Abstract
Objectives
To test the hypothesis that multiple firing and silica deposition on the zirconia surface influence the bond strength to porcelain.
Materials and methods
Specimens were cut from yttria-stabilized zirconia blocks and sintered. Half of the specimens (group S) were silica coated (physical vapor deposition (PVD)) via reactive magnetron sputtering before porcelain veneering. The remaining specimens (group N) had no treatment before veneering. The contact angle before and after silica deposition was measured. Porcelain was applied on all specimens and submitted to two (N2 and S2) or three firing cycles (N3 and S3). The resulting porcelain–zirconia blocks were sectioned to obtain bar-shaped specimens with 1 mm 2 of cross-sectional area. Specimens were attached to a universal testing machine and tested in tension until fracture. Fractured surfaces were examined using optical microscopy. Data were statistically analyzed using two-way ANOVA, Tukey’s test ( α = 0.05) and Weibull analysis.
Results
Specimens submitted to three firing cycles (N3 and S3) showed higher mean bond strength values than specimens fired twice (N2 and S2). Mean contact angle was lower for specimens with silica layer, but it had no effect on bond strength. Most fractures initiated at porcelain–zirconia interface and propagated through the porcelain.
Significance
The molecular deposition of silica on the zirconia surface had no influence on bond strength to porcelain, while the number of porcelain firing cycles significantly affected the bond strength of the ceramic system, partially accepting the study hypothesis. Yet, the Weibull modulus values of S groups were significantly greater than the m values of N groups.
1
Introduction
Zirconia-based ceramics is being proved a successful infrastructure material. Studies have reported no fractures of the zirconia infrastructure in short or medium-term periods of clinical observation . The failures of porcelain–zirconia restorations are frequently associated with biological complications , such as secondary caries, periodontal support and tooth fracture, which likely are not related to the materials used in fixed prostheses and some structural deficiencies of the material such as marginal discrepancies, weak performance of the veneering ceramics and its limited bond to the zirconia substrate . Chip-off (chipping) and veneer fracture with exposure of the zirconia core ceramic (delaminations) are clinical problems that are currently the subject of comprehensive investigations and remain to be overcome.
Studies showed that residual tensile stresses are created within the porcelain at or near the ceramic–porcelain interface and could contribute to the porcelain fracture in zirconia systems . The stresses are believed to have multifactorial origin, potentially involving the ceramic thermal history, restoration’s geometric factors (i.e. infrastructure design and core–veneer thickness ratio), material’s elastic properties (ceramics strength) and poor wetting of the core by the veneer . Therefore, these factors should be handled carefully to prevent development of high-magnitude tensile stresses.
The application of several layers of porcelain and, consequently, using multiple firing cycles, may be necessary for the fabrication of all-ceramic restorations, especially when using the standard layering technique to match the esthetics of the natural dentition. The effect of multiple firing cycles on the porcelain–zirconia adhesion remains unclear. Residual stresses can likely accumulate during the heating and cooling firing procedures mainly because of the cooling rate and the coefficient of thermal expansion (CTE) mismatch between core and veneer ceramics . When additional stresses are applied to the restoration, the probability of failure due to fatigue crack propagation might increase , explaining the delamination, which is considered a clinical failure mode. In addition, it has been reported on the negative influence of water, alcohol and modeling liquid on faceting Y-TZP grains at the interface with porcelain .
In order to improve the porcelain–zirconia mechanical behavior and the bond strength between zirconia and resin cements, Zhang and Kim developed a graded glass–zirconia structure: glass was incorporate to the external surface of the zirconia core. This graded material showed high resistance to intermediate flexural damage, better compatibility with the veneering porcelain and with the resin cements than homogeneous zirconia. This could be particularly interesting to the analysis of the porcelain–zirconia interface, where an improvement of the zirconia surface wettability, by a glass layer deposition, could lead to an increase in the quality of core–veneer bond strength.
A silica thin layer deposited by physical vapor is believed to be a reasonable approach to obtain a similar high-quality graded structure (glass/zirconia) based on the rationale that silicon oxides can be molecular deposited on the zirconia surface as an interlayer , improving the wettability at the interface. Additionally, a silica layer could reduce the negative effect of liquids from the slurry on the Y-TZP grains. Thus, assuming that good core–veneer bond strength is a clinical requirement to avoid premature failure of all-ceramic restorations , such as veneer delamination, the relationship between sequential number of porcelain firings and the presence of a thin silica layer should be investigated.
The objective of this study was to evaluate the effect of a silica thin layer deposited on the zirconia infrastructure and the number of porcelain firings on the zirconia–porcelain bond strength, testing the hypotheses that the ceramic bond strength increases with the presence of a silica interlayer and with the number of porcelain firing cycles.
2
Materials and methods
The brand name, type, chemical composition and manufacturers of the materials used in this study are described in Table 1 .
Brand name | Material type | Chemical composition a | Manufacturer |
---|---|---|---|
Vita VM9 Base Dentin – V9 (LOT n. 192164) | Feldspathic ceramic | SiO 2 (60–64%), Al 2 O 3 (13–15%), K 2 O (7–10%), Na 2 O (4–6%), TiO 2 (<0.5%), CeO 2 (<0.5%), ZrO 2 (0–1%), CaO (1–2%), B 2 O 3 (3–5%), BaO (1–3%), SnO 2 (<0.5%), Mg, Fe and P oxides (<0.1%) | Vita Zanhfabrik, Bad Säckingen, Germany |
Lava Frame Zirconia – YZ (LOT n. 391266) | Transformation toughening zirconia | ZrO 2 (95%), Y 2 O 3 (<3%), HfO 2 (<1–3%), Al 2 O 3 (<1%) e SiO 2 (<1%). | 3M-ESPE, St. Paul, Minnesota, USA |
Si target | Target | Si (99,999%) | Kurt J. Lesker, Pittsburgh, USA |
Sixteen ceramic blocks (10 mm × 10 mm × 12 mm) were obtained from partially sintered yttria-stabilized zirconia blocks (YZ). Before sintering ( Table 2 – Vita ZYrcomat furnace, Vita-Zahnfabrik, Germany), the blocks were ground finished to 1200 SiC paper and sonically cleaned (Vitasonic, Vita Zanhfabrik, Germany) in distilled water for 5 min.
Ceramic | Initial temperature (°C) | Heating rate (°C/min) | Holding temperature (°C) | Holding time (min) |
---|---|---|---|---|
Vita VM9 Base Dentin (V9) | 500 | 55 | 910 | 1 |
Lava Frame Zirconia (YZ) | 40 | 17 | 1530 | 120 |
A silica thin layer was deposited on the surface of eight YZ blocks (group S). The remaining blocks (group N) received no treatment before porcelain veneering. The layer deposition was performed in a cylindrical vacuum chamber evacuated to a base pressure of 5.0 × 10 −5 Torr by reactive magnetron sputtering technique, using a mixture of argon (20 sccm) and oxygen (5 sccm) in flux. The deposition pressure, cathode voltage and electric current were kept constant at 7 mTorr, 500 V and 0.5 A, respectively. A high purity silicon target (99,999%) was used during the experiments. The argon and oxygen mixture promotes sputtering on the silicon target surface. The silicon atoms react with the oxygen originating silica, which is deposited on the YZ surface. The temperature of the substrate holder in the reactor was kept at 105 °C using a thermocouple during the layer deposition, which was carried out for 30 min. Cathode voltage, electric current and substrate temperature were measured every 5 min to keep process stability.
Based on the sessil drop technique and controlled room temperature (20 °C) and humidity (40%), a drop of deionized water (15 μL) at room temperature was placed on the specimen surface and allow to flow until it reached stability (equilibrium) (20 s). Contact angle measurements were performed using a goniometer (Technological Institute of Aeronautics, São José dos Campos, SP, Brazil) before and after silica deposition ( n = 5).
The YZ blocks were placed into a silicone mold to control the thickness (3 mm) of the porcelain layer (V9). The V9 powder–liquid mix was applied on the YZ blocks, the porcelain liquid excess was blot out with absorbent paper and the blocks were carefully extruded from the mold. The blocks in groups S and N were randomly divided into 2 sub-groups according to the number of porcelain firings ( Table 2 – Vita Vacumat 40 furnace, Vita-Zahnfabrik, Germany): two firings (S2 and N2) or three firings (S3 and N3).
The YZ-V9 blocks were embedded into acrylic resin (JET, Clássico, SP, Brazil) for cutting with a diamond blade at 300 rpm using a cutting machine (Labcut 1010, Extec Technologies Inc., EUA) to fabricate bar-shaped specimens with a cross-sectional area of 1 mm 2 .
The specimens were bonded using cyanoacrylate-based glue (Loctite, Super Bonder, São Paulo, Brazil) to a micro-tensile device that was attached to the universal testing machine (DL-1000, EMIC, São José dos Pinhais, PR, Brazil). Uniaxial tensile load was applied at cross-head speed of 0.5 mm/min. The load at fracture was recorded and used to calculate the tensile bond strength ( σ , in MPa).
Fracture surfaces were examined under an optical microscope (Olympus CBB, Tokyo, Japan) using up to 100× magnification. Selected surfaces were prepared and examined under the scanning electronic microscope (SEM) (LEO 435VPi, LEO-Zeiss, Tokyo, Japan) using secondary electron mode (20 kV). The fracture origin was determined and described as follows: (A) adhesive failure with fracture initiating at the interface between the porcelain and zirconia; (B) cohesive failure of the porcelain; and (C) cohesive failure of the zirconia. Specimens that failed before the test (during preparation and cutting procedures) and those with purely cohesive fracture (fracture types B and C) were not considered for bond strength calculations ( Table 3 ).
Group | Porcelain firings | SiO x layer | Discarded specimens b | Tested specimens ( n ) | σ (SD) a (MPa) | m a | σ 0 (MPa) | σ 0.05 (MPa) | σ 0.01 (MPa) |
---|---|---|---|---|---|---|---|---|---|
N2 | 2 | No | 18 | 30 | 15.0 (6.6) a | 2.4 a | 16.9 | 5.0 | 2.6 |
N3 | 3 | No | 18 | 30 | 18.4 (6.1) b | 3.2 a | 20.5 | 8.1 | 4.9 |
S2 | 2 | Yes | 28 | 20 | 13.8 (2.3) a | 6.8 b | 14.8 | 9.6 | 7.5 |
S3 | 3 | Yes | 23 | 25 | 16.3 (2.9) ab | 5.7 b | 17.6 | 10.4 | 7.8 |
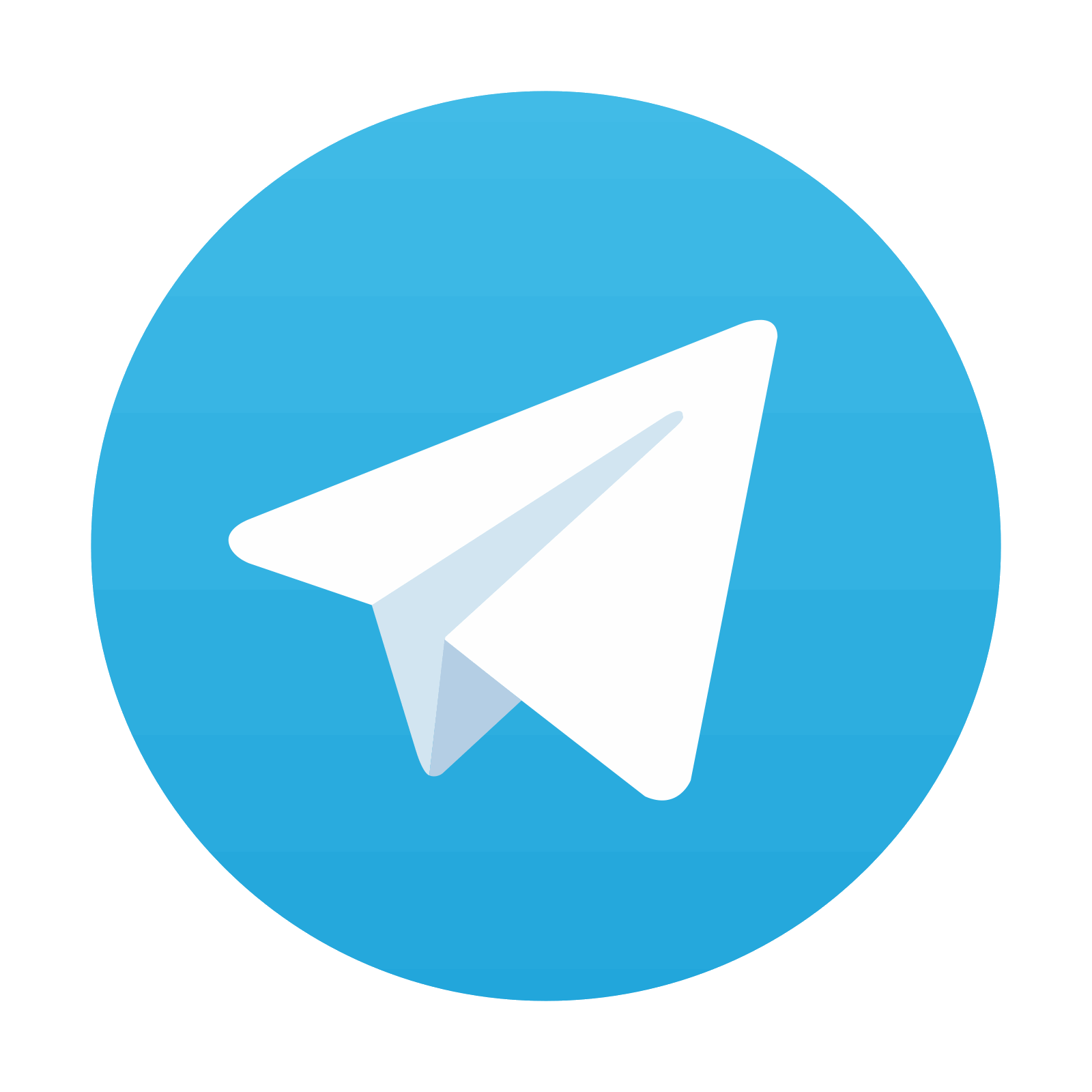
Stay updated, free dental videos. Join our Telegram channel

VIDEdental - Online dental courses
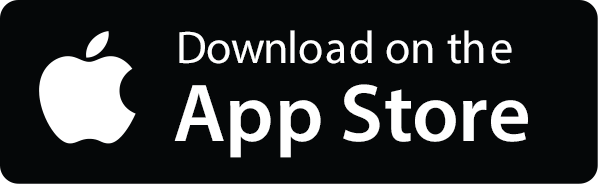

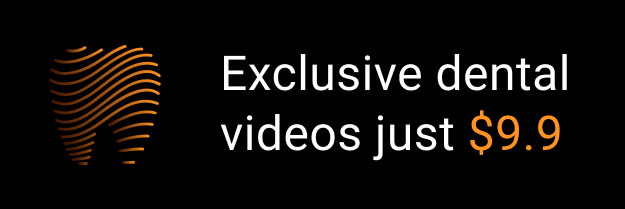