Chapter 12 Other dental cements
Learning Objectives
From this chapter, the reader will:
• Be aware of the range of other dental cements currently available
• Understand the setting mechanisms and the ways they may be manipulated
• Understand their indications, contraindications and limitations
• Have an increased appreciation of how to use these materials more effectively and to their best advantage.
Introduction
This chapter deals with the other, more traditional, cements that dentists have used for many years. While their use has diminished to some extent in recent years as a result of the development of new materials, traditional cements are still available and widely used. It is therefore important that their composition, uses and handling characteristics are still understood by the dental team.
Essentially, these cements are varying permutations of a combination of an acidic liquid and a basic powder (Table 12.1), which, when mixed together, form a salt plus water. The acids and bases react to form different materials. The permutations of these interactions are illustrated in Figure 12.1. Glass ionomer cement has already been discussed in detail in Chapter 9. Silicate cement is no longer used in modern dentistry and therefore there is no need to consider it further. The other cement permutations are:
Table 12.1 Acids and bases participating in the formation of traditional dental cements
Acids | Bases |
---|---|
Phosphoric acid | Zinc oxide |
Poly(acrylic acid) | Magnesium oxide |
Maleic acid | Copper oxide |
Eugenol | Fluoro-alumino-silicate glass |
Mellitic acid |
Zinc oxide eugenol cement has further been modified with the addition of other active ingredients, marketed as a steroid/antibiotic cement. This modified cement and other materials such as setting calcium hydroxide cements and cavity varnishes are also discussed in this chapter.
General Structure
Zinc phosphate, zinc polycarboxylate and zinc oxide eugenol cements have the same structure (Figure 12.2). This is because these products have the same base (zinc oxide) and the different cements are produced by the reaction of this base with different acids. In each case, only the surface of the zinc oxide particles will react with the acid when mixed. The set cement is therefore composed of unreacted cores of zinc oxide powder surrounded by the matrix of the reaction product, namely zinc phosphate, zinc polycarboxylate or zinc eugenolate, respectively.
Zinc Phosphate Cements
Chemical constituents
Zinc phosphate cements have been used in dentistry for many decades. The material is generally supplied as zinc oxide powder and phosphoric acid liquid. Other chemicals are added to both the powder and liquid to modify the properties of the product (see Table 12.2).
Setting reaction and structure
The setting reaction of zinc phosphate cements is a two-stage process. In the first part of the reaction, the zinc oxide in the powder reacts with the phosphoric acid in the liquid to form zinc phosphate and water. This newly formed zinc phosphate reacts with more zinc oxide, forming hopeite. This compound is hydrated zinc phosphate. Aluminium when present prevents crystallization and permits the formation of an amorphous cement, which is very similar in structure to the glass ionomer cement (see Chapter 9).
Properties
Exothermic reaction and factors affecting the speed of set
The chemical reaction of zinc phosphate cement is the most exothermic of all the dental cements and so there is a potential risk that the heat produced during the setting reaction could cause pulpal inflammation. There are two methods by which manufacturers attempt to reduce this:
• By including buffers in the liquid component
• Treating the powder by heating it to above 1000°C. The higher this temperature, the less reactive is the powder.
Heat treatment of the powder causes granulation which, as the name suggests, converts the product into granules. The product is then sintered with other less reactive oxides (Figure 12.3) before being ground to a fine powder. The smaller the particles are ground, the greater is their reactivity.
Sintering: a heating process to densify and purify a mixture of components. Heating is carried out below the temperature of the lowest melting component.
Densify: to heat a product so that its particles coalesce but no ingredients are lost in the process. This can be compared to melting an Aero bar (Nestlé). None of the chocolate is lost, but as its constituents come closer together as a result of the heating, its volume decreases.
Mixing on a cooled glass slab permits the heat produced in the reaction to dissipate more easily and slows the chemical reaction, providing the dentist with a longer time for manipulation of the cement. Care must be taken not to cool the slab below the dew point or water condensation will form and affect the properties of the cement (Figure 12.4). Further regulation of the rate of setting is possible by varying the rate of incorporation of the powder to the liquid. The slower the incorporation of the powder fraction, the more slowly the cement will set. This is partly due to the fact that there is a reduction in temperature rise observed as each increment of cement powder starts to react at a different time. All of these factors may be used in the clinic to control the setting time of the cement.
Erosion
While the solubility of the cement is low, it further reduces with age as the cement matures and the water becomes bound into the matrix. The set cement starts to erode in an acid medium when the pH drops below 4.5, and the erosion becomes more marked with increasing acidity. In the clinical scenario, the set cement exposed to the oral environment will be subjected to cyclical changes in pH, which frequently falls below 4.5 (see Chapter 1).
Mechanical properties
The mechanical properties of the final cement are dependent on the powder/liquid ratio used. The mechanical properties increase with increased powder content until a point is reached where the material will not mix to a homogeneous mass. The more powder that is incorporated, the thicker the cement lute that is produced. The consistency of the mixed cement produced will depend on the clinical indication. Table 12.3 sets out the effects of some handling variables on the properties of the final cement.
Advantages and disadvantages
The advantages and disadvantages of zinc phosphate cement are set out in Table 12.4.
Table 12.4 Advantages and disadvantages of zinc phosphate cements
Advantages | Disadvantages |
---|---|
Easy to mix | Possibly irritant to the pulp |
Sharp set | Does not bond to tooth tissue or restorative materials |
Acceptable properties for purpose | Brittle |
Cheap | No antibacterial effects |
Long successful track record | Soluble in the mouth |
Opaque |
Indications and contraindications
Indications and contraindication are set out in Table 12.5.
Table 12.5 Indications and contraindications of zinc phosphate cement
Indications | Contraindications |
---|---|
Definitive cementation of inlays, metal-based crowns, metal-based bridges and orthodontic bands | Definitive cementation of all ceramic crowns and bridges |
As a base | When in very close proximity to the pulp without another intermediate material such as calcium hydroxide |
Temporary restorations where adequate retention is present |
Commercially available products
Commercially available products are shown in Table 12.6.
Table 12.6 Some zinc phosphate cements currently available on the market
Product name | Manufacturer |
---|---|
De Trey Zinc | Dentsply |
Hy-Bond Zinc Phosphate Cement | Shofu |
Zinc Cement | SS White |
Zinc Phosphate Cement | Heraeus |
Mixing
It is very important that the cement is mixed correctly as the properties of the cement will be determined by the reaction between the powder and liquid. The recommended method of mixing zinc phosphate cement to lute a cast restoration is illustrated in Box 12.1 and should be followed precisely.
Zinc Polycarboxylate (Polyalkenoate/Polyacrylate) Cements
Chemical constituents
Most products are presented as a powder, which is primarily zinc oxide (Table 12.7). The powder is mixed with the liquid, a viscous solution of poly(acrylic acid). Some manufacturers, however, vacuum dry the poly(acrylic acid) and add it to the zinc oxide powder. In these products the setting reaction is initiated by the addition of water to the powder.
The advantage of blending the poly(acrylic acid) and zinc oxide together in one composition is that the component will be in optimized proportions for use. The disadvantage is that the powder must be kept completely dry or the setting reaction will commence prematurely. In climates where the humidity is high this can be a major problem even with a desiccant being incorporated into the storage bottle cap (see Figure 9.19, p. 114).
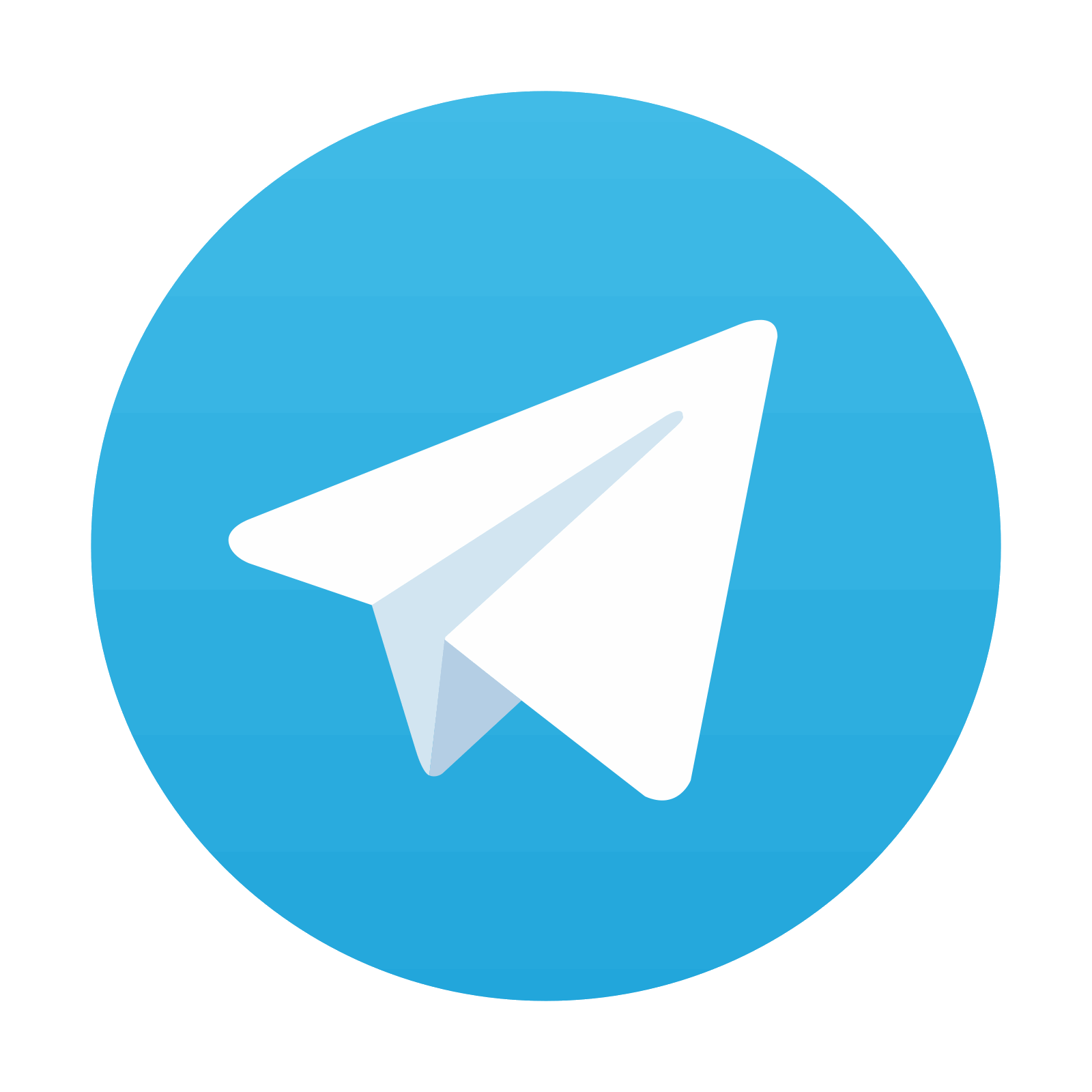
Stay updated, free dental videos. Join our Telegram channel

VIDEdental - Online dental courses
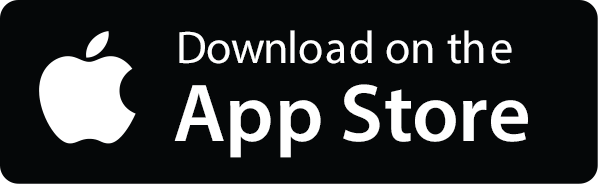
