Abstract
Objectives
We investigated the elastic properties of one dental restoration resin composite of common use, Venus Diamond, at submicrometer spatial resolution.
Methods
We performed both nanoindentation experiments with atomic force microscopy, and microindentation experiments with a traditional indenter setup. We also used scanning electron microscopy and energy dispersive X-rays spectroscopy to better understand the correlation between properties and microscopic structure and composition.
Results
With atomic force microscopy we obtained quantitative evaluation of the elastic modulus (10.8 ± 4.3 GPa), in agreement with the microindentation value (reduced modulus of 12.7 ± 2.0 GPa), and by microindentation we also obtained an hardness value (460 ± 109 MPa) compatible in turn with the nominal value provided by the material manufacturer ( H ∼ 578 MPa). The nanoindentation also revealed that no relevant difference in elasticity appears between the 5 and 10 μm diameter filler particles and the surrounding areas, showing an excellent uniformity of the composite. In support of this finding, compositional uniformity of the material was also observed by X-rays spectroscopy. We conclude that the composite contains prepolymerized particles.
Significance
We demonstrate that, in addition to reliable quantitative analysis, the high resolution and two-dimensional mapping capability of atomic force microscopy allows for advanced insights into the microstructure of the composite that are not accessible via traditional microindentation.
1
Introduction
In all the fields of science and technology the relationship between material structure and its properties is a critical issue for the desired functionality of a tool or device. Nowadays it is possible to investigate this relationship down to the nanoscale, and recently also the field of dental materials is undergoing extensive application of nanoscience and nanotechnology concepts . In this streamline, we have tried to explore the possible connections between structure and functionality of a dental restoration material on a submicrometric scale, especially focusing on the elastic mechanical properties. To this goal, we have selected one single dental resin composite of common use, on which we have already focused our attention recently , and have investigated its elastic modulus by means of both instrumented indentation, termed microindentation in the following, and atomic force microscopy (AFM) force–distance measurements, termed nanoindentation in the following. Recently, AFM nanoindentation has been claimed to be able to extract quantitative mechanical information from the samples, coupled with its inherently high spatial resolution of imaging. However, the validity of numerical data obtained by AFM is still an open issue . At the same time, the capability to measure mechanical properties with resolution similar to AFM topographic imaging on nanocomposite materials such as the currently used dental restoratives is promising. In this study we address both points, namely consistency of AFM mechanical measurements with those from traditional microindentation, and the possible use of the high AFM spatial resolution in nanoscale mechanical characterization. In particular, for our composite we make the hypothesis that a significant difference in elastic modulus between large fillers and filler–matrix interface regions exists. The experimental study has also been complemented with scanning electron microscopy (SEM) combined with energy-dispersive X-ray spectroscopy (EDS) microanalysis.
2
Materials and methods
2.1
Sample preparation
As the dental restorative material of interest we selected Venus Diamond (Heraeus Kulzer, Dübendorf, Germany), shortly VD in the following. VD belongs to the class of small particle hybrid composite materials sometimes also termed in more detail as midifill, since they contain both nanofillers and microfillers in a 5 nm–20 μm diameter range . The VD fillers are Barium Aluminim Fluoride glass, with 64% loading by volume . Four VD square specimens of ∼10 mm × 10 mm area and ∼1.5 mm thickness were prepared by compressing the composite paste into a polyethylene hollow matrix with an amalgam condenser and removing the excess material. The specimens were cured for 40 s with a blue (440–480 nm wavelength) LED lamp (Translux Power Blue, Heraeus Kulzer) with irradiance ∼1 W/cm 2 , stored in air and characterized three weeks after preparation.
In one case (see Fig. 3 d–f), in order to set the filler surface free from any overcoating resin matrix layer, which could affect the surface measurements carried out by AFM, the specimen was subjected to polishing. This was performed by a flat plate grinding–polishing station with 1 min steps of 600 grit SiC paper, 800 grit SiC paper, and 0.1 μm particle size diamond paste, subsequently, under current water flow.
2.2
SEM analysis
SEM measurements were carried out at 15 kV electron acceleration voltage with a JSM-6490LA (JEOL Ltd., Tokyo, Japan). The samples did not require conductive coating thanks to the low vacuum operation (2.5 × 10 −1 mbar). EDS was also performed for identification of the elemental atomic species in the material.
2.3
AFM imaging
The measurements were taken with a MFP-3D (Asylum Research, USA). The relative height maps were acquired in air in tapping mode, with silicon probes NSG10 (NT-MDT, Russia) with nominal spring constant and fundamental resonance frequency of ∼10 N/m and ∼250 kHz, respectively. Optimum scan size was estimated to be 30 μm, as representative of a typical surface area for early colonizing bacteria in vivo . Four specimens were measured in three different regions each ( n = 12). The roughness was evaluated from the AFM images as the root mean square (RMS) of the distribution of heights, to be used as a minimum limit of indentation depth to be applied for the microindentation experiments.
2.4
Microindentation
Instrumented indentation was performed on a NanoTest setup (Micro Materials Ltd., Wrexham, UK) with a Berkovich diamond indenter with nominal tip radius ∼50 nm, in a cabinet with constant temperature of 23 °C, under load–control, with 0.01 mN/s loading and unloading rate. The setup was first calibrated by five iterative indentations in fused silica (with maximum load F max increasing from 0.5 to 200 mN). Then, the samples were indented with the same procedure. For a given specimen, the indentation program was repeated four times on different regions (i.e. 4 × 4 = 16 indentation programs).
From selected raw data both the reduced modulus E r and the hardness H were extracted, after the Oliver–Pharr model based on the diamond area function (DAF) of the calibrated tip . To this goal the maximum indentation depth δ max should be high enough so that all microasperities on the surface are fully penetrated, which would otherwise lead to underestimation of E r and especially of H . In fact, the maximum load of the final (fifth) cycle in the program ( F max = 200 mN) corresponded to a δ max ∼ 5 μm, which is largely in excess of the AFM measured RMS roughness. On the other hand, with such a high penetration the diamond area function used does not describe the experiment accurately, since the actual indenter shape starts to be rather conical than a Berkovich . Therefore we decided to limit the postprocessing of raw data to the first two cycles of the program at lowest F max (up to 80 mN, n = 16 × 2 = 32 indentations), resulting in a δ max ∼ 2.6 μm, also well above the RMS roughness.
2.5
AFM nanoindentation
For nanoindentation, i.e. force–distance curves, the same AFM instrument as above was used, yet operated in contact mode in liquid. Liquid environment allowed to remove the instabilities and spurious signals associated to non-specific adhesion due to ambient moisture. We worked mainly in water. In some cases, to ensure that the force–distance curves were not affected by electric force due to static charging , we worked in an aqueous solution of 1× phosphate buffer saline (PBS). To significantly indent the composite (nominal hardness of 578 MPa ), probe model NSG20 (NT-MDT) was chosen, with nominal spring constant and fundamental resonance frequency of 30–90 N/m and 300–600 kHz, respectively. Each force–distance curve (1024 sampling datapoints) was carried out with a vertical piezo extension of 1 μm, in an approach-retract closed loop at 1 Hz frequency, with F max between 700 and 900 nN. On the different specimens, several 2D maps of 40 × 40 force–distance curves were acquired, called each a force–volume (FV) data set, evenly distributed on scan areas of between 8 μm × 8 μm and 30 μm × 30 μm.
From these FV data set the maps of contact stiffness S were first extracted, defined as the slope of the unload part of the force–indentation curve between 50% and 95% of F max . From one of these representative maps, the elastic modulus E of the samples was also extracted from a limited number of representative force–indentation curves, by fitting to the Hertz model of contact , on assumption of elastic modulus of 180 GPa and Poisson’s ratio of 0.3 for the silicon probe. Since the maximum nanoindentation depth was always ≤10 nm and the nominal tip apex radius was also 10 nm, we assumed the nanoindenter tip to be a sphere.
To assign both the E value and its uncertainty, we used a method already adopted in Ref. . Namely, for the central E value some force–distance curves with S value close to the observed distribution mean S mean were fitted, and the respective values averaged to obtain E mean . For the uncertainty in E it was assumed that E scales linearly with S , as in the known relationship of the Oliver–Pharr model E r ∝ S √ A c , with A c contact area . Henceforth, the respective standard errors have been assumed to be identical, σ E / E mean = σ S / S mean , and σ E thus obtained has been used as the error for E mean . In this way we could assume an n ≤ 40 × 40 = 1600 from the single FV dataset selected, where only few datapoints were discarded as not working properly in the S calculation routine.
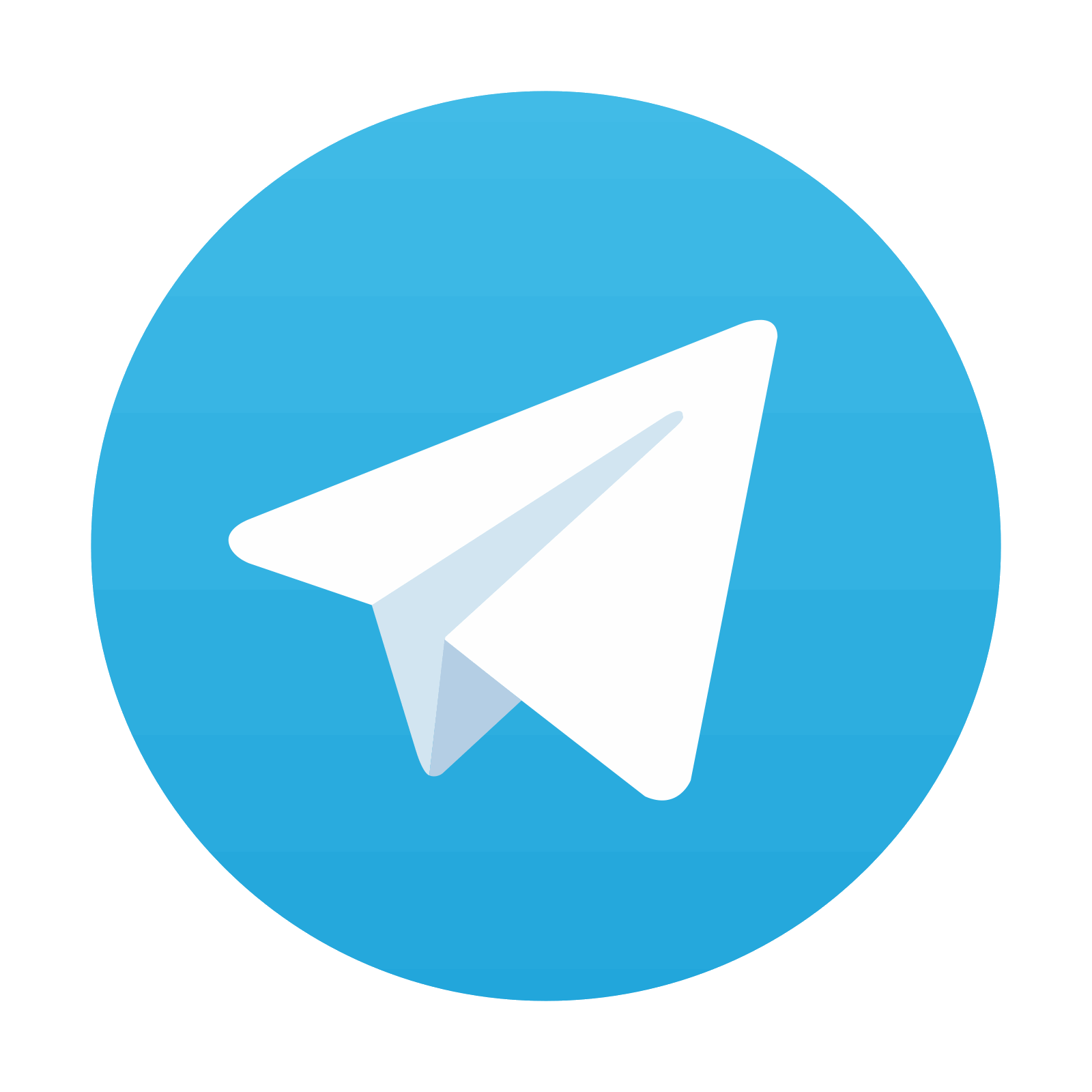
Stay updated, free dental videos. Join our Telegram channel

VIDEdental - Online dental courses
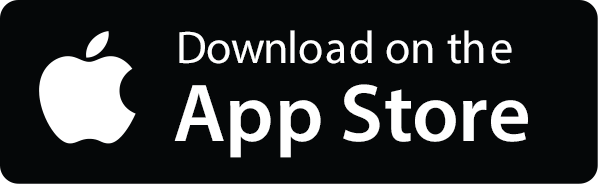
