Abstract
Objective
To evaluate the cyclic contact fatigue resistance and failure mode of ceramics for monolithic and multilayer restorations.
Methods
Ceramic structures (10 mm × 1.8 mm) were fabricated as follows (n = 28): (1) CAD-on- trilayer structure composed of Y-TZP (yttria stabilized tetragonal zirconia polycrystal- IPS e.max ZirCAD) infrastructure, fusion glass–ceramic (IPS e.max CAD Crystall/Connect) and lithium disilicate-based glass–ceramic (IPS e.max CAD); (2) ZFC- bilayer structure composed of Y-TZP infrastructure veneered by a fluorapatite glass–ceramic (IPS e.max Ceram); (3) LDC- monolithic lithium-disilicate glass–ceramic (IPS e.max CAD); and (4) YZW- monolithic Y-TZP (Zenostar Zr Translucent). All ceramics structures were bonded to a dentin analog substrate (G10). Specimens were submitted to cyclic contact fatigue test in a pneumatic cycling machine with 80 N load and 2 Hz frequency in distilled water at 37 °C. Test was interrupted after 10 4 , 10 5 , 5 × 10 5 and 10 6 cycles and the presence or absence of failure was recorded. Fatigue data were analyzed using Kaplan–Meier (log rank) and Holm–Sidak tests ( α = 0.05). The relationship between the type of crack leading to failure and the experimental group was analyzed using chi-square test ( α = 0.05).
Results
There was no statistical difference between CAD-on and YZW groups (p = 0.516), which presented the highest survival rates after cyclic loading, followed by ZFC and LDC groups (p < 0.01). There was a significant relationship between type of crack and experimental group (p < 0.001). LDC specimens showed the greatest frequency of radial cracks, while cone cracks were more prevalent for ZFC and CAD-on specimens.
Significance
Monolithic Y-TZP (YZW) showed similar fatigue resistance to CAD-on multilayer specimens, but different failure mode. Monolithic lithium disilicate glass–ceramic (LDC) and Y-TZP conventionally veneered by glass–ceramic (ZFC) showed lower survival time under fatigue.
1
Introduction
Studies have reported that all-ceramic restorations, especially veneered zirconia-frameworks, exhibit chipping, cracking, or delamination of the porcelain [ ]. These clinical failures occur due to some factors, such as: low fracture toughness and fracture strength of the veneering porcelain [ ], inadequate porcelain sintering and cooling rate [ ], low bond strength between infrastructure and veneering porcelain and thermal incompatibility between materials [ , , ].
Few all-ceramic systems were introduced attempting to minimize such problems. An option is to produce monolithic restorations using crystal-reinforced glass–ceramics, which have good mechanical and optical behaviors, but have limitations on clinical indications (e.g. long spam bridges). More recently, the composition and microstructure of zirconia-based ceramics were modified resulting in more translucent materials, offering an additional alternative to produce monolithic restorations [ ]. Another option is to replace the porcelain conventionally used to veneer the zirconia framework by a ceramic with better mechanical properties and good bonding to zirconia. This is the case of CAD-on technique (Ivoclar®), where the yttria stabilized tetragonal zirconia polycrystal (Y-TZP) framework and the lithium disilicate-based glass–ceramic veneer are fabricated using CAD/CAM technology and fused together with a low-fusion glass–ceramic, resulting in a trilayer ceramic restoration [ ].
Clinically, dental restorations need to withstand the oral environment with variable conditions of pH, temperature, and humidity, and stress induced by mastication and parafunctional habits [ ]. Moreover, ceramics are susceptible to slow crack growth (SCG) in humid environment and to fatigue mechanisms that can degrade its fracture resistance and reduce the restoration lifetime [ , ]. SCG involves the stable growth of cracks at stress intensity factor (K I ) levels lower than those necessary for the crack to become unstable (K Ic ). Stress-corrosion results from a water-assisted rupture and cleavage of siloxane bonds at the crack tip under mechanical loads [ ]. Ceramics with high glass content, such as felspathic porcelain and fluorapatite glass–ceramic, are more susceptible to SCG. Ceramics with higher crystalline content, such as lithium disilicate-based glass–ceramic and Y-TZP, are more resistant to stress-corrosion, but they can experience additional cyclic fatigue damage accumulation ahead of the crack tip in the form of localized microplasticity, or microcracking, often refer to as intrinsic fatigue mechanisms. Extrinsic mechanisms of fatigue could also be present and act in the wake behind the crack tip, reducing the effect of a crack-tip shielding process [ , ]. Therefore, fatigue failure happens at lower loads than predicted by fast fracture [ , ].
All-ceramic crowns show various fracture modes. For monolithic ceramic crowns, catastrophic failures are usually associated to radial cracks originated in the cementation surface, especially in occlusal and marginal areas. Otherwise, for multi-layered crowns, chipping and delamination are mostly associated to the veneer material and initiated from cracks introduced during axial and off-axial occlusal contacts (i.e. cone, partial cone and median cracks) [ ]. In addition, fatigue degradation has been associated with progressive surface wear due to abrasion and attrition [ ].
Thus, it is important to evaluate different monolithic and multi-layered ceramic systems under fatigue challenging as an attempt to reproduce failure mechanisms reported for all-ceramic restorations [ ]. Therefore, the objective of this study was to evaluate the cyclic contact fatigue resistance and failure mode of monolithic and multilayer ceramic structures, testing the hypothesis that monolithic zirconia and CAD-on multilayer structures show higher survival rates after cyclic loading than monolithic lithium disilicate glass–ceramic and Y-TZP conventionally veneered by glass–ceramic.
2
Materials and methods
Different ceramics and manufacturing techniques were used to obtain four types of ceramic structures (10 mm diameter × 1.8 mm thickness), simulating the configuration of ceramic restorations, as described below (n = 28):
– CAD-on : Multilayer structure made of a zirconia (Y-TZP; IPS e.max ZirCAD, Ivoclar Vivadent, Schaan, Liechtenstein) framework (1.0 mm) and a lithium disilicate-based glass–ceramic (LDC; IPS e.max CAD, Ivoclar Vivadent, Schaan, Liechtenstein) veneer (0.7 mm), fused together with a glass–ceramic (G; IPS e.max CAD Crystall./Connect, Ivoclar Vivadent, Schaan, Liechtenstein). Y-TZP and LDC blocks were turned into cylindrical structures by machining (Ferdimat CA51H, Sao Jose dos Campos, Brazil) under water cooling. The cylindrical structures were cut into disc-shaped specimens using a diamond disc under water cooling in a metallographic cutting machine (Struers Minitron, Copenhagen, Denmark). Specimens were polished (Struers Abramin, Copenhagen, Denmark) up to 800- and 1200-graded silicon carbide papers under water cooling. Y-TZP discs were sintered (Zirkonofen 600/V2, ZirkonZahn, Gais, South Tyrol, Italy) according to manufacturer’s instructions ( Table 1 ). The disc-shaped Y-TZP and LDC were fused according to manufacturer’s instructions ( Table 1 ), as described in a previous study [ ]. The thickness of G layer was estimated in 0.1 mm, since the final thickness of the CAD-on structure was 1.8 mm.
Material | Composition | Firing cycle |
---|---|---|
IPS e.max Zircad MO * | ZrO 2 , Y 2 O 3 , HfO 2 , Al 2 O 3 , SiO 3, and other oxides | Heating rate 8 °C/min; firing temperature 1500 °C for 120 min; cooling rate 8 °C/min. |
IPS e.max CAD Crystall./Connect * | Oxides, water, butandiol and chloride | CAD-on technique: Pre-drying temperature 403 °C for 2 min; heating rate 30 °C/min; firing temperature (1) 820 °C for 2 min and firing temperature (2) 840 °C for 7 min; vacuum start temperature 550 °C; vacuum finish temperature 820 °C. |
IPS e.max CAD * | SiO 2 , Li 2 O, K 2 O, P 2 O 5 , ZrO 2 , ZnO, other and coloring oxides | Monolithic: Pre-drying temperature 403 °C for 6 min; heating rate 60 °C/min; firing temperature 840 °C; vacuum start temperature 550 °C; vacuum finish temperature 820 °C. |
IPS e.max Zirliner * | SiO 2 , Al 2 O 3 , Na 2 O, K 2 O, CaO, P 2 O 5 , F, other oxides and pigments | Pre-drying temperature 403 °C for 4 min; heating rate 40 °C/min; firing temperature 960 °C; vacuum start temperature 450 °C; vacuum finish temperature 959 °C. |
IPS e.max Ceram * | SiO 2 , Al 2 O 3 , Na 2 O, K 2 O, KnO, CaO, P 2 O 5 , F, other oxides and pigments | Pre-drying temperature 403 °C for 4 min; heating rate 40 °C/min; firing temperature 750 °C; vacuum start temperature 450 °C; vacuum finish temperature 749 °C. |
Zenostar Zr Translucent ¥ | ZrO 2 , HfO 2 , Y 2 O 3 and other oxides | Heating rate 5 °C/min; firing temperature 1450 °C for 120 min; cooling rate 5 °C/min. |
* Ivoclar Vivadent, Schann, Liechtenstein. Information from manufacturers.
¥ Wieland Dental, Ivoclar Vivadent; Schaan, Liechtenstein. Information from manufacturers.
– ZFC : Bilayer structure made of Y-TZP (IPS e.max ZirCAD) framework (1.0 mm) veneered with a fluorapatite glass–ceramic (0.7 mm) (FC – IPS e.max Ceram), obtained by the traditional layering technique (powder/liquid). Y-TZP structure was fabricated as described for CAD-on. Before applying FC, a thin layer (about 0.1 mm) of IPS e.max ZirLiner (Ivoclar Vivadent, Schaan, Liechtenstein) was applied on the Y-TZP surface and fired (Programat EP5000) according to manufacturer’s instructions ( Table 1 ). The Y-TZP discs were placed into a silicone matrix (Zetaplus, Zhermack SpA, Badia Polesine, Italy) and a FC layer was applied using the conventional layering technique. The ceramic veneer was sintered according to manufacturer’s instructions ( Table 1 ).
– YZW : Monolithic structure (1.8 mm thick) of zirconia (Zenostar Zr Translucent, Wieland Dental, Rosbach vor der Höhe, Germany). A cylindrical pattern was scanned (Cerec InLab, Sirona Dental Company, Bensheim, Germany) and data was transferred to the milling machine (InLab MC X5, Sirona Dental Company, Bensheim, Germany) for multi-cylinder YZW machining. YZW cylinders were cut into discs with a metallographic cutting machine (Struers Minitron, Copenhagen, Denmark) using diamond disc under water cooling. Disc-shaped specimens were sintered (Zirkonofen 600/V2) according to manufacturer’s instructions ( Table 1 ).
– LDC : Monolithic structure (1.8 mm thick) of lithium disilicate-based glass–ceramic (IPS e.max CAD) fabricated as described for CAD-on. LDC structures were crystallized (Programat EP5000) according to manufacturer’s instructions ( Table 1 ).
Ceramic structures were bonded to a fiber-reinforced epoxy resin-based (G10- NEMA G10, International Paper, Hampton, SC, USA), which served as a dentin analog substrate [ , ]. That is, 25-mm in diameter G10 cylinders were cut in slices of 4 mm thick using a diamond disc on a metallographic cutting machine (Struers Minitron, Copenhagen, Denmark) under water cooling. Aluminum oxide particles (D50 = 110 μm; Renfert do Brasil, Ribeirão Preto, Brazil) were used to sandblast (20 s) the bonding surface of G10 with a pressure of 2 bars from a 10-mm distance. The bonding surface of all ceramic structures was also sandblasted as described for G10. Both G10 and ceramic structures were sonically cleaned in a distilled water bath (5 min), water-sprayed and air-dried before the adhesive process. The adhesive system (Primers A and B, Ivoclar Vivadent, Schaan, Liechtenstein) was applied on the sandblasted surface of G10. Bonding surface of the ceramics was treated with silane (Monobond S, Ivoclar Vivadent, Schann, Liechtenstein) for 3 min and air-dried for 10 s. The dual resin cement containing phosphate monomer (MDP) (Multilink N, Ivoclar Vivadent, Schaan, Liechtenstein) was mixed and applied on the treated surfaces of G10 and ceramic, which were bonded together and placed under a 750 g load for 1 min. Excess cement was removed with a brush (cavibrush, FGM, Joinvile, SC, Brazil) and specimens were light-activated for 40 s from each side using a light curing unit (Bluephase N, Ivoclar Vivadent, Schann, Liechtenstein; 1.200 mW/cm 2 ).
Specimens were stored in 37 °C distilled water for 24 h prior to fatigue tests in a pneumatic cycling machine (BioPDI, Biocycle, São Carlos, Brazil) with 2 Hz frequency in distilled water at 37 °C. A load of 80 N was applied to the ceramic surface with a spherical stainless steel metal piston (diameter: 6 mm) [ ]. Test was interrupted after 10 4 , 10 5 , 5 × 10 5 e 10 6 cycles and the presence or absence of failure was recorded. The fatigue protocol (load and number of cycles) was defined based on data from a pilot study. Failure was reported when cracking, chipping or catastrophic fracture was detected. Survived specimens showed no evidence of crack or fracture. Transillumination and optical microscopy were used to examine the specimens and failure report followed fractographic principles. Cracks leading to failure were classified as follows: radial crack, cone crack, and combined (when both radial and cone cracks were presented) [ ].
Fatigue data were analyzed using Kaplan–Meier and Holm–Sidak survival test ( α = 0.05). The relationship between experimental group and the type of crack was analyzed with Chi-square test ( α = 0.05).
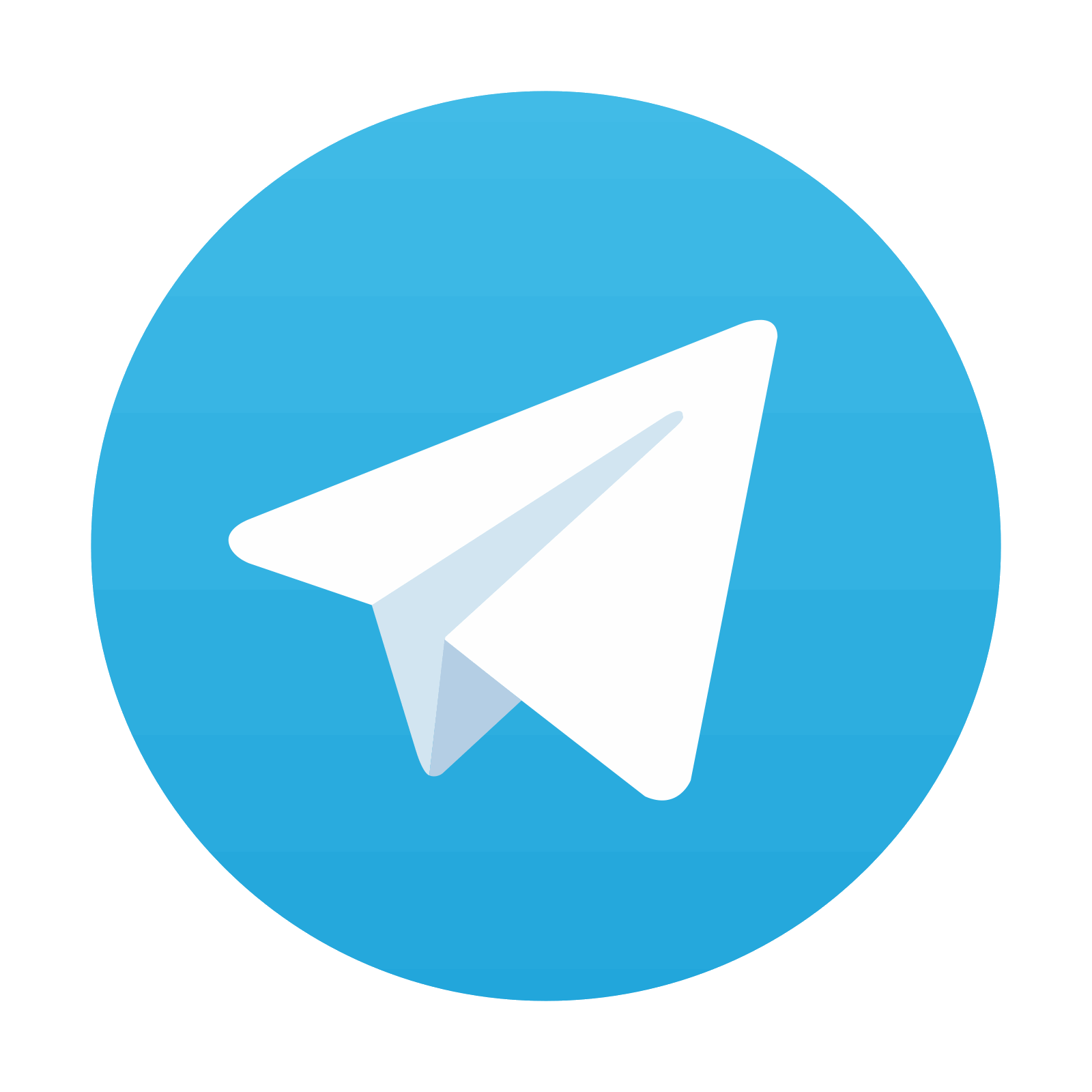
Stay updated, free dental videos. Join our Telegram channel

VIDEdental - Online dental courses
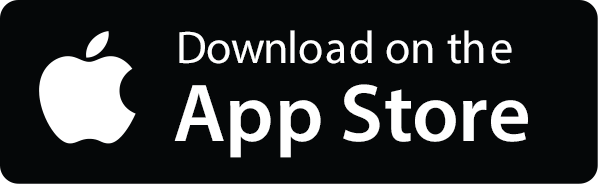
