Highlights
- •
Against a hard antagonist, glass-ceramics exhibit moderate wear but extensive subsurface fracture.
- •
Resin composites show large wear craters with the absence of subsurface damage.
- •
The polymer-infiltrated reinforced-glass material displays large wear craters and severe subsurface damage.
- •
Under extreme occlusal loading, restoration failure can occur from excessive wear, as well as by fracture and chipping.
Abstract
Objective
Most previous work conducted on the wear behavior of dental materials has focused on wear rates and surface damage. There is, however, scarce information regarding the subsurface damage arising from sliding contact fatigue. The aim of this study was to elucidate the wear mechanisms and the subsurface damage generated during sliding contact fatigue in 5 contemporary CAD/CAM materials against a zirconia indenter.
Methods
Forty discs (Ø12 mm, 1.55 mm thick) were cut out of IPS e.max CAD (e.CAD), Suprinity PC (SUP), Enamic (ENA), Vitablocs Mark II (VMII) and Lava Ultimate (LU) blocks and mirror polished. After cementation onto a dentin-like composite, off-axis mouth-motion cycling was conducted with a spherical zirconia indenter ( r = 3.18 mm) in water (200 N load, 2 Hz frequency) for 5 different cycling periods (10 2 , 10 3 , 10 4 , 10 5 , 10 6 cycles, n = 8). Analysis of the wear scars was conducted using light-microscopy, scanning-electron-microscopy and optical profilometry. Subsurface damage was assessed using sagittal and transverse sections of the samples.
Results
Fatigue wear mechanisms predominated in glassy materials (e.CAD, SUP, VMII), accompanied by extensive subsurface damage, whereas abrasive wear mechanisms were responsible for the large wear craters in the resin composite (LU) with an absolute absence of subsurface fracture. A combination of both mechanisms was observed in the polymer-infiltrated reinforced-glass (ENA), displaying large wear craters and severe subsurface damage.
Significance
Well-controlled laboratory simulation can identify wear and subsurface damage susceptibility of various classes of restorative materials. Both wear and subsurface fracture are determining factors for the long-term success of restorations.
1
Introduction
Computer-aided-design and computer-aided-manufacturing (CAD/CAM) technologies have revolutionized the fabrication of dental restorations, not only by an immense reduction in the laboratory working times, but also by opening the door to a wide spectrum of new materials. Originally designed for the machining of hard ceramics, computer assisted technologies have expanded to almost every restorative material in modern dentistry, encompassing feldspathic ceramics and glass-ceramics and, more recently, also resin composites. Parallel to this strong industrial development, intensive research has been done by dental material’s scientists in order to better characterize and predict the mechanical behavior of these newly introduced materials. This is reflected by the vast amount of literature published in the field over the last few years focusing on their microstructure [ , ], strength [ ], fracture toughness [ , ] and wear behavior [ ]. This latter property has been considered as a clinical predictor of the material’s resistance to masticatory forces and oral attrition. Still, a direct correlation of in vitro results to clinical data has shown to be strongly dependent upon the material in question and the testing method employed [ ]. Therefore, data from the literature tend to be difficult to assess, preventing a direct comparison of their findings and limiting the application of their conclusions in clinical scenarios.
Wear is defined as a gradual loss of material originated by the mechanical interaction between two contacting surfaces that are in relative motion under a given load [ ]. Physical separation during the process occurs mainly due to microfracture and chemical dissolution [ ], creating telltale marks on the worn surface characteristic to the wear mechanisms that originated them. Accordingly, four main types of wear have been described: adhesive-, abrasive-, fatigue- and corrosive wear [ , ]. Abrasive wear is the most commonly observed wearing type in dental restorative materials, generally occurring under plastic contacts. Its main mechanism is ploughing [ ], with material removal by the indentation of asperities or hard particles into the softer surface of the antagonist [ ]. As a consequence, abrasive grooves are formed in the direction of sliding. These wear marks depend on the nature of the indented material and the ploughing mechanism, varying from microcutting in ductile surfaces, to microfracture in brittle materials [ ]. Fatigue wear, on the other hand, occurs under repeated elastic contacts, with crack propagation from microdefects in the sliding path of the indenter as the main mechanism. The friction force caused by sliding introduces shear stresses at the contact interfaces, whereas compressive stresses are generated ahead of the motion and tensile stresses develop at the trailing edge of the sliding indenter [ ]. Thus, nucleation and propagation of cracks is favored by the cyclic motion, eventually causing the cracks to reach the surface and leading to delamination and material loss or spallation in the surrounding areas [ ].
In the subsurface of the material, repeated cycling favors the development and growth of partial cone cracks, which are generated by tensile stresses at the trailing edge of the indenter and further driven by hydraulic pumping of water into the cracks [ , ]. Their morphology, density and crack-to-surface angles are closely related to the coefficient of friction at the interface [ , ], as well as to the fracture toughness of the indented material [ ]. Hence, materials with higher toughness will exhibit enhanced resistance to propagation of partial cone cracks during sliding contact fatigue. On the other hand, higher coefficients of friction lead to steeper penetration angles, as well as higher crack densities [ ]. The continuous growth of this type of cracks into the bulk of the material, especially at high penetration angles, can seriously jeopardize the final strength of the restoration by acting as stress concentrators and ultimately as fracture origins [ ].
Most literature published over the years on the wear behavior of CAD/CAM materials has been focusing on the wear rates and the surface damage caused by different indenters (natural teeth, steatite, metals, oxide ceramics, etc.) under diverse testing conditions (i.e. two- or three-body wear). There is, however, scarce information regarding the underlying damage arising from sliding contact fatigue, which seems to be a determining factor for the long-term success of these restorative materials [ ]. Moreover, only limited descriptions of the subsurface damage modes and the resistance against crack propagation of newly introduced materials, such as polymer-infiltrated reinforced-glass networks (PIRGN) or lithia-based glass-ceramics, is available. Therefore, the goal of the present study was to characterize the surface and subsurface damage mechanisms in five contemporary CAD/CAM materials subjected to cyclic sliding contact fatigue against a spherical zirconia indenter. Tests were conducted in water at a relatively high load in order to allow a complete development of partial cone cracks at the trailing edge of the indenter. Their growth, as well as the concomitant surface degradation, was successively followed up to 1 million cycles.
2
Materials and methods
2.1
Sample preparation
Five ceramic-containing dental materials currently in use for milling CAD/CAM restorations were selected from a wide range of material classes. They include two lithia-based glass-ceramics (IPS e.max CAD, Ivoclar-Vivadent, Schaan, Lichtenstein; and Suprinity PC, Vita Zahnfabrik, Bad Säckingen, Germany), a feldspar-reinforced aluminosilicate glass (Vitablocs Mark II, Vita Zahnfabrik), a polymer-infiltrated reinforced-glass network, PIRGN (Enamic, Vita Zahnfabrik), and a pre-polymerized nanoparticle/nanocluster resin composite (Lava Ultimate, 3 M, St. Paul, MN, USA). The blocks with initial dimensions 14 × 12 × 18 mm 3 (e.g. C14, I14) were ground round (Ø = 12 mm) using diamond lapping and subsequently cut with a precision diamond saw (IsoMet 1000, Buehler, Lake Bluff, IL, USA) into 1.80 mm thick slices under constant water irrigation. Obtained discs were then ground parallel and fine polished down to 1 μm diamond lapping plates and diamond suspensions on a power head polisher (Ecomet 4, Buehler). Forty specimens, with final thicknesses of 1.50 ± 0.05 mm, were prepared for each material. One of the sample’s surfaces was etched using 5% hydrofluoric acid (Ceramic Etch, Vita Zahnfabrik) for 20 s (IPS e.max CAD and Suprinity) or 60 s (Vitablocs Mark II and Enamic), except for Lava Ultimate samples, which were sandblasted with 30 μm Al 2 O 3 particles at 2 bar for 15 s. A silane coupling agent (Monobond Plus, Ivoclar-Vivadent) was applied onto the etched surfaces, while a universal adhesive (Scotchbond Universal, 3 M) was used for Lava Ultimate. The specimens were cemented onto previously hydrated (30 days storage in distilled water) glass-fiber reinforced epoxy resin rods (Ø25 × 15 mm, Epoxyglass G10, Acculam, Accurate Plastic, Yonkers, NY, USA) using one of two resin-based dual polymerizing luting agents: Multilink Automix (Ivoclar-Vivadent) for silanized surfaces and RelyX Ultimate (3 M) for Lava Ultimate. Photopolymerization of the luting agent was carried out by exposing the ceramic/cement interface to a LED curing light with an irradiance of 850 mW/cm 2 for 40 s for 4 consecutive times from different directions (Ultra Lume LED 5, Ultradent, South Jordan, UT, USA). After cementation, the ceramic/cement/G10 assemblies were stored in distilled water at 37 °C for 7 days for continued polymerization and hydration of the cement.
2.2
Sliding contact fatigue
Frictional sliding testing was conducted in an electrodynamic biaxial mouth-motion simulator (Elf-3300, EnduraTEC, TA Instrument, Minnetonka, MN, USA) using a spherical 3Y-TZP indenter ( r = 3.18 mm, surface roughness R a = 0.254 μm) at 200 N load and 1.5–2.0 Hz frequency in distilled water. The test set-up is displayed in Fig. 1 . Specimens were mounted onto a tilted block (30°) in order to generate off-axis loading of the indenter. The sliding cycle consisted of an initial contact of the indenter with the specimen’s surface at which the maximum load was transferred while sliding down for about 1 mm. After unloading, the indenter was lifted off of the specimen’s surface while the specimen was returned to its original position. Specimens of each material where randomly divided into 5 subgroups ( n = 8) and subjected to fatigue testing for a different number of cycles: 10 2 , 10 3 , 10 4 , 10 5 or 10 6 , after which the specimen was removed from the machine and the G10 was carefully cut, leaving a thin layer of G10 attached to the ceramic/cement disc.

2.3
Light microscopy and SEM analysis
The surface appearance and dimensions of the generated wear scars were analyzed under the light stereomicroscope (MZ-APO, Leica, Wetzlar, Germany) using reflected light. The presence of a polished surface surrounding the wear crater allowed a neat observation of its boundaries, as well as the surface features of the partial cone cracks. One specimen of each material tested for 10 4 cycles was selected for SEM analysis of the wear crater (TM4000Plus Tabletop Microscope, Hitachi, Tokyo, Japan). An additional sample of these subgroups was carefully removed from the remaining G10 and fine polished on the cementation surface. The wear scar was then analyzed under transilluminated light in the stereomicroscope and the characteristics of the subsurface damage (crack systems) where highlighted by varying the direction and incidence angle of the light source.
Two further samples of each material at 10 4 cycles were selected and embedded in clear epoxy resin and then sectioned saggitally or transversally (i.e. parallel or normal to the direction of sliding), slightly away from the wear scar [ ]. The cross-sectioned samples were polished up until the half of the fatigue scar was reached and then fine polished down to 1 μm diamond suspension. The features of the partial cone cracks in both planes were assessed using the stereomicroscope under transilluminated light.
2.4
Optical profilometric analysis
The dimensions of the wear scars at each cycling interval were examined using a high-resolution confocal optical profilometer (CT 100, CyberTechnologies, Eching, Germany), with a vertical resolution of 0.02 μm and measuring with XY step sizes of 5 μm. The width, length and maximum depth of the wear scars, as well as the volume loss of five samples per cycling interval per material were measured. One-way analysis of variance (ANOVA) was used to analyze the data (Minitab 17, Minitab Inc., State College, PA, USA). Statistical differences between groups at 5% significance level were determined using the Tukey’s post-hoc test.
3
Results
Results for the wear behavior of the different tested materials are displayed in Figs. 2 and 3 , as well as in Table 1 . In general, the 3 ceramic materials (Vitablocs Mark II, IPS e.max CAD and Suprinity PC) exhibited similar wear patterns with significantly smaller wear scars relative to Enamic (PIRGN) and Lava Ultimate, especially following prolonged cyclic sliding contact ( Fig. 2 ). Interestingly, an initial run-in stage, with higher wear rates, was observed between the first two measurement intervals, i.e. 10 2 –10 3 cycles for all materials, with the exception of Vitablocs Mark II ( Fig. 3 ). Indeed, a closer examination of Fig. 2 revealed a strong increase in the width of the wear scars between these two intervals, corresponding well with the measured increment in all wear parameters (width, depth and volume loss) shown in Fig. 3 and Table 1 . In addition, despite marked differences in microstructure, strength and toughness among the 3 ceramic materials [ ], the overall volume loss in these materials was similar, being an order of magnitude less than that of the PIRGN and Lava Ultimate ( Table 1 ). Although the initial volume of the PIRGN was far greater than that of Lava Ultimate, the latter exhibited a much higher steady-state wear rate, leading to similar long-term volume losses in the 2 materials.


Material | 10 2 cycles | 10 3 cycles | 10 4 cycles | 10 5 cycles | 10 6 cycles |
---|---|---|---|---|---|
Enamic | 0.005 A (0.0007) | 0.044 A (0.002) | 0.138 A (0.012) | 0.319 A (0.066) | 0.463 A (0.155) |
Lava Ultimate | 0.0007 B (0.0002) | 0.0053 B (0.0003) | 0.049 B (0.001) | 0.311 A (0.019) | 0.68 A (0.034) |
Vitablocs Mark II | 0.006 A (0.003) | 0.009 B (0.005) | 0.011 C (0.002) | 0.025 B (0.007) | 0.046 B (0.009) |
IPS e.max CAD | 0.0005 B (0.00005) | 0.007 B (0.0004) | 0.012 C (0.003) | 0.024 B (0.013) | 0.029 B (0.005) |
Suprinity PC | 0.0006 B (0.0002) | 0.011 B (0.004) | 0.019 C (0.009) | 0.024 B (0.013) | 0.042 B (0.015) |
To shed some light on the wear mechanisms, damage sustained in each class of material has been examined in detail and the results are shown in Fig. 4 through Fig. 8 . An important surface degradation was observed for the feldspar reinforced glass, with material spalling and large herringbone cracks at the trailing edge of the indenter ( Fig. 4 a–c), whereas surface damage in the PIRGN showed a combination of resin matrix abrasion and fracture and partial removal of the feldspathic reinforced glass network ( Fig. 5 a, b). Degradation in the resin composite samples was limited to abrasive wear patterns, displaying smooth surfaces crossed by plough marks and worn off of the nanoparticles and clusters ( Fig. 6 a, b). Fatigue wear mechanisms dominated in the glass-ceramics, with surface damage arising predominantly from subsurface herringbone cracks at the tail of the indenter’s path and fully developed cone cracks at the arresting point ( Figs. 7 a–c and 8 a–c). More severe fracture features were observed at the surface of Suprinity PC samples, than in their IPS e.max CAD counterparts.

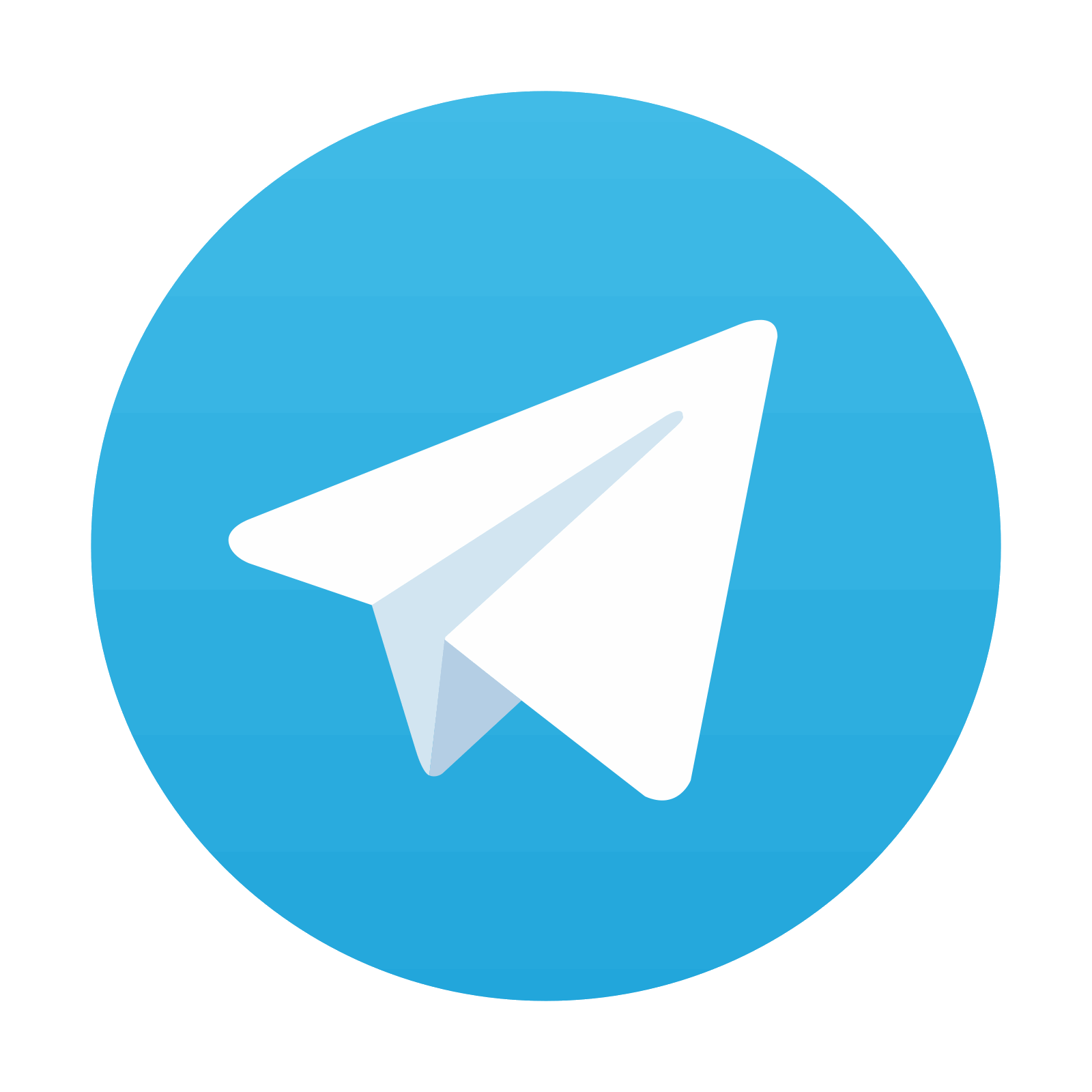
Stay updated, free dental videos. Join our Telegram channel

VIDEdental - Online dental courses
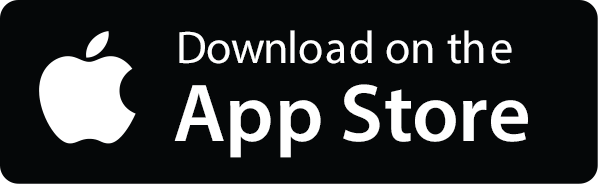

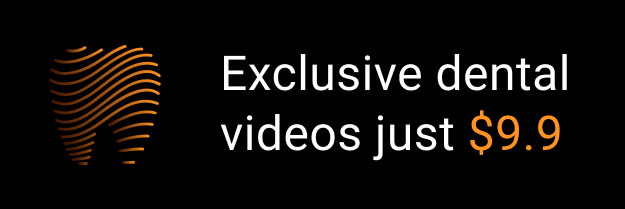