Thank you very much for your interesting comments on our article.
We agree that the concept of a common coordinate system for cone-beam computed tomography orientation has direct implications for clinicians’ assessments of the amount of directional changes in both cross-sectional and longitudinal studies. Our article was written for clinician readers, and so we described the implications of head orientation on components of directions in 3D distances rather than describing the mathematical formulas and scalar vs vectorial variations in transformations of the coordinate system.
Prelabeling the landmarks before head orientation does not eliminate small observer imprecisions in landmark plotting. The 3D distance (Euclidean distance) was calculated directly by VAM software (Vectra; Canfield Scientific, Fairfield, NJ) based on the smallest distance between the coordinates of landmarks that the software generates after observer plotting. Small and statistically insignificant differences in 3 dimensions can be due to errors in landmark plotting. The prelabeling was performed in the ITK-SNAP open-source software ( http://www.itksnap.org/ ), and the landmark plotting was performed using the VAM software to measure the differences. Even with the prelabeling procedure, the landmark plotting can present small differences because the operator can place the landmarks in different parts of the prelabeled model (a little bit to the right or left, superior or inferior, posterior or anterior) before and after head orientation (or for 2 different time points). However, prelabeling decreases the possibility of errors because it limits the errors to the size of the prelabeled model. The prelabeling procedure was a careful methodologic step to minimize errors due to the choice of landmark locations, but it still can’t prevent all errors due to landmark plotting.
The mathematical computation for 3D measurements was implemented in the VAM software code, and there are no issues with accuracy of the software measurements.
Two-dimensional distances can cause more errors due to the operator. In our study, 2D distances were obtained by the differences between the x, y, and z coordinates of the same landmarks generated by the VAM software. But the x, y, and z differences between the 2 models were not obtained directly from the VAM software. They were calculated by applying formulas in the spreadsheets. Then, the coordinates for each landmark were copied and pasted into different sheets to calculate the x, y, and z differences for each of the 7 landmarks used in our study. Two-dimensional differences can incorporate more errors compared with 3D differences due to human failures, such as elaborating the formula, and also errors in digitalizing the data many times.
Our group has developed a new tool called “quantification of 3D components (Q3DC)” in the Slicer software (distributed as a 3DSlicer; www.slicer.org – extension, https://www.slicer.org/slicerWiki/index.php/Documentation/Nightly/Extensions/Q3DC ) that allows us to obtain the 3D distances, the 3D components (x, y, and z), and also the pitch, roll, and yaw rotations directly from the software, without needing to use formulas or transferring the data to another software, as already applied in more recent studies. The Q3DC tool decreases the possibility of error due to operator and 3D and 2D differences that would have the same range of errors (relative to landmark plotting).
Based on our experience using the software, we can suggest the following recommendations to minimize errors due to landmark placing and plotting.
During the prelabeling step, in the ITK software, we recommend that you (1) open the 2 time points in 2 separate screens of the software, side by side, using one as a guide for the other one; and (2) place the landmark using the paintbrush tool in a round shape, 3D format, size 4, using a different color of the 3D label map volume already built.
And we can also suggest the following recommendations to minimize errors in getting the measurements: (1) use the Slicer software (Q3DC tool), instead of VAM software + formulas in the Excel software; (2) open the 3D surface models of the 2 time points in 2 separate screens of the software, side by side, to place the landmarks; (3) zoom in the 3D surface models of the prelabeled landmarks and try to place the landmark in the same position in the 2 time points, displayed side by side (the more you zoom in, the easier it will be), using 1 time point as reference for another; and (4) obtain the x, y, and z differences generated directly by the Q3DC tool after checking the “calculate” icon (the software will automatically generate the differences based on the coordinates of the landmarks, without human errors and much faster than building formulas, copying, and pasting to the Excel software).
Although our findings could be checked by repeating the measurements using the new tool (Q3DC in the Slicer software), the importance of our study was mainly to reinforce the importance of head orientation after image acquisition, as already described in the literature for projected measurements (x, y, and z components) and also to propose a new reproducible method of head orientation using 3D surface models to obtain consistent measurements across subjects.
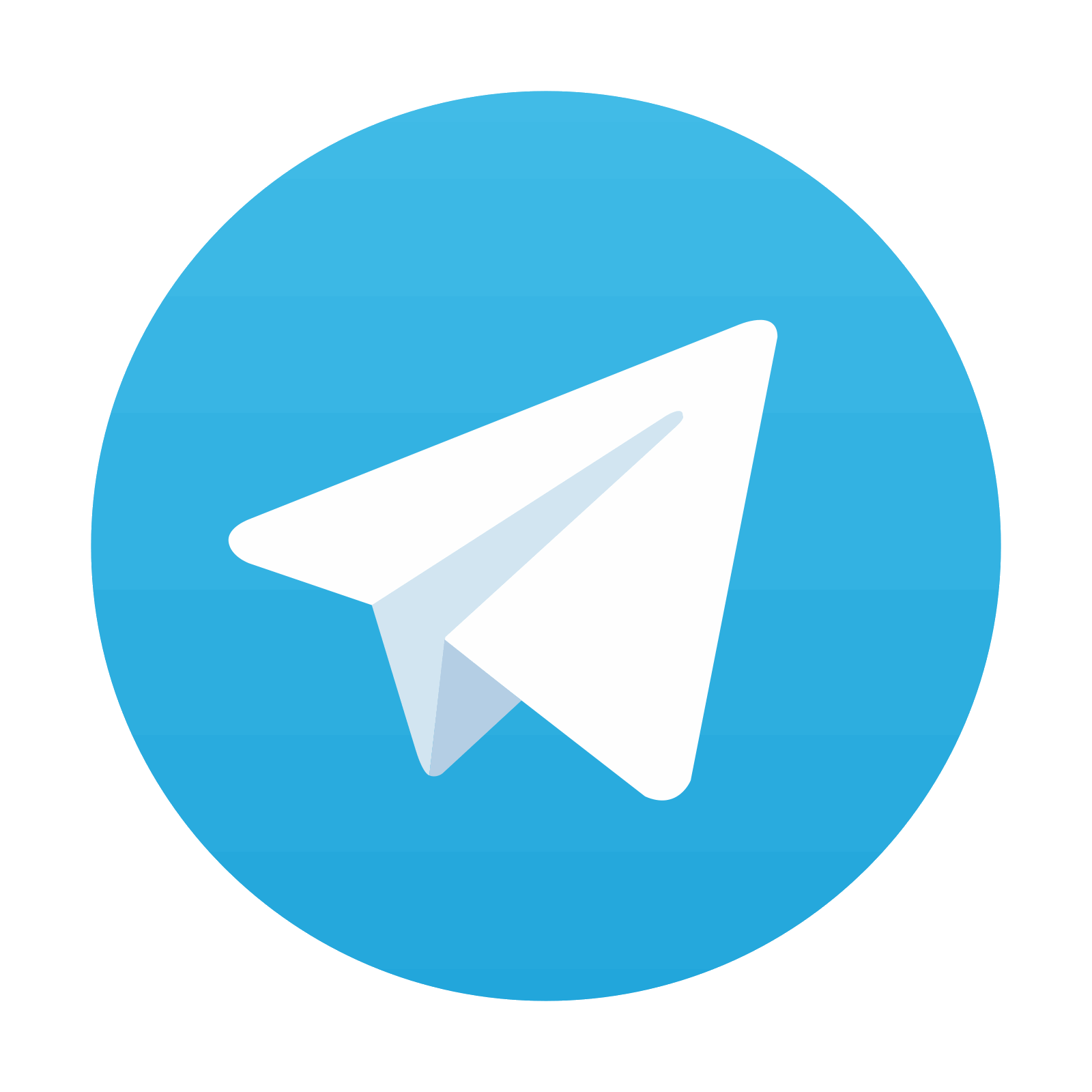
Stay updated, free dental videos. Join our Telegram channel

VIDEdental - Online dental courses
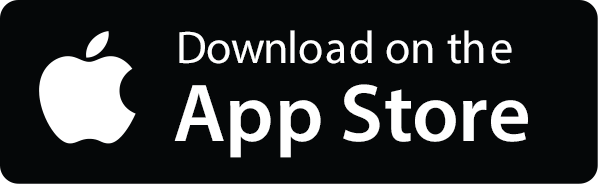
