Structure and Properties of Cast Dental Alloys
Metals and Alloys
The wide range of dental alloy compositions is described briefly in this chapter and they are discussed further in Chapter 16. Dental casting alloys are associated with the following groups:
1. Dental amalgams, which contain mercury (Hg), silver (Ag), tin (Sn), and copper (Cu).
2. High noble (HN) alloys, which contains at least 40 wt% gold (Au) and 60 wt% of noble metals.
3. Noble (N) metal alloys, which are typically based on palladium (Pd) as the main noble metal with a total noble metal content of at least 25 weight percent. Noble metal alloys may also contain gold, silver, copper, gallium (Ga), indium (In), platinum (Pt), and tin (Sn).
4. Predominantly base (PB) metal alloys, which contain less than 25 wt% of noble metals, are most commonly composed of one of the following groups: nickel and chromium (Ni-Cr); cobalt and chromium (Co-Cr); iron, carbon, and chromium (Fe-C-Cr); commercially pure titanium (CP-Ti); and titanium-aluminum and vanadium (Ti-Al-V).
Two nonwhite metals in the periodic table of the elements (Table 5-1) are gold and copper, both of which are important components of cast dental alloys. Alloys with a relatively high gold content are yellow in hue and those containing significant concentrations of copper are reddish-yellow in hue. Most cast dental alloys, which are based on either cobalt, nickel, palladium, or silver, are “white” or silver in appearance, although these alloys may exhibit slight differences in hue and chroma. There is one exception, however. In the late 1970s a palladium-indium (Pd-In) alloy was introduced that exhibited a yellow hue. This color was attributed to an optical effect involving the intermetallic compound Pd-In. Argenco Y+ (Argen Corporation, San Diego, CA) is an example of such an alloy. Another alloy of this type, Castell (Jensen Dental, North Haven, CT) is marketed as a yellow type III alloy. This alloy contains 20% Au, 20% Pd, 17% In, 38% Ag, 17% In, 4% Zn, 1% Cu and other minor elements. Because it contains more than 25% by weight of noble metals, it would be classified as a noble alloy. Alloys of this type exhibit a pale yellow to gold color derived from the interaction of two white metals, palladium and indium. Alloying additions are included to improve castability, ductility, strength, hardness, tarnish resistance, and corrosion resistance. These alloys have recently gained in popularity because of the high price of gold. The tarnish resistance of the alloy is highly dependent on the composition and quality of the casting. Any porosity or contamination will result in rapid discoloration of the alloy. Once lab technicians learn how to use the alloy correctly, it can have great success clinically.
TABLE 5-1
Physical Properties of Alloy-Forming Elements
Element | Symbol | Atomic Weight | Melting Point (°C) | Boiling Point (°C) | Density (g/cm3) | Thermal Expansion Coefficient (10−6/K) |
Aluminum | Al | 26.98 | 660.3 | 2450 | 2.70 | 23.6 |
Carbon | C | 12.01 | 630.5 | 4830 | 2.22 | 6.0 |
Chromium | Cr | 52.00 | 271.3 | 2665 | 7.19 | 6.2 |
Cobalt | Co | 58.93 | 1495.0 | 2900 | 8.85 | 13.8 |
Copper | Cu | 63.54 | 1083.0 | 2595 | 8.96 | 16.5 |
Gold | Au | 196.97 | 1063.0 | 2970 | 19.32 | 14.2 |
Indium | In | 114.82 | 156.2 | 2000 | 7.31 | 33.0 |
Iridium | Ir | 192.20 | 2454.0 | 5300 | 22.50 | 6.8 |
Iron | Fe | 55.85 | 1527.0 | 3000 | 7.87 | 12.3 |
Magnesium | Mg | 24.31 | 650.0 | 1107 | 1.74 | 25.2 |
Mercury | Hg | 200.59 | −38.9 | 357 | 13.55 | 40.0 |
Molybdenum | Mo | 95.94 | 2619.0 | 5560 | 10.22 | 4.9 |
Nickel | Ni | 58.71 | 1453.0 | 2730 | 8.90 | 13.3 |
Palladium | Pd | 106.40 | 1552.0 | 3980 | 12.02 | 11.8 |
Platinum | Pt | 195.09 | 1769.0 | 4530 | 21.45 | 8.9 |
Rhodium | Rh | 102.91 | 1966.0 | 4500 | 12.44 | 8.3 |
Silicon | Si | 28.09 | 1410.0 | 2480 | 2.33 | 7.3 |
Silver | Ag | 107.87 | 960.8 | 2216 | 10.49 | 19.7 |
Tin | Sn | 118.69 | 231.9 | 2270 | 7.30 | 23.0 |
Titanium | Ti | 47.90 | 1668.0 | 3260 | 4.51 | 8.5 |
Tungsten | W | 183.85 | 3410.0 | 5930 | 19.30 | 4.6 |
Zinc | Zn | 65.37 | 420.0 | 906 | 7.133 | 0.4 |
Data from Lyman T, editor: Metals Handbook, ed 8, vol 1. Cleveland OH, American Society for Metals, 1964.
Of the 118 elements currently listed in the periodic table, about 88 (74.6%) can be classified as metals. No element having an atomic number higher than 92 occurs naturally in large quantities. It is of scientific interest that the metallic elements can be grouped according to density, ductility, melting point, and nobility. This indicates that the properties of metals are closely related to their valence electron configuration. The groups of pure metal elements can be seen in Figure 5-1, the periodic chart of the elements. All elements in the same group—for example, the alkali metals in group 1—have the same number of outer electrons, which results in similar chemical properties. The halogens within group 17 also have similar properties. For example, when halogen atoms react, they gain an electron to form negatively charged ions. Each ion has the same electron configuration as the other noble gases in the same period. Thus, the ions formed are more chemically stable than the elements from which they were formed.
The properties of the pure elements do not change abruptly from metallic to nonmetallic as viewed from the left to the right side of the periodic chart in Figure 5-1. The boundary between metals and nonmetals is indistinct, and the elements near the boundary exhibit characteristics of both metals and nonmetals. The elements boron, carbon, and silicon are often combined with metals to form commercially important engineering materials. Silicon is termed a semiconductor because its electrical conductivity is intermediate between that of a metal and that of an insulator. However, in dentistry the most common casting alloys used for dental appliances and prostheses are based on a majority of one or more of the following metallic elements: cobalt (Co), gold (Au), iron (Fe), nickel (Ni), palladium (Pd), silver (Ag), and titanium (Ti).
Metallic Bonding
Pure metals, in common with other chemical elements, can be identified by their specific melting and boiling points and by their basic physical and chemical properties. Some of these properties for metals of dental interest are listed in Table 5-1. Pure metals have limited uses in dental and engineering applications, because they are too soft and some may corrode excessively. To optimize properties, most metals used in engineering and dental applications are either mixtures of two or more metallic elements or mixtures of one or more metals and nonmetallic elements. These alloys are generally prepared by fusion of the elements above their melting points. For example, a small amount of carbon is added to iron to form steel. A certain amount of chromium is added to iron, carbon, and other elements to form stainless steel, an alloy that is highly resistant to corrosion. As previously noted, chromium is also used to impart corrosion resistance to nickel or cobalt alloys, which comprise two of the major groups of base metal alloys used in dentistry. Chromium provides this corrosion resistance by forming a very thin, adherent surface oxide (Cr2O3) that prevents the diffusion of oxygen or other corroding species to the underlying metal. Although pure gold is also highly resistant to corrosion, copper is added to gold for many dental alloys to increase their strength and resistance to permanent deformation. In this chapter, the term metal is used to describe alloys as well as pure metals.
Classification of Alloys
The simplest alloy is a solid solution, in which atoms of two metals are mutually completely soluble and dispersed in specific arrays within the same crystal structure, such as face-centered cubic (FCC) as shown in Figure 5-1, body-centered cubic (BCC), and hexagonal close-packed (HCP). When observed with an optical microscope, the individual grains and the microstructures overall of solid solution alloys may resemble those of pure metals. The structure will appear to be entirely homogeneous, since only one phase is formed during solidification. The temperature-versus-composition graphs for such alloys are sometimes referred to as “isomorphous phase diagrams.” Most gold alloys used in clinical dentistry are predominantly solid solutions, although they usually contain more than two metals.
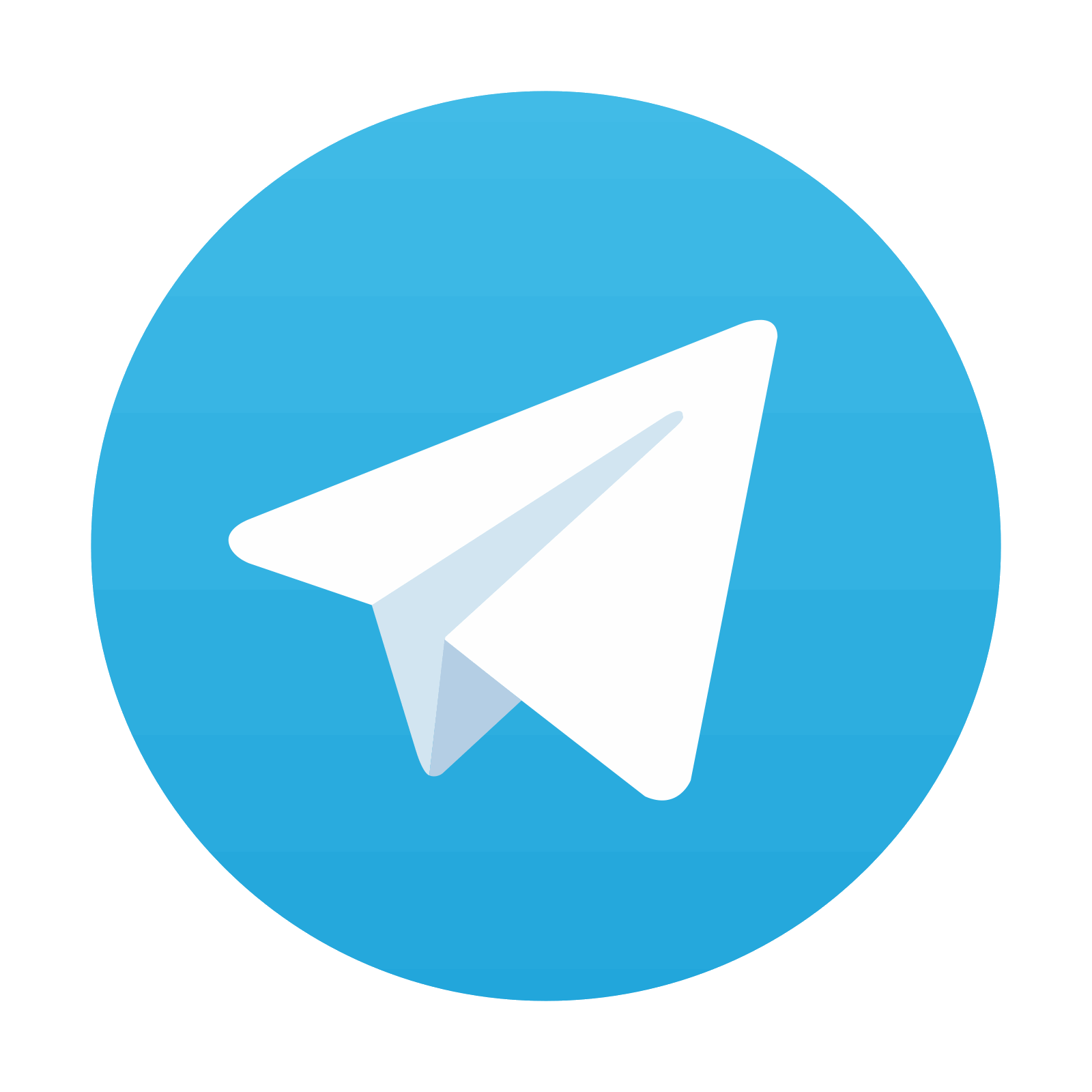
Stay updated, free dental videos. Join our Telegram channel

VIDEdental - Online dental courses
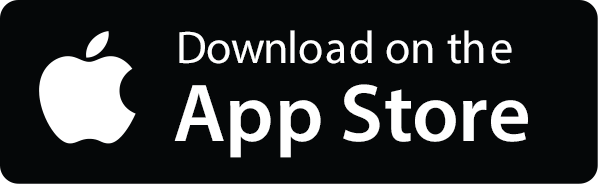
