Chapter 11 Polishing
Section A Current Technology and Clinical Approaches to Polishing of Dental Restorations
Relevance to Esthetic Dentistry
1. Removes restorative marginal excess and refines the margins of the restoration
2. Reduces the risk of fracture, because a rough surface is more likely to fracture
3. Reduces surface imperfections, hence diminishing surface area and the risk of surface breakdown and corrosion
4. Produces a smooth surface that is less likely to retain plaque
5. Improves oral function and mastication, because food slides more easily over polished tooth surfaces
6. Produces smooth surfaces that facilitate oral hygiene procedures, allowing access to all surfaces, marginal areas, and interproximal areas with normal toothbrushing and use of dental floss
7. Produces smooth restoration contacts, leading to less wear on opposing and adjacent teeth
8. Yields a more esthetic, naturally light-reflecting restoration
Brief History of Clinical Development and Evolution of the Procedure
Most dental finishing and polishing devices operate in the two-body mode, a harder material abrading a softer material. Nevertheless, dentist, hygienists, and laboratory technicians often use loose abrasives, that is, the “three-body abrasive mode,” in the form of prophy or polishing pastes. A three-body abrasive wear situation exists when loose particles move in the interface between the specimen surface and the polishing application device. Such a situation occurs when abrasives are intentionally deposited to roll on the surface of the polishing substrate. A three-body mode may also occur when small pieces of material are detached from the specimen to be polished and become trapped, or circulate, within the contact between the two first bodies. Figure 11-1 further illustrates how the various dental finishing and polishing procedures fall within these two basic tribologic mechanisms.
Clinical Considerations
Indications
Finishing and polishing in restorative dentistry, as illustrated in Figure 11-2, involve the steps of (1) performing gross contouring of the restoration to obtain the desired anatomy, (2) reducing and smoothing the surface roughness and scratches created by finishing instruments in the process of gross reduction and initial polishing, and (3) producing a highly smooth, light-reflective, enamel-like surface.
Material Options
Rubber Wheels, Cups, and Points
Rubber polishing instruments are used to finish, smooth, and/or polish composites. These finishing and polishing instruments are abrasive instruments based on fine or ultra-fine hard, abrasive particles dispersed and held in a softer, elastic matrix. The various configurations of these flexible or rubber finishers and polishers complement the access limitations of the coated abrasive disks for areas such as anterior lingual and posterior occlusal surfaces. Shapes, with varying sizes and dimensions, include disks, wheels, cups, and points. Figure 11-3 depicts the wide range of different types of bonded and elastomeric finishers and polishers available. They are often sold as kits with a variety of shapes and grits to accommodate the differing tooth dimensions and contours seen in clinical practice. Flexible, bonded-abrasive devices are made by molding abrasive particles, of varying particle size and size distribution, in an elastomeric matrix. The elastomeric matrix can be a natural or synthetic rubber, silicone, or other synthetic elastic polymer. One system uses a “urethane” elastic polymer in which a wide range of abrasive particles can be dispersed, including aluminum oxide and diamond.
Loose-Abrasive Polishing Pastes and Rotary Applicator Devices for Loose Abrasives
Loose-abrasive polishing pastes are used extensively in industrial and scientific applications. In the three-body, loose-abrasive polishing process, the loose-abrasive wear induces cutting and plowing on a micrometer and nanometer scale. Following the example from other industrial and scientific disciplines, dentists have used loose-abrasive finishing and polishing compositions for several decades. Loose-abrasive polishing pastes, used in dental applications, are predominantly based on dispersed and suspended ultra-fine aluminum oxide or diamond particles. Aluminum oxide polishing pastes are usually glycerin based, with a mean particle size distribution of 1 µm or less. Diamond polishing pastes also use a glycerin-based material but with a larger mean particle distribution—10 µm to less than 1 µm. Two diamond polishing pastes contain mean sizes of diamond particles on the order of 4 to 6 µm and less than 1 µm. In a study examining the surface morphology and smoothness of the transition from a glass-ceramic insert to a bonded composite resin interface, samples finished with a sequence of progressively smoother diamond abrasive finishing burs (45 µm, 25 µm, and 10 µm), followed by polishing with first a 4- to 6-µm–grit diamond polishing paste and then a sub-micron diamond polishing paste, exhibited the smoothest transition from composite resin to insert. Of perhaps equal importance, studies and research findings have indicated that the mode of application and the structure and the composition of the applicator device can be as important as the composition of the paste used in the polishing procedure. Although the commonly used method for applying polishing paste is the flexible rubber prophy cup, surface roughness data strongly suggest that such a mode of application results in increased surface roughness, or at best no improvement in surface smoothness. On the other hand, use of soft foam or felt applicators can significantly improve the efficacy of loose-abrasive polishing paste, especially those pastes containing aluminum oxide as the abrasive agent. Surface roughness decreased by 50% when a 1-µm aluminum oxide polishing paste was applied with a porous synthetic foam cup (Ra ≅ 0.10),* as compared with application of the same paste with a conventional rubber prophy cup (Ra ≅ 0.20).
Figure 11-4 depicts visually the wide range of types and sizes of both felt and foam polishing paste applicators that are best for loose-abrasive polishing of dental restorations. These applicators can be used with both aluminum oxide–based and diamond-based polishing pastes.
Controversies
1. Why do I need to polish the restoration, as after contouring and some intermediate finishing, the “wet” restoration looks esthetic?
2. Is a one-step polishing device approach truly effective and beneficial in all situations?
3. Why are polishing devices (rubber discs/cups/points and or polishing pastes) necessary? I often use them without much effect on the surface gloss of the restoration?
4. Are the fastest and easiest procedures the most beneficial?
Near-Future Developments
Recent New Technology in the Realm of Dental Finishing and Polishing
Abrasive-Impregnated Brushes and Felt Devices
Abrasive-impregnated, latch-type polishing brushes were introduced to the profession in the late 1990s. These polishing brushes are provided in several shapes (pointed; cup shaped), with various types of polymer “bristles” impregnated with different abrasive polishing particles. The brushes are intended to reach into the grooves, fissures, and interproximal areas of ceramic and resin composite restorations, areas that cannot be reached with other finishing or polishing devices without unintentionally removing anatomic grooves, fissures, and contours. Several of these brushes are depicted in Figure 11-5. Aschmann and colleagues (U.S. Patent 6,312,257) describe a “brush for surface treatments in restorative dentistry [that] comprises one or several lamellar abrasive elements.” Dubbe and colleagues (U.S. Patent 6,554,614) describe “a brush for a dental handpiece … wherein at least some of the bristles comprise an elastomeric material and a number of abrasive particles distributed throughout the elastomeric material.” The particulate abrasive used in the Sof-Lex Brush (3M ESPE, St Paul, Minnesota) is aluminum oxide.
Rotary Resin-Matrix Stain, Cement, and Composite Removing Devices
Several rotary devices based on a polymer or composite resin binder or matrix, with apparent “controlled” abrasivity, have recently been introduced to selectively remove surface-adherent restorative materials, including composite resin and residual cement (Figure 11-6). Among this new class of abrasive devices is Flashbuster (Danville Materials, San Ramon, California), a latch-type, rotary composite fiber bur that is claimed to remove residual composite with no damage to either enamel or porcelain. It can also remove residual orthodontic adhesive and stains from areas with limited access and can be used in periodontal root planing. The structure of the rod bur consists of fibers and particles embedded in a resin matrix. This yields a working surface that has continuous abrasive power.
Clinical Techniques
Clinical Step by Step
Step 1 (not shown): Using fine and micro-fine finishing diamonds and multi-fluted carbide, gross excess of the composite resin is removed, avoiding excessive contact with or damage to the enamel portion of the restoration margin. The marginal areas (and selected occlusal areas) of the class I composite restoration are carefully trimmed and finished using an aluminum oxide–containing bonded-abrasive finishing point or cup. The occlusion is checked and adjusted with fine and extra-fine diamonds, multi-fluted finishing burs, and the elastic bonded-abrasive finishing cups, points, and/or disks.
Step 2: Figure 11-7, A, illustrates an appropriate device for the optimal application of aluminum oxide polishing pastes—namely, a porous synthetic foam cup in a low-speed handpiece.
Step 3: Figure 11-7, B, illustrates the initial application of the 1-micron aluminum oxide polishing paste (Prisma Gloss, DENTSPLY Caulk). Note that the porous surface of the synthetic foam polishing cup eliminates the need to carry excess paste; the paste is carried in the surface porosities of the foam cup.
Step 4: Figure 11-7, C, illustrates the flexibility of the synthetic foam polishing cup to adapt to the contour of the occlusal surface during the application of the loose-abrasive polishing paste. A critical element in the polishing paste procedure is the rotary application of the polishing paste dry (without water) in a continuous motion over the surface of the restoration. Application times of 30 to 60 seconds ar/>
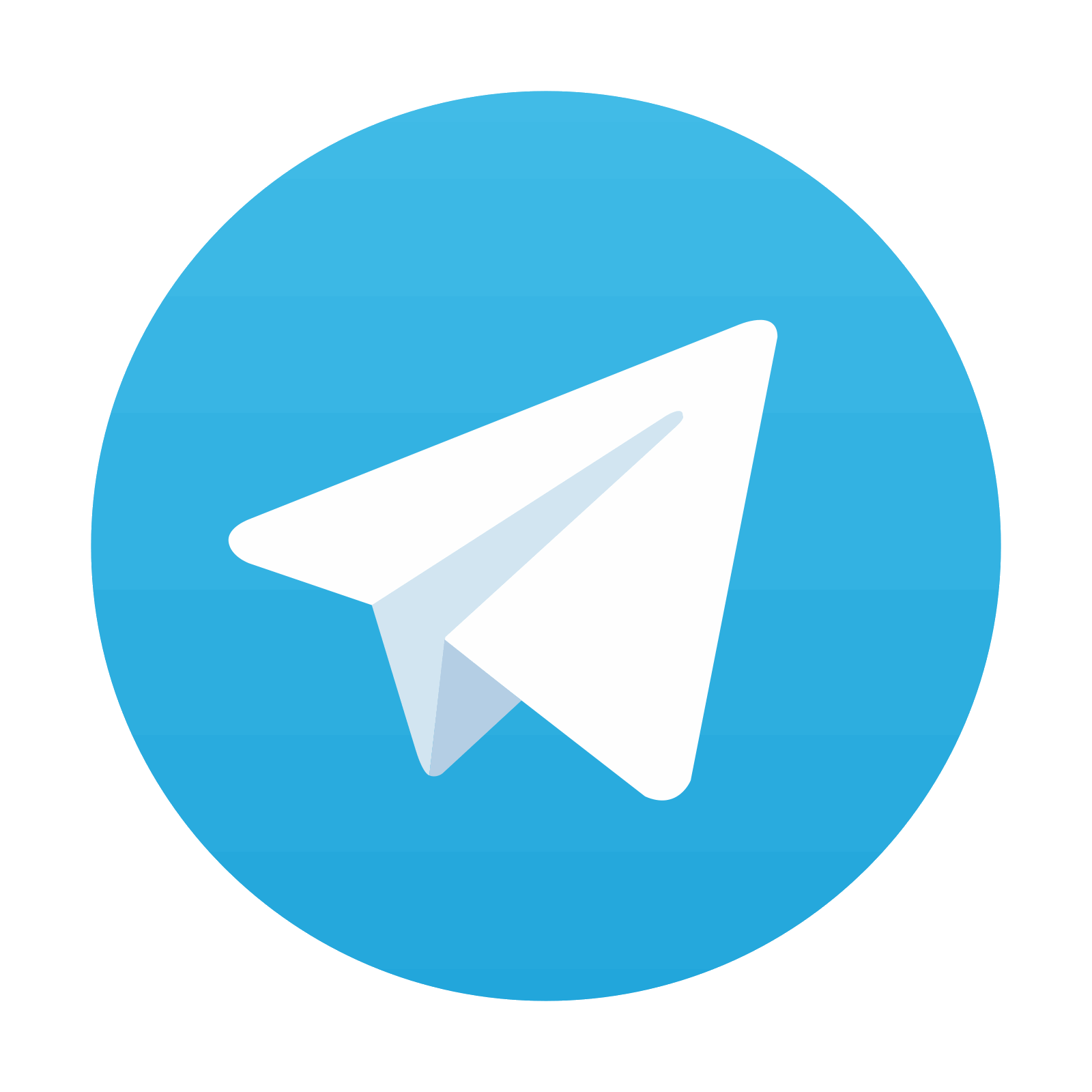
Stay updated, free dental videos. Join our Telegram channel

VIDEdental - Online dental courses
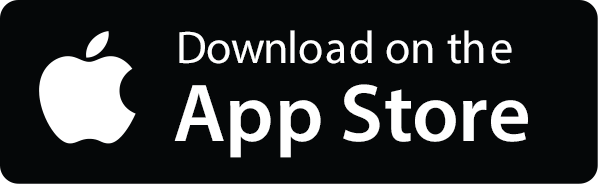
