Replicating Materials—Impression and Casting
Impression materials are used to register or reproduce the form and relationship of the teeth and oral tissues. Hydrocolloids and synthetic elastomeric polymers are among the materials most commonly used to make impressions of various areas of the dental arch. Each of these classes of materials has certain advantages and disadvantages. An understanding of the physical characteristics and the limitations of each material is necessary for their successful use in clinical dentistry. Digital impressions are described in Chapter 14. Waxes and dental pattern materials are discussed on the website. http://evolve.elsevier.com/sakaguchi/restorative
Purpose Of Impression Materials
Impression materials are used to make an accurate replica or mold of the hard and soft oral tissues. The area involved may vary from a single tooth to the whole dentition, or an impression may be made of an edentulous mouth. The impression is a negative reproduction of the tissues, and by filling the impression with dental stone or other model material, a positive cast is made that can be removed after the model material has set. An impression and a stone cast made from the impression are shown in Figure 12-1. Casts of the mouth are used to evaluate the dentition when orthodontic, occlusal, or other problems are involved, and in the laboratory fabrication of restorations and prostheses.
Usually the impression material is carried to the mouth in an unset (plastic) condition in a tray and applied to the area under treatment. When the impression material has set, it is removed from the mouth with the tray. The cast is made by filling the impression with dental stone or other model material. The accuracy, detail, and quality of this final replica are of greatest importance. When the positive reproduction takes the form of the tissues of the upper or lower jaw and serves for the construction of dentures, crowns, fixed dental prostheses, and other restorations, it is described as a cast. The positive reproduction of the form of a prepared tooth constitutes a die for the preparation of inlays or fixed dental prostheses. When a positive likeness of the arch or certain teeth is reproduced for orthodontic treatment, it is sometimes described as a model, although the term cast is the more proper term. On other occasions and in other branches of dentistry, these terms are used interchangeably. Sometimes impression materials are used to duplicate a cast or model that has been formed when more than one positive reproduction is required. Such impression materials are referred to as duplicating materials (refer to website for addition information).
A variety of impression trays are used to make impressions. Examples of typical impression trays are shown in Figure 12-2. The tray is placed so the material is supported and brought into contact with the oral tissues, then held without movement until the impression material has set. The tray with the impression material is then removed from the mouth, and the impression is ready for disinfection and pouring with a cast material to make a positive replica. The clinical impression technique and the production of the cast vary with each impression material. The properties of custom trays are discussed later in this chapter.
Desirable Qualities
Affording safe contact with tissues in the mouth and having the ability to fulfill the needs of clinical procedures are critical requirements that dictate the physical properties of dental impression materials. No impression material fulfills every requirement, and selection of the material best suited for a particular clinical situation and technique rests with the dentist. The desirable properties of an impression can be summarized briefly as follows:
1. A pleasant odor, taste, and acceptable color
< ?mpslid E94?>< ?mpslid S95?>
2. Absence of toxic or irritant constituents
< ?mpslid E95?>< ?mpslid S96?>
3. Adequate shelf life for requirements of storage and distribution
< ?mpslid E96?>< ?mpslid S97?>
4. Economically commensurate with the results obtained
< ?mpslid E97?>< ?mpslid S98?>
5. Easy to use with the minimum of equipment
< ?mpslid E98?>< ?mpslid S99?>
6. Setting characteristics that meet clinical requirements
< ?mpslid E99?>< ?mpslid S100?>
7. Satisfactory consistency and texture
< ?mpslid E100?>< ?mpslid S101?>
< ?mpslid E101?>< ?mpslid S102?>
< ?mpslid E102?>< ?mpslid S103?>
10. Adequate strength to avoid breaking or tearing upon removal from the mouth
< ?mpslid E103?>< ?mpslid S104?>
< ?mpslid E104?>< ?mpslid S105?>
12. Compatibility with cast and die materials
< ?mpslid E105?>< ?mpslid S106?>
< ?mpslid E106?>< ?mpslid S107?>
14. Readily disinfected without loss of accuracy
< ?mpslid E107?>< ?mpslid S108?>
15. No release of gas or other byproducts during the setting of the impression or cast and die materials
< ?mpslid E108?>
Types of Impression Materials
Alginate hydrocolloid and elastomeric impression materials are the most widely used today, and the properties of these are examined first. Elastomeric impression materials have replaced rigid setting materials such as plaster, impression compound, and zinc oxide–eugenol for recording soft-tissue and occlusal relationships. Information on plaster, impression compound, and zinc oxide–eugenol impression materials can be found on the website http://evolve.elsevier.com/sakaguchi/restorative
Alginate Hydrocolloids
Dental alginate impression materials change from the sol phase to the gel phase because of a chemical reaction. Once gelation is completed, the material cannot be re-liquefied to a sol. These hydrocolloids are called irreversible to distinguish them from the agar reversible hydrocolloids. Agar impression materials are described on the website. Alginate impressions are widely used to form study casts used to plan treatment, monitor changes, and fabricate provisional restorations and removable dental prostheses. http://evolve.elsevier.com/sakaguchi/restorative
Alginate impression products have acceptable elastic properties. Preparation for use requires only the mixing of measured quantities of powder and water. The resulting paste flows well and registers acceptable anatomical detail. Gypsum casts and models are made by pouring dental plaster or stone into the impression; no separating medium is necessary. The powder is supplied in bulk containers along with suitable measures for dispensing the correct quantities of powder and water. The powder is also available in small sealed packets containing a quantity suitable for a single impression and ready for mixing with a measured quantity of water. These methods of packaging, together with the measuring devices supplied by the manufacturer, are shown in Figure 12-3.
Composition and Chemistry
Potassium and sodium salts of alginic acid have properties that make them suitable for compounding a dental impression material. Alginic acid, which is prepared from a marine plant, is a high-molecular-weight block copolymer of anhydro-β-d-mannuronic acid and anhydro-β-d-guluronic acid, as shown in the top part of the formula for alginate below. The properties of alginate raw material depend largely on the degree of polymerization and the ratio of guluronan and mannuronan blocks in the polymeric molecules. The mannuronan regions are stretched and flat, whereas the guluronan regions contribute less flexibility. Also, mainly guluronan blocks bind with Ca2+. Therefore, alginates rich in guluronan form strong, brittle gels, whereas those rich in mannuronan form weaker and more elastic gels.
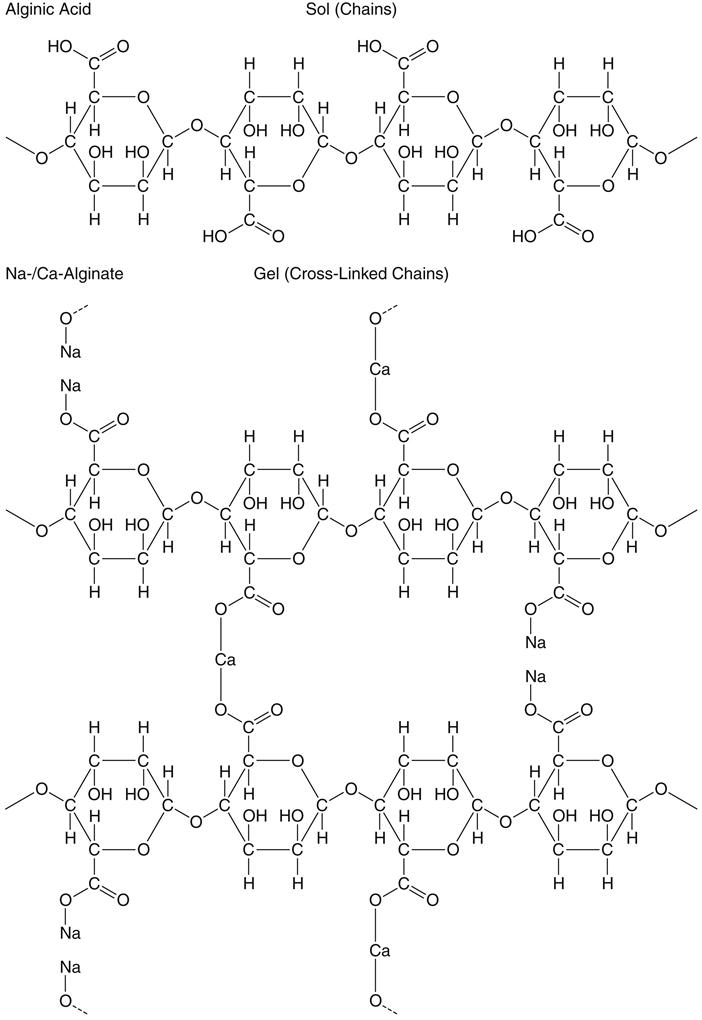
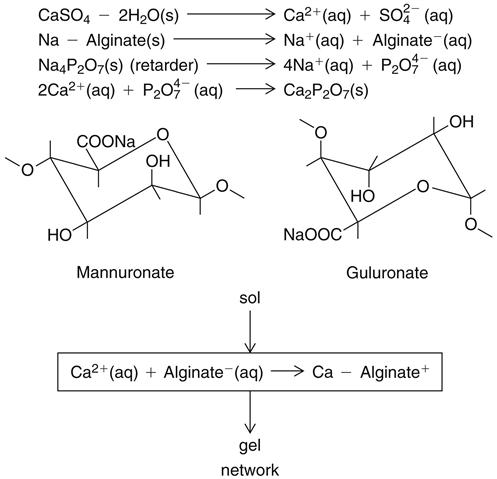
Solutions of these soluble salts, when reacted with a calcium salt, produce an insoluble elastic gel commonly called calcium alginate; the structures are shown above. Upon mixing with water, the alginate impression material first forms a sol. Following the chemical reaction described above, a gel is formed to create the set impression material. The gel-forming ability of alginates is mainly related to the proportion of L-guluronan blocks. The concept of sols and gels is presented in the discussion of colloids in Chapter 4.
The nature of this chemical reaction is shown above for the sodium salt. The equally common potassium salt reacts similarly. In an alginate impression compound, the calcium sulfate dihydrate, soluble alginate, and sodium phosphate are included in the powder. When water is added to the powder, compounds disassociate as shown. Calcium ions from the calcium sulfate dihydrate react preferentially with phosphate ions from the sodium phosphate and pyrophosphate to form insoluble calcium phosphate. Calcium phosphate is formed rather than calcium alginate because it has a lower solubility; thus the sodium phosphate is called a retarder and provides working time for the mixed alginate.
After the phosphate ions are depleted, the calcium ions react with the soluble alginate to form the insoluble calcium alginate, which together with water forms the irreversible calcium alginate gel. The calcium alginate is insoluble in water, and its formation causes the mixed material to gel. This reaction is irreversible; it is not possible to convert the calcium alginate to a sol after it has set.
To meet the critical requirements of a dental impression material, this reaction must be controlled to attain the desirable properties of consistency, working time, setting time, strength, elastic quality, and smooth, hard surfaces on gypsum casts. These requirements are achieved by adding agents to control the rate of the reaction, develop strength and elasticity in the gel, and counteract the delaying effect of alginate on the setting of gypsum products. The use of suitable fillers in correct quantities produces a consistency that is suitable for various clinical uses.
The composition of a typical alginate impression material and the function of its ingredients are shown in Table 12-1. Manufacturers adjust the concentration of sodium phosphate to produce regular- and fast-set alginates. They also adjust the concentration of filler to control the flexibility of the set impression material from soft-set to hard-set. Although alginate impressions are usually made in a tray, injection types are much more fluid after mixing and more flexible after setting. Manufacturers add organic glycols to the alginate powder to reduce dust. Diatomaceous earth or fine siliceous particles are used as fillers. Because these particles can be a respiratory irritant, inhalation of the dust should be minimized. Impressions should be disinfected with a spray solution after removal from the mouth and before pouring with a casting material. Other ingredients in some products include antimicrobials agents and pH indicators that change color when setting has occurred.
TABLE 12.1
Ingredients in an Alginate Impression Powder and Their Functions
Ingredient | Weight (%) | Function |
Potassium alginate | 18 | To dissolve in water and react with calcium ions |
Calcium sulfate dihydrate | 14 | To react with potassium alginate to form an insoluble calcium alginate gel |
Potassium sulfate, potassium zinc | 10 | To counteract the inhibiting effect of the hydrocolloid on the fluoride, silicates, or borates setting of gypsum, giving a high-quality surface to the die |
Sodium phosphate | 2 | To react preferentially with calcium ions to provide working time before gelation |
Diatomaceous earth or silicate | 56 | To control the consistency of the mixed alginate and the powder flexibility of the set impression |
Organic glycols | Small | To make the powder dustless |
Wintergreen, peppermint, anise | Trace | To produce a pleasant taste |
Pigments | Trace | To provide color |
Disinfectants (e.g., quaternary ammonium salts and chlorhexidine) | 1-2 | To help in the disinfection of viable organisms |
Proportioning and Mixing
The proportioning of the powder and water before mixing is critical to obtaining consistent results. Changes in the water/powder ratio will alter the consistency and setting times of the mixed material and also the strength and quality of the impression. Usually the manufacturers provide suitable containers for proportioning the powder and water by volume, and these are sufficiently accurate for clinical use.
The mixing time for regular alginate is 1 minute; the time should be carefully measured, because both undermixing and overmixing are detrimental to the strength of the set impression. Fast-set alginates should be mixed with water for 45 seconds. The powder and water are best mixed vigorously in a flexible rubber bowl with an alginate spatula or a spatula of the type used for mixing plaster and stone. Mechanical mixing devices are also available.
Properties
Some typical properties of a tray-type alginate impression material are listed in Table 12-2.
TABLE 12.2
Typical Properties of Alginate and Heavy-Bodied Agar Hydrocolloid Impression Materials
< ?comst?>
Working Time (min) | Setting Time (min) | Gelation (°C) | Recovery∗ (%) | Flexibility† (%) | Compressive Strength‡ (MPa) | Tear Strength§ (kN/m) | |
Alginate | 1.25-4.5 | 1.5-5.0 | — | 98.2 | 8-15 | 0.49-0.88 | 0.4-0.7 |
Agar | — | — | 37-45 | 99.0 | 4-15 | 0.78 | 0.8-0.9 |
< ?comen?>< ?comst1?>
< ?comst1?>
< ?comen1?>
< ?comst1?>< ?comen1?>∗< ?comst1?>< ?comen1?>At 10% compression for 30 seconds; †At a stress of 1000 g/cm2; ‡at a loading rate of 10 kg/min; §ASTM Tear Die C at 25 cm/min.
Working Time
The fast-set materials have working times of 1.25 to 2 minutes, whereas time of the regular-set materials is usually 3 minutes, but may be as long as 4.5 minutes. With a mixing time of 45 seconds for the fast-set types, 30 to 75 seconds of working time remain before the impression needs to be completely seated. For the regular-set materials, a mixing time of 60 seconds leaves 2 to 3.5 minutes of working time for materials that set at 3.5 to 5 minutes. In both cases, the mixed alginate must be loaded into the tray and the impression made promptly.
Setting Time
Setting times range from 1 to 5 minutes. The ANSI/ADA (American National Standards Institute/American Dental Association) specification No. 18 (ISO [International Organization for Standardization] 1563) requires that it be at least that value listed by the manufacturer and at least 15 seconds longer than the stated working time. Lengthening the setting time is better accomplished by reducing the temperature of the water used with the mix than by reducing the proportion of powder. Reducing the ratio of powder to water reduces the strength and accuracy of the alginate. Selecting an alginate with a different setting time is a better alternative than changing the water/powder ratio.
The setting reaction is a typical chemical reaction, and the rate can be approximately doubled by a temperature increase of 10° C. However, using water that is cooler than 18° C or warmer than 24° C is not advisable. The clinical setting time is detected by a loss of surface tackiness. If possible, the impression should be left in place 2 to 3 minutes after the loss of tackiness, because the tear strength and elastic recovery (recovery from deformation) increase significantly during this period.
Color-changing alginates provide a visual indication of working time and setting time. The mechanism of the color change is a pH-related change of a dye. One such alginate changes its color from light pink to white.
Elastic Recovery
A typical alginate impression is compressed about 10% in areas of undercuts during removal. The actual magnitude depends on the extent of the undercuts and the space between the tray and the teeth. The ANSI/ADA specification requires that the elastic recovery be more than 95% when the material is compressed 20% for 5 seconds at the time it would normally be removed from the mouth. As indicated in Table 12-2, a typical value for elastic recovery is 98.2%. The corresponding permanent deformation is 1.8%.
The permanent deformation, indicated as percent compression set, is a function of percent compression, time under compression, and time after removal of the compressive load, as illustrated in Figure 12-4. Note that permanent deformation is a time-dependent property. Lower permanent deformation (higher elastic recovery) occurs (1) when the percent compression is lower, (2) when the impression is under compression a shorter time, and (3) when the recovery time is longer, up to about 8 minutes after the release of the load. Clinically these factors translate into requirements for a reasonable bulk of alginate between the tray and the teeth, appropriate retention of the alginate in the tray, and a rapid removal of the impression from the mouth. The usual procedures followed to disinfect the impression and produce a gypsum model provide adequate time for any recovery that might occur.
Flexibility
The ANSI/ADA specification permits a range of 5% to 20% at a stress of 0.1 MPa, and most alginates have a typical value of 14%. However, some of the hard-set materials have values from 5% to 8%. A reasonable amount of flexibility is required for ease of removal of the impression.
Strength
The compressive and tear strengths of alginates are listed in Table 12-2. Both properties are time dependent, with higher values obtained at higher rates of loading. Compressive strengths range from approximately 0.5 to 0.9 MPa. The ANSI/ADA specification requires that certified products have a compressive strength of at least 0.35 MPa. Tear strengths vary from 0.4 to 0.7 kN/m, and this property is probably more important than the compressive strength. The tear strength is a measure of the force/thickness ratio needed to initiate and continue tearing and is often determined on a specimen of the shape shown in Figure 12-5. Tearing occurs in the thin sections of the impression, and the probability of tearing decreases with increasing rates of removal. The effect of loading rate on the tear strength of several alginates is shown in Figure 12-6. Values for tray materials range from 0.38 to 0.48 N/mm at 20 mm/min to 0.6 to 0.7 N/mm at 500 mm/min. The lower tear strength at corresponding rates for the syringe materials reflects the decreased alginate in the syringe material.
Compatibility with Gypsum
The selection of an alginate-gypsum combination that produces good surface quality and detail is highly important. The surface quality and ability of alginate-gypsum combinations to reproduce fine V-shaped grooves are shown in Figure 12-7, A and B. A type III model plaster was poured against an alginate in Figure 12-7, A, and type IV dental stone was poured against the same alginate in Figure 12-7, B. The finest groove was 0.025 mm wide in each instance. The combination in Figure 12-7, B, was not as compatible as the one in Figure 12-7, A, with respect to either surface quality or detail. For purposes of comparison, in Figure 12-7, C, the same type IV dental stone used in Figure 12-7, B, was poured against a polysulfide impression.
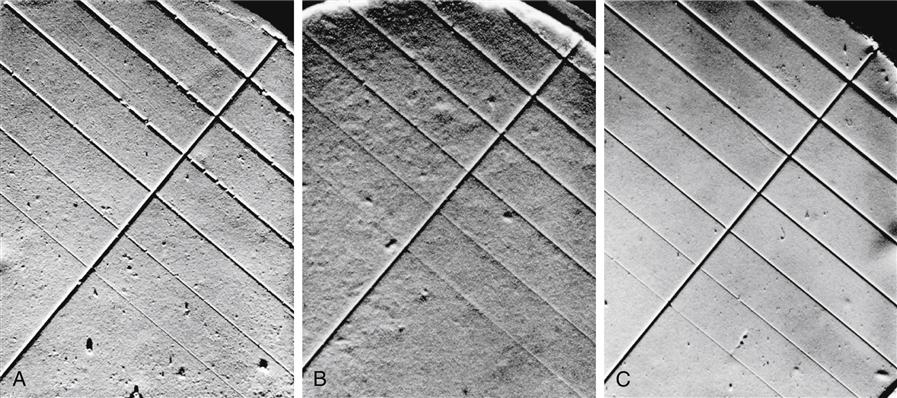
A, Model plaster poured against alginate; B, dental stone poured against the same alginate; and C, the same dental stone poured against polysulfide. It should be emphasized that another alginate with the same plaster and stone could yield opposite results. (From Craig RG, MacPherson GW: University of Michigan School of Dentistry, Ann Arbor, 1965.)
The impression must be rinsed well in cold water to remove saliva and any blood, and then disinfected. Next, all free surface water should be removed before preparing a gypsum model. Saliva and blood interfere with the setting of gypsum, and if free water accumulates, it tends to collect in the deeper parts of the impression and dilute the gypsum model material, yielding a soft, chalky surface. The excess surface water has been removed when the reflective surface becomes dull. If the alginate impression is stored for 30 minutes or more before preparing the model, it should be rinsed with cool water to remove any exudate on the surface caused by syneresis of the alginate gel; exudate will retard the setting of the gypsum. Thereafter, it should be wrapped loosely in a moist paper towel and sealed in a plastic bag to avoid moisture loss.
The set gypsum model should not remain in contact with the alginate impression for periods of several hours because contact of the slightly soluble calcium sulfate dihydrate with the alginate gel containing a great deal of water is detrimental to the surface quality of the model.
Dimensional Stability
Alginate impressions lose water by evaporation and shrink when standing in air. Impressions left on the bench for as short a time as 30 minutes may become inaccurate enough to require remaking the impression. Even if the impression stored for more than 30 minutes in air were immersed in water, it would not be feasible to determine when the correct amount of water had been absorbed, and in any case the previous dimensions would not be reproduced. For maximum accuracy, the model material should be poured into the alginate impression as soon as possible. If for some reason the models cannot be prepared directly, the impressions should be stored in 100% relative humidity in a plastic bag or wrapped in a damp (but not wringing-wet) paper towel. There is a greater chance for distortion the longer the impression is stored (Figure 12-8). New alginates have improved long-term storage ranging from 48 to 120 hours when stored in a plastic bag. Now, orthodontists routinely send alginate impressions to companies that offer digital fabrication of appliances.
Disinfection
Disinfection of impressions is a concern with respect to viral diseases such as hepatitis B, acquired immunodeficiency syndrome, and herpes simplex, because the viruses may be transferred to gypsum models and present a risk to dental laboratory and operating personnel.
All alginate impressions should be disinfected before pouring with gypsum to form a cast. The most common form of disinfection is spraying, but studies have shown that such impressions can be immersed in disinfectant also. The effect of disinfection in 1% sodium hypochlorite or 2% potentiated glutaraldehyde solutions on accuracy and surface quality has been measured after 10- to 30-minute immersion. Statistically significant dimensional changes were observed; however, the changes were on the order of 0.1% and the quality of the surface was not impaired. Such changes would be insignificant for clinical applications such as the preparation of study models and working casts. In another study, immersion disinfection of alginates demonstrated little effect on accuracy and surface quality, but it was shown that one alginate product was best immersed in iodophor and another brand in glyoxal glutaraldehyde. The effect of disinfection on agar impression materials has not been reported, but considering the similarity of the two hydrocolloids, similar recommendations are reasonable.
Elastomeric Impression Materials
Four types of synthetic elastomeric impression materials are available to record dental impressions: polysulfides, condensation silicones, addition silicones (polyvinylsiloxanes), and polyethers. Polysulfides were the first synthetic elastomeric impression material introduced (1950). Condensation silicones were made available to dentists in 1955, polyether in 1965, and addition silicones in 1975. Polysulfide and condensation silicone impression materials are described on the website. Polyvinylsiloxanes and polyethers form the vast majority of elastomeric impressions used worldwide today. Changes in recent years have provided greater choice of consistency and new mixing techniques. http://evolve.elsevier.com/sakaguchi/restorative
Consistencies
Elastomeric impression materials are typically supplied in several consistencies (viscosities) to accommodate a range of impression techniques. Addition silicones are available: extra-low, low (syringe or wash), medium (regular), monophase, high (tray), and putty (extra-high) consistencies. Polyether impression materials are now available in low, medium, and high consistencies.
Mixing Systems
Two types of systems are available to mix the catalyst and base thoroughly before taking the impression: static automixing and dynamic mechanical mixing A very popular means of mixing the catalyst and base is with a so-called automixing system. The base and catalyst are in separate cylinders of the plastic cartridge. The cartridge is placed in a mixing gun containing two plungers that are advanced by a ratchet mechanism to extrude equal quantities of base and catalyst. The base and catalyst are forced through the static-mixing tip containing a stationary plastic internal spiral; the two components are folded over each other many times as they are pushed through the spiral, resulting in a uniform mix at the tip end. Because one cylinder may be filled slightly more that the other, the first part of the mix from a new cartridge should be discarded.
The mixed material can be extruded directly into an injection syringe or into the impression tray. Intraoral delivery tips can be placed on the end of the static mixing tip, and the mixed material can be injected into and around the cavity preparation. The tip can be removed, and additional mixed material can be extruded into the impression tray. The automixing systems have been shown to result in mixes with many fewer voids than hand mixes. Although for each mix the material left in the mixing tip is wasted, the average loss is only 1 to 2 mL, depending on the manufacturer’s tip, whereas three to four times this much is wasted in a hand mix as a result of overestimating the amount needed. Initially, automixing was used for low consistencies, but new designs of guns and mixing tips allow all consistencies except putty to be used with this system. Addition silicones and polyethers are available with this means of mixing.
The second and newest system is a dynamic, mechanical mixer, illustrated in Figure 12-9. The catalyst and base are supplied in large plastic bags housed in a cartridge, which is inserted into the top of the mixing machine. A new, plastic mixing tip is placed on the front of the machine, and when the button is depressed, parallel plungers push against the collapsible plastic bags, thereby opening the bags and forcing material into the dynamic mixing tip. This mixing tip differs from automixing in that the internal spiral is motor driven so it rotates. Thus mixing is accomplished by this rotation plus forward motion of the material through the spiral. In this manner, thorough mixing can be ensured and higher viscosity material can be mixed with ease. The advantage of this system is ease of use, speed, and thoroughness of mixing, but more must be invested in the purchase of the system compared with hand and automixing. In addition, there is slightly more material retained in the mixing tip than with automixing, but less than that wasted when mixed by hand. Polyether and addition silicone impression materials are available for mixing with this system.
One variation in mixing is with the addition silicone two-putty systems mixed by hand. Scoops are supplied by the manufacturer for dispensing, and the putties are most often kneaded with fingers until free from streaks. The putty materials that have a liquid catalyst are initially mixed with a spatula until the catalyst is reasonably incorporated, and mixing is completed by hand. It should be noted that latex gloves may interfere with setting of addition silicone impression materials, as discussed later.
Impression Techniques
Three common methods for making impressions for fixed restorations are a simultaneous, dual-viscosity technique, a single-viscosity or monophase technique, and a putty-wash technique. In nearly all cases, impression material is injected directly on and into the prepared teeth and a tray containing the bulk of the impression material is placed thereafter. After the impression is set, the tray is removed.
The simultaneous, dual-viscosity technique is one in which low-consistency material is injected with a syringe into critical areas and the high-consistency material is mixed and placed in an impression tray. After injecting the low-viscosity material, the tray containing the higher-viscosity material is placed in the mouth. In this manner, the more viscous tray impression material forces the lower-viscosity material to flow into fine aspects of the areas of interest. Because they are both mixed at nearly the same time, the materials join, bond, and set together. After the materials have set, the tray and the impression are removed. An example of an impression using this procedure is shown in Figure 12-10.
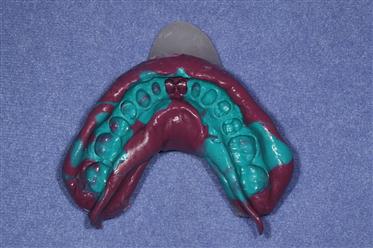
Turquoise material is of a low or injection consistency, and maroon material of a high or tray consistency. (Courtesy of Dr. Charles Mark Malloy, Portland, OR.)
In the single-viscosity or monophase technique, impressions are often taken with a medium-viscosity impression material. Addition silicone and polyether impression materials are well suited for this technique because both have a capacity for shear thinning. As described in Chapter 4, pseudoplastic materials demonstrate a decreased viscosity when subjected to high shear rates such as occurs during mixing and syringing. When the medium viscosity material is forced through an impression syringe, the viscosity is reduced, whereas the viscosity of the same material residing in the tray is unaffected. In this manner, such materials can be used for syringing and for trays, as previously described for the simultaneous, dual-viscosity technique. The mechanism for shear thinning is discussed in the later section on the viscosity of impression materials.
The putty-wash technique is a two-step impression procedure whereby a preliminary impression is taken in high- or putty-consistency material before the cavity preparation is made. Space is provided for a low-consistency material by a variety of techniques, and after cavity preparation, a low-consistency material is syringed into the area and the preliminary impression reinserted. The low- and high-consistency materials bond, and after the low-consistency material sets, the impression is removed. This procedure is sometimes called a wash technique. The putty-consistency material and this technique were developed for condensation silicones to minimize the effects of dimensional change during polymerization. Most of the shrinkage during polymerization takes place in the putty material when the preliminary impression is made, confining final shrinkage to the thin wash portion of the impression. Care must be taken so the wash material can freely escape via vents in the putty material when the wash impression is made. If not, the wash material can compress the putty in the second-stage impression, inducing permanent distortion and inaccuracies to the impression. The putty-wash technique was extended to addition silicones after their introduction, even though their polymerization shrinkage is significantly lower.
Manufacturers add coloring agents to the accelerator or base as an aid in determining the thoroughness of the mix. Normally a different color is used for each consistency of a particular product line so one can distinguish the wash (low) consistency from the tray consistency in the set impression. Retarders may be added as well to control working and setting time of the products.
Composition and Reactions
The next two sections describe the general composition and setting reactions of addition silicone and polyether impression materials. The following section describes their physical properties, permitting a more direct comparison of the various types and their properties.
Addition Silicone
Addition silicone is available in extra low, low, medium, heavy, and very heavy (putty) consistencies. A representative product line of addition silicones is shown in Figure 12-11. The base paste of this class of impression materials contains a moderately low-molecular-weight polymer (polymethylhydrosiloxane) with more than 3 and up to 10 pendant or terminal hydrosilane groups per molecule (see formulas below and addition silicone formula 1 [AS1]). The base also contains filler.
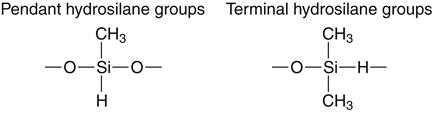
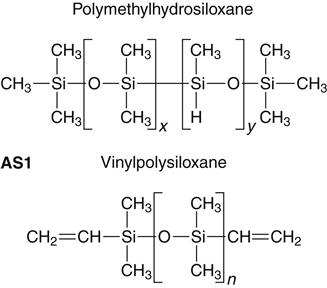
The accelerator (catalyst) and the base paste contain a dimethylsiloxane polymer with vinyl terminal groups, plus filler. The accelerator also contains a platinum catalyst of the so-called Karstedt type, which is a complex compound consisting of platinum and 1,3-divinyltetramethyldisiloxane. Unlike the condensation type, the addition reaction does not normally produce a low-molecular-weight byproduct, as indicated in the reaction shown below (AS2).
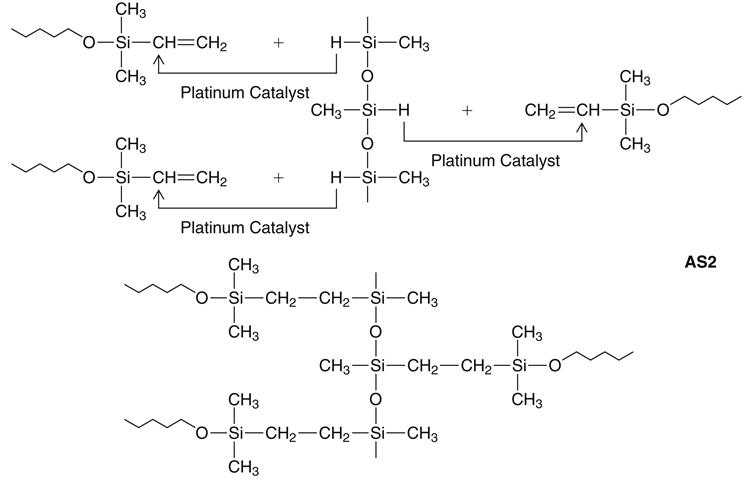
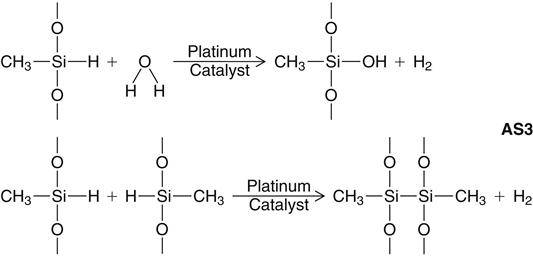
A secondary reaction can occur, however, with the production of hydrogen gas if —OH groups are present. The most important source of —OH groups is water (H—OH), the reaction of which under consumption of Si—H-units is illustrated above (AS3). Another possible source of hydrogen gas is a side reaction of the Si—H units of the polymethylhydrosiloxane with each other, under the influence of the platinum catalyst, also shown above (AS3).
Not all addition silicone impression materials release hydrogen gas, and because it is not known which do, it is recommended that one wait at least 30 minutes for the setting reaction to be completed before the gypsum models and dies are poured. Epoxy dies should not be poured until the impression has stood overnight. The difference in the delay with gypsum and epoxy is that gypsum products have much shorter setting times than epoxy die materials. Some products contain a hydrogen absorber such as palladium, and gypsum and epoxy die materials can be poured against them as soon as practical. Examples of high-strength stone poured after 15 minutes against addition silicone, with and without a hydrogen absorber, are shown in Figure 12-12.
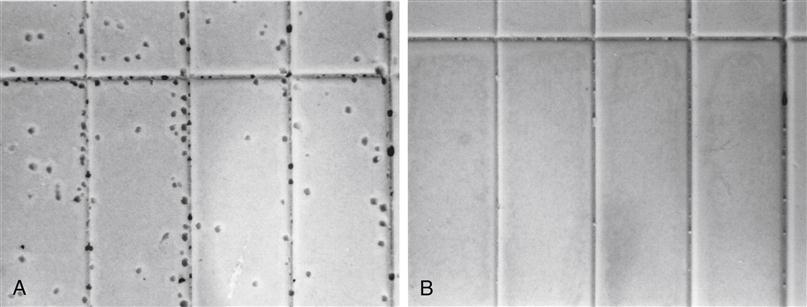
A, Bubbles are caused by the release of hydrogen. B, No bubbles are apparent because palladium hydrogen absorber is included in the impression material.
Latex gloves have been shown to adversely affect the setting of addition silicone impressions. Sulfur compounds that are used in the vulcanization of latex rubber gloves can migrate to the surface of stored gloves. These compounds can be transferred onto the prepared teeth and adjacent soft tissues during tooth preparation and when placing tissue retraction cord. They can also be incorporated directly into the impression material when mixing two putties by hand. These compounds can poison

the platinum-containing catalyst, which results in retarded or no polymerization in the contaminated area of the impression. Thorough washing of the gloves with detergent and water just before mixing sometimes minimizes this effect, and some brands of gloves interfere with the setting more than others. Vinyl and nitrile gloves do not have such an effect. Residual monomer in acrylic provisional restorations and resin composite cores has a similar inhibiting effect on the set of addition silicone materials. The preparation and adjacent soft tissues can also be cleaned with 2% chlorhexidine to remove contaminants.
Polyether
Polyethers are supplied in low-, medium-, and heavy-body consistency. The base paste consists of a long-chain polyether copolymer with alternating oxygen atoms and methylene groups (O—[CH2]n) and reactive terminal groups (see polyether 1 [PE1]). Also incorporated are a silica filler, compatible plasticizers of a nonphthalate type, and triglycerides. In the catalyst paste, the former 2,5-dichlorobenzene sulfonate was replaced by an aliphatic cationic starter as a cross-linking agent. The catalyst also includes silica filler and plasticizers. Coloring agents are added to base and catalyst to aid in the recognition of different material types. Examples of polyether impression materials are shown in Figure 12-9.
The reaction mechanism is shown (PE2) in a simplified form. The elastomer is formed by cationic polymerization by opening of the reactive terminal rings. The backbone of the polymer is believed to be
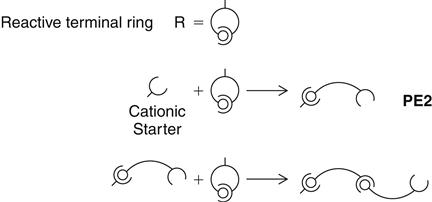
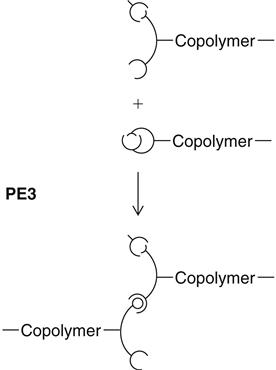
a copolymer of ethylene oxide and tetramethylene oxide units. The reactive terminal rings open under the influence of the cationic initiator of the catalyst paste and can then, as a cation itself, attack and open additional rings. Whenever a ring is opened, the cation function remains attached, thus lengthening the chain (see PE3). Because of the identical chemical base, all polyether consistencies can be freely combined with each other. A chemical bond between all materials develops during curing.
Setting Properties
Typical values of the setting properties of elastomeric impression materials are presented in Table 12-3. The temperature rise in typical mixes of impression materials was pointed out in the previous section, but Table 12-3 illustrates that the temperature rise is small and of no clinical concern.
TABLE 12.3
Setting Properties of Elastomeric Impression Materials
< ?comst?>
Material | Consistency | Temperature Rise (° C) | Viscosity 45 sec after Mixing (cp) | Working Time (min) | Setting Time (min) | Dimensional Change at 24 hr (%) |
POLYSULFIDES | ||||||
Low | 3.4 | 60,000 | 4-7 | 7-10 | −0.40 | |
Medium | 110,000 | 3-6 | 6-8 | −0.45 | ||
High | 450,000 | 3-6 | 6-8 | −0.44 | ||
SILICONES | ||||||
Condensation | Low | 1.1 | 70,000 | 2.5-4 | 6-8 | −0.60 |
Very high | 2-2.5 | 3-6 | −0.38 | |||
Addition | Low | 2-4 | 4-6.5 | −0.15 | ||
Medium | 150,000 | 2-4 | 4-6.5 | −0.17 | ||
High | 2.5-4 | 4-6.5 | −0.15 | |||
Very high | 1-4 | 3-5 | −0.14 | |||
POLYETHERS | ||||||
Low | 4.2 | 3 | 6 | −0.23 | ||
Medium | 130,000 | 2.5-3 | 6 | −0.24 | ||
High | 2.5 | 5.5 | −0.19 |
< ?comen?>< ?comst1?>
< ?comst1?>
< ?comen1?>
Viscosity
The viscosity of materials 45 seconds after mixing is listed in Table 12-3. As expected, the viscosity increases for the same type of material from low to high consistencies. Viscosity is a function of time after the start of mixing.
A shearing force can affect the viscosity of polyether and addition silicone impression materials, as was mentioned in the section on impression techniques. This effect is called shear thinning or pseudoplasticity. For impression materials possessing this characteristic, the viscosity of the unset material diminishes with an increasing outside force or shearing speed. When the influence is discontinued, the viscosity immediately increases. This property is very important for the use of monophase impression materials, and is illustrated for polyether in Figure 12-13. In the case of polyether, shear-thinning properties are influenced by a weak network of triglyceride crystals. The crystals align when the impression material is sheared, as occurs when mixed or flowing through a syringe tip. The microcrystalline triglyceride network ensures that the polyether remains viscous in the tray or on the tooth but flows under pressure. This allows a single or monophase material to be used as a low- and medium-consistency material. Cooling of the pastes results in substantial viscosity increase. Before using, pastes have to be brought to room temperature.
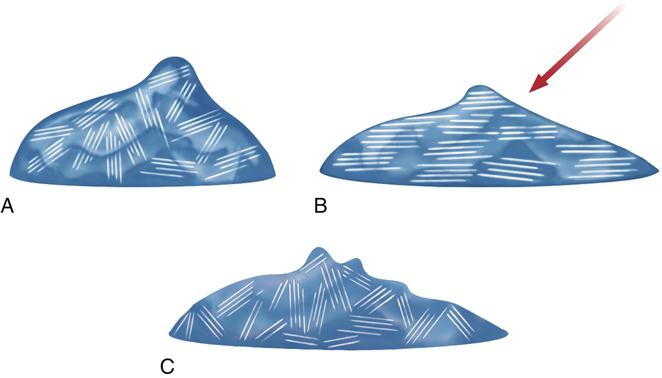
The trigliceride network, A, within the impression material aligns when sheared as with syringing, and B, to achieve a lower viscosity. Once the shear force is removed, the viscosity increases with randomization of the triglyceride network, C.
The effect of shear rate (rotational speed of the viscometer) on the viscosity of single-consistency (monophase) addition silicones is shown in Figure 12-14. Although all products showed a decrease in viscosity with increasing shear rate, the effect was much more pronounced for two products, Ba and Hy, with about an eightfold to eleven-fold decrease from the lowest to the highest shear rate. The substantial decrease in viscosity at high shear stress, which is comparable with the decrease during syringing, permits the use of a single mix of material, with a portion to be used as syringe material and another portion to be used as tray material in the syringe-tray technique.
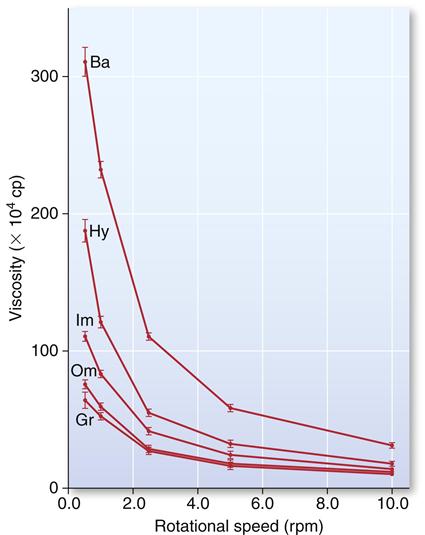
A rotational speed of 0.5 rpm would represent a shear rate comparable with that observed when placing the material in a tray, and a speed of 10 rpm would represent a shear rate comparable with that experienced when syringing the material. (Data from Kim KN, Craig RG, Koran A III: J. Prosthet. Dent. 67,794, 1992.)
Working and Setting Times
The working and setting times of addition silicone and polyether impression materials are listed in Table 12-3. In general, for a given class of elastomeric impression materials by a specific manufacturer, the working and setting times decrease as the viscosity increases from low to high. Polyethers show a clearly defined working time with a sharp transition into the setting phase. This behavior is often called snap-set. This transition from plastic condition into elastic properties is rather short compared with older addition silicones, which was shown in investigations of rheological properties of setting materials (Figure 12-15).
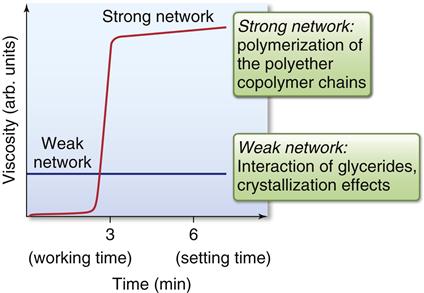
The initial viscosity of the unset material is influenced by the structural triglycerides, whereas the polymerization of copolymer chains thereafter provides the quick increase in viscosity as the material sets.
Note that the working and setting times of the elastomeric impression materials are shortened by increases in temperature and humidity; on hot, humid days this effect should be considered in the clinical application of these materials.
The initial (or working) and final setting times can be determined fairly accurately by using a penetrometer with a needle and weight selected to suit these materials. The Vicat penetrometer, as shown in Figure 12-16, with a 3-mm diameter needle and a total weight of 300 g, has been used by a number of investigators. A metal ring, 8 mm high and 16 mm in diameter, is filled with freshly mixed material and placed on the penetrometer base. The needle is applied to the surface of the impression material for 10 seconds, and a reading is taken. This is repeated every 30 seconds. The initial set is that time at which the needle no longer completely penetrates the specimen to the bottom of the ring. The final set is the time of the first of three identical nonmaximum penetration readings. When the material has set, the elasticity still allows penetration of the needle, but it is the same at each application.
Dimensional Change on Setting
The impression material undergoes a dimensional change on setting. The major factor for contraction during setting is cross-linking and rearrangement of bonds within and between polymer chains. Impressions can expand if water sorption takes place and an impression can be distorted if seated after the material has set to any degree. Finally, distortion or creep will occur if the material does not recover elastically when the set impression is removed from undercuts. Imbibition is discussed in the section on disinfecting impressions, and creep-induced distortion is discussed under elastic recovery.
Addition silicone and polyether impression materials undergo shrinkage due to polymerization. The linear dimensional change between a die and the impression after 24 hours is listed in Table 12-3. The addition silicones have the smallest change, about −0.15%, followed by the polyethers at about −0.2%. The contraction is low for these two products because there is no loss of byproducts.
The rate of shrinkage of elastomeric impression materials is not uniform during the 24 hours after removal from the mouth. In general, about half the shrinkage observed at 24 hours occurs during the first hour after removal; for greatest accuracy, therefore, the models and dies should be prepared promptly, although in air the elastomeric impression materials are much more stable than hydrocolloid products.
Mechanical Properties
Typical mechanical properties of elastomeric impression materials are listed in Table 12-4. The permanent deformation (in the current specification, elastic recovery, which is 100% minus the permanent deformation), strain in compression, and dimensional change are properties used in ANSI/ADA specification No. 19 (ISO 4823) to classify elastomeric impression materials as low, medium, high, or very high viscosity types. The requirements for these properties are given in Table 12-5. Further requirements of the specification for elastomeric impression materials are indicated in Table 12-6. The consistency diameter is used to classify viscosity by measuring the diameter of the disk formed when 0.5 mL of mixed material is subjected to a 5.6-N weight at 1.5 minutes after mixing for 12 minutes. Because the setting times of elastomeric impression materials vary, the consistency diameter is affected not only by the viscosity but also by the setting time. The classification of a material by the consistency diameter may be different from that by a true viscosity measurement.
TABLE 12.4
Mechanical Properties of Elastomeric Impression Materials
< ?comst?>
Material | Consistency | Permanent Deformation∗ (%) | Strain in Compression (%) | Flow (%) | Shore A Hardness | Tear Strength (kN/m) |
POLYSULFIDES | ||||||
Low | 3-4 | 14-17 | 0.5-2 | 20 | 2.5-7.0 | |
Medium | 3-5 | 11-15 | 0.5-1 | 30 | 3.0-7.0 | |
High | 3-6 | 9-12 | 0.5-1 | 35 | — | |
SILICONES | ||||||
Condensation | Low | 1-2 | 4-9 | 0.05-0.1 | 15-30 | 2.3-2.6 |
Very high | 2-3 | 2-5 | 0.02-0.05 | 50-65 | — | |
Addition | Low | 0.05-0.4 | 3-6 | 0.01-0.03 | 35-55 | 1.5-3.0 |
Medium | 0.05-0.3 | 2-5 | 0.01-0.03 | 50-60 | 2.2-3.5 | |
High | 0.1-0.3 | 2-3 | 0.01-0.03 | 60-70 | 2.5-4.3 | |
Very high | 0.2-0.5 | 1-2 | 0.01-0.1 | 50-75 | — | |
POLYETHERS | ||||||
Low | 1.5 | 3 | 0.03 | 35-40 | 1.8 | |
Medium | 1-2 | 2-3 | 0.02 | 40-60 | 2.8-4.8 | |
High | 2 | 3 | 0.02 | 40-50 | 3.0 |
< ?comen?>< ?comst1?>
< ?comst1?>
< ?comen1?>
< ?comst1?>< ?comen1?>∗< ?comst1?>< ?comen1?>Elastic recovery from deformation is 100% minus the percent permanent deformation.
TABLE 12.5
< ?comst?>
Viscosity Type | Minimum Elastic Recovery (%) | Strain in Compression (%) | ||
Minimum | Maximum | Maximum Dimensional Change in 24 Hours (%) | ||
Low | 96.5 | 2.0 | 20 | 1.5 |
Medium | 96.5 | 2.0 | 20 | 1.5 |
High | 96.5 | 0.8 | 20 | 1.5 |
Very high | 96.5 | 0.8 | 20 | 1.5 |
< ?comen?>< ?comst1?>
< ?comst1?>
< ?comen1?>
TABLE 12.6
< ?comst?>
Viscosity | Maximum Mixing Time (min) | Minimum Working Time (min) | Diameter of Consistency Disk (mm) | Reproduction of Detail | ||
Minimum | Maximum | Line Width in Impression (mm) | Line Width in Gypsum (mm) | |||
Low | 1 | 2 | 36 | — | 0.020 | 0.020 |
Medium | 1 | 2 | 31 | 41 | 0.020 | 0.020 |
High | 1 | 2 | — | 35 | 0.050 | 0.050 |
Very High | 1 | 2 | — | 35 | 0.075 | 0.075 |
< ?comen?>< ?comst1?>
< ?comst1?>
< ?comen1?>
Elastic Recovery
The order in which the permanent deformation of the elastomeric impression materials is listed in Table 12-4 demonstrates that addition silicones have the best elastic recovery during removal from the mouth, followed by polyethers. A material with a permanent deformation of 1% has an elastic recovery of 99%.
Strain in Compression
The strain in compression under a stress of 0.1 MPa is a measure of the flexibility of the material. Table 12-4 illustrates that, in general, the low-consistency materials of each type are more flexible than the high-consistency elastomeric impressions. For a given consistency, polyethers are generally the stiffest, followed by addition silicones.
Flow
Flow is measured on a cylindrical specimen 1 hour old, and the percent flow is determined 15 minutes after a load of 1 N is applied. As seen in Table 12-4, silicones and polyethers have low values of flow.
Typical elastomeric impression materials apparently have no difficulty meeting the mechanical property requirements of ANSI/ADA specification No. 19 (see Table 12-6). Although the flow, hardness, and the tear strengths of elastomeric impression materials are not mentioned in the specification, these are important properties; they are also listed in Table 12-4.
Hardness
The Shore A hardness increases from low to high consistency. When two numbers are given, the first represents the hardness 1.5 minutes after removal from the mouth, and the second number is the hardness after 2 hours. The low-, medium-, and high-viscosity addition silicones do not change hardness significantly with time, whereas the hardness of polyethers does increase with time. In addition, the hardness and strain in compression affect the force necessary to remove the impression from the mouth. Low flexibility and high hardness can be compensated for clinically by producing more space for the impression material between the tray and the teeth. This can be accomplished with additional block-out for custom trays or by selecting a larger tray when using disposable trays.
A new variation in polyether provides less resistance to deformation during removal of the impression from the mouth and the gypsum cast from the impression. To achieve this, the filler content was reduced from 14 to 6 parts per unit, thereby reducing the Shore A hardness from 46 to 40 after 15 minutes, and from 61 to 50 after 24 hours. The ratio of high-viscous softener to low-viscous softener was changed to achieve a consistency similar to that of the conventional monophase polyether.
Tear Strength
Tear strength is important because it indicates the ability of a material to withstand tearing in thin interproximal areas and margins of periodontally involved teeth. The tear strengths listed in Table 12-4 are a measure of the force needed to initiate and continue tearing a specimen of unit thickness. As the consistency of the impression type increases, tear strength undergoes a small increase, but most of the values are between 2.0 and 3.9 kN/m. Values for very high consistency types are not listed because this property is not important for these materials. Higher tear strengths for elastomeric impression materials are desirable, but compared with the values for hydrocolloid impression materials of 0.3 to 0.7 kN/m, they are a major improvement.
Creep Compliance
Elastomeric impression materials are viscoelastic, and their mechanical properties are time dependent. For example, the higher the rate of deformation, the higher the tear strength; and the longer the impressions are deformed, the higher the permanent deformation. As a result, plots of creep compliance versus time describe the properties of these materials better than stress-strain curves. Creep-compliance time curves for low-consistency polysulfide, condensation silicone, addition silicone, and medium-consistency polyether are shown in Figure 12-17. The initial creep compliance illustrates polysulfide is the most flexible and polyether is the least flexible. The flatness or parallelism of the curves with respect to the time axis indicates low permanent deformation and excellent recovery from deformation during the removal of an impression material; addition silicones and polyethers have the best elastic recovery.
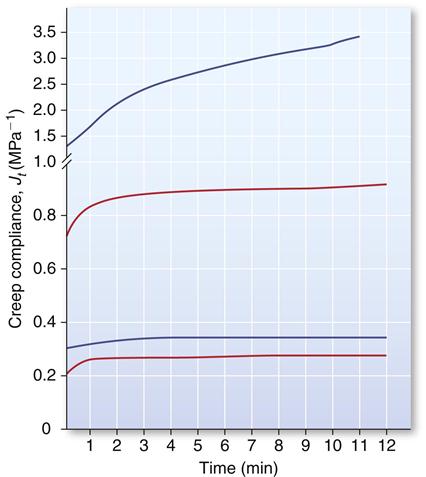
Curves from top to bottom: polysulfide, condensation silicone, addition silicone, and polyether. (Data from Craig RG: J. Mich. Dent. Assoc. 59, 259, 1977.)
The recoverable viscoelastic quality of the materials is indicated by differences between the initial creep compliance and the creep compliance value obtained by extrapolation of the linear portion of the curve to zero time. As a result, addition silicones have the lowest viscoelastic quality and require less time to recover viscoelastic deformation, followed by the polyethers.
Detail Reproduction
The requirements of elastomeric impression materials are listed in Table 12-6. Except for the very high-viscosity products, all should reproduce a V-shaped groove and a 0.02-mm wide line in the elastomeric. The impression should be compatible with gypsum products so the 0.02-mm line is transferred to gypsum die materials. Low-, medium-, and high-viscosity elastomeric impression materials have little difficulty meeting this requirement.
Wettability and Hydrophilization of Elastomeric Impression Materials
Wettability may be assessed by measuring the advancing contact angle of water on the surface of the set impression material or by using a tensiometer to measure forces as the material is immersed and removed (Wilhelmy technique). The advancing contact angles for elastomeric impression materials are listed in Table 12-7. Of all the impression materials discussed in this chapter, only alginates/>
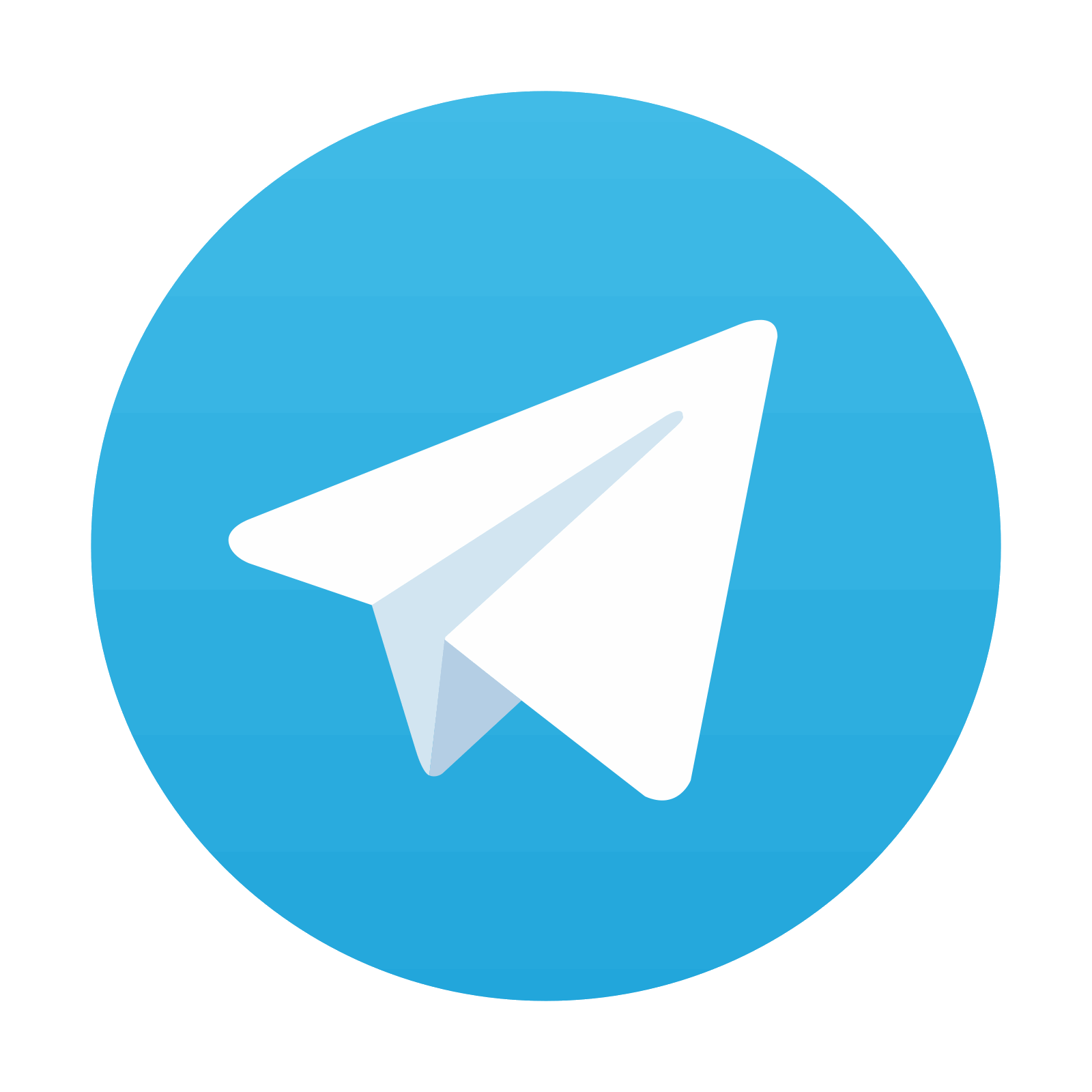
Stay updated, free dental videos. Join our Telegram channel

VIDEdental - Online dental courses
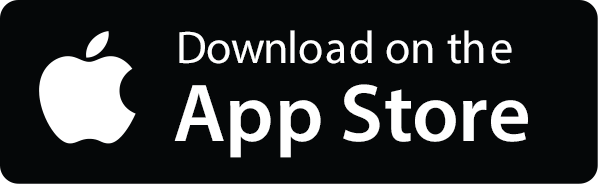
