Highlights
- •
Hard machining reduced around 27% the leucite glass–ceramic strength.
- •
Glaze firing is able to reduce the leucite glass–ceramic strength.
- •
Glaze firing can change the ceramic microstructure by forming amorphous material.
- •
HF acid etching produces rougher surfaces but not reduce the ceramic strength.
- •
Post-machining roughness is influenced by machining order and by the pair of burs.
Abstract
Objective
To evaluate the effects of hard machining, glaze firing and hydrofluoric acid etching on the biaxial flexural strength and roughness of a CAD/CAM leucite glass–ceramic; to investigate if ceramic post-machining surface roughness is influenced by the machining order and by the pair of burs used for it.
Methods
A hundred forty four discs were machined by six nominally identical pairs of burs and divided into groups ( n = 24): (1) machining—M, (2) machining and glaze firing—MG, (3) machining and hydrofluoric acid etching—MA, (4) machining, glaze firing and hydrofluoric acid etching—MGA, (5) machining followed by polishing, as a control—MP, (6) machining, polishing and hydrofluoric acid etching—MPA. The roughness after each treatment ( R a and R z ) was measured. The discs were submitted to a piston-on-three ball flexure test (ISO 6872/2008) and strength data analyzed through Weibull statistics (95% CI).
Results
M resulted in lower characteristic strength ( σ 0 ) (128.2 MPa) than MP (177.2 MPa). The glaze firing reduced σ 0 (109 MPa), without affecting roughness. Hydrofluoric acid etching increased the roughness without affecting σ 0 . Spearman’s coefficient ( r s ) indicated strong and significant correlation between machining order and roughness ( r s R a = −0.66; r s R z = −0.73). The ceramic post-machining surface roughness differed significantly according to the pair of burs employed ( p < 0.05).
Significance
hard machining and glaze firing reduced the leucite ceramic strength, while hydrofluoric acid etching did not affect the strength. Variability in the roughness might be expected after machining, since it was influenced by the machining order and by the bur pairing.
1
Introduction
Due to the brittle nature of ceramics, their fracture strength is strongly influenced by the presence of defects, which can be considered especially critical when located at the cementation surface of a ceramic crown . A compressive load applied to the occlusal surface of a ceramic single crown induces tensile stresses on the cementation surface, which may contribute to initiate the clinical fracture of a ceramic restoration .
The introduction of CAD/CAM (Computer-Aided Design; Computer-Aided Machining) technology in Dentistry has enabled the production of complex restorations using prefabricated ceramic blocks, which are reduced by diamond cutting tools in the dimensions and anatomy informed in a software compatible with the machining system . In spite of reducing processing defects, once the ceramic blocks are produced in a standard process independent of the manual ability of a technician, the machining induces a complex network of events in the ceramic, resulting in radial and lateral cracks, chipping, subsurface damage, residual stresses and even plastic deformation . Therefore, knowledge of the effects that machining has on the ceramic strength is essential.
Machining can be performed using fully sintered ceramics (hard machining), such as with feldspar-, leucite- and lithium disilicate-based ceramics, or by using partially sintered blocks (soft machining), such as with Y-TZP ceramics. Depending on the type of machining (hard or soft), different effects to the strength of the ceramics may be expected . Wang et al. reported that CAD/CAM soft machining produced surface damage and significantly reduced the strength of zirconia, which may result in unexpected failures at stresses much lower than the ideal strength of the material.
After machining and clinical adjustments, CAD/CAM glass–ceramic restorations can undergo a final glaze to promote a glossy and smooth surface. During the glazing process, the ceramic may be submitted to a range of temperatures near the glass transition temperature ( T g ). Residual stress relief has been reported due to thermal treatment, leading to different effects on ceramic strength. Giordano, Cima and Pober reported a reduction in strength after heat treatment, which was attributed to the relief of compressive stresses resulting from polishing. Griggs, Thompson and Anusavice reported that self-glazing did not improve the strength of indented porcelain discs, although having provided flaw modification through a crack-blunting mechanism. According to those authors, a compressive residual stress created during manufacture of the specimens may be removed by annealing the discs during a self-glaze process. In the study of Addison et al. , thermal treatment followed by slow cooling did not affect the strength of machined feldspathic ceramic discs. Considering that machining may be able to introduce a thin compressive layer within the ceramic surface, producing a positive effect on the material strength , glaze firing may reduce the ceramic fracture strength due to relief of the residual compressive stresses.
Regarding ceramic surface conditioning, hydrofluoric acid etching (HF) is an imperative procedure for the success of adhesive cementation of silica-based ceramics. HF creates irregularities in the ceramic surface, increasing the surface energy, and optimizing the resin bond to the ceramic. However, these surface irregularities could negatively affect the material fracture strength . Currently, according to the current authors’ knowledge, there is no study that assesses the isolated effect of hydrofluoric acid etching using biaxial flexure strength testing of hard machining ceramic discs.
Therefore, taking into account the increasing use of CAD/CAM technology in Restorative Dentistry, in which machining may introduce new features to the cementation surface of ceramic restorations, this study assessed the effect of hard machining on the biaxial flexure strength (BFS) and roughness of a leucite glass–ceramic. The impact of procedures preceding cementation to the BFS of machined ceramic discs (the thermal cycle used in glazing and hydrofluoric acid etching) were also investigated. The hypothesis tested was that all procedures (machining, glaze firing and hydrofluoric acid etching) would reduce the ceramic BFS.
Another aim of the current study was to investigate whether the ceramic surface roughness would be influenced by the order of machining and by the pair of burs used for the production of the discs. The hypothesis tested was that the post-machining ceramic roughness would be independent of the machining order and of the pair of burs used.
2
Materials and methods
2.1
Machining of ceramic discs by CAD/CAM
Two different stone models were produced: a preparation model ( Fig. 1 a) and a reference model ( Fig. 1 b). The preparation model was a customized cylindrical crown with an internal preparation (13.5 mm diameter; 1.4 mm depth) and, adjacent to it, two simple cylindrical crowns with flat occlusal surfaces. Three simple crowns formed the reference model. These models were scanned (Scanner CEREC inLab, Sirona Dental Systems Gmbh, Germany) and the three-dimensional images were processed in CAD CEREC inLab 3D software, version 3.85 (Sirona Dental Systems Gmbh, Germany). Using the software interface, a correlation of equality was established between the models, indicating that the restoration to be created for the preparation model should follow the same anatomy of the reference model. Thus, it was possible to machine a disc shaped restoration that had a 13.5 mm diameter and 1.4 mm thickness ( Fig. 1 c and d) using leucite glass–ceramic fully sintered blocks (14 mm × 14 mm × 18 mm) (IPS Empress CAD C14L, Ivoclar Vivadent AG, Liechtenstein), using CEREC inLab MC XL machine (Sirona Dental Systems Gmbh, Germany).

Six nominally identical pairs of diamond burs ( A – F ), each containing one cylindrical (Cylinder pointed bur 12S, Sirona Dental Systems Gmbh, Germany) and one stepped pattern (Step bur 12S, Sirona Dental Systems Gmbh, Germany) bur, were used for machining 154 ceramic blocks. Each block was used for one disc, with the machining order (from 1st up to 28th) and the pair of burs ( A , B , C , D , E or F ) recorded for each individual disc. For the first pair of burs used, the cylindrical bur fractured while machining the 29th disc. Therefore, the maximum number of discs obtained from each pair of burs was set at 28, with the exception of the last pair of burs ( F ) which was used to prepare 13 discs due to the number of remaining ceramic blocks. From the total number of machined discs, nine were employed in a pilot study and one was eliminated due to the bur fracturing while it was bring machined. The remaining 144 discs were randomly divided into six experimental groups ( n = 24).
2.2
Experimental groups
The experimental groups consisted of discs submitted to the following treatments: (1) machining (M), (2) machining and glaze firing (MG), (3) machining and hydrofluoric acid etching (MA), (4) machining, glaze firing and hydrofluoric acid etching (MGA), (5) machining and polishing (MP), (6) machining, polishing and hydrofluoric acid etching (MPA).
The glaze firing treatment was performed in a Vita Vacumat 6000 MP furnace (Vita Zahnfabrik, Germany) and followed the glaze firing protocol indicated for IPS Empress CAD ® by the manufacturer, without the use of any glaze paste (initial temperature 403 °C; temperature rise 100°/min; final glazing temperature 790 °C for 90 s; vacuum initiated at 450 °C and released at 789 °C) . Ten minutes after opening the furnace, the discs were removed and bench cooled.
Polishing was performed manually using 400, 600 and 1200 grit silicon carbide paper on the bottom surface of the discs, removing 80 μm of the machining surface, in order to remove defects caused by machining. The depths of removal in the center of the discs were controlled by means of a micrometer (210 MAP, Starrett, USA).
Etching was applied on the bottom surface of the discs, using 10% hydrofluoric acid (Condac Porcelana, FGM, Brazil) for 60 s. The specimens were then washed in distilled water for 60 s and air dried for 30 s.
The final thickness at the center of the discs, as measured by a micrometer (210 MAP, Starrett, USA), was adjusted using 240, 400 and 600 grit silicon carbide paper on the upper surface of the discs to a thickness of 1.32 ± 0.02 mm.
The sprue attachment created during the machining process was located on the lateral circumference of the discs and allowed for the re-orientation of the specimens during the roughness measurements. The sprue was removed for the flexural test using a diamond bur at low speed.
2.3
Measurement of the surface roughness
The roughness of the bottom surface of every disc was measured after machining (initial roughness) and at the end of each treatment (final roughness), using a contact stylus profilometer (SJ-410, Mitutoyo, Japan).
The R a (average surface roughness; μm) and R z (the arithmetic mean peak-to-valley height; μm) values were determined using the average of three measurements, transversal to the machining path. The sampling length was equivalent to five times the cut-off value ( λ c ), as defined according to ISO 4287:1997 , using the R a values recorded at a first reading as a reference. Thereafter, the final roughness of the group MP was evaluated using λ c = 0.25 mm (tabulated value for 0.02 < R a ≤ 0.1), resulting in a sampling length of 1.25 mm. The initial and final roughness measurements for the other groups were conducted using λ c = 0.8 mm (tabulated value for 0.1 < R a ≤ 2.0), resulting in a sampling length of 4 mm. In addition to the use of a correct cut-off value, a Gaussian filter was employed to differentiate between shape defects and the roughness profile.
2.4
Analysis of leucite crystals: X-ray diffraction
In order to evaluate the effect of the glaze firing on the leucite crystals, two discs were submitted to X-ray diffraction (D8 Advanced XRD, Bruker AXS GmbH, Germany) before and after heat treatment, using a length wave of 1.5416 Å (Cu K α ), a scan from 10° to 90°, a step wise of 0.02° and a time of 187 s.
The average size of leucite crystallites was determined before and after glaze firing for the most intense peaks (0 0 4 and 4 0 0) using the Debye equation (Eq. (1) ) .
T = 0.9 λ β cos Θ
where T is the crystallites average diameter, λ is the wavelength of an X-ray (1.5416 Å), θ is the location of the peak and β is the width of the middle-height of a selected peak, in radians. The real value of β , the free of measurement errors, was calculated using the following equation:
β 2 = β M 2 − β S 2
where β M is the value of β obtained using ceramic diffraction and β s is the value of β obtained for a crystal with a size greater than 1000 Å, in this case, silicon.
2.5
Piston-on-three ball biaxial flexure test
The fracture strength of the discs was determined using a piston-on-three ball test, according to ISO 6872/2008 , using a universal testing machining (DL-1000 Emic, Brazil). The bottom surface of the disc – the experimental surface – was positioned on the top of three steel spheres (2.5 mm in diameter, 120° apart and forming a circle of 10 mm diameter), with a load applied at a rate of 1 mm/min, perpendicular to the center of the top surface of the disc, by a circular cylinder steel piston with a 1.4 mm diameter flat tip. An adhesive tape of 25 μm was placed between the piston and the disc before loading to fracture. The fracture strength, in MPa, was calculated using Eqs. (3)–(5) :
σ = − 0.2387 P X − Y d 2
X = ( 1 + v ) ln B C 2 + 1 − v 2 B C 2
Y = 1 + v 1 + ln A C 2 + 1 − v A C 2
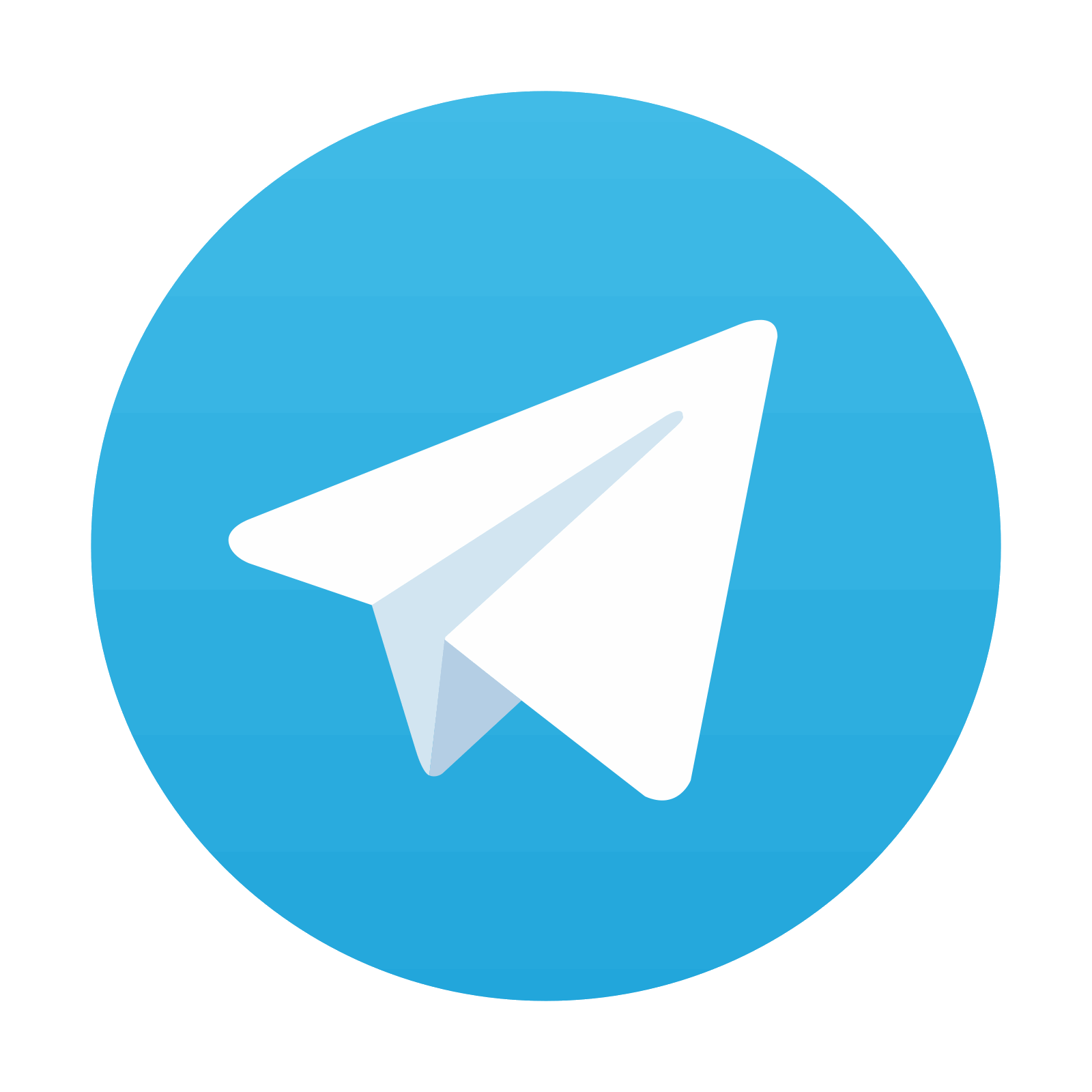
Stay updated, free dental videos. Join our Telegram channel

VIDEdental - Online dental courses
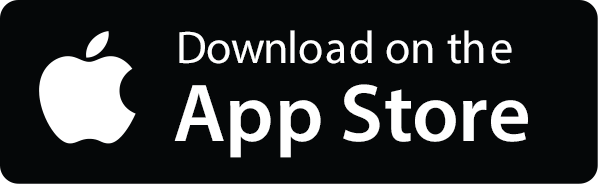
