For additional ancillary materials related to this chapter, please visit thePoint.
Objectives
After studying this chapter, the student will be able to do the following:
1. Define the following terms: study model, cast, and die.
2. Discuss the major differences between dental plaster, stone, and improved stone.
3. Explain the meaning of initial and final setting times.
4. Give three examples of how to increase and decrease the setting times of gypsum products.
5. Discuss wet and dry strength as it relates to gypsum products.
6. Summarize the recommended technique for use of gypsum products for measuring, mixing, and filling the impression. Include hand and vacuum mixing.
Key Words/Phrases
accelerators
articulator
calcination
cast
die
dry strength
final setting time
gypsum products
high-strength stone
improved stone
initial setting time
plaster
retarders
stone
study model
water/powder ratio
wet strength
working time
Introduction
Gypsum materials are mixed with water to produce a replica from an impression. Gypsum materials are used in dental offices and laboratories by dentists, hygienists, assistants, and lab technicians. These materials are quite old but still popular due to their ease of use, their affordability, and the long-term stability of the resulting cast.
I. Gypsum Materials
A. Use of Gypsum Products in Dentistry
Gypsum products are supplied as fine powders that are mixed with water to form a fluid mass or slurry that can be poured and shaped and that later hardens into a rigid, stable mass. An example of this powder is illustrated in Figure 9.1. Gypsum products are used mainly for positive reproductions or replicas of oral structures. These replicas are called casts, dies, or models, and they are obtained from negative reproductions, such as alginate impressions. Each replica has a specific purpose.
FIGURE 9.1. Gypsum powder (front): bulk package and premeasured envelope.
1. A study model is used to plan treatment and to observe treatment progress (Fig. 9.2A).
2. A cast is a replica on which a restoration or appliance is fabricated. A cast is more accurate than a study model and is a replica of more than one tooth, such as a quadrant or a full arch. It may be partially or completely edentulous. Examples of dental casts are shown in Figure 9.2B.
3. A die is a working replica of a single tooth, as shown in Figure 9.3. Typically, it is a removable part of a cast.
FIGURE 9.2. A. Preoperative and postoperative orthodontic study models. B. Dental casts made of stone for partial denture construction. (Part B reprinted from Richardson RE, Barton RE. The Dental Assistant. 5th ed. New York: McGraw-Hill; 1978, with permission.)
FIGURE 9.3. Cast with mounted dies. A. Five dies in cast. B. One die removed. C. All dies removed.
Because indirect dental restorations are fabricated on these cast or die replicas, it is essential that the particular gypsum product be carefully manipulated to ensure an accurate restoration.
B. Desirable Properties
Several properties are required of a material to be used for making casts, models, or dies. These properties are
1. Accuracy
2. Dimensional stability
3. Ability to reproduce fine detail
4. Strength and resistance to abrasion
5. Compatibility with the impression material
6. Color
7. Biological safety
8. Ease of use
9. Cost
Not all gypsum products display all of these desirable properties equally.
II. Types of Gypsum Products
Gypsum products are made from gypsum rock, which is a mineral found in various parts of the world. Gypsum rock is mined, ground into a fine powder, and then processed by heating to form a variety of products. Chemically, gypsum rock is calcium sulfate dihydrate (CaSO4·2H2O). Pure gypsum is white, but in most deposits, it is discolored by impurities. Gypsum products are used in dentistry, medicine, homes, and industry. In homes, gypsum plaster is used to make walls; in industry, it is used to make molds.
In this chapter, three types of gypsum products are discussed: plaster, stone, and high-strength or improved stone. Chemically, all three are calcium sulfate hemihydrate. They are produced as a result of heating gypsum and driving off part of the water of crystallization. This process is called calcination and is shown in the following equation:

Plaster, stone, and improved stone differ in the physical characteristics of their powder particles as a result of differing calcination methods. These differences in powder particles are responsible for their different properties, which make them suitable for various uses. The manufacturers add other chemicals to improve handling and properties.
A. Plaster
Plaster was the first gypsum product available for dentistry. It is manufactured by grinding the gypsum rock into a fine powder and then heating that powder in an open container. This direct and rapid heating in open air drives part of the water of crystallization from the crystal and shatters the crystal. The resulting powder consists of porous, irregular particles (Fig. 9.4A). Plaster is the weakest and least expensive of the three gypsum products. It is used mainly when strength is not a critical requirement, such as preliminary casts for complete dentures and attaching casts to a mechanical device called an articulator. This device simulates the patient’s occlusion and mastication process and is shown in Figures 1.8C and 11.6F; these photographs illustrate the use of plaster to secure the cast to the articulator.
FIGURE 9.4. Scanning electron micrographs of A. dental plaster powder particles and B. dental stone powder particles. (Courtesy of Diane Schwegler-Berry, NIOSH, Morgantown, WV.)
Plaster is usually white in color and sometimes is referred to as beta-hemihydrate or Type II. In the past, plaster was modified for use as an impression material by the addition of chemicals and was called impression plaster (see Chapter 8, Impression Materials).
B. Stone
Stone is made from gypsum by carefully controlled calcination under steam pressure in a closed container. This method of calcination slowly releases the water of crystallization from the crystal so that the resultant powder particle (Fig. 9.4B) is more regular, more uniform in shape, and less porous compared to that of plaster. Stone is stronger and more expensive than plaster. It is used mainly in making casts for diagnostic purposes and casts for complete and partial denture construction, which require greater strength and surface hardness than that of plaster.
The stone is usually light tan in color, but it can be obtained in other colors. It is often referred to as alpha-hemihydrate, Type III stone, or Hydrocal.
C. High-Strength or Improved Stone
High-strength stone, or improved stone, is also made from gypsum by calcining the gypsum but in a calcium chloride solution. This method of calcination results in a powder particle that is very dense, is cuboidal in shape, and has a reduced surface area. High-strength stone is the strongest and most expensive of the three gypsum products, and it is used mainly for making casts or dies for crown, bridge, and inlay fabrication. Figure 9.3 shows an example of an improved stone cast and several dies for the fabrication of crowns. This material is used because high strength and surface hardness are required during the fabrication process; the fabrication of crowns is described in the next chapter. High-strength stone is often referred to as Type IV stone, die stone, densite, or modified alpha-hemihydrate. A newly developed high-strength stone with a higher compressive strength than that of Type IV stone is also available. It displays higher setting expansion and is referred to as Type V stone.
D. Other Types of Gypsum
Other types of gypsum products are produced for special uses, such as fast set, mounting of casts on articulators, and impressions. Gypsum-based investments are presented in Chapter 10, Materials for Fixed Indirect Restorations and Prostheses.
III. Setting Reaction
When any of the various types of calcium sulfate hemihydrate are mixed with water, the hemihydrate is changed back to dihydrate by the process of hydration. Heat is liberated, as shown by the following reaction:

The calcium sulfate hemihydrate dissolves in the mixing water. The dihydrate forms as it is less soluble than the hemihydrate. The calcium sulfate dihydrate precipitates out of solution as interlocking crystals forming a hard mass.
IV. Water/Powder Ratio
The proportion of water to powder used to make a workable mix of a particular gypsum product is called the water/powder ratio. For dental use, an excess amount of measured water above the theoretically correct amount required for hydration is always necessary. This excess amount is needed to make a workable mix or slurry that can be poured and shaped. The excess water is distributed as free water in the set mass without taking part in the chemical reaction, and it contributes to subsequent porosity or microscopic voids in the set product. The proper water/powder ratio for each product depends on the physical characteristics of the powder particles. Plaster requires more gauging water (measured water) to wet the powder surfaces, fill the pores, and float the irregular porous particles. The dense particles of stone require less gauging water to float them, and their regular shape allows them to roll over one another more easily. High-strength stone, because of its very dense and cuboidal type of particle as well as modifications made by the manufacturer, requires even less gauging water than does stone. For dental use, the proper water/powder ratios (fractions) are as follows:
- For the average mix of plaster, 45 to 50 mL/100 g (0.45–0.50)
- For the average mix of stone, 28 to 30 mL/100 g (0.28–0.30)
- For the average mix of improved stone, 19 to 24 mL/100 g (0.19–0.24)
This difference in the amount of measured water that is required to make a workable mix results in different consistencies for the products when first mixed at the proper water/powder ratio. Plaster is usually thin in consistency, like a “smoothie,” whereas improved stone is like thick cake batter. Dental stone has an intermediate consistency. The water/powder ratio has a direct effect on the properties of each gypsum product and must be controlled for optimum results.
V. Setting Time
A. Definitions
Knowledge of the setting characteristics of a gypsum product is important for proper manipulation. The clinician should be aware of two time intervals in the setting process.
1. Working Time or Initial Setting Time
Working time or initial setting time is the length of time from the start of the mix until the setting mass reaches a semi-hard stage. It represents the available time for manipulating the product, and it indicates partial progress of the setting reaction.
2. Final Setting Time
Final setting time represents the length of time from the start of the mix until the setting mass becomes rigid and can be separated from the impression. The final setting time indicates the major completion of the hydration reaction.
B. Measurement
Setting times are usually measured with a surface penetration test. Gillmore needles are commonly used for this measurement and are shown in Figure 9.5. When the surface of the setting product has developed sufficient strength to support the weight of the ¼-lb needle and of the 1-lb needle, the initial setting time and the final setting time, respectively, have occurred. In other words, each designated setting time is reached when its respective needle no longer makes an indentation in the gypsum specimen. This method is somewhat arbitrary, and it is difficult to correlate directly with the setting reaction. In addition, the resulting values are mainly used for comparisons of different products. For practical purposes in a typical dental office, loss of surface gloss can be used as a determination of the working time; it is typically 5 to 7 minutes. The failure of penetration by a fingernail or dull knife would indicate relative rigidity and hardness and could be used as an indication of final set. Usually, a time of 30 to 45 minutes is used as a subjective criterion for the time of final set.
FIGURE 9.5. The 1-lb (left) and ¼-lb (right) Gillmore needles with a sample of a gypsum product.
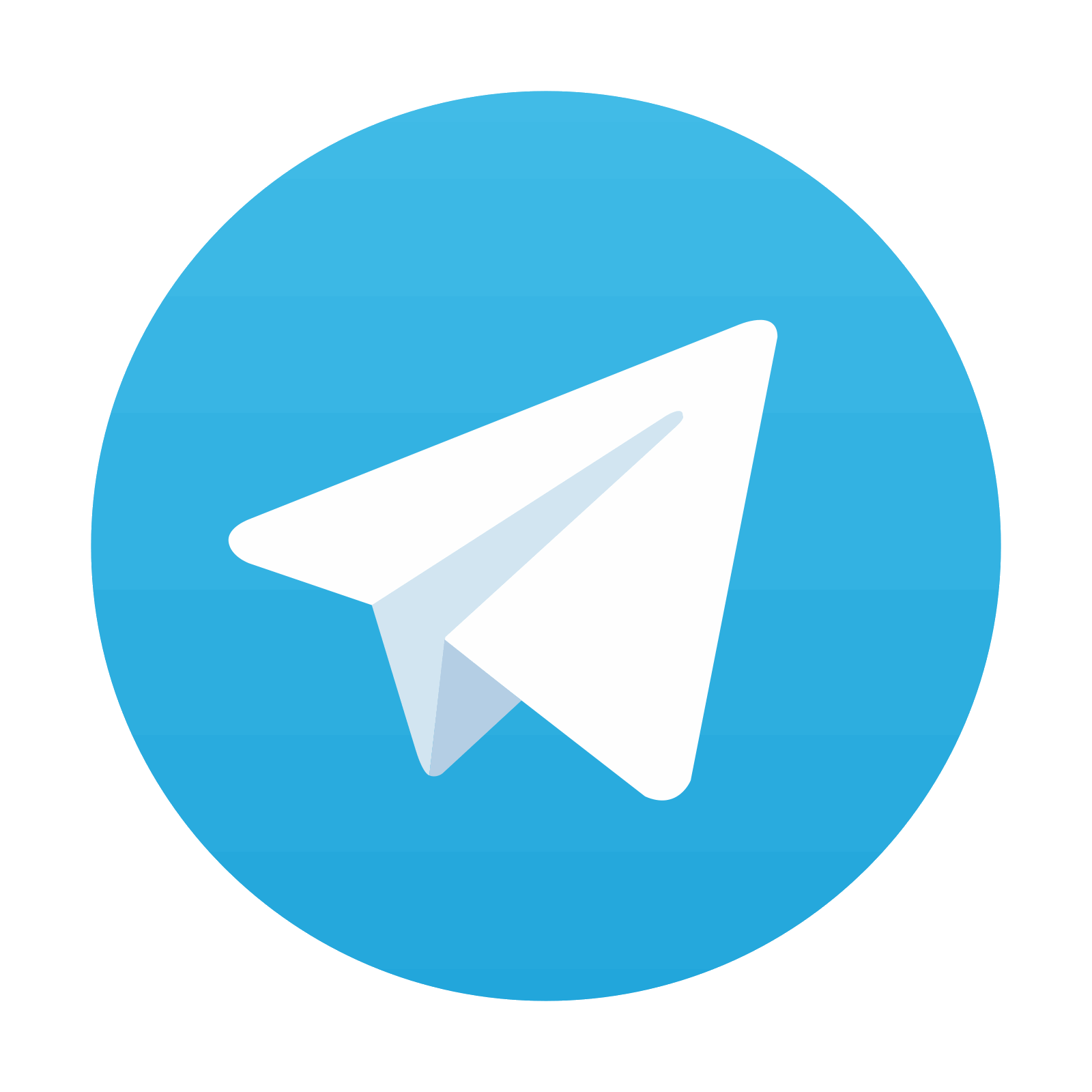
Stay updated, free dental videos. Join our Telegram channel

VIDEdental - Online dental courses
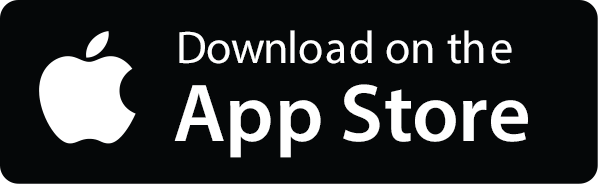
