CHAPTER 14 Stage III: how it works
Objectives
Indeed, having exploited all the advantages of free tipping early in treatment, it is imperative that Tip-Edge should have a reliable uprighting and torquing mechanism, well beyond the capability of conventional brackets. Without this, it would be unable to match the finishing precision for which the straight-wire appliance has set the standard. That the Tip-Edge appliance has this capability is due to the use of rectangular wire in an entirely new way, which is unique in orthodontics.1 For reasons which will be fully explained, it has the intrinsic capability to produce a more accurate finish than existing bracket systems. To aid understanding, this and the hitherto established method of torquing with rectangular archwires will be compared.
Limitations of conventional torquing
Although such a simple method may have served well over many generations, within its self-imposed limits, it is fundamentally flawed in one major area. Primarily, this is because the active component in torque production is the archwire itself, which is effectively acting as a spring. The rectangular wire is therefore required to provide the two-fold function of actively torquing those teeth requiring correction, while at the same time offering three-dimensional stability to the remainder. Combining these two conflicting functions in a single archwire is a physical impossibility. Many world respected researchers have identified and tried to address the problems of the unwanted reciprocals, whereby active torque imparted to a single unit, or quadrant, will inevitably impart unwanted secondary torque reactions in adjacent units, or groups of teeth, resulting in some ‘round tripping’.2–13
Lastly, there is the question of archwire size. It is customary, in the majority of straight-wire techniques, not to exceed archwires of .019 × .025 inch, within a standard .022 × .028 inch bracket slot. This is partly to limit the active forces fed to a tooth by too heavy an archwire, but also to allow ease of insertion and removal. This degree of tolerance will equate to nearly 10 degrees of ‘torque slop’ between archwire and bracket slot.14 Although evidently regarded as a physiological safety feature, it may nonetheless result in up to 10 degrees of undertreatment, unless compensated by individualized torque adjustment in the archwire, or a modified torque prescription in the bracket itself.15
How does Tip-Edge torque?
It is essential first to understand that a Tip-Edge bracket cannot be torqued by an active archwire in the conventional manner, even with a fully closed bracket slot. Examination of the design of the bracket will explain why (Fig. 14.1). The intact upper and lower finishing surfaces in each bracket (see Fig. 3.2) are offset from one another, and are therefore never directly opposed. Insertion of an actively torqued rectangular archwire will therefore elevate one finishing surface and depress the other. In effect, the torquing effort in the archwire will have dispersed, by increasing the vertical dimension within the Tip-Edge slot. The net result will be a relapse of root uprighting in the mesio-distal direction, rather than any third order torque imparted to the root (Fig. 14.2). This is known as ‘torque escape’.
Originally, with the Rx-1 bracket, the Side-Winder spring provided the auxiliary force and this was the first time in orthodontics that an auxiliary spring, acting in the tip plane, had been shown to generate third order torque (those with an interest in the underlying mathematics are referred to Parkhouse & Parkhouse16). While the method might have appeared cumbersome, since it required a Side-Winder for each individual bracket, the Plus bracket has revolutionized Stage III by eliminating the springs altogether. Now, all torquing and tipping can be carried out more simply and less obtrusively with a nickel–titanium auxiliary archwire, threaded through the deep tunnels, beneath the overall security of a stainless rectangular main archwire. This contains t/>
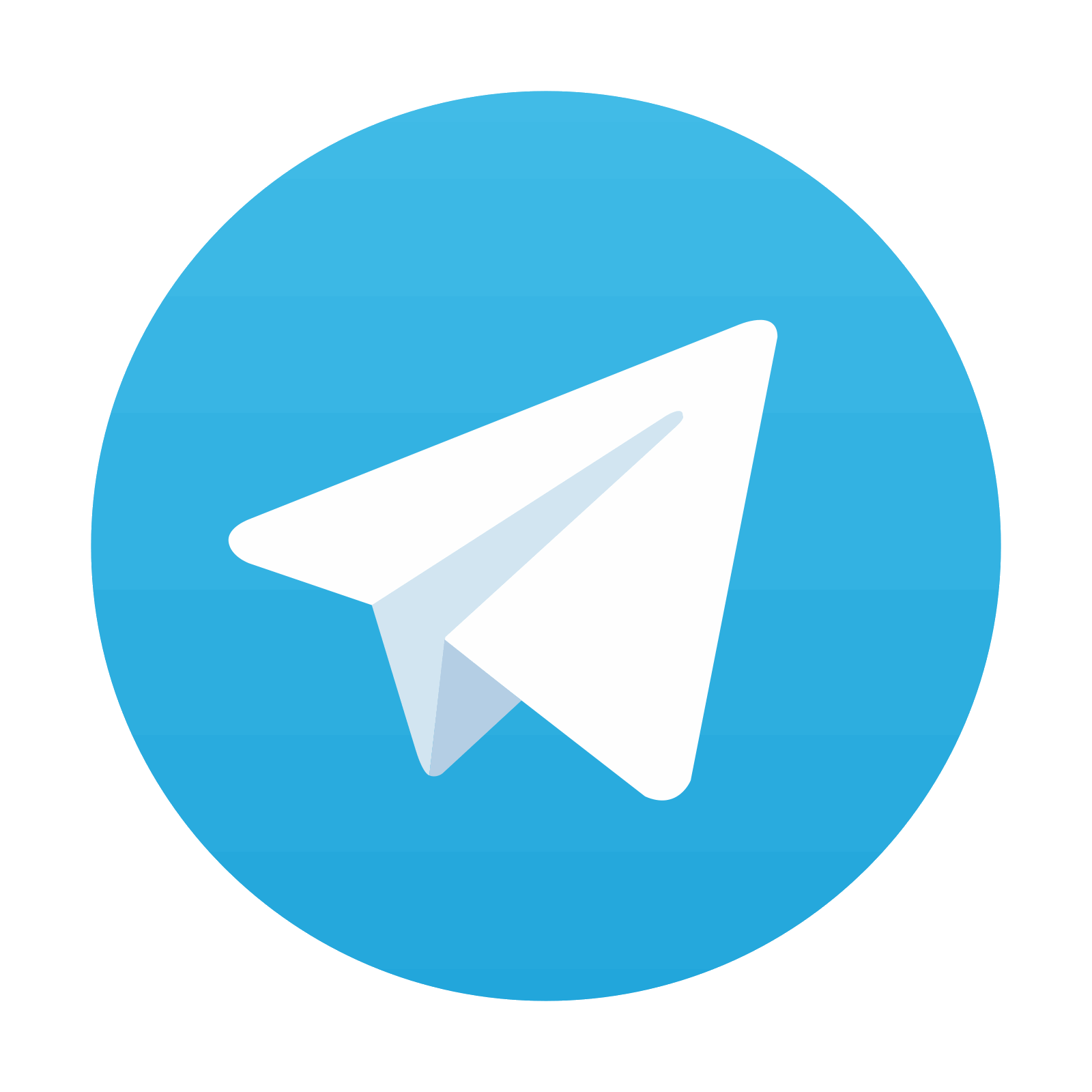
Stay updated, free dental videos. Join our Telegram channel

VIDEdental - Online dental courses
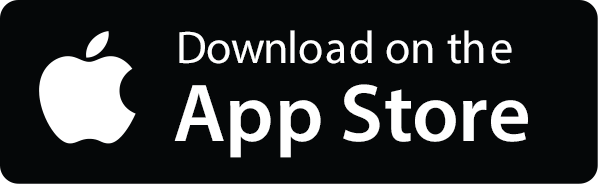
