Graphical abstract

Highlights
- •
Carbon-added anatase-rich TiO 2 layers were formed via two-step thermal oxidation.
- •
TiO 2 layers showed antibacterial properties in visible light.
- •
TiO 2 layers possessed excellent bonding strength: more than 80 MPa.
Abstract
Objective
To avoid risk of infections associated with dental implants, thermal oxidation processes for practical dental Ti alloys were studied for both high bonding strength and antibacterial properties in visible light.
Methods
Two-step thermal oxidation, comprising carburization (first step of treatment: in Ar-1%CO gas) and subsequent oxidation (second step of treatment: in air), was conducted on commercially pure (CP) Ti, Ti-6Al-4V (Ti64), and Ti-6Al-7Nb (Ti67) alloys to form TiO 2 layers. Their bonding strengths and antibacterial properties against Escherichia coli ( E. coli ) in visible light (λ ≥ 400 nm) were evaluated.
Results
TiO 2 layers formed on each metal were composed of anatase and/or rutile. Anatase fraction and carbon concentration in the layers decreased with increasing temperature in the second step of treatment. Antibacterial properties of the TiO 2 layers were dependent on the temperature in the second step of treatment. An approximate antibacterial activity value of 2 (killing ∼99% bacteria) was obtained when the temperatures in the second step of treatment were 673 and 773 K for CP Ti, 773 K for Ti64, and 773 and 873 K for Ti67. It was found that the TiO 2 layer must contain carbon and be anatase-rich to exhibit excellent antibacterial properties. Bonding strength between the substrate and TiO 2 layers formed at 773 K in the second step of treatment exceeded 80 MPa and was independent of substrate type.
Significance
TiO 2 layers, possessing both high bonding strength and excellent antibacterial properties, were successfully formed on practical dental Ti alloys via two-step thermal oxidation.
1
Introduction
Because of their excellent specific strength, corrosion resistance, and biocompatibility; titanium and its alloys are extensively used as biomaterials. Their most notable advantage is osseointegration: Ti achieves direct and tight connection with the bone at the optical microscopic level [ , ]. Because this phenomenon enables direct load transmission to living bones, Ti and its alloys are used as artificial hip joints, dental implants and so on, which directly connect to living bones [ , ]. In particular, almost 100% of dental implants are made of Ti and its alloys.
Even though the 10-year survival rate of dental implants is as high as 90–96%, dental implants bear inflammation risks [ ]. It was reported that the 10–15-year incidence of peri-implantitis was 14% [ ]. Elimination of pathogenic bacteria, bone regeneration and re-osseointegration are required to treat peri-implantitis in terms of function, esthetics and survival rate [ ].
Titania (TiO 2 ) coating on Ti and its alloys contributes to the improvement of bone compatibility and achievement of antibacterial properties induced by photocatalytic reactions, which could be applied on treatment and prevention of peri-implantitis. Further, because photocatalytic reactions occur only in the light, cell damage on TiO 2 coatings would be minimized after treatment and prevention using light are completed. Attempts to use photocatalytic TiO 2 coatings to implement antibacterial properties on medical devices thus eliminating pathogens have been made [ , , ]. In the case of dental implants, the surface of the infected implant can be irradiated by light because the surrounding soft and bone tissues recede via an inflammatory reaction. By using a combination of physical decontaminations, such as scaling and a photocatalytic antibacterial TiO 2 layer, effective elimination of bacteria on the implant surfaces can be realized. However, there are only a few reports on the formation of the TiO 2 coatings on practical dental Ti materials with the antibacterial properties in visible light [ ].
Previously, the formation of anatase TiO 2 layers on Ti substrates using “two-step” thermal oxidation was studied. It was reported that NaCl-type Ti(C,O) layers were formed on commercially pure (CP) Ti [ , ], Ti–Nb [ , ] and Ti–Mo alloys [ ] via the first step of treatment using Ar–CO gas, and subsequently TiO 2 layers containing anatase were formed via the second step of treatment in air. These oxide layers exhibited photo-induced superhydrophilicity and degraded organic matters in ultra violet (UV) light [ , ].
To apply the photocatalytic coatings on the treatment and prevention of peri-implantitis, processes that achieve TiO 2 layers with excellent photocatalytic activity in visible light, which is less harmful on the human body compared to UV light, must be invented. Addition of transition and non-metallic elements, including carbon, is beneficial to the visible-light activation of TiO 2 [ ]. Carbon was introduced into TiO 2 layers containing anatase via two-step thermal oxidation [ ], indicating that this process could achieve the visible-light activation of the layers. However, their antibacterial properties in visible light have not been clarified yet.
Based on this background, we hypothesize that TiO 2 layers, formed by two-step thermal oxidation, can exhibit visible-light-active antibacterial properties upon addition of carbon. The objective of this study is to establish the processing conditions, in particular, the temperature in the second step of the two-step thermal oxidation, suitable to form TiO 2 layers on practical dental implant materials. TiO 2 layers were formed on CP Ti, Ti-6Al-4V (Ti64), and Ti-6Al-7Nb (Ti67) alloys, by two-step thermal oxidation. The temperature in the second step of the process was changed from 673 K to 1073 K. The phase, anatase fraction, oxide layer thickness, surface roughness, and chemical composition of C, Al, V, and Nb in the TiO 2 layers were investigated. The bonding strength and antibacterial properties in visible light of the TiO 2 layers were evaluated. The effects of temperature on the formation of the anatase phase in the second step of the process were also clarified.
2
Materials and methods
2.1
Substrate materials
Bars of CP Ti (Japanese Industrial Standard, JIS, Gr. 2: ϕ30 mm, UEX), Ti-6Al-4 V (Ti64: ϕ14 mm, UEX), and Ti-6Al-7Nb (Ti67: ϕ14 mm, UEX) were cut into circular plates with diameters of ϕ12 mm and a thickness of 1 mm. A mirror finished surface was obtained by wet polishing. After cleaning the surface by ultrasonication in ethanol and ultrapure water for 0.6 ks, the plates were subjected to two-step thermal oxidation. The same treatment was performed for the CP Ti and Ti alloys before thermal oxidation.
2.2
Formation of TiO 2 layer by two-step thermal oxidation
As the first step of treatment, substrates were heated in Ar-1%CO mixed gas at a flow rate of 400 sccm (6.7 × 10 –6 m 3 s –1 ) at 1073 K for 3.6 ks, using a horizontal tubular furnace. The second step of treatment in air was conducted at 673–1073 K for 10.8 ks using a box furnace at a heating rate of 0.14 K s –1 and the cooling condition of furnace cooling. Temperature in the second step of treatment was changed to clarify the phase stability of the oxide layers, while the other heat treatment conditions remained constant.
2.3
Analyses and observation of reaction layers
Phases of reaction layers were identified using the α-2θ X-ray diffraction (XRD) measurement via Cu Kα radiation (Smart Lab 9 kW, Rigaku, 45 kV, 200 mA), after the first and second steps of treatment. Incident angle (α) was set at 1.0°. For each condition, substrate (CP Ti, Ti64, or Ti67), and treatment (first step or second step at 673–1073 K), one XRD measurement was performed to obtain the maximum peak intensity of anatase and rutile phases. The anatase fraction ( f A ) against rutile in the TiO 2 layers was calculated using Eq. (1) :
where I A and I R are the maximum peak intensity of anatase and rutile, respectively, in α-2θ XRD patterns [ ]. Surface roughness of TiO 2 layers was evaluated on the basis of the arithmetic average height, S a , which was measured on one TiO 2 layer for each condition, using a scanning probe microscope (SPM, AFM5100 N, Hitachi High-Technologies Science). A Si self-sensing piezoresistive cantilever (PRC-DF40 P, Hitachi High-Technologies Science) with a tip radius of 20 nm and tip height 8 μm, respectively, was used. Scan was performed in the dynamic force mode. Scan area was 20 μm × 20 μm with the number of image element of 512 (x) × 256 (y). Scan frequency was 0.6 Hz. The cross sections of the TiO 2 layers were observed using the scanning electron microscope (SEM: XL-30FEG, Royal Philips Electronics). For cross-sectional observation, the TiO 2 layers were embedded in conductive resins, followed by cutting and wet polishing to obtain the cross sections. Diamond paste with a diameter of 1 μm was used for the final polishing. Specimens were coated with Os (Os coater, HPC-30, vacuum device) to enhance the conductivity for SEM observations. Secondary electron images were obtained at the magnification of 10,000× at the accelerating voltage of 25.0 kV and the working distance of 10–10.5 mm. The elemental concentrations and the surface chemical states of the reaction layers were analyzed using X-ray photoelectron spectroscope (XPS: AXIS-ULTRA DLD, Shimadzu). Monochromatic Al Kα radiation was used at 15 kV (150 W), where the estimated depth of analysis was 3.6 nm. The pass energies were set at 160 and 40 eV for the survey and narrow scans, respectively. The resolution of the system was 0.68 eV. Survey scans were performed from 1200 to −5 eV in 1 eV steps, followed by narrow scans for O (542.9–522.9 eV), V (525.1–509.1 eV), Ti (469.9–449.9 eV), C (297.9–277.9 eV), Nb (213.5–197.5 eV), and Al (83.9–67.9 eV) in 0.1 eV steps. Casa XPS software (ver. 2.3.15) was used for binding state analysis. The binding energies were calibrated using surface contaminated hydrocarbons adsorbed from the atmosphere and referenced to the C 1s line at 284.8 eV. The surface chemical states were analyzed without sputter etching by Ar ions. The depth profiles of the elemental concentrations were obtained as with the sputter etching by Ar ions at sputtering rate of 1–2×10 −1 nm s −1 . One specimen for each condition was used for XPS analysis.
2.4
Bonding strength of TiO 2 layers
The bonding strengths of the TiO 2 layers on the substrates were measured using the stud pull test performed using a mechanical strength tester (Romulus, Quad Group). Al studs (Testing diameter: ϕ2.7 mm, P/N 901106, Quad Group) were administered on the TiO 2 layers using epoxy resins. After the resins were solidified through heat treatment in air at 423 K for 3.6 ks, the studs were pulled out with a loading speed of 2.0 kg s −1 and the maximum loads were measured, from which the bonding strengths were calculated. The averages and standard deviations of the bonding strengths were then obtained from five identical TiO 2 layers. After the test, the failure mode was examined using optical microscopy (OM: BX51, Olympus) and SEM (VE-7800, Keyence). Each OM image was obtained by combined 16 (4 × 4) adjacent images taken at the magnification of 50×. Specimens were coated by Os using the Os coater before the SEM observation and tilted 45°. Secondary electron images were obtained at the magnification of 30× under the condition of the accelerating voltage of 20 kV and the spot size of 8.
2.5
Evaluation of antibacterial activity under visible-light irradiation
To evaluate the antibacterial properties of the TiO 2 layers in visible light, the antibacterial property test was carried out using Escherichia coli ( E . coli : DH5α) and based on the glass-adhesion method. In this study, JIS R 1752: 2013 [ ] and Industrial standard organization (ISO) 17094: 2014 [ ] were referred to and modified.
Bacterial suspensions of E. coli in nutrient broth (NB) medium with a bacterial concentration of 10 8 CFU mL −1 were prepared by incubation at 310 K and were used for the antibacterial property test.
Three identical TiO 2 layers formed on each substrate, CP Ti, Ti64, and Ti67, by two-step thermal oxidation at temperature levels of 673–923 K in the second step of treatment were used. Further, 5 μL of bacterial suspension (bacterial number: 10 8 CFU mL −1 × 0.005 mL = 5 × 10 5 CFU) was dropped on each TiO 2 layer and covered using slide glass (ϕ10 × 0.12–0.15 t mm, Matsunami Glass). Then, one of the three was irradiated with visible-light irradiation ( I visible = 1 mW cm −2 , λ ≥ 400 nm) for 14.4 ks, another was placed in the dark for 14.4 ks, and the other was immediately used to measure the initial number of viable bacteria without visible-light irradiation nor placement in the dark. Xe lamp mounted with the UV cut filter was used as the light source.
After the viable bacteria on each of the three TiO 2 layers were collected in 2 mL of phosphate buffered saline (PBS), the numbers of viable bacterial ( N ) were measured through the plate dilution method using NB medium agar plates. Dilutions were conducted to obtain 30–300 colonies on each agar [ ]. Using the average number of colonies formed on two agar plates ( Z ), the numbers of viable bacteria can be calculated using Eq:
here E refers to the dilution factor, V refers to the volume of PBS used to collect the bacteria, and s refers to the volume of suspension smeared on each agar plate: in this study, E = 1–100, V = 2 mL, and s = 0.1 mL. Hereafter, different subscripts are added to N depending on treatment after dropping bacterial suspension: N Visible for 14.4-ks visible-light irradiation, N Dark for 14.4-ks placement in the dark, and N 0 for immediate collection without these treatments. The viable bacteria ratios were obtained through the normalization of N Visible and N Dark by N 0 as N Visible / N 0 and N Dark / N 0 , respectively. For the statistical test, the student’s t -test was performed on common logarithms of N Visible / N 0 and N Dark / N 0 for each substrate and each temperature level in the second step of treatment.
3
Results
3.1
TiO 2 layers on Ti alloys through two-step thermal oxidation
Fig. 1 (a) shows the SEM secondary electron image of the cross section of the reaction layer on CP Ti after the first step of treatment. From the results of XRD and XPS analyses (not shown here), it was confirmed that the phase of this reaction layer was the titanium oxycarbide, Ti(C,O), which has the NaCl-type structure. Ti(C,O) layers were also formed on Ti64 and Ti67 through the first step of treatment (Supplementary Fig. 1). The existence of oxygen in the layers were checked by XPS analyses (Supplementary Fig. 2). Fig. 1 (b)–(d) shows the SEM images of the cross sections of the reaction layers on CP Ti, Ti64, and Ti67 after the second step of treatment. According to the α-2θ XRD patterns shown in Fig. 2 , these reaction layers were TiO 2 , excepting those formed on Ti64 and Ti67 at 1073 K contained Al 2 O 3 . After the second step of treatment, Ti(C,O) formed at the first step of treatment was not detected for any substrate. This indicates that Ti(C,O) was oxidized to TiO 2 by the second step of treatment in air. The phases of TiO 2 were anatase and/or rutile. The anatase fraction ( f A ) against rutile in the TiO 2 layers on CP Ti, Ti64, and Ti67 after the second step of treatment at 673–1073 K was shown in Fig. 3 . f A was calculated using Eq. (1) . The TiO 2 layers were single anatase phase at 673 K. Anatase fraction was decreased as the temperature in the second step of treatment increased.
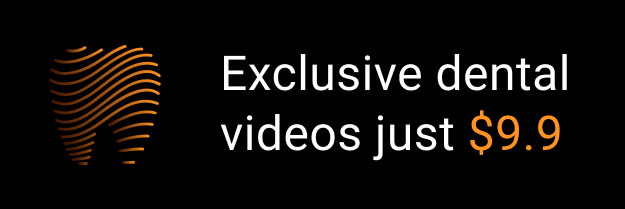