Abstract
Objective
Glass ionomer cements (GIC) are clinically accepted dental restorative materials mainly due to their direct chemical adhesion to both enamel and dentin and their ability to release fluoride. However, their mechanical properties are inferior compared to those of amalgam and composite. The aim of this study is to investigate if combinations of nano- and macrogranular glass with different compositions in a glass ionomer cement can improve the mechanical and physical properties.
Methods
Glasses with the composition 4.5 SiO 2 –3 Al 2 O 3 –1.5 P 2 O 5 –(5 − x ) CaO − x CaF 2 ( x = 0 and x = 2) were prepared. Of each type of glass, particles with a median size of about 0.73 μm and 6.02 μm were made.
Results
The results show that the setting time of GIC decreases when macrogranular glass particles are replaced by nanogranular glass particles, whereas the compressive strength and Young’s modulus, measured after 24 h setting, increase. The effects are more pronounced when the nanogranular glass particles contain fluoride. After thermocycling, compressive strength decreases for nearly all formulations, the effect being most pronounced for cements containing nanogranular glass particles. Hence, the strength of the GIC seems mainly determined by the macrogranular glass particles.
Cumulative F − -release decreases when the macrogranular glass particles with fluoride are replaced by nanogranular glass particles with(out) fluoride.
Significance
The present study thus shows that replacing macro- by nanogranular glass particles with different compositions can lead to cements with approximately the same physical properties (e.g. setting time, consistency), but with different physicochemical (e.g. F − -release, water-uptake) and initial mechanical properties. On the long term, the mechanical properties are mainly determined by the macrogranular glass particles.
1
Introduction
Glass ionomer cements (GIC), also known as polyalkenoate cements, were discovered in the late 70s and are known for their good esthetical properties, their anti-cariogenic potential and their biocompatibility. Moreover, they have the unique ability to bind to wet tooth tissue. This prevents microleakage and increases the durability of a restoration. However, GIC are highly sensitive to moisture during initial hardening and have poor mechanical properties compared to other restorative materials, such as resin-modified GIC and composites . For these reasons they are predominantly used as luting and base cements and as filling materials in low load-bearing dental restorations.
Conventional GIC set by an acid-base reaction between a polyalkenoic acid and an aluminosilicate glass powder . The aluminosilicate glass powder normally contains Al, Si, and Ca. The ratio of these components determines whether the glass will form a cement. Si 4+ and Al 3+ are important compounds as they form a network of tetrahedrae with oxygen bridges . In this network, Al 3+ induces negative charges. These charges are compensated by Ca 2+ , which can also make the glass more basic by its network modifying capability . When mixed with polyalkenoic acid, the glass degrades, so that Ca 2+ and Al 3+ -ions are set free. These ions form complexes with the acid, so that a firm gel is formed. In a later stage, the silica ions eluted from the glass condensate and form a silica gel matrix .
The chemistry and formulation of the basic glass and the polyalkenoic acid both affect the setting reaction and the properties of the GIC. An increase of the molecular weight of the polyalkenoic acid results in improved mechanical properties, but reduces the handling properties . Lyophilized polyalkenoic acid was introduced, as an aqueous solution is unstable and becomes viscous in time . Photopolymerizable resin modified glass ionomer cements (RM-GIC) were developed by adding hydroxyethylmethacrylate (HEMA) and photo-initiators to a modified polyalkenoic acid. These cements are stronger and have better handling characteristics, but are still prone to water-uptake .
Over the years, many researchers have focused on the optimization of the composition of the glass to improve the physical and mechanical properties of the cement . Griffin and Hill have incorporated fluoride and phosphate in the calcium aluminosilicate glass and investigated the effect on the setting and mechanical properties of the GIC . F − was originally added to the glass mixture as a flux to decrease the melting temperature . It was found that fluoride disrupts the glass-network by forming Al–F–Ca( n ) and F–Ca( n ) species. In glasses with high fluoride content, additional Si–F–Ca( n ) species are formed. The incorporation of calcium into these species results in a reduction of the number of available cations to charge balance non bridging oxygens . This makes the glass more reactive and in this way it improves the mechanical properties of the GIC . Furthermore, as the polyalkenoic acid attacks the glass during setting, F − leaches from the glass and a reservoir of F − is formed within the matrix, which leads to a long-term release of F − . F − has been shown to have an anticariogenic effect due to the inhibition of the formation of bacterial plaques and due to the formation of fluorapatite, which is more resistant to acid dissolution than hydroxyapatite . Phosphor, on the other hand, can integrate in the tetrahedral network, which might create extra places for the acid to degrade the glass. However, phosphor also balances the charge deficit caused by aluminum and leads to a less reactive glass. During setting, cations can also bind to PO 4 3− , so that less cations are available to react with the acid groups. This consequently leads to weaker GIC with longer setting times .
Apart from the chemical composition of the glass and the polyalkenoic acid, the contact area between these components also controls the setting and mechanical properties of GICs. So, powder/liquid (P/L) ratio as well as particle size distribution are determining parameters for the setting rate and mechanical strengths of the set cement. Increasing the P/L ratio increases the setting rate and mechanical strength of GICs . Smaller particles reduce the setting time , and improve wear resistance, surface hardness and compressive strength . However, viscosity increases, which impedes the workability . This is a result of the higher surface area that is available for the acid to react with the glass . On the other hand, a combination of small particles with the original glass particles of the same composition results in GIC with better mechanical and handling properties .
Although several studies have demonstrated that the properties of GICs can be optimized by changing the composition or the particle size and distribution of the glass, the combined effect of such changes has not yet been explored.
The purpose of this study is two-fold. First, the effect of the particle size of the glass on the physical and mechanical properties of the GIC is evaluated. Secondly, as the properties of a GIC are also determined by the composition of the glass, the effect of combining nano- and macrogranular particles of glasses with different compositions on the physical and mechanical properties of the GIC is investigated. The hypothesis is that mixing nano- and macrogranular particles of glasses with different compositions can result in GIC with optimal physicochemical and mechanical properties.
2
Materials and methods
For all solutions, demineralized water was used (Milli-Q system, Millipore, Bedford, MA, USA).
2.1
Synthesis of the glass powder
Glass with the composition 4.5 SiO 2 –3 Al 2 O 3 –1.5 P 2 O 5 –(5 − x ) CaO − x CaF 2 was prepared, as described by Griffin and Hill, by mixing appropriate amounts of SiO 2 (Merck 7536), Al 2 O 3 (Merck 1095), CaCO 3 (Merck 2066), P 2 O 5 (Fluka 79612) and CaF 2 (Mallinckrodt (AR) 4168) . A total batch size of 100 g was made. Glass without ( x = 0) and with ( x = 2) fluoride was synthesized.
The powder mixture of glass without fluoride and glass with fluoride was heated respectively at 1475 °C and 1450 °C in alumina crucibles in a furnace (HTF17, Carbolite, Hope valley, UK). After homogenization, the glass melt was poured in demineralized water to produce a glass frit .
The glass frit was ground in a planetary mill (Pulverisette 6, Fritsch GmbH, Idar-Oberstein, Germany) with a zirconia mortar and balls at 300 rpm and sieved (Vibratory Sieve-Shaker, Analysette 3 Fritsch GmbH, Idar-Oberstein, Germany). The fraction with a particle diameter <38 μm was further used and is referred to as “macrogranular glass particles”. Macrogranular glass particles without fluoride will be referred to as “M 0 ”, those with fluoride as “M 2 ”. The particle size was further reduced by grinding the macrogranular glass particles in isopropanol in the planetary mill using a zirconia mortar with zirconia beads (Ø 0.5 mm) at 600 rpm. This fraction is referred to as “nanogranular glass particles”. In accordance with the macrogranular glass particles, nanogranular glass particles without fluoride will be referred to as “N 0 ”, those with fluoride as “N 2 ”.
2.2
Characterization of the powder
The chemical composition of the glasses was determined according to the method described by De Maeyer and Verbeeck . The Ca, Al and Si content was determined using atomic absorption spectrophotometry (Varian SpectrAA-30, Agilent Technologies, Santa Clara, USA). The fluoride content was determined with a fluoride selective electrode coupled to an Orion 940 Ionanalyzer with a 960 Autochemistry system (Orion Research, Boston, MA, USA). PO 4 3− content was determined with a differential spectrophotometric method using a Pye Unicam PU 8670 VIS/NIR spectrophotometer (Philips Scientific Equipment, Brussels, Belgium).
The homogeneity of the glasses was evaluated using XRD-patterns recorded for diffraction angles between 2° and 60° 2θ with a PW1830 Philips diffractometer (PANalytical, Almelo, The Netherlands). In order to eliminate differences in P/L ratio, the density of the glasses was checked with a micropycnometer (Quantachrome Instruments, FL, USA).
Specific surface area of the glasses was measured by means of the Brunauer–Emmet–Teller (BET) method with nitrogen as adsorbent gas and helium as carrier gas (Monosorb appliance, Quantachrome, USA). Particle size distribution of the nano- and macrogranular glass particles was determined with laser diffraction (Mastersizer, Malvern, Worcestershire, UK). Isopropanol was used as a fluid.
The reactivity of the glass was determined by adding 0.025 g of glass to 20 ml 0.01 M acetic acid (pH 3.4). During the dissolution of the basic glass, pH of the solution was measured with a pH-electrode (Primatrode, Metrohm, Switzerland). The rate of pH change is a marker for the reactivity .
2.3
Preparation and characterization of glass ionomer cement
Glass mixtures were prepared by combining macro- and nanogranular glass particles. The different combinations of glasses used in this study are given in Table 1 .
Glass formulation | Notation | Glass formulation | Notation |
---|---|---|---|
Macrogranular glass without F − | M 0 | Macrogranular glass with F − | M 0 |
90% macrogranular glass without F − + 10% nanogranular glass without F − | M 0 10N 0 | 90% macrogranular glass with F − + 10% nanogranular glass without F − | M 2 10N 0 |
80% macrogranular glass without F − + 20% nanogranular glass without F − | M 0 20N 0 | 80% macrogranular glass with F − + 20% nanogranular glass without F − | M 2 20N 0 |
90% macrogranular glass without F − + 10% nanogranular glass with F − | M 0 10N 2 | 90% macrogranular glass with F − + 10% nanogranular glass with F − | M 2 10N 2 |
80% macrogranular glass without F − + 20% nanogranular glass with F − | M 0 20N 2 | 80% macrogranular glass with F − + 20% nanogranular glass with F − | M 2 20N 2 |
The GIC powder was formulated by mixing freeze-dried polyacrylic acid (versicol E7, Allied Colloids, Bradford, England) with the glass mixture in a glass:polyacid ratio of 5:1. The cement was prepared by mixing the GIC powder with a 10 wt% tartaric acid solution, so that the powder:liquid ratio was 4:1. This mixture was thoroughly mixed by hand on a glass plate with a spatula to form a paste .
To determine the consistency, 0.05 ml of the cement paste was placed on a glass plate using a syringe. The cement was covered with a second glass plate. Within 2 min, starting from mixing, a 2.5 kg mass was lowered on top of this glass plate for another 2 min. The mean horizontal and vertical diameter of the flattened cement paste was taken as a measure for the consistency.
Setting time at 22 °C was determined with an indentator (Ø 1 mm, 400 g). A metal mold (Ø 1 cm, H 2 mm) was filled with the paste within 2.5 min after the start of mixing. The needle was lowered on the cement surface every 15 s. The setting time is recorded as the time elapsed between the start of mixing and the time when the needle does not form a complete circular indentation on the cement.
For each glass combination ( Table 1 ), 12 GIC-cylinders (Ø 6 mm, H 12 mm) were made using a stainless steel mold. All cylinders were matured for 24 h in 80% relative humidity at 37 °C. 6 samples were subsequently subjected to thermocycling (5–55 °C, 5000 cycli, 30 s/cycle, Thermocycler THE-1100, SD Mechatronik, Feldkirchen-Westerham, Germany).
Compressive strength of the 12 cylinders was determined with a universal testing machine (LRX plus, Lloyd Instruments, Bognor Regis, UK). Cylinders were loaded at a speed of 1 mm/min. Compressive strength (MPa) and Young’s modulus E (MPa) were determined from the stress–strain curve.
The mass of each sample used for compressive strength, was measured before and after thermocycling. The relative mass increase is a measure for the water uptake and consequently the water sensitivity of the GIC .
Fluoride-release was determined using 3 cylindrical GIC specimens (Ø 6 mm, H 3 mm) of each glass combination ( Table 1 ), made using a stainless steel mold. The samples were matured in 80% relative humidity for 24 h before transferring them into PE flasks with 25 ml demineralized water. The water was renewed at 0.25, 1, 2, 7, 14, 21 and 28 days after the start of the immersion. The concentration of fluoride was measured at each time interval with a fluoride selective electrode coupled to an Orion 940 Ionanalyzer with a 960 Autochemistry system (Orion Research, Boston, MA, USA). The cumulative amount of fluoride released ( <SPAN role=presentation tabIndex=0 id=MathJax-Element-1-Frame class=MathJax style="POSITION: relative" data-mathml='Fcum−’>F−cumFcum−
F cum −
) was calculated and converted to micrograms of fluoride released per unit surface area (μg/cm 2 ) .
2.4
Evaluation of the results
The effect of the formulation on the properties of the experimental GIC was evaluated with ANOVA. Significant differences between means were determined with a multiple comparison test (Bonferroni, 95% confidence level).
2
Materials and methods
For all solutions, demineralized water was used (Milli-Q system, Millipore, Bedford, MA, USA).
2.1
Synthesis of the glass powder
Glass with the composition 4.5 SiO 2 –3 Al 2 O 3 –1.5 P 2 O 5 –(5 − x ) CaO − x CaF 2 was prepared, as described by Griffin and Hill, by mixing appropriate amounts of SiO 2 (Merck 7536), Al 2 O 3 (Merck 1095), CaCO 3 (Merck 2066), P 2 O 5 (Fluka 79612) and CaF 2 (Mallinckrodt (AR) 4168) . A total batch size of 100 g was made. Glass without ( x = 0) and with ( x = 2) fluoride was synthesized.
The powder mixture of glass without fluoride and glass with fluoride was heated respectively at 1475 °C and 1450 °C in alumina crucibles in a furnace (HTF17, Carbolite, Hope valley, UK). After homogenization, the glass melt was poured in demineralized water to produce a glass frit .
The glass frit was ground in a planetary mill (Pulverisette 6, Fritsch GmbH, Idar-Oberstein, Germany) with a zirconia mortar and balls at 300 rpm and sieved (Vibratory Sieve-Shaker, Analysette 3 Fritsch GmbH, Idar-Oberstein, Germany). The fraction with a particle diameter <38 μm was further used and is referred to as “macrogranular glass particles”. Macrogranular glass particles without fluoride will be referred to as “M 0 ”, those with fluoride as “M 2 ”. The particle size was further reduced by grinding the macrogranular glass particles in isopropanol in the planetary mill using a zirconia mortar with zirconia beads (Ø 0.5 mm) at 600 rpm. This fraction is referred to as “nanogranular glass particles”. In accordance with the macrogranular glass particles, nanogranular glass particles without fluoride will be referred to as “N 0 ”, those with fluoride as “N 2 ”.
2.2
Characterization of the powder
The chemical composition of the glasses was determined according to the method described by De Maeyer and Verbeeck . The Ca, Al and Si content was determined using atomic absorption spectrophotometry (Varian SpectrAA-30, Agilent Technologies, Santa Clara, USA). The fluoride content was determined with a fluoride selective electrode coupled to an Orion 940 Ionanalyzer with a 960 Autochemistry system (Orion Research, Boston, MA, USA). PO 4 3− content was determined with a differential spectrophotometric method using a Pye Unicam PU 8670 VIS/NIR spectrophotometer (Philips Scientific Equipment, Brussels, Belgium).
The homogeneity of the glasses was evaluated using XRD-patterns recorded for diffraction angles between 2° and 60° 2θ with a PW1830 Philips diffractometer (PANalytical, Almelo, The Netherlands). In order to eliminate differences in P/L ratio, the density of the glasses was checked with a micropycnometer (Quantachrome Instruments, FL, USA).
Specific surface area of the glasses was measured by means of the Brunauer–Emmet–Teller (BET) method with nitrogen as adsorbent gas and helium as carrier gas (Monosorb appliance, Quantachrome, USA). Particle size distribution of the nano- and macrogranular glass particles was determined with laser diffraction (Mastersizer, Malvern, Worcestershire, UK). Isopropanol was used as a fluid.
The reactivity of the glass was determined by adding 0.025 g of glass to 20 ml 0.01 M acetic acid (pH 3.4). During the dissolution of the basic glass, pH of the solution was measured with a pH-electrode (Primatrode, Metrohm, Switzerland). The rate of pH change is a marker for the reactivity .
2.3
Preparation and characterization of glass ionomer cement
Glass mixtures were prepared by combining macro- and nanogranular glass particles. The different combinations of glasses used in this study are given in Table 1 .
Glass formulation | Notation | Glass formulation | Notation |
---|---|---|---|
Macrogranular glass without F − | M 0 | Macrogranular glass with F − | M 0 |
90% macrogranular glass without F − + 10% nanogranular glass without F − | M 0 10N 0 | 90% macrogranular glass with F − + 10% nanogranular glass without F − | M 2 10N 0 |
80% macrogranular glass without F − + 20% nanogranular glass without F − | M 0 20N 0 | 80% macrogranular glass with F − + 20% nanogranular glass without F − | M 2 20N 0 |
90% macrogranular glass without F − + 10% nanogranular glass with F − | M 0 10N 2 | 90% macrogranular glass with F − + 10% nanogranular glass with F − | M 2 10N 2 |
80% macrogranular glass without F − + 20% nanogranular glass with F − | M 0 20N 2 | 80% macrogranular glass with F − + 20% nanogranular glass with F − | M 2 20N 2 |
The GIC powder was formulated by mixing freeze-dried polyacrylic acid (versicol E7, Allied Colloids, Bradford, England) with the glass mixture in a glass:polyacid ratio of 5:1. The cement was prepared by mixing the GIC powder with a 10 wt% tartaric acid solution, so that the powder:liquid ratio was 4:1. This mixture was thoroughly mixed by hand on a glass plate with a spatula to form a paste .
To determine the consistency, 0.05 ml of the cement paste was placed on a glass plate using a syringe. The cement was covered with a second glass plate. Within 2 min, starting from mixing, a 2.5 kg mass was lowered on top of this glass plate for another 2 min. The mean horizontal and vertical diameter of the flattened cement paste was taken as a measure for the consistency.
Setting time at 22 °C was determined with an indentator (Ø 1 mm, 400 g). A metal mold (Ø 1 cm, H 2 mm) was filled with the paste within 2.5 min after the start of mixing. The needle was lowered on the cement surface every 15 s. The setting time is recorded as the time elapsed between the start of mixing and the time when the needle does not form a complete circular indentation on the cement.
For each glass combination ( Table 1 ), 12 GIC-cylinders (Ø 6 mm, H 12 mm) were made using a stainless steel mold. All cylinders were matured for 24 h in 80% relative humidity at 37 °C. 6 samples were subsequently subjected to thermocycling (5–55 °C, 5000 cycli, 30 s/cycle, Thermocycler THE-1100, SD Mechatronik, Feldkirchen-Westerham, Germany).
Compressive strength of the 12 cylinders was determined with a universal testing machine (LRX plus, Lloyd Instruments, Bognor Regis, UK). Cylinders were loaded at a speed of 1 mm/min. Compressive strength (MPa) and Young’s modulus E (MPa) were determined from the stress–strain curve.
The mass of each sample used for compressive strength, was measured before and after thermocycling. The relative mass increase is a measure for the water uptake and consequently the water sensitivity of the GIC .
Fluoride-release was determined using 3 cylindrical GIC specimens (Ø 6 mm, H 3 mm) of each glass combination ( Table 1 ), made using a stainless steel mold. The samples were matured in 80% relative humidity for 24 h before transferring them into PE flasks with 25 ml demineralized water. The water was renewed at 0.25, 1, 2, 7, 14, 21 and 28 days after the start of the immersion. The concentration of fluoride was measured at each time interval with a fluoride selective electrode coupled to an Orion 940 Ionanalyzer with a 960 Autochemistry system (Orion Research, Boston, MA, USA). The cumulative amount of fluoride released ( <SPAN role=presentation tabIndex=0 id=MathJax-Element-2-Frame class=MathJax style="POSITION: relative" data-mathml='Fcum−’>F−cumFcum−
F cum −
) was calculated and converted to micrograms of fluoride released per unit surface area (μg/cm 2 ) .
2.4
Evaluation of the results
The effect of the formulation on the properties of the experimental GIC was evaluated with ANOVA. Significant differences between means were determined with a multiple comparison test (Bonferroni, 95% confidence level).
3
Results
3.1
Characterization of the powder
Table 2 shows the molar ratios relative to the Si content of the components of the glasses synthesized in this study. The theoretical molar ratios for the glasses are also given for comparison. The composition of the glass without F − matches the theoretical composition. The Al/Si and F/Si ratios of the glass with F − are significantly smaller than the theoretical ratios.
Glass | Al/Si | Ca/Si | P/Si | F/Si |
---|---|---|---|---|
M 0 | 1.30 ± 0.06 | 1.10 ± 0.04 | 0.66 ± 0.02 | / |
M 2 | 1.17 ± 0.05 | 1.08 ± 0.04 | 0.61 ± 0.02 | 0.47 ± 0.02 |
Theoretical molar ratio | 1.33 | 1.11 | 0.67 | 0.89 a |
The X-ray diffraction patterns of both glasses are typical for an amorphous solid, indicating that M 0 and M 2 contain no crystalline phases.
The density of the macrogranular glass particles (2.743 ± 0.011 g/cm 3 for M 0 and 2.740 ± 0.011 g/cm 3 for M 2 ) equals within the experimental error that of the nanogranular glass particles (2.734 ± 0.011 g/cm 3 for N 0 and 2.742 ± 0.011 g/cm 3 for N 2 ).
The specific surface area of the macrogranular glass particles (0.77 ± 0.05 m 2 /g for M 0 and 0.78 ± 0.05 m 2 /g for M 2 ) is more than 10 times smaller than that of the nanogranular glass particles (10.1 ± 0.6 m 2 /g for N 0 and 12.6 ± 0.8 m 2 /g for N 2 ). The specific surface areas of the glasses without and with F are not significantly different.
The particle size distribution of the macro- and nanogranular glass particles is represented in Fig. 1 . The particle size distribution is asymmetrical for the macrogranular glass particles and symmetrical for the nanogranular glass particles. The size distribution is considerably broader for the macrogranular glass particles compared to that of the nanogranular glass particles.
The pH change during the reaction of the alkaline glasses and the acetic acid is shown in Fig. 2 . A reduction in size drastically increases the reactivity of particles with the same composition. On the basis of a non-linear regression analysis, the maximal increase of the pH ((ΔpH) max ) and the initial reaction rate after 1 min (dpH/dt) t =1 were calculated ( Table 3 ). (ΔpH) max of the macrogranular glass particles is about 1.6 times smaller than that of the nanogranular glass particles. (dpH/dt) t =1 is about 10 times smaller for the macrogranular glass particles compared to the nanogranular glass particles. Both parameters are comparable for the glass without and with F − ( P > 0.05).
Constant | M 0 | M 2 | N 0 | N 2 |
---|---|---|---|---|
(ΔpH) max | 0.39 ± 0.02 | 0.39 ± 0.01 | 0.61 ± 0.01 | 0.65 ± 0.01 |
(dpH/dt) t =1 | 0.0080 ± 0.0001 | 0.0117 ± 0.0001 | 0.09 ± 0.01 | 0.13 ± 0.02 |
3.2
Characterization of the cement
Table 4 shows that consistencies are roughly the same and consequently have no effect on the clinical handling of the cement.
GIC | M 0 | M 0 10N 0 | M 0 20N 0 | M 0 10N 2 | M 0 20N 2 | M 2 | M 2 10N 0 | M 2 20N 0 | M 2 10N 0 | M 2 20N 0 |
---|---|---|---|---|---|---|---|---|---|---|
Diameter (mm) | 23.70 (0.99) | 20.65 (0.35) | 21.83 (0.04) | 23.88 (0.14) | 19.73 (0.21) | 18.60 (0.42) | 21.59 (0.34) | 22.08 (0.39) | 22.08 (0.07) | 21.18 (0.34) |
Setting times of the different GIC are given in Fig. 3 A . Adding F − to the formulation decreases the setting time significantly ( P < 0.001). The setting time decreases with an increasing amount of nanogranular glass particles replacing the macrogranular glass particles ( P < 0.030), the effect being most pronounced for the nanogranular glass particles with fluoride ( P < 0.002).
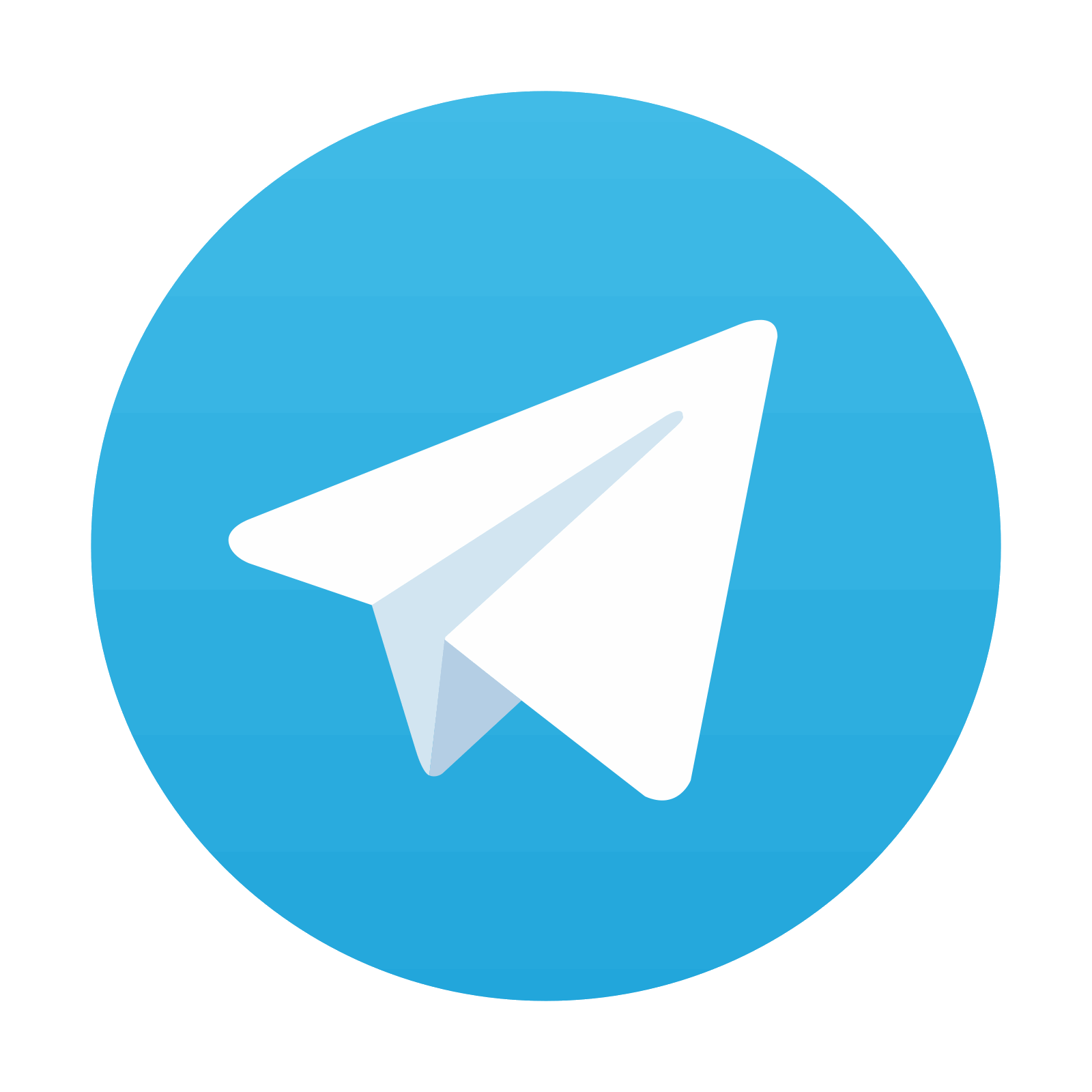
Stay updated, free dental videos. Join our Telegram channel

VIDEdental - Online dental courses
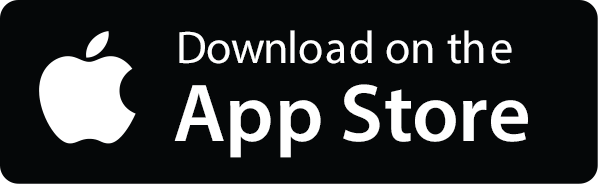

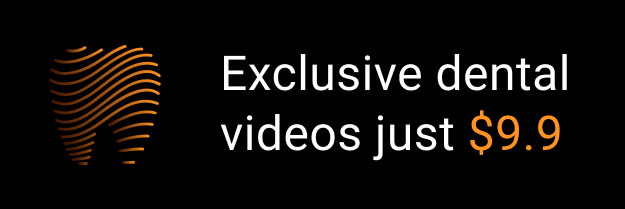