dentistry because they offered potential solutions to the two main problems associated with hydrocolloids – poor tear resistance and poor dimensional stability.
Four types of elastomers are in general use:
- Polysulphides;
- Silicone rubbers (condensation curing type);
- Silicone rubbers (addition curing type);
- Polyethers.
A classification and some properties of these materials is given in the ISO Standard for Dental Elastomeric Impression Materials (ISO 4823). Apart from the chemical nature of the material, the primary method of classification is according to consistency. This is measured by pressing 0.5 ml of mixed material between two flat plates using a force of 1.5 N. The consistency, defined by the average diameter of the resulting disc of the material, is related to the viscosity of the material at the time when the force is applied. Materials are categorized as types 0–3, as shown in Table 19.1.
The specification limits defining consistency overlap significantly between types. Hence, a material producing a disc of 31–34 mm diameter could be classified as type 0, 1 or 2. It is the manufacturer who makes the choice in this situation. The situation is further complicated by the use of terms such as ‘soft putty’, which generally indicates a type 0 material, with a relatively low viscosity (high consistency disc diameter). The situation is clarified somewhat by consideration of the manner in which the materials are used. Types 0 and 1 are normally used in combination with a type 3 material whilst type 2 materials are normally used alone and are sometimes referred to as monophase elastomeric materials. Manufacturers often package their materials in a manner which reflects their preferred combination of high viscosity (type 0 or 1) and low viscosity (type 3) product. The techniques for using the combined high and low viscosity materials are described later in this chapter.
19.2 Polysulphides
Composition: These materials are generally supplied as two pastes which are dispensed from tubes (see Fig. 19.1). One paste is normally labelled base paste whilst the other is labelled catalyst paste. The composition of a typical material is given in Table 19.2.
The liquid polysulphide prepolymer in the base paste can be represented by the formula:
although the actual structure is known to be slightly more complex than this and contains pendant thiol groups (—SH) in addition to the terminal groups shown in the structural formula. For mechanistic purposes the structure of the pre-polymer is conveniently represented by the simplified structure given in Fig. 19.2. The viscosity of the paste is governed by the quantity of filler incorporated by the manufacturer. Three grades of paste are normally available to the practitioner – ‘light-bodied’, ‘regular-bodied’ and ‘heavy-bodied’, having increasing filler contents and viscosity values.
The base paste is normally white, due to the filler, and has an unpleasant odour caused by the high concentration of thiol groups. The colour of the catalyst paste is governed by the nature of the oxidizing agent used; materials containing lead dioxide are normally dark brown. The colour contrast between the two pastes is an aid to efficient mixing, which is continued until a homogeneous colour, with no streaks, is achieved. An adhesive is used to promote adhesion between the impression material and tray.
Table 19.1 Classification of elastomeric impression materials according to consistency.
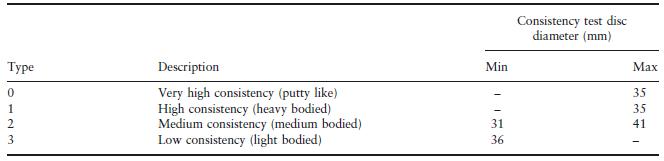
Table 19.2 Composition of polysulphide impression materials.
Component | Function | |
Base paste | Polysulphide prcpolymer with terminal and pendant thiol (–SH) groups | This is further polymerised and cross-linked to form rubber |
Plasticizer-di-n-butyl phthalate | To control viscosity | |
Inert filler – possibly chalk or titanium dioxide | To give ‘body’, control viscosity and modify physical properties | |
Catalyst paste | Lead dioxide or other alternative oxidizing agent | To react with thiol groups – causing setting |
Sulphur | Involved in setting reaction | |
Inert oil – normally paraffinic type or di-n-butyl phthalate | To form a paste with PbO2 and sulphur |
Fig. 19.1 This shows an example of a polysulphide impression material. The two pastes with contrasting colours are mixed together on a mixing pad with a metal spatula.
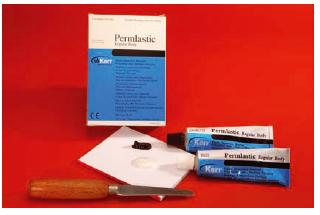
Fig. 19.2 Simplified structural formula of the polysulphide prepolymer showing terminal and pendant – SH groups.
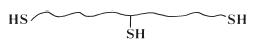
Setting reaction: On mixing the two pastes, terminal and pendant thiol groups of the prepolymer chains undergo a reaction with lead dioxide. Some of these reactions result in chain extension and cross-linking as shown in Fig. 19.3. The reaction is of the condensation polymerization type since one molecule of water is produced as a byproduct of each reaction stage. As chain extension proceeds, the viscosity increases. When the degree of cross-linking reaches a certain level the material develops elastic properties.
Properties: The setting characteristics of the polysulphides differ considerably from those of the alginates (Section 18.3). Setting commences immediately on mixing of the two pastes and is characterised by a gradual increase in viscosity and a rather slow development of elasticity. Setting times of 10 minutes or more are not uncommon, particularly for light-bodied materials. The polysulphide elastomers have very good tear resistance. They can, typically, withstand about 700% tensile strain before tearing. Some of this strain is non-recoverable, since the elastic properties of these materials are far from ideal. They are considered as viscoelastic and recover only slowly and not completely after being compressed or stretched. The time required for recovery and the degree of permanent deformation are functions of the severity of the undercuts and the time for which the material is under strain. In order to optimize elastic recovery the impression should be removed with a single, swift pull.
Fig. 19.3 Schematic representation of the chain lengthening and cross-linking of the polysulphide prepolymer through oxidation of the –SH groups forming disulphide links. Water is liberated as byproduct.
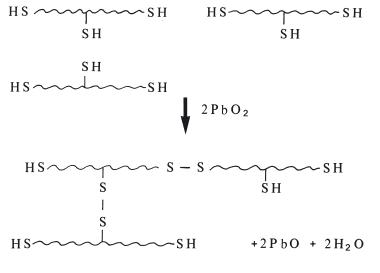
Table 19.3 Influence of filler content on some properties of polysulphides.

Many of the properties of these products are directly related to the amount of filler incorporated in the pastes. This particularly applies to viscosity, setting contraction, thermal contraction after removal of the impression from the mouth and dimensional stability (Table 19.3). It can be seen that the heavy-bodied materials are potentially more accurate, since they exhibit less setting and thermal contraction and have better dimensional stability. Their high viscosity means that they are unable to record the same level of fine detail as the more fluid, light-bodied materials.
Dimensional changes occurring after apparent setting of polysulphides are due to two major factors. Firstly, continued reaction occurs for some time after the apparent setting time, causing further shrinkage. Secondly, water produced as a byproduct of the setting reaction may be lost by evaporation from the surface. In this case the dimensional change is also associated with a change in weight of the material. The better dimensional stability of the heavy-bodied materials is due to the fact that they contain a lower concentration of reactive groups and therefore produce fewer byproducts. Although the polysulphides do not have perfect dimensional stability they perform far better than hydrocolloids in this respect.
The use of lead compounds in polysulphide materials has been questioned because of the known toxic effects of lead. It is unlikely that the lead contained in these products is able to exert a harmful effect as the material is in the patient’s mouth for only a few minutes and is hydrophobic, reducing the chances of ‘washing out’ of lead compounds by saliva. The use of lead-free polysulphides is likely to increase, however, as a wider range of alternative materials becomes available.
Clinical use: These materials are most commonly used in two viscosities, high and low, and must be used in a special tray. They have a number of advantages clinically, including reasonable tear strength and good elastic properties. They have an unpleasant odour and taste. They are moderately hydrophilic and hence can work well in the presence of some moisture. They are commonly used for crown and bridge impressions and only infrequently for other applications. The clinical technique usually adopted for polysulphides is a one-stage procedure. Freshly mixed low viscosity material is loaded into an impression syringe and the high viscosity material is loaded into the special tray. The light-bodied material is injected around those teeth on which cavities have been cut or crown cores prepared. The tray, containing heavy-bodied material, is then seated so that the two materials can set simultaneously. Figure 19.4 is a line diagram which gives the appearance of the impression viewed in cross-section. It can be seen that the bulk of the impression is recorded in heavy-bodied material – assuring optimum accuracy and dimensional stability. The thin layer of the impression adjacent to the oral tissues is recorded in light-bodied material – assuring optimum fine-detail reproduction.
Fig. 19.4 Line diagram showing section of an impression in which heavy-bodied, A, and light-bodied, B, materials have been used to obtain optimal accuracy and dimensional stability.
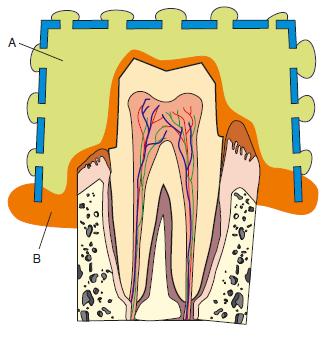
Once set the casts can be disinfected with the regime already described and can be poured after a short period to allow for full elastic recoil of the material. The casts should be poured within 24 hours of mixing if possible. Whilst the materials have good short term dimensional accuracy, they will undergo plastic flow after setting. One great benefit is that the surface of the impression can be electroplated using a copper sulphate electroplating bath. An epoxy resin die material can then be used to form the bulk of the working cast. Such metal/plastic dies, whilst expensive to produce, are very hard and are not prone to damage in the laboratory when the crown and bridgework is being made.
This approach can be used when multiple operations are being undertaken on the same die. One example of this would be when a clinician wants to make multiple crowns or a combination of crowns and bridges for a patient on the working cast. It can then be difficult to record accurate impressions of many teeth in one impression. In this circumstance, multiple impressions are used to produce accurate individual metal/resin dies for each of the teeth concerned. A plastic transfer coping is then made for each die. This is a small thimble of plastic which is made without spacing to fit over each die. The transfer copings are then taken back to the patient and placed over each of the prepared teeth. A locating impression is then recorded, capturing all of the copings in the impression. The individual dies are then placed in their respective copings and a working model is produced by pouring a base around the dies, usually from dental stone. This master model is then used by the technician to produce the metal or porcelain crowns and bridges. If this approach is attempted with conventional gypsum-based dies there is a high chance of their margins being damaged during the manufacture of the transfer copings, thus diminishing the chances of achieving an accurate fit with the definitive crown and bridge work.
There have been some limited reports of allergic responses to these materials, from people with an allergy to latex products.
Table 19.4 Composition of a paste–liquid silicone rubber impression material (condensation curing).
Component | Function | |
Paste | Hydroxyl-terminated polydimethylsiloxane (liquid silicone prepolymer) | Undergoes cross-linking to form rubber |
Insert filler such as silica | Gives ‘body’, controls viscosity and modifies physical properties | |
Liquid | Alkyl silicate such as tetraethylsilicate | Acts as cross-linking agent |
Tin compound such as dibutyl tin dilaurate | Acts as reaction catalyst |
19.3 Silicone rubbers (condensation curing)
Composition: These materials may be supplied as two pastes or as a paste and liquid. Whichever method of dispensation is used the principle of the setting reaction is similar and depends on the cross-linking of hydroxyl-terminated polydimethylsiloxane chains, brought about by an alkyl silicate cross-linking agent and a tin compound as catalyst. The ingredients required for this reaction to occur are reflected in the composition of a typical paste/liquid material, given in Table 19.4. These materials are very similar to the room temperature polymerizing silicones used as denture soft liners. Figure 19.4 gives the structural formula of the silicone prepolymer. The viscosity of the paste is controlled by the amount of inert filler, as in the case of the polysulphides. Light-bodied, regular-bodied, heavy-bodied and ‘putty’ materials are available. The latter is a paste of a very high viscosity and its availability denotes an important difference between the silicones and polysulphides.
Proportioning of the paste/liquid materials is by mixing a given volume of paste with a fixed number of drops of liquid. For paste/paste materials equal lengths of pastes are mixed together. A colour contrast between the pastes enables the operator to see when proper mixing has been achieved.
Setting reaction: On mixing the two components, either two pastes or paste and liquid, a reaction begins immediately in which the terminal hydroxyl groups of prepolymer chains react with the crosslinking agent under the influence of the catalyst (see Fig. 19.5). Each molecule of cross-linking agent may, potentially, react with up to four prepolymer chains causing extensive cross-linking. Each reaction stage also produces one molecule of ethyl alcohol as a byproduct. Cross-linking produces an increase in viscosity and the rapid development of elastic properties.
Properties: The setting characteristics of the silicone materials tend to be more favourable than those of the polysulphides. Setting times are generally shorter and elasticity is developed earlier.
The silicone impression materials are very hydrophobic and are readily repelled by water or saliva. As a result, it is necessary to dry areas of the mouth for which an accurate impression is required. If a dry field is not secured ‘blow holes’ are likely to occur in the impression as the material will fail to drive away the residual moisture.
The set material has adequate tear resistance for most purposes. A regular-bodied si/>
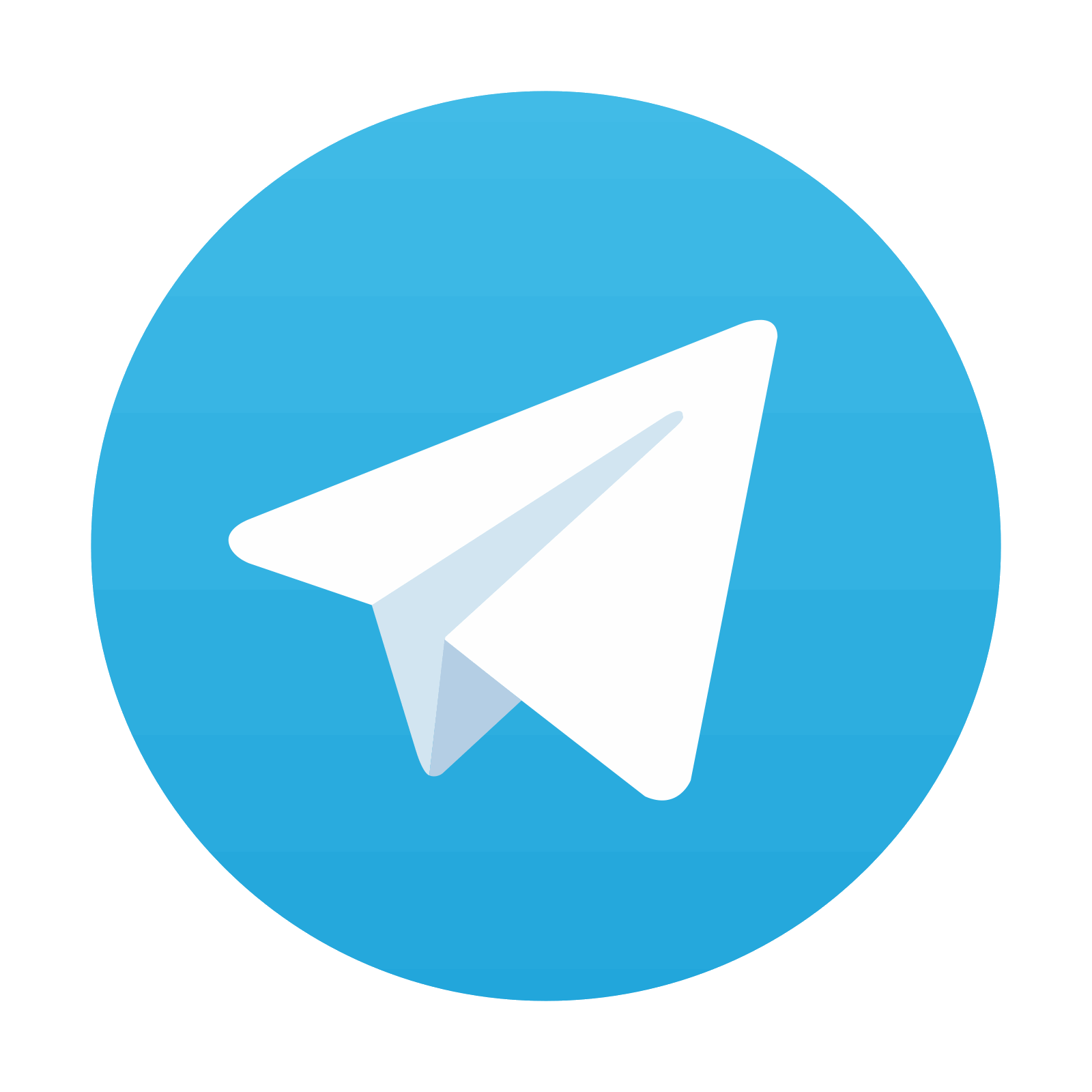
Stay updated, free dental videos. Join our Telegram channel

VIDEdental - Online dental courses
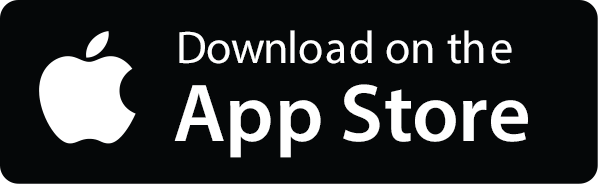
