For additional ancillary materials related to this chapter, please visit thePoint.
Objectives
After studying this chapter, the student will be able to do the following:
1. Name the two types of polymerization reactions commonly seen in dental materials, and explain the meaning of “addition” in “addition polymerization.”
2. Discuss the following properties of restorative resins:
- Polymerization shrinkage
- Coefficient of thermal expansion
- Abrasion resistance
3. Summarize the relationship between a filler particle, the matrix, and the coupling agent of a composite restorative material.
4. Compare the advantages and disadvantages of light-activated and chemically activated composite materials.
5. Explain the importance of proper eye protection when light-curing dental materials.
6. Relate the importance of the following procedures and/or characteristics of dental composites:
- Depth of cure
- Addition of material in increments
- Inhibition by air
- Unreacted C═C bonds
- Shades
- Shortcomings of the matrix
7. For filler particles found in dental composites, summarize the importance of the following properties:
- Composition
- Size
- Amount (percentage)
- Abrasion resistance
- Refractive index
- Clinical detection
8. Choose one of the three types of dental composites, and justify its use in the following dental situations:
- Bonding orthodontic brackets to enamel
- Class V “gingival notch” restoration
- Small class I or II restoration
9. Briefly explain the reason(s) for the development of flowable and condensable composites.
10. Discuss the role the dental hygienist should play in the placement and maintenance of pit and fissure sealants.
11. Discuss the use of a primer with pit and fissure sealants.
12. Briefly describe “preventive resin restoration” and “composite cement.”
13. Assess the positive and negative characteristics of light-cure and chemical-cure glass ionomer cements.
14. Discuss the similarities between compomers, glass ionomers, and composites.
Key Words/Phrases
activation
addition polymerization
compomer
condensable composites
crazing
depth of cure
diluent
dual cure
filler particles
flowable composites
free radical
hybrid composite
incremental addition
inhibitor
initiation
macrofilled composite
matrix
microfilled composite
monomers
oligomer
percolation
pit and fissure sealants
polymerization
polymers
preventive resin restoration
propagation
silane coupling agent
termination
thermoplastic polymers
thermoset polymers
Introduction
Polymers are materials that are made of large, long molecules formed by chemically reacting molecular building blocks called monomers. A variety of polymers exist, and they exhibit a variety of properties. The chemical reaction that links the monomers together to produce a polymer (macromolecule) is called polymerization. Common polymers or “plastics,” such as polyethylene and Plexiglas (an acrylic resin), are made by addition polymerization and are used to make soda and milk bottles and many other everyday objects. Polyethylene materials have long, linear chains that are easily recycled because they can be remelted and reprocessed. These materials are called thermoplastic polymers because they can be heated (thermo) and molded or shaped (plastic) after the polymerization reaction, similar to wax.
Polymers with a cross-linked rather than a linear structure tend not to melt. Rather, they decompose. These materials are called thermoset polymers. They cannot be heated and molded, so their use requires them to be in the final shape when the polymerization reaction occurs. They tend to be stronger and tougher than thermoplastic materials. Most dental resins are cross-linked and are therefore thermoset.
Polymers were introduced in Chapter 2, Materials Science and Dentistry. In this chapter, we discuss acrylic resins and dental composites used to replace and restore teeth.
I. Acrylic Resins
Acrylic resins were first used in dentistry for denture bases (see Figs. 1.6 and 1.7). A denture base is the pink plastic part of a denture that simulates the gingiva and the lost alveolar bone. Denture teeth are bonded to the base to form the denture. Dental acrylic resin is the same polymer used in Plexiglas, a tough plastic that serves as a glass substitute in windows. Acrylic resins have been adapted for many uses in dentistry and are covered in greater detail in later chapters. The chemistry of acrylic resins is presented in this chapter because it is the same chemistry as that of most direct polymeric restorative materials. Acrylic resins were once used for anterior restorations but were very susceptible to recurrent decay. When dental composites became available, direct acrylic restorative materials were made obsolete. The shortcomings of acrylic resins and the improved performance of composite materials are discussed in this chapter.
A. Addition Polymerization—Optional
The polymerization reaction of acrylic resins, called addition polymerization, is very common in dental materials. The other common polymerization reaction, condensation polymerization, will be covered when impression materials are discussed. Acrylic resins and composite materials, such as restorative materials, cements, sealants, and adhesives, all set by addition polymerization. The common factor relating all these materials to each other is the same chemical structure of the reactive or functional group. The functional group is the part of the molecule responsible for its important chemical properties.
1. Functional Groups
Monomers are molecules with a reactive group that participates in the polymerization reaction. This reactive group is called the functional group. The functional group of acrylic resin monomers is the carbon–carbon double bond. We will denote this bond as C═C. The “double bond” has two pairs of electrons shared by the two carbon atoms, so four electrons are involved in the double bond. Although C═C is the reactive part of the monomer, other atoms and side groups (besides hydrogen) can be bonded to either or both of the carbon atoms of the C═C. The side groups become pendants (like a charm on a charm bracelet) on the polymer chain, and they determine the chemical and physical properties of the resulting polymer.
2. Free Radicals
The chemical (polymerization) reaction of acrylic resins is called free radical or addition polymerization. The first name, free radical polymerization, is used because a free radical, an unpaired electron, is involved in the reaction. The other name, addition polymerization, is used because one monomer at a time is added to the polymer chain as the reaction proceeds. Addition polymerization is a very common polymerization reaction used to make a variety of polymers or plastics.
B. Steps in Addition Polymerization—Optional
1. Initiation
The first step in addition polymerization reaction is called initiation. Actually, initiation can be thought of as two reactions. The first involves several activation methods to form a free radical, which is a molecule with an unpaired electron (Fig. 5.1A). In the second reaction, the free radical reacts with a monomer molecule to start a growing chain (Fig. 5.1B ).
FIGURE 5.1. Initiator molecules are activated by A1. heat, A2. chemical reaction, and A3. light to form free radicals. B. Initiation of chain growth, C. propagation of chain growth, and one example of D. chain termination are also illustrated. A, activator; I, initiator; BPO, benzoyl peroxide; NR3, tertiary amine; •, unpaired electron, a free radical; *, an excited molecule.
a. Formation of Free Radicals (Polymerization Activation)
An initiator molecule can become activated (changed into a free radical) by heat, light, or a chemical reaction. Several types of chemical reactions are used in dentistry to form free radicals. One is a chemical reaction that begins when chemicals are mixed together. The other is a chemical reaction that is started by light (Fig. 5.1A).
As a result of the various activation methods, materials are classified as heat activated (also known as heat cure), chemically activated (also known as cold cure or chemical cure), or light activated (also known as photo cure or light cure). In this text, heat and chemical activation will be presented in detail, whereas light activation will be described only in general terms.
b. Reaction of Free Radical and Monomer
Regardless of the method by which the free radical is formed, the second reaction during initiation of polymerization is for the free radical to react with the C═C of the monomer. As previously mentioned, a free radical is an unpaired electron. An unpaired electron is “unhappy” (high-energy state) and wants to form an atomic bond by pairing with another electron (forming a lower-energy state). In addition polymerization, it does so by reacting with one of the electron pairs of the C═C of the monomer. A group of three electrons, however, is not the result. Rather, a single C–C bond and another free radical on the end of the growing chain are formed, as illustrated in Figure 5.1B. The first “link” in the growing chain has been added.
2. Propagation
Figure 5.1C illustrates the second step in addition polymerization, which is the growth or lengthening of the chain. This step is called propagation. The free radical of the “initiated chain” reacts with a monomer, and the chain is one monomer longer. The process is similar to initiation. Propagation involves adding the second, third, fourth, and later monomers to the growing chain until that chain is hundreds or even thousands of monomers long. Polymerization continues as long as monomers are available to react with the free radical at the end of the growing chain. Polymerization reactions result in a long chain of monomers. Such addition polymerization reactions are also called chain-lengthening reactions.
3. Termination
Two free radicals at the ends of two growing chains may react. If they do, they will form a carbon–carbon bond, as illustrated in Figure 5.1D. At this point, no free radicals are left to continue growth of the chain. Termination of polymerization of both chains is the result; thus, termination is the name given to this step. Free radicals also react with contaminants, which may also cause termination of polymerization.
C. Activation of Addition Polymerization
1. Heat Activated
Heat-activated acrylic resins typically use benzoyl peroxide (BPO) as the initiator. Heat is the activator. When heated to 60°C, BPO breaks down into CO2 and free radical molecules, as illustrated in Figure 5.1A1. Heat-activated acrylic resins are manufactured as a powder/liquid systems. The powder and liquid are mixed to form a dough for molding into the desired shape. The polymerization reaction does not start until the material is heated, typically in a hot water bath. Most complete and partial dentures use heat-activated acrylic resins for the denture base.
2. Chemically Activated
Chemically activated acrylic resins, as well as composite materials, commonly use BPO as the initiator. A variety of chemicals is used as the activator. Activators used in dental polymers belong to a group of chemicals called tertiary amines. We will use NR3 to denote a tertiary amine, which is an organic molecule with a nitrogen atom bonded to a three carbon-containing groups. Figure 5.1A2 shows the reaction of the tertiary amine with BPO and the formation of free radical molecules. Chemically activated materials are typically a powder and a liquid that are mixed together to start the polymerization process. Chemically activated acrylic resins are used to make temporary crowns, custom impressions trays, orthodontic retainers, and many other dental devices.
3. Light Activated
Light-activated dental materials use several activator and initiator chemicals. The activator absorbs light and then reacts with the initiator. Figure 5.1A3 represents the formation of free radical–containing molecules by light activation. Light-activated materials are supplied as a single paste; no mixing is required. The polymerization process does not begin until the material is exposed to a very bright light source. The “set on demand” nature of light-activated materials has made them very popular. The most common light-activated dental materials are composite restorative materials, but a few light-activated acrylic products exist.
4. Dual-Cure Materials
Several dental materials have both chemical and light-activated capabilities. These materials are called dual-cure materials. Polymerization is started with a curing light, but material that cannot be reached by the intense light sets by the chemical activation mechanism.
D. Addition Polymerization Is an Exothermic Reaction
In chemical factories, the heat of this rapid exothermic polymerization reaction must be removed, or the rise in temperature can become dangerous. Dental acrylic resins react by addition polymerization and are also quite exothermic. In a later chapter, we see that controlling the rise in temperature is important for the proper processing of an acrylic denture.
II. Inhibitors and Competing Reactions
A. Working Time
Polymerization reactions can occur very rapidly. For a dental material to be useful, the reaction must either occur when desired (as with light-activated materials) or be delayed after mixing and occur somewhat slowly (as with chemically activated products). The reaction of chemically activated materials is initially delayed for several minutes by the presence of a chemical called an inhibitor. An inhibitor, typically hydroquinone, reacts with (destroys) the first free radicals that are produced during the initiation process. This reaction (destruction of free radicals) competes with the polymerization reaction and wins. The competing reaction of inhibitor with free radicals delays polymerization and provides working time for placement, molding, and shaping of the material. Without this delay, materials would set too fast for clinical use. After a period of time, the inhibitor is used up, and polymerization begins to occur. We shall see that other dental materials also have competing inhibition and setting chemical reactions that provide working time for their use.
B. Shelf Life—Optional
The liquid component of an acrylic resin product is almost entirely composed of monomer. In theory, one free radical could polymerize an entire container of monomer. This can happen when acrylic resin products are stored for several years. To prevent this and provide a reasonable shelf life for their products, manufacturers add a small amount of inhibitor to materials that contain monomer. Inhibitors are present at a much smaller concentration in light-activated and heat-activated products than they are in chemical-activated systems. Inhibitors provide shelf life for monomer-containing mixtures of materials. Without an inhibitor, what was once a liquid or a paste would become a solid chunk of polymer over time.
III. Problems with Unfilled Resins
Polymers without filler additives are not suitable for use as restorative materials. A discussion of several problems will aid our understanding of the importance of fillers.
A. Polymerization Shrinkage
Polymerization reactions make a few very large polymer molecules from many small monomer molecules. Atoms and molecules become packed much closer together when polymerized, and the resulting material is smaller in volume than the starting components. Polymerization shrinkage is an important problem with the use of polymers. In dentistry, polymeric restorative materials shrink when they set; thus, they have the potential to open gaps at the margins of these restorations. Bonding materials to tooth structure reduces the potential for these gaps and the resulting microleakage.
B. Coefficient of Thermal Expansion
Polymeric materials have high coefficients of thermal expansion compared to tooth structure. In fact, these coefficients can be from 2 to 10 times greater. Repeated expansion and contraction of polymeric restorative materials can open and close gaps at the margin of a restoration. This phenomenon is called percolation and is illustrated in Figure 4.1. As a result, leakage increases, and recurrent caries are much more likely.
C. Strength and Abrasion Resistance of Polymeric Materials
Even the best polymers are unable to withstand occlusal forces in the oral environment. They lack strength and abrasion resistance. Polymeric materials are useful in dentistry, however, because they can be placed into a cavity preparation as a plastic mass and then molded and shaped. Next, they are polymerized in the mouth, forming a replacement for lost tooth structure. Forming a restoration directly in the mouth is very useful, but time and temperature limit which polymers can be used.
IV. Improvements to Dental Resins
Several techniques have been used to improve dental resins. These techniques originated in nondental industries, but they have greatly improved polymeric restorative materials. The most successful and notable individual in this process was Dr. Raphael Bowen, who developed the first dental composites.
A. Fillers and Silane Coupling Agents
Industrial uses of polymers greatly expanded when strong, hard fillers were added to strengthen plastics to form composites. Fiberglass is one such material. It combines a polymer with glass fibers and is much stronger and more useful compared to the polymer alone. Composite materials were introduced in Chapter 2, Materials Science and Dentistry. Filler particles are typically inexpensive, strong, hard ceramic materials. Many fillers are naturally occurring silica (SiO) minerals, but others are specially prepared glass materials (also silica based).
Dr. Bowen incorporated a strong ceramic filler particle into his polymer system to form a much stronger dental restorative material. Two examples of dental composites are shown in Figure 5.2. To obtain the maximum benefit from the addition of these particles, the polymer (or matrix, as it is called in a composite system) is bonded to the filler particle with a coupling agent. The coupling agent couples, or transfers, stress from the relatively weak matrix to the relatively strong filler. Dental composites use ceramic filler particles coated with silane coupling agents. Silane coupling agents work a bit-like soap; they have a different chemical group at each end of the molecule. Silane coupling agents are molecules that react with the polymer matrix at one end and with the ceramic filler at the other end, as illustrated in Figure 5.3. The end that reacts with the polymer matrix has a C═C that participates in the addition polymerization reaction. The other end has a silane group, hence the name silane coupling agent. The silane group has silicon and oxygen atoms that react with the silicon and oxygen on the surface of the ceramic filler particle.
FIGURE 5.2. Scanning electron micrographs of two dental composites B and D and their filler particles A and C. The smaller filler particles result in composite restorations with a smoother surface. (Courtesy of BISCO, Inc.)
FIGURE 5.3. A. Example of silane coupling agent and B. its reaction with the polymer matrix on the left and the filler particle on the right.
Fillers are selected for their physical properties. Luckily, the strong, hard ceramic materials that are chosen also have a low coefficient of thermal expansion. When mixed with polymers, the resulting dental composites have coefficients closer to that of tooth structure than the polymers on which they are based. Because a composite has less polymer in the system, polymerization shrinkage is reduced when the material sets.
Manufacturers try to maximize the filler content of their dental composites because adding more filler increases strength, decreases polymerization shrinkage, and decreases thermal expansion to nearer that of tooth structure. However, there is a limit to the amount of filler that can be added. When mixing dough for bread, excess flour results in a defective product; the same is true for filler in dental composites. If all filler particles are not properly wetted by the liquid monomers, voids and gaps between the filler particles result. As previously mentioned, voids do not resist any stress placed on a material; they also concentrate stress in the material in the vicinity of the void.
B. Bowen’s Resin—Optional
In addition to adding fillers to form composites, Dr. Bowen also developed a polymer for dental composites. This molecule is actually a combination of several monomer molecules to form what is called an oligomer. The notable features of Dr. Bowen’s oligomer are polar side groups that increase chain-to-chain hydrogen bonding and two reactive C═C groups. Because each C═C group can participate in the formation of a growing polymer chain, the oligomer is called bifunctional. Bifunctional monomers and oligomers result in cross-linking and greatly improve the strength of the resulting polymer. Dr. Bowen’s oligomer is called bis-GMA and is illustrated in Figure 5.4 along with methyl methacrylate, the monomer most commonly found in dental acrylic systems, and triethylene glycol dimethacrylate. The bis-GMA is a very viscous material and needs to be diluted and thinned with other bifunctional monomers, such as triethylene glycol dimethacrylate, when dental composites are formulated. Although bis-GMA is more properly called an oligomer, we shall use the term monomer when referring to it.
FIGURE 5.4. Structure of A. methyl methacrylate, B. triethylene glycol dimethacrylate, and C. bis-GMA.
V. Composite Materials
Composite materials are the combination of two materials. The result is a material that is superior to either component alone.
A. Dental Composites
Dental composites are supplied in a variety of shades (colors) and handling characteristics. Their use continues to expand and replace other materials. Before dental composites were introduced, other esthetic materials were used, such as acrylic resins, but they lacked clinical efficacy. Acrylic resin materials had a high coefficient of thermal expansion, and polymerization shrinkage was excessive. Recurrent caries around and under acrylic resin restorations was typical. Silicate cements were also used as an esthetic material, but they dissolved too quickly and required frequent replacement. In the 1960s, when dental composites were developed, they quickly replaced acrylic resin and silicate restorative materials.
B. Components of a Dental Composite
Dental composites are composed of two phases: matrix and filler. The matrix is soft, weak, flexible, and prone to wear compared to the filler. In addition, two “molecular components” are present: a silane coupling agent and a polymerization system.
1. Matrix
The matrix of a dental composite is a polymer, typically bis-GMA or a similar monomer. An organic chemical called a diluent is added to control the viscosity of the final product. For both bis-GMA and the diluent, C═C is the functional group. The matrix of a dental composite polymerizes by a chemical reaction (addition polymerization). Polymerization is activated by a chemical reaction (chemical activation) or light energy (light activation). Light-activated materials are the most commonly used dental composites, but chemically activated materials have their uses.
The polymer matrix of dental composites is chemically similar to enamel and dentin adhesives. Composites chemically bond to primers and adhesives of dental bonding systems because both have C═C functional groups and both set by addition polymerization, as discussed earlier. Adhesives of enamel bonding systems and dentinal bonding systems are typically bis-GMA and diluents formulated to have the proper viscosity. The currently used dentinal bonding systems, composite restorative materials, and resin cements are very compatible with each other. It is common to use a dental bonding system from one manufacturer and composite restorative material from another.
The matrix of a dental composite has several important functions. The matrix is the phase that polymerizes to form a solid mass and bonds to tooth structure. However, the matrix has several shortcomings. It is the weakest and the least wear-resistant phase of a dental composite material. It also absorbs water and can stain and discolor. Therefore, manufacturers minimize the matrix content of composite materials by maximizing the filler content. Stronger composite materials result.
2. Fillers
In the beginning, fillers in dental composites were naturally occurring quartz materials (sand). Quartz materials are strong, hard, and chemically stable in the oral environment. Recently, manufacturers have “engineered” glass materials for dental composites. These engineered glass materials are formulated to have the proper strength, hardness, and chemical properties as well as optical properties for use in dental composites. The glass is ground to have the proper-size particles. These particles are coated with a silane coupling agent. The silanated filler is mixed with monomers, diluents, coloring agents, and other chemicals to form the paste that is purchased from the manufacturer.
a. Filler Size
The size of the filler in a dental composite determines the surface smoothness of the resulting restoration. Larger particles result in a rougher surface (see Fig. 5.2 ). Composites are most often classified by the size of their filler particles. This text will discuss three categories of dental composites: macrofill, microfill, and hybrid (blends). In reality, each category of composite has some range of particle size. It would be needlessly expensive for manufacturers to select a narrow range of particle size.
b. Evolution of Fillers
Filler particles have evolved from the strongest, most abrasion-resistant materials to somewhat softer, less abrasion-resistant materials. A softer particle is more likely to wear down rather than to be pulled out of the matrix when abrasion occurs. If a particle is pulled out, the surface is now soft resin that will wear away quickly. If the particle wears and stays partially embedded in the matrix, however, the surface has an overall greater abrasion resistance and wears at a slower rate.
c. Filler Content (Amount of Filler)
With the exception of proper handling, the percentage of filler is the most important determinant of the physical properties of dental composites. As the filler content increases, the resin content decreases. Therefore, polymerization shrinkage decreases, and the coefficient of thermal expansion becomes more like that of tooth structure. Hardness and abrasion resistance increase as well.
3. Silane Coupling Agents
Although not a true phase in a dental composite, the silane coupler is a very important component of the material. The silane coupler must be chemically compatible with both the filler and the resin phases. Manufacturers have accomplished this, and the stress placed on a restoration is thus transferred from the weaker resin phase to the stronger filler phase. Dentistry has recognized the effectiveness of silane couplers and now uses them to silanate ceramic restorations, such as a crown, in the dental lab or at chairside. The silane coupling agent enables adhesive materials to bond ceramic restorations to tooth structure.
One theory of composite wear proposes that the bond between the silane coupler and the filler particle is slightly soluble in the oral environment. As the bond is broken, the filler particles are pulled out of the resin matrix, exposing the soft resin. The resin is then worn away, exposing more filler particles to the oral environment, and the cycle continues.
4. Polymerization Systems
Two polymerization systems are used to convert the matrix–filler paste to a solid composite material. All dental composites use addition polymerization.
a. Chemically Activated Materials
Chemically activated materials are two-paste systems, as shown in Figure 5.5. One paste contains the tertiary amine, and the other contains the BPO initiator. The pastes have different colors and are mixed at chairside until the two colors blend into one. The pastes are supplied in small plastic jars or screw-type syringes. When the two pastes are mixed, the inhibitor destroys the free radicals that are produced for a short period of time, as previously described. This results in a limited amount of working time to place and contour the material. When the inhibitor has reacted completely, polymerization begins. Because two pastes are mixed, air bubbles are unavoidably incorporated during mixing. Any porosity, such as these air bubbles, weakens the set material and increases staining. Care must be taken to minimize these defects in the final product.
FIGURE 5.5. Photograph of the base and catalyst pastes (top) of the Concise system shown in Figure 4.4 and the mixed composite material (bottom).
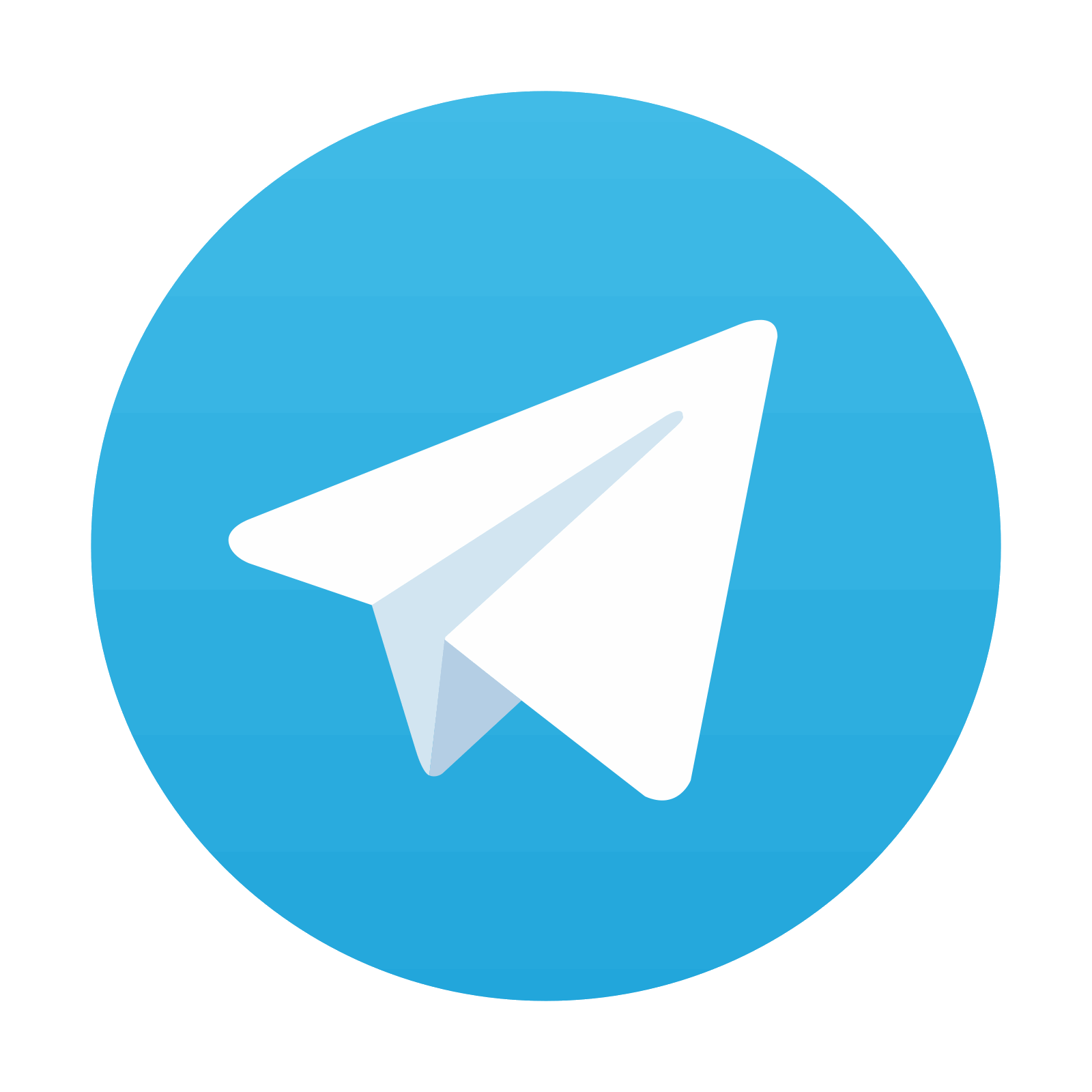
Stay updated, free dental videos. Join our Telegram channel

VIDEdental - Online dental courses
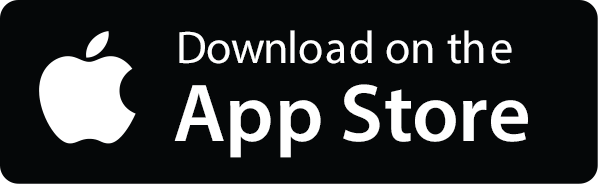
