Introduction
Polymer brackets still have some disadvantages because of decreased wear resistance and hardness. The aim of this study was to investigate the mechanical properties of alternative bracket polymers; urethane-dimethacrylate, high-density polyethylene, and an experimental bracket polymer (EBP) consisting of polyethylene and a copolymer were tested. Polycarbonate and polyoxymethylene brackets served as controls.
Methods
The mechanical properties of urethane-dimethacrylate, high-density polyethylene, EBP, polycarbonate, and polyoxymethylene bracket materials were evaluated after thermocycling (6000 × 5 °C-55 °C) in a mastication device before testing. Three medium-wear, fracture toughness, and Vickers hardness tests were performed.
Results
High-density polyethylene had the highest values of wear and the lowest values of fracture toughness and Vickers hardness. The urethane-dimethacrylate bracket material and the EBP had better mechanical properties than polycarbonate. The polyoxymethylene bracket material had the highest values of fracture toughness and Vickers hardness, and the lowest values of wear compared with the other investigated polymers.
Conclusions
High-density polyethylene seems to be unsuitable as bracket material because it demonstrated excessive wear and insufficient fracture toughness. Polyoxymethylene had the best performance during mechanical testing.
Nowadays, requests for esthetic fixed orthodontic appliances have increased. More young patients want an esthetic appearance during treatment with fixed appliances. In addition, the demand for adult treatment is growing in orthodontics. Therefore, the introduction of esthetic brackets has been a blessing for some patients. Esthetic bracket materials are ceramics and various polymers. The advantages of ceramic brackets include color stability and great strength. On the other hand, excessive wear of enamel surfaces on opposing teeth has been observed during treatment with ceramic brackets. Damage to the enamel during removal of the brackets and bracket breakage because of brittleness were also reported.
In the 1970s, the first plastic brackets were manufactured from polycarbonate. Later, polyurethane, fiber-reinforced, and filler-reinforced brackets became available. In 1997, a German patent was issued for a new plastic bracket of polyoxymethylene. Despite these innovations, plastic brackets still have some disadvantages because of their decreased mechanical properties compared with ceramic brackets and their inability to withstand the torquing forces generated by rectangular wires. In addition, water sorption of plastic brackets could cause a plasticizing effect. Plasticizing decreases the properties of the polymeric structure in a wet environment. Therefore, further efforts are necessary to improve the mechanical properties of plastic brackets to offer patients cost-effective, tooth-colored plastic brackets that are easier to handle than ceramic brackets.
The aim of the study was to compare 3 experimental bracket polymers with polyoxymethylene and polycarbonate bracket materials. The first experimental bracket polymer (EBP) is well established in bearing technology and consists of a polyethylene and a copolymer. Additionally, the characteristics of high-density polyethylene and urethane-dimethacrylate were studied for use as bracket materials in orthodontics. To simulate the moisture of saliva and the temperature changes in the oral environment, all samples were thermocycled in an artificial oral environment. All bracket polymer groups were alternately flooded every 2 minutes with warm (55°C) and cold (5°C) distilled water for 6000 cycles in a mastication device to initiate plasticizing of the polymers before testing. Then, fracture toughness, which is the resistance of the polymer to crack expansion and wear, was determined with a 3-medium wear test device. Vickers hardness of the bracket materials was also calculated.
Material and methods
A total of 100 rectangular beams (20 per group) were manufactured with the dimensions of 36 × 8 × 4 mm (length × width × thickness). Five polymer groups were investigated: group 1, polyoxymethylene; group 2, polycarbonate; group 3, EBP; group 4, high-density polyethylene; and group 5, urethane-dimethacrylate. The surface of each beam was ground with sand paper (800 grit) first. Then, all beams were polished.
Before fracture toughness was tested, all beams were thermocycled in a mastication device (6000 × 5°C-55°C). For determining fracture toughness, the beams were prepared in this manner: at the midspan, a 3-mm deep and 0.5-mm wide notch was sawn. This cut was extended to a notch of 0.2 to 0.5 mm long by using a razor blade device (Ivoclar Vivadent, Schaan, Liechtenstein).
After preparation of the beams, a 3-point bending test was performed with a universal testing machine (model 1446, Zwick, Ulm, Germany). The load was axially applied in the center of the beams directly above the notch. The crosshead speed chosen was v = 1 mm per minute.
Fracture toughness depends on fracture load, dimensions of the samples, notch length, and the support distance of the 3-point bending test. Fracture toughness was calculated for each sample according to the method of Williams and Cawood.
A 3-medium wear test was performed by using a wear testing machine (Willytec, Munich, Germany). Ten samples of the 5 polymer groups were placed adhesively in the individual chambers of the round Academic Center Tandheelkunde Amsterdam sample holder. The tests were performed by using an abrasion medium consisting of rice (120 g) and millet seed shells (30 g) that were ground in a rotating blade grinder (Moulinette, Moulinex, Alencon, France) for 60 seconds and mixed with distilled water (275 mL). A total of 200,000 cycles were completed by using an antagonist wheel with a press-on load of 15 N. Every 50,000 cycles, the abrasion medium was replaced. A wear track on the sample wheel was caused by the antagonist wheel. The trace depth of this wear track was determined by using a roughness testing device (Perthometer S6P, Perthon-Feinprüf, Göttingen, Germany).
The bracket materials were loaded by a pyramid-shaped loading die (load weight, 0.5 kg) of the Vickers hardness measurement device (model B3212001, Zwick). The loading time was set to 60 seconds. The pyramid-shaped indention in the resin depended on the hardness of the bracket. Vickers hardness is proportional to the quotient of applied load and the area of the indention and was determined with the following formula.
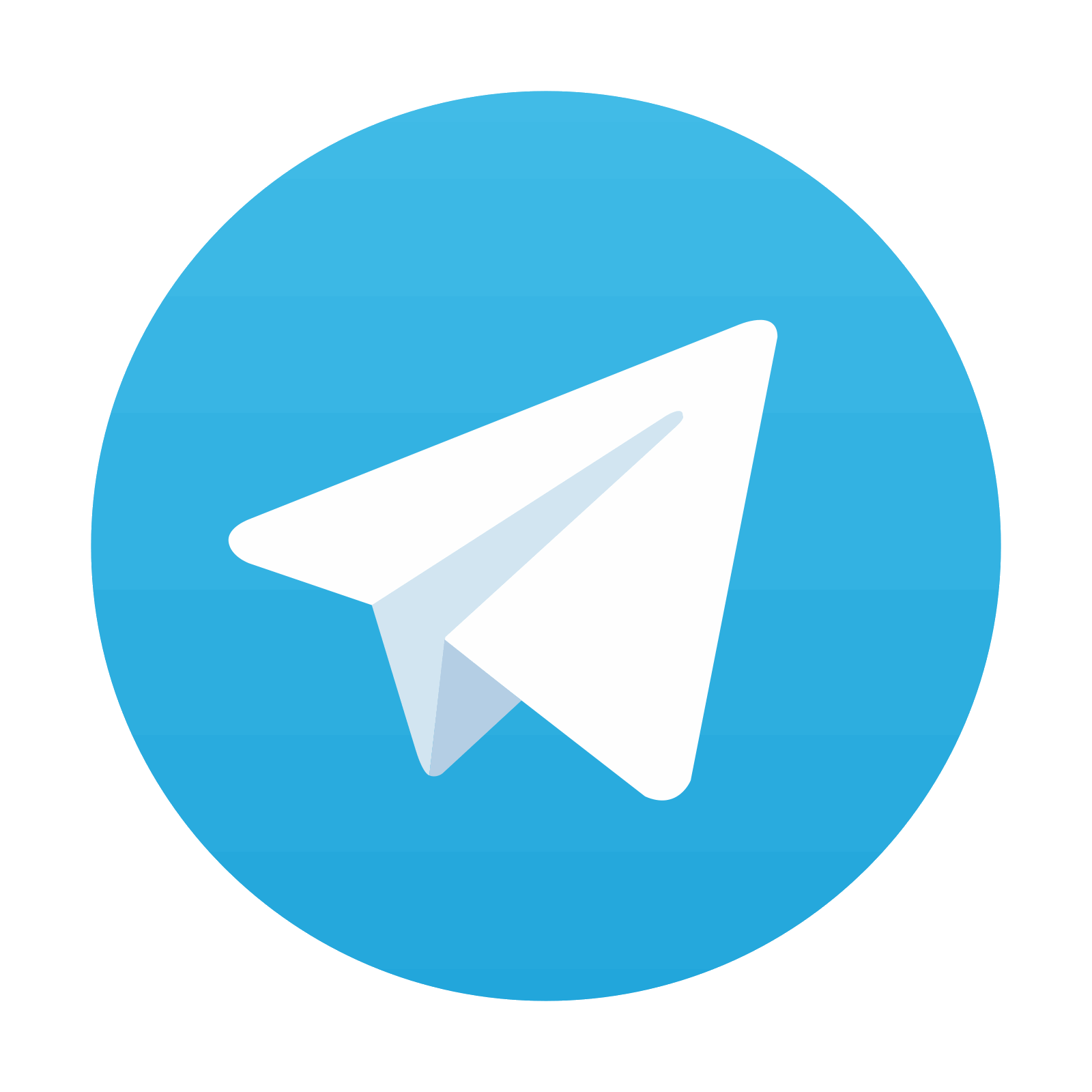
Stay updated, free dental videos. Join our Telegram channel

VIDEdental - Online dental courses
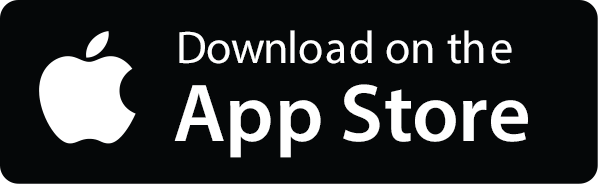
