Chapter 3
Gypsum Products for Dental Casts
3.1 Introduction
Gypsum is a naturally occurring, white powdery mineral with the chemical name calcium sulphate dihydrate (CaSQ4·2H2O). Gypsum products used in dentistry are based on calcium sulphate hemihydrate (CaSO42)2·H2O. Their main uses are for casts or models, dies and investments, the latter being considered in Chapter 5.
Many dental restorations and appliances are constructed outside the patient’s mouth using models and dies which should be accurate replicas of the patient’s hard and soft tissues.
The term model is normally used when referring to a replica of several teeth and their associated soft tissues or, alternatively, to an edentulous arch. The term die is normally used when referring to a replica of a single tooth.
The morphology of the hard and soft tissues is recorded in an impression and models and dies are prepared using materials which are initially fluid and can be poured into the impression, then harden to form a rigid replica.
Many materials have been used for producing models and dies but the most popular are the materials based on gypsum products.
The current ISO Standard for Dental Gypsum Products identifies five types of material as follows:
Type 1 | Dental plaster, impression |
Type 2 | Dental plaster, model |
Type 3 | Dental stone, die, model |
Type 4 | Dental stone, die, high strength, low expansion |
Type 5 | Dental stone, die, high strength, high expansion |
The Type 1 material will be discussed in Chapter 17 (Non-elastic Impression Materials).
3.2 Requirements of dental cast materials
The main requirements of model and die materials are dimensional accuracy and adequate mechanical properties. The accuracy of fit of any restoration or appliance constructed outside the mouth depends inter alia on the dimensional accuracy of the replica on which it is constructed. Thus, the dimensional changes which occur during and after the setting of these model materials should, ideally, be minimal in order to produce an accurate model or die. The final fit of the appliance may depend upon a balancing of small expansions or contractions which occur at different stages in its construction and it would be unwise to consider, in isolation, dimensional changes occurring with the model and die materials.
Although small dimensional changes during setting can often be tolerated and even compensated for, changes occurring during storage are a more serious problem. Hence, the dimensional stability after setting should be as good as possible.
The material should, ideally, be fluid at the time it is poured into the impression so that fine detail can be recorded. A low contact angle between the model and impression materials would help to minimize the presence of surface voids on the set model by encouraging surface wetting.
The set material should be sufficiently strong to resist accidental fracture and hard enough to resist abrasion during the carving of a wax pattern.
The material should be compatible with all the other materials with which it comes into contact. For example, the set model should easily be removed from the impression without damage to its surface and fracture of teeth. It should give a good colour contrast with the various waxes which are often used to produce wax patterns.
3.3 Composition
Gypsum products used in dentistry are formed by driving off part of the water of crystallization from gypsum to form calcium sulphate hemihydrate.
Applications of gypsum products in dentistry involve the reverse of the above reaction. The hemihydrate is mixed with water and reacts to form the dihydrate.
The various types of gypsum product used in dentistry are chemically identical, in that they consist of calcium sulphate hemihydrate, but they may differ in physical form depending upon the method used for their manufacture.
Dental plaster (plaster of Paris): Dental plaster is indistinguishable from the white plaster used in orthopaedics for stabilizing fractured limbs during bone healing. Plaster is produced by a process known as calcination. Gypsum is heated to a temperature of about 120°C in order to drive off part of the water of crystallization. This produces irregular, porous particles which are sometimes referred to as β-hemihydrate particles (Fig. 3.1a). Overheating the gypsum may cause further loss of water to form calcium sulphate anhydrite (CaSO4), whilst underheating produces a significant concentration of residual dihydrate. The presence of both components has a marked influence upon the setting characteristics of the resultant plaster.
Fig. 3.1(a) Particles of calcium sulphate β-hemihydrate (dental plaster) (×235).
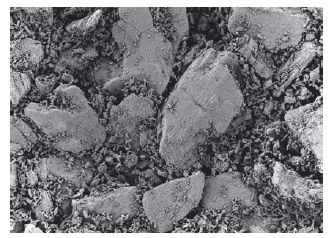
Dental stone: Dental stones may be produced by one of two methods. If gypsum is heated to about 125°C under steam pressure in an autoclave a more regular and less porous hemihydrate is formed (Fig. 3.1b). This is sometimes referred to as an α-hemihydrate.
Fig. 3.1(b) Particles of calcium sulphate α-hemihydrate (dental stone) (×235).
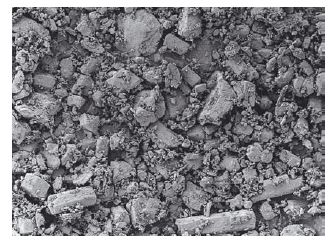
Alternatively, gypsum may be boiled in a solution of a salt such as CaCl2. This gives a material similar to that produced by autoclaving but with even less porosity. Manufacturers normally add small quantities of a dye to dental stones (see Fig. 3.2) in order that they may be differentiated from dental plaster, which is white.
Fig. 3.2 Dental stone. This shows powdered dental stone which is a gypsum product commonly used in dentistry for making casts and models. Note the colour of the stone which in this case is pale yellow. This is to enable the user to distinguish it from dental plaster which although chemically similar is of a different physical nature and is normally white coloured. In use, the powder is mixed with water to form a paste which then hardens to form a hard mass.
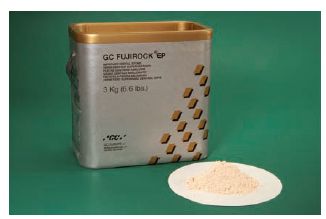
3.4 Manipulation and setting characteristics
Plaster and stone powders are mixed with water to produce a workable mix. Hydration of the hemihydrate then occurs producing the gypsum model or die.
Table 3.1 gives an indication of the water/ powder (W/P) ratio used for each material along with the theoretical ratio required to satisfy the chemical reaction which occurs. Although a ratio of only 0.186 is required to satisfy the reaction, such a mix would be too dry and unworkable. In the case of the more dense material, dental stone, a ratio of about 0.3 is required to produce a workable mix, whereas for the more porous plaster a higher W/P ratio of 0.55 is required. The excess water is absorbed by the porosities of the plaster particles. Considerable quantities of air may be incorporated during mixing and this may lead to porosity within the set material. Air porosity may be reduced either by vibrating the mix of plaster or stone in order to bring air bubbles to the surface or by mixing the material mechanically under vacuum, or both.
Table 3.1 Water/powder ratios for gypsum model and die materials.
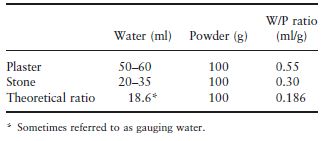
For hand mixing a clean, scratch free rubber or plastic bowl having a top diameter of about 130 mm is normally recommended. The presence of gypsum residues in the mixing bowl can noticeably alter the working and setting characteristics of a fresh mix and so the need for cleanliness is emphasized. A stiff spatula with a round-e/>
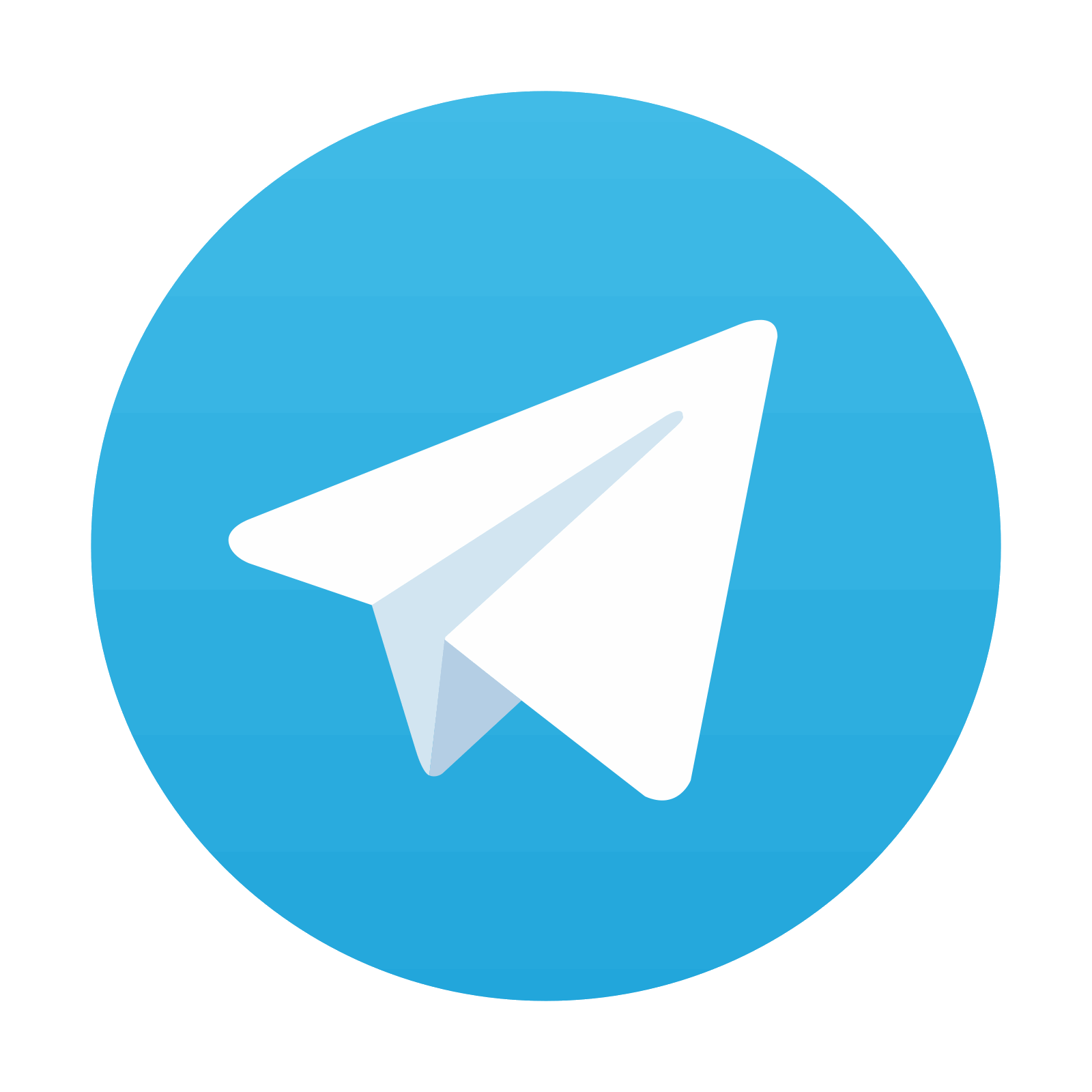
Stay updated, free dental videos. Join our Telegram channel

VIDEdental - Online dental courses
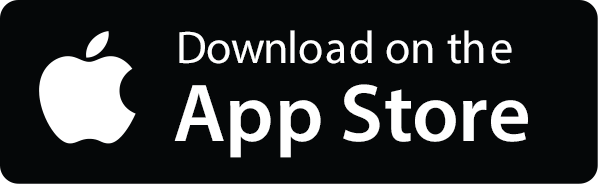
