Introduction
During sliding mechanics, frictional resistance is an important counterforce to orthodontic tooth movement, which must be controlled to allow application of light, continuous forces. We investigated the static frictional resistance between 3 modern orthodontic brackets—ceramic with gold-palladium slot, ceramic, and stainless steel—and 4 archwires (0.019 × 0.025-in)—stainless steel, nickel-titanium, titanium-molybdenum alloy (TMA), and low-friction colored TMA.
Methods
All tests were carried out in a dry state on a universal testing machine. Surface topography of bracket slots and archwires was studied by using a scanning electron microscope and quantified by using a surface roughness testing machine (profilometer).
Results
In the scanning electron microscope measurements, the smoothest surface was the ceramic gold-palladium bracket and stainless steel wire. The profilometer quantified the surface roughness, which also was lowest for the ceramic gold-palladium bracket and stainless steel wire. The ceramic bracket with the gold-palladium slot showed the least frictional values in all combinations and could be a promising alternative to solve the problem of friction. Frictional values for colored TMA were comparable with stainless steel wires and might be a good alternative during space closure in sliding mechanics.
Conclusions
Ceramic with gold-palladium slot bracket and colored TMA archwire seem to be a good alternative to stainless steel in space closure with sliding mechanics.
Orthodontic brackets and archwires are important constituents of an orthodontic appliance. During sliding mechanics, it is either the bracket or the archwire that slides through the bracket slot. Overcoming the friction between the 2 surfaces demands an important consideration in appliance design, since friction opposes every action that an orthodontist takes to move teeth.
The first law of friction states that the frictional force is proportional to the applied load (N) by a constant, the coefficient of friction (μ) (F = μ × N). The coefficient of friction depends on the material’s relative roughness. Surface roughness is a characteristic of the material itself, its shelf life, and the manufacturing processes (polishing, heat treatment). All surfaces, no matter how smooth, have irregularities, and real contacts occur only at a few small peaks or asperities. Hence, understanding the friction forces between the brackets and wires is essential for achieving adequate tooth movement and an optimal biologic response.
Several variables of friction, which affect sliding tooth movement, have been investigated in previous studies. But there are conflicting views on the influence of surface roughness of archwires and bracket slots on measured frictional resistance. Kusy et al were the first to look at the effect of surface topography of wires using laser spectroscopy on friction coefficients. Their results showed that low surface roughness was not a sufficient condition for low-friction coefficients. Prososki et al also showed similar results using a profilometer. However, in these studies, surface roughness of the bracket slots was not considered.
Of all the different materials tested so far, stainless steel (SS) brackets with SS archwires are preferred for their low frictional force values. However, concerns have been expressed in the literature about the nickel content of SS in the oral environment. The newer esthetic ceramic brackets are known for high frictional values. To combat both demands, esthetic ceramic brackets with a metal slot have been developed.
Newer grades of archwires are known for their high resiliency, shape memory, low rigidity, such as nickel-titanium (NiTi), titanium-molybdenum alloy (TMA), and, recently, colored TMA.
Burstone and Farzin-Nia showed that ion implantation enhances archwire properties. Cash et al reported that honeydew-colored and ion-implanted TMA might allow space closure with minimal development of frictional forces.
No study has correlated the surface roughness of these new wires with newly developed ceramics with a gold-slot bracket. Thus, the aims of this study were to evaluate the static frictional resistance between orthodontic brackets (SS, ceramic, and ceramic with gold-palladium slot) and archwires (SS, NiTi, TMA, and low-friction colored TMA) and to evaluate the relationship between surface roughness and the amount of frictional resistance between various bracket-wire combinations.
Material and methods
Three types of 0.022-in slot MBT prescription canine brackets were tested: stainless steel (Victory Series, 3M Unitek, Monrovia, Calif), ceramic (Illusion Plus, Ortho Organizers, Carlsbad, Calif), and ceramic with gold-palladium slot (Virage, American Orthodontics, Sheboygan, Wis). A total of 40 brackets of each type were used ( Table I ).
Archwire alloy | Wire section (in) | Brackets (n) | ||
---|---|---|---|---|
SS | C | C/GP | ||
SS | 0.019 × 0.025 | 10 | 10 | 10 |
NiTi | 0.019 × 0.025 | 10 | 10 | 10 |
TMA | 0.019 × 0.025 | 10 | 10 | 10 |
Colored TMA | 0.019 × 0.025 | 10 | 10 | 10 |
Four types of archwires were tested: SS (Permachrome resilient archwire, 3M Unitek), NiTi (super elastic, 3M Unitek), TMA (beta III titanium, 3M Unitek), and low-friction honeydew-colored TMA (Ormco, Glendora, Calif). All wires had a dimension of 0.019 × 0.025 in. A total of 30 archwire segments of each wire were used ( Table I ).
To measure roughness, photomicrographic examination of the bracket slots and wires was carried out by using a scanning electron microscope (SEM) (JSM-6380A, JEOL, Mumbai, India, with 10-20 kV).
A surface profilometer (SV, Mitutoyo, Tokyo, Japan) was used to measure wire and bracket slot roughness. This instrument has a stylus, which moves on the surface for the prescribed length and quantifies roughness as an Ra value. We evaluated 4-mm lengths of wire and 2 mm of the bracket slot surface for surface roughness. All brackets and archwire segments were evaluated by using the profilometer, and average Ra values were recorded for each bracket and archwire type.
Friction was measured with a universal testing machine (model 5582, Instron, Wycombe, Buckinghamshire, United Kingdom) at a room temperature of 25° in the dry state.
A total of 120 bracket-wire samples were studied ( Table I ). Each bracket was tested only once, and each wire specimen was drawn through 1 bracket only, to eliminate the influence of wear. Thus, for each bracket-archwire combination, the test was carried out 10 times, and the average was recorded.
Before testing, an experimental model was prepared by using a 150 × 20 × 3-mm SS plate, on which brackets were bonded with Araldite epoxy resin adhesive (Bostik, Leicester, United Kingdom). Each bar had a line scribed in the midline, parallel to the long axis, to act as a guide for reproducible bond position and as a vertical when compared with the plumb line while testing ( Fig 1 ). To position the brackets accurately on SS plate, a jig was prepared by using 0.021 × 0.028-in SS wire, as described by Thomas et al ( Fig 1 ).
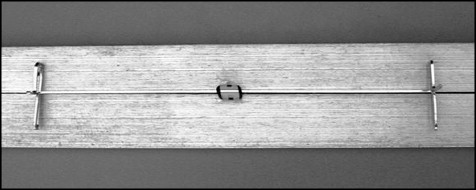
The whole bracket-wire assembly was then positioned vertically in the jaws of the floor-mounted testing machine ( Fig 2 ). The 10-N load cell was calibrated between 0 and 10 N, and the archwires were drawn through the brackets as the crosshead moved up and down at a rate of 0.5 mm per minute. The resulting frictional force was recorded on a computer in the form of a force-distance graph. Peak values in the graphs represented static friction. Similarly, friction was measured and recorded on a graph for all bracket and archwire combinations.
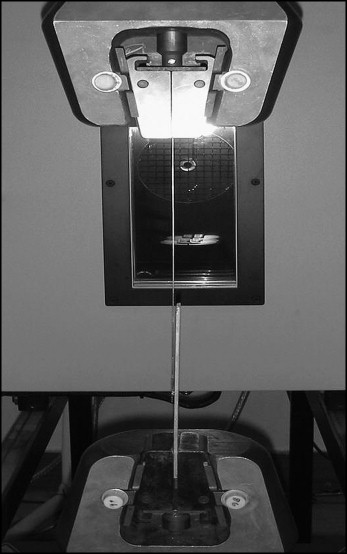
Statistical analysis
Descriptive statistics, including means, standard deviations, and minimum and maximum values were calculated for each bracket-archwire combination. The data were stored on a personal computer and submitted to statistical analysis.
The results were examined by using analysis of variance (ANOVA). For the post-hoc test, the Mann-Whitney U test was used, and the Bonferroni adjustment was applied. The level of significance for all tests was set at P <0.05. The data were tabulated and analyzed with SPSS software (version 10, SPSS, Chicago, Ill).
Results
SEM examination of bracket slots magnified at 1000 times showed the smoothest surface with the ceramic gold-palladium slot bracket followed by the SS bracket ( Fig 3 ). The traditional ceramic bracket surface was roughest.

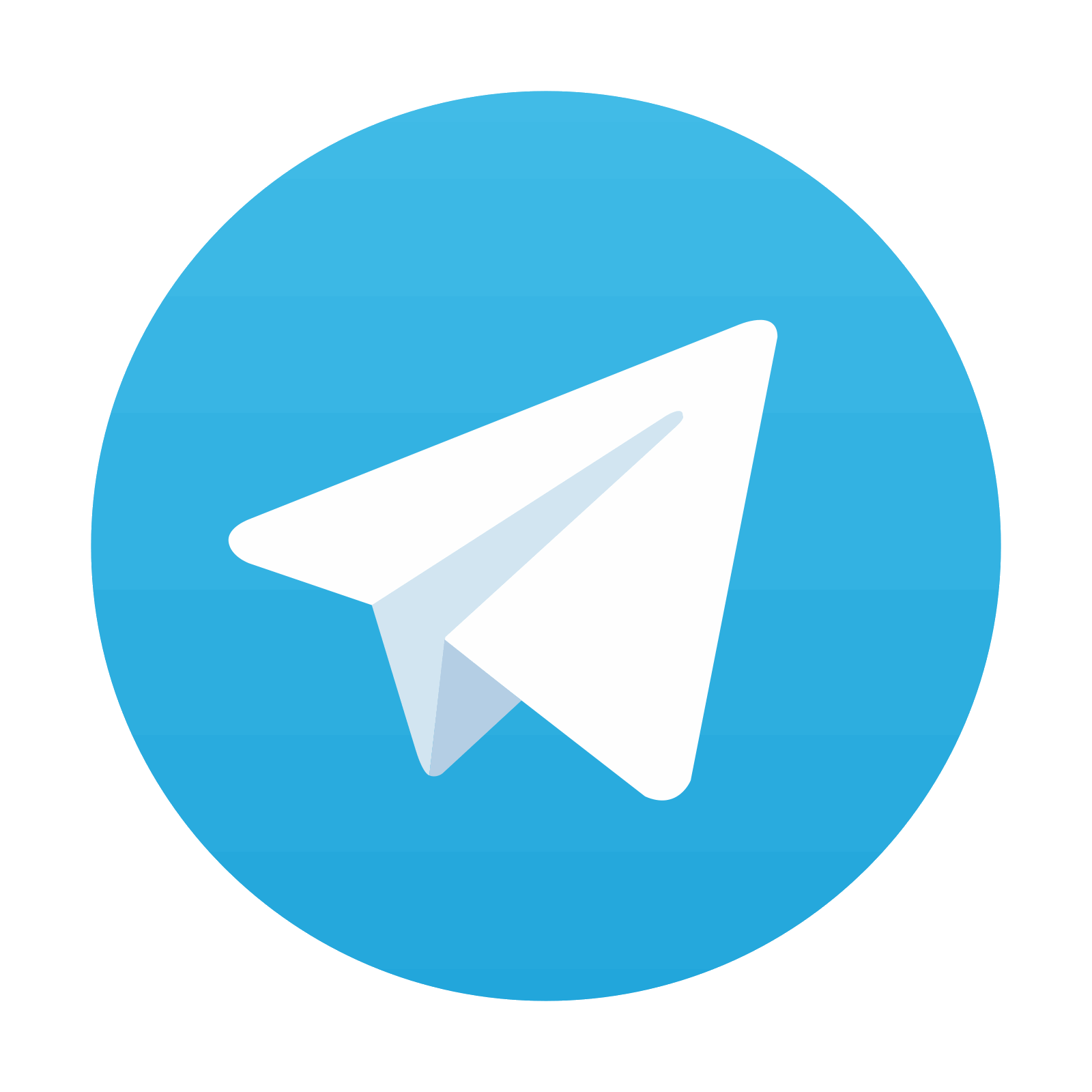
Stay updated, free dental videos. Join our Telegram channel

VIDEdental - Online dental courses
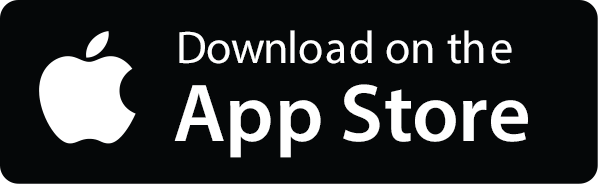

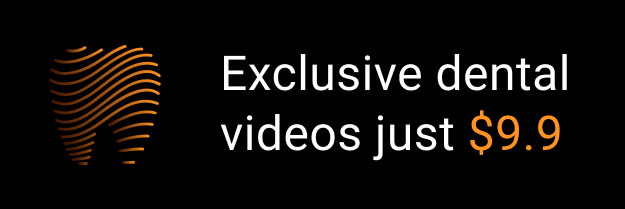