Abstract
Objectives
The veneering process of frameworks induces residual stresses and can initiate cracks when combined with functional stresses. The stress distribution within the veneering ceramic as a function of depth is a key factor influencing failure by chipping. This is a well-known problem with Yttria-tetragonal-zirconia-polycrystal based fixed partial dentures. The objective of this study is to investigate the influence of veneer thickness on the stress profile in zirconia- and metal-based structures.
Methods
The hole-drilling method, often used for engineering measurements, was adapted for use with veneering ceramic. The stress profile was measured in bilayered disc samples of 20 mm diameter, with a 1 mm thick zirconia or metal framework. Different veneering ceramic thicknesses were performed: 1 mm, 1.5 mm, 2 mm, 2.5 mm and 3 mm.
Results
All samples exhibited the same type of stress vs. depth profile, starting with compressive at the ceramic surface, decreasing with depth up to 0.5–1.0 mm from the surface, and then becoming compressive again near the framework, except for the 1.5 mm-veneered zirconia samples which exhibited interior tensile stresses. Stresses in the surface of metal samples were not influenced by veneer thickness. Variation of interior stresses at 1.2 mm from the surface in function of veneer thickness was inverted for metal and zirconia samples.
Significance
Veneer thickness influences in an opposite way the residual stress profile in metal- and in zirconia-based structures. A three-step approach and the hypothesis of the crystalline transformation are discussed to explain the less favorable residual stress development in zirconia samples.
1
Introduction
The manufacture of crowns and fixed dental prostheses (FDPs) generates residual stresses within the veneering ceramic and framework during the cooling process. These “locked-in” stresses add to functional loads and are an important predictive factor for the mechanical behavior of restorations, as compressive stresses reinforce ceramic and tensile stresses facilitate the initiation and the propagation of cracks. Knowledge of the residual stress distribution within the veneering ceramic as a function of depth is a key factor for understanding and predicting chipping and delaminations. Such fractures are reported as an important cause of short-term clinical failure with Yttria-tetragonal-zirconia-polycrystal (Y-TZP) based FPDs . These complications are more frequent in zirconia-based restorations than in ceramic-fused-to-metal structures (PFMs) .
Stress profile in the veneering ceramic is generated by the successive effects of the thermal gradients occurring during the cooling/solidification period of the veneer liquid phase sintering process, and the mismatch in thermal expansion properties between core and veneering ceramic . In the case of ceramic fused to metal frameworks, the thermal expansion coefficient (CTE) of the ceramic is generally slightly lower than the framework so that during cooling from T g to room temperature, interior compressive stresses are developed within the ceramic near the framework, with compensating tensile stresses developed within the framework. The second parameter influencing stress profile is thermal gradients, which induce non-uniform solidification, from the surface to the center, thereby causing contraction mismatch within the ceramic. The resulting residual stresses are compressive in the surface of the veneering ceramic, the magnitude of these stresses decreasing with depth and being influenced by the cooling rate around the glass transition temperature T g due to the effect of viscoelastic parameters . Thermal gradients are determined by cooling rate but also by material thickness and conductivity.
The cooling rate dependence of stress profiles in veneering ceramics layered on different core materials has been studied through mathematical models and more recently through residual stress measurements in veneered metal and zirconia disk samples .
To author’s knowledge, the influence of veneering ceramic thickness on residual stress in metal and zirconia-based structures has been not well described. However core/veneer thickness ratio and framework design is reported to influence all ceramic restorations reliability, particularly Y-TZP restorations . Ensuring an optimal support to veneering ceramic with an anatomical framework and avoiding excessive thickness is recommended to prevent chipping. Swain calculated the independent influence of the cooling rate, thickness and thermal expansion coefficient on residual stresses profile . His 2D mathematical model was a bilayer composed of glass ceramic, alumina or zirconia substrates. Among the three factors studied, thickness predominated as the most influencing parameter. He found that thick layers of veneering ceramic on framework with low thermal diffusivity, such as Y-TZP, promotes the development of high tensile interior residual stresses which may result in chipping. Bonfante et al. studied stresses in a 3D zirconia crown model. He observed slight tensile stress fields at the interface of the core and the veneer layer of both standard and modified core systems characterized by different veneer thicknesses. But models are limited by the difficulty encountered when mimicking such a complex thermal process as the veneer firing procedure. Particularly the cited models did not account for thermal gradients and variations of thermo-physical properties of ceramic in the glass transition range.
A residual stress measurement method is now available for dental applications . The hole-drilling method, a standardized method developed for industrial applications , was adapted for measuring residual stresses in the veneering ceramic. This method is based on the removal of some stressed material and the measurement of the resulting deformations in the adjacent material . The deformations are measured on the surface, typically using strain gages, from which the residual stresses can be calculated. Stresses are calculated from surface to depth, typically with 0.1 mm steps, and giving a stress profile within a 1.2 mm depth. This method was used previously to study the influence of cooling rate on residual stress profile in veneered metal and zirconia samples .
The first objective of this study is to investigate the veneer thickness dependence of stress profiles in PFM and Y-TZP structures using the hole-drilling method. A second objective is to understand how the veneer thickness of zirconia-based-restorations can influence their mechanical behavior, comparing stress profile in metal- and zirconia-based structures.
2
Materials and methods
2.1
Specimen preparation
Bilayered disc samples composed of veneering ceramic sintered either on Y-TZP framework (VZr, 10 samples), or on dental CoCr alloy framework (VM, 10 samples) were manufactured following standard dental laboratory procedures and manufacturer’s recommendations. CoCr core discs (Duceralloy C, DeguDent GmbH, Hanau, Germany), 20 mm diameter, were cast and sequentially ground with 80-grit, 180-grit and 500-grit silicon carbide discs (Struers LabPol polishing machine, Copenhagen, Denmark) to a thickness of 1.0 ± 0.02 mm. The surface to be veneered was sandblasted at 4 bars with 125 μm alumina particles.
Y-TZP core discs were cut out of a pre-sintered Vita In-Ceram YZ blocks (Vita Zahnfabrik, Bad Säckingen, Germany), were rounded by polishing, and densely sintered at 1530 °C for 120 min with heating rate 10 °C/min, and heating time 149 min (Zircomat furnace, Vita Zahnfabrik, Bad Säckingen, Germany). The sintered Y-TZP discs were ground and dimensioned in the same way as CoCr, but not sandblasted.
CoCr and Y-TZP discs were veneered respectively with feldspar veneering ceramic: Vita VM 13 ( T g ∼ 560–565 °C, T s ∼ 635 °C, following the manufacturer) and Vita VM9 ( T g ∼ 600 °C, T s ∼ 670 °C, following the manufacturer) (shade 3M2) (Vita Zahnfabrik, Bad Säckingen, Germany). A Vita Vacumat 4000 Premium furnace (Vita Zahnfabrik, Bad Säckingen, Germany) was used for all firing procedures, as summarized in Table 1 . All samples were baked on the same ceramic mesh-tray.
Starting T (°C) | Pre-drying t (min), closing t | Heating rate (°C/min) | Heating t (min) | Firing T (°C) | Holding t (min) | Vacuum holding t (min) | |
---|---|---|---|---|---|---|---|
Alloy core oxidation | 600 | 3 | 75 | 4 | 900 | 2 | 4 |
Vita VM13 Opaque | 600 | 2 | 75 | 4 | 900 | 1 | 4 |
Vita VM13 Dentin | 600 | 8 | 50 | 6 | 900 | 6 | 6 |
VM finished | 600 | 8 | 50 | 6 | 900 | 6 | 6 |
Y-TZP core regeneration firing | 500 | – | 100 | 5 | 1000 | 15 | – |
Vita VM9 Effect bonder | 500 | 6 | 75 | 6 | 950 | 1 | 6 |
Vita VM9 Dentin | 500 | 6 | 55 | 7.27 | 910 | 4 | 7.27 |
VZr finished | 600 | 8 | 50 | 6 | 900 | 6 | 6 |
The sandblasted surfaces of the VM samples were oxidized before ceramic layering according to the manufacturer’s guidelines. Vita VM 13 Opaque ceramic powder mixed with Vita VM opaque fluid was applied to the substructure with a brush, and fired to enhance the bond to the alloy surface. Three layers of dentin ceramic were successively fired. This layering technique promotes adhesion between opaque and dentin ceramic and reproduces the dental laboratory procedure. Samples were sequentially ground with 80-grit, 180-grit and 500-grit silicon carbide discs to obtain either a 1.0 mm ( n = 2), a 1.5 mm ( n = 2), a 2 mm ( n = 2), a 2.5 mm ( n = 2) or a 3.0 mm ( n = 2) thick ceramic layer.
For the VZr samples preparation, the Y-TZP discs were exposed to a “regeneration firing”, which is a final thermal treatment of the core to reverse any phase transitions in the zirconia due to the grinding procedures. A thin coat of Vita VM 9 Effect Bonder was applied and fired on the surface to be veneered. Then, Vita VM 9 Base Dentin was progressively layered on the effect bonder and samples were dimensioned in the same way than VM samples.
After final polishing, all specimens were exposed one by one to a last firing cycle (see Table 1 ). This last firing cycle restores the residual stress profile through the veneering ceramic thickness. All samples were placed in the same position, on the center of the mesh-tray and of the furnace. They were tempered from 900 °C to room temperature by opening the furnace door, as typically performed in dental laboratories, and removed from the mesh-tray at 200 °C. In compliance with the manufacturer’s recommendations, the firing temperature was maintained 6 min in place of 1 min in order to reach 900 °C within the framework.
2.2
Hole-drilling method
2.2.1
Strain gage rosette installation
A specialized six-element Type C rosette (N2K-06-030RR-350/DP, Vishay, Malvern, PA, USA) was installed on the center of the veneering ceramic surface. To promote the strain gage bond, the ceramic surface was prepared by etching with 10% hydrofluoric acid for 1 min, and was then cleaned for 5 min in an ultrasonic bath containing 90% alcohol. The strain gage rosette was installed with M-Bond 200 Adhesive (Vishay, Malvern, PA, USA), following the manufacturer’s instructions. The adhesive was allowed to cure overnight to ensure complete curing. The installation was monitored using an optical microscope.
2.2.2
Electrical measurement chain
The strains expected from the strain gages are very small and cannot be measured with sufficient accuracy using conventional industrial equipment. A specialized data acquisition system was therefore built where each strain gage was connected in a Wheatstone bridge circuit with 3 control gages (identical gages attached to an undisturbed sample). All gages and control rosettes were exposed to identical constant temperature conditions. Finally, the very low voltage measurements were performed with specific custom-built electronic equipment comprising a precision DC and AC current source 6221 (Keithley Instruments, Inc., Cleveland, OH, USA) and 3 Nanovoltmeters 2182A (Keithley Instruments, Inc., Cleveland, OH, USA). Filtered measurements were recorded on a computer using NI LabView software (National Instruments, Austin, TX, USA).
2.2.3
Temperature control
The specimens were placed in an aluminum container. After sample centering in the drilling machine, the container was filled with silicon oil to enhance drilling lubrication, thermal conductivity and electrical insulation. In addition, the silicon oil bath was thermally controlled and maintained at 36 °C ± 0.1 °C with a Eurotherm 3208 system (Eurotherm Ltd., Worthing, UK) to avoid the effects of any ambient temperature variations. Temperature at the sample contact was recorded with a thermocouple connected to NI LabView data acquisition system.
2.2.4
Hole-drilling
An Isel CAD-CAM machine (CPM 3020, Houdan, France) was used for the drilling procedure. To increase strain sensitivity, the maximum allowable hole diameter for the strain gage rosette type was performed with a 2.5 mm diameter cylindrical bur (Asahi Diamond Industrial Europe SAS, Chartres, France). The bur rotation speed was 19,000 rpm. A hole was cut at the center of the rosette in steps of 0.1 ± 0.01 mm, as measured by a Digimatic indicator (Mitutoyo Corporation, Kawazaki, Japan). Hole diameter and concentricity were checked after the experiment with an optical microscope and motorized micrometer, Micro Controle CV 78 (Newport, Irvine, CA, USA). The protocol of the hole-drilling method was designed to eliminate/minimize crack initiation through choice of drilling process, drill type and lubricant used. However, in the few cases where cracks had nevertheless occurred, abnormal large variations of microstrains were induced. If these were confirmed by optical microscopy, the sample was eliminated.
2.2.5
Strain measurements and residual stress calculation
Strain measurements were taken continuously during each step of the drilling procedure and for 10 min afterwards. This time allowed stabilization of any temperature fluctuations caused by the drilling process. The strain measurements were recorded in an Excel spreadsheet (Microsoft Corporation, Redmond, WA, USA). Mean values were evaluated for each strain gage based of the final 200 values (1 Hz acquisition) registered for each step. Mean strain measurements for each step were calculated from the values registered from the two samples of each group. The corresponding profiles of residual stress vs. depth from the specimen surface were then calculated according to ASTM Standard Test Method E837-08 using H-Drill software (Vishay, Malvern, PA, USA). For the rosette size used, the hole-drilling method can measure residual stresses to depths to 1.2 mm.
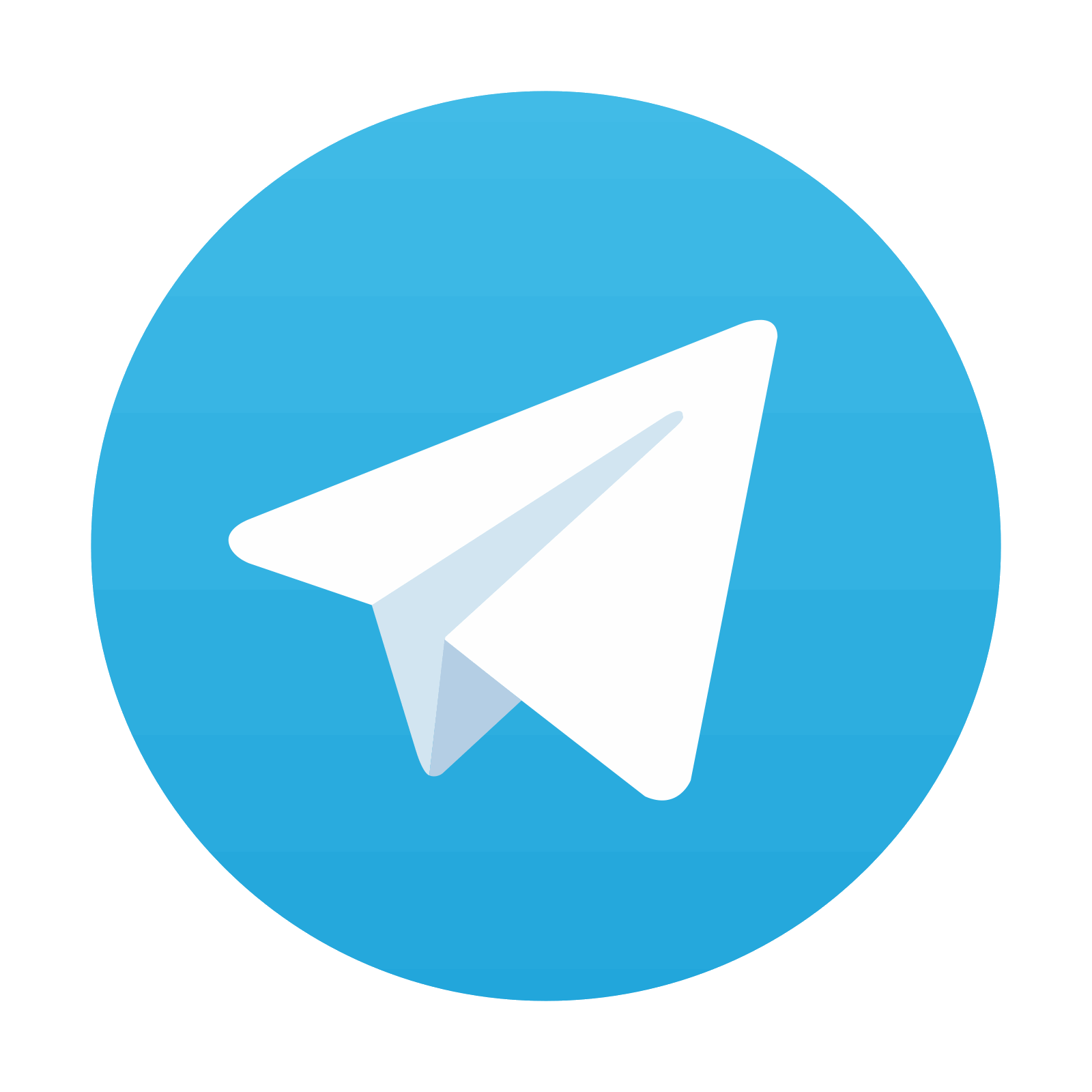
Stay updated, free dental videos. Join our Telegram channel

VIDEdental - Online dental courses
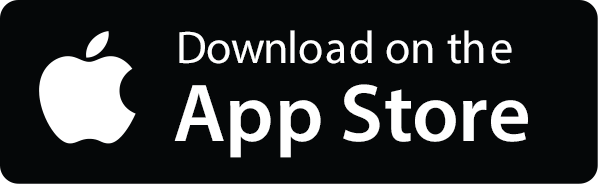
