For additional ancillary materials related to this chapter, please visit thePoint.
Objectives
After studying this chapter, the student will be able to do the following:
1. Differentiate between an amalgam alloy and a dental amalgam.
2. Compare the composition of conventional and high-copper dental amalgams.
3. Describe the function (effects) of the major elements of dental amalgams.
4. Discuss the self-sealing property of amalgam.
5. List and describe the three shapes of amalgam alloy particles.
6. Describe the effect of moisture contamination on amalgam.
7. Describe the use and advantages of direct gold restorations.
Optional
1. Discuss the trituration and setting processes.
2. Describe the reactions involved in both conventional and high-copper amalgams.
3. Recall the composition, relative strength, and relative corrosion resistance of the four most common amalgam phases.
Key Words/Phrases
admixed alloy
alloys
amalgam
amalgam alloy
amalgamation
amalgamator
blended alloys
cohesive gold
creep
delayed expansion
dental amalgam
direct gold
gold foil
lathe-cut alloys
precipitation
spherical alloys
trituration
triturator
working time
Introduction
Dental amalgam is a very old, but still widely used, restorative material. The present forms of amalgam evolved from the “silver paste” that was developed in the 1800s. The popularity of dental amalgam results from its cost-effectiveness and ease of use. During the 1970s and 1980s, more than a million amalgam restorations were placed each year. Dental amalgam is used in all surfaces of posterior teeth and, occasionally, in the lingual pits of anterior teeth. Use of dental amalgam is decreasing as caries prevention becomes more and more successful. Composites are also widely used as an alternative material.
I. What Is Dental Amalgam?
A. Amalgam is a metal alloy of which one of the elements is mercury (Hg). Alloys are metals that are a combination of several elements.
B. Dental amalgam is made by mixing approximately equal parts (by weight) of a powdered metal alloy with liquid mercury. These components are illustrated in Figure 6.1. The powdered metal is called an amalgam alloy and is predominantly silver (Ag) and tin (Sn). The mixing process of the alloy with the liquid mercury is called amalgamation or trituration. A mechanical device called an amalgamator or triturator, as shown in Figure 6.2, “shakes” the capsule containing the alloy powder and mercury at high speed, mixing the two components into a plastic mass, as shown in Figure 6.3. The triturated material is reacting or setting while it is forced, or condensed, into the cavity preparation. The cavity preparation is always overfilled with amalgam. The excess is then removed (carved) to restore the original anatomy of the tooth. The condensation and carving procedures are illustrated in Figure 6.4.
C. The setting reaction of amalgam starts during trituration and progresses while condensation and carving take place. The working time of amalgam (the time that is needed to condense and carve) is not directly controlled by the dentist, as it is with light-activated composites.
D. Amalgam is a direct restorative material that is held in place by mechanical retention. Examples of mechanical retention include undercuts and grooves that are placed by the dentist in the cavity preparation with a handpiece and bur. Examples of convergent undercuts and retentive grooves are shown in Figure 6.5.
E. The particles of the amalgam alloy may be formed by two methods.
1. The first method used to produce dental amalgam particles is grinding an ingot of metal to produce filings. Such amalgam alloys are called lathe-cut alloys, and an example is shown in Figure 6.6A.
2. The second method used to produce dental amalgam particles is to spray molten metal into an inert atmosphere. The droplets cool as they fall, producing spherical alloys, as shown in Figure 6.6B.
3. Some products are a combination of both lathe-cut and spherical particles, as shown in Figure 6.6C. These products are called admixed or blended alloys.
4. Regardless of the production method used, the particles are mixed and react with liquid mercury. The result is dental amalgam.
F. It is important to note that the term “amalgam alloy” does not mean the same thing as “dental amalgam.” Amalgam alloy is the silver–tin (Ag–Sn) powdered metal before it is mixed with mercury. Dental amalgam is the result of mixing the powdered metal with mercury and is used to restore teeth. Many times, including in this text, the terms “amalgam” and “amalgam alloy” are used. Most of the time little confusion results. Occasionally, however, it is important (usually for test questions) to understand which material is being discussed: amalgam alloy, the resulting dental amalgam, or both.
FIGURE 6.1. Starting at the left and moving clockwise: capsule, liquid mercury, pestle, freshly mixed amalgam, and powdered amalgam alloy.
FIGURE 6.2. Photographs of A. a triturator and B. an amalgam capsule in place, ready to be triturated.
FIGURE 6.3. Photograph of properly triturated dental amalgam.
FIGURE 6.4. Illustration of condensing and carving procedures. A. The cavity is prepared. B. The first increment of amalgam is placed in the preparation and condensed to eliminate voids. C and D. The second and succeeding increments are placed until the preparation is overfilled. E and F. While still “soft,” the material is carved to reproduce the proper anatomical contours.
FIGURE 6.5. Illustration of the retentive features of an amalgam restoration. Buccal (B), distal (D), lingual (L), and mesial (M) surfaces are labeled for orientation.
FIGURE 6.6. Scanning electron micrograph of amalgam particles. A. Lathe-cut amalgam alloy. B. Spherical amalgam alloy. C. Admixed amalgam alloy. (Courtesy of Special Metals Corporation, Ann Arbor, MI.)
II. Advantages of Using Dental Amalgam
Because of its toughness and wear resistance, amalgam is a long-lasting, cost-effective restorative material. In addition, amalgam has the ability to seal its margins during service. As the margins corrode, the tooth/restoration interface fills with corrosion products so that microleakage is reduced. Often, margins of a dental amalgam may look broken down but are actually well sealed just below the surface. Clinical research has shown that marginal integrity of dental amalgams is a poor predictor of recurrent decay.
Amalgam is the least technique-sensitive permanent restorative material that is available to the dentist. In addition, it is the only material that might work when placed in a wet, contaminated environment.
The life expectancy of an amalgam restoration, like that of any other direct restorative material, is indirectly related to the size of the restoration. As the restoration increases in size, the stress within the restoration also increases, and the life expectancy of the restoration decreases. Based on clinical research, the life expectancy for a conservative class I amalgam is 15 to 18 years. A class II amalgam should last 12 to 15 years. It is important to remember that the patient has a great deal of influence on the longevity of restorations. The patient’s diet and oral hygiene practices are very important and can contribute to a longer life expectancy of their restorations.
III. History of Dental Amalgam
A. Initial Development
Dental amalgam was developed in France in the 1800s and was introduced to the United States in 1833. At that time, the only alternatives for direct restorative materials were time consuming or ineffective. The clinical success of dental amalgam was improved greatly by the work of Flagg and Black.
B. Specification 1
In the 1920s, the National Bureau of Standards (now the National Institute of Standards and Technology) was asked by the US government to develop a set of standard tests for dental amalgam. The standard was enthusiastically received by the field of dentistry and became Specification #1 of the American Dental Association (ADA). Specifications are discussed in Chapter 1, Introduction. In the first half of the 20th century, most amalgam alloys followed the formula of G.V. Black because his composition was included in the specification.
C. Introduction of High-Copper Amalgam
Around 1960, an amalgam alloy with a higher copper (Cu) content was developed. Increasing the copper content reduced the percentage of the weakest phase of the resulting dental amalgam. Clinical performance improved markedly. Today, numerous high-copper dental amalgams are on the market, and a variety of particle shapes and compositions are available. The copper content ranges from 10% to 30%.
IV. Low-Copper Dental Amalgam
Low-copper amalgams are included in this text for historical perspective. In addition, they are a good starting point because of their simple composition and chemistry. Today, high-copper amalgams are the state of the art and dominate the market.
A. Composition
The composition of a low-copper, “traditional” or “conventional” amalgam alloy is based on Black’s composition: approximately 65% silver, 25% tin, less than 6% copper, and, sometimes, 1% zinc.
B. Function of Components
1. Silver causes setting expansion and increases strength and corrosion resistance.
2. Tin causes setting contraction and decreases strength and corrosion resistance.
3. In low-copper amalgams, copper functions much the same as silver.
4. If the zinc content is greater than 0.01%, the amalgam is called a zinc-containing amalgam. If the content is less, the amalgam is called a nonzinc amalgam. During manufacture, zinc reduces oxidation of the other metals in the alloy. For many years, the clinical effect of zinc was debated. Recently, clinical research has shown that zinc-containing dental amalgams have a longer clinical life expectancy than do nonzinc amalgams.
C. Setting Reaction of Low-Copper Amalgam—Optional

Or, simply,

1. γ is the Greek letter gamma and is used to designate the Ag–Sn alloy, or gamma phase.
2. γ1, or gamma-one, is used to designate the Ag–Hg phase.
3. γ2, or gamma-two, is used to designate the Sn–Hg phase.
4. When the liquid mercury is mixed with the amalgam alloy, the mercury is bold absorbed by the alloy particles and dissolves the surface of the particles.
5. Silver and tin continue to dissolve in the liquid mercury, which then becomes saturated with silver and tin. New γ1 and γ2 phases begin to precipitate. These are new compounds, the result of the setting reaction. Precipitation is a process in which a solid is formed from material dissolved in a liquid. Examples of precipitation include freezing water (ice is the precipitate), sugar that forms in old honey, and the curdling of milk (milk protein is the precipitate).
6. Precipitation of the γ1 and γ2 phases continues until the mercury is consumed and a solid mass results. The reaction products bind the unreacted γ particles together resulting in a “cored” structure.
D. Mercury/Alloy Ratio
The composition of the set dental amalgam depends on several factors. The mercury/alloy ratio is the amount of mercury that is mixed with the amalgam alloy. Using more mercury increases the mercury-containing reaction products. Using less mercury decreases the mercury-containing reaction products. Proper trituration and condensation techniques can also reduce the mercury content of the set amalgam. Because the mercury-containing reaction products are weaker than the Ag–Sn starting material, minimizing mercury results in an improved restoration. The strength of the amalgam is increased, and marginal breakdown is reduced. Remember, as with other dental materials, the liquid mercury must wet all alloy particles and form a cohesive mass without voids. An inadequate mercury/alloy ratio results in voids and poor restorations.
E. Microstructure of Low-Copper Amalgams—Optional
Dental amalgams are a mixture of elements and phases.
1. The γ (Ag–Sn) phase is typically the strongest and most corrosion-resistant phase. It is approximately one-quarter of the volume of a dental amalgam.
2. The γ1 (Ag–Hg) phase is somewhat strong and corrosion resistant, but it is also brittle. The γ1 phase makes up approximately half of the amalgam and is the matrix phase that holds this multiphase material together.
3. The γ2 (Sn–Hg) phase is the weakest and most corrosion prone. It makes up approximately one-tenth of the material, but is the “weak link” in the structure.
4. It is important to realize that the chemical formulas for amalgam phases do not include minor components, which affect the properties of each phase and of the resulting amalgam. The γ1 (Ag–Hg) phase usually contains some copper, tin, zinc, and other amalgam alloying elements.
V. High-Copper Dental Amalgams
Starting in the 1960s, a variety of high-copper dental amalgams were developed. The clinical performance of many, but not all, of these amalgams is superior to that of the best low-copper amalgams. The significant factor that determined improved performance is elimination of the weak γ2 phase. Strength is increased, and corrosion and marginal breakdown are reduced. Currently, high-copper amalgams dominate the dental market. These high-copper amalgams can be categorized into several groups.
A. Admix High-Copper Amalgam
“Blended,” “admix,” or “dispersion” alloys are a mixture of two kinds of particles, as shown in Figure 6.6C.
1. These high-copper amalgams contain lathe-cut particles with the same composition as those of the low-copper amalgam alloys, silver and tin. The other particles are spherical and contain 28% copper and 72% silver. This composition is called the Ag–Cu eutectic.
2. The first high-copper amalgam was “Dispersalloy,” developed by Innes and Yondelis in Canada in 1963. It was originally sold to Johnson & Johnson, but the patent and trademark have since been sold several times to other dental materials companies. Several admix amalgams are available, but Dispersalloy maintains a significant market share.
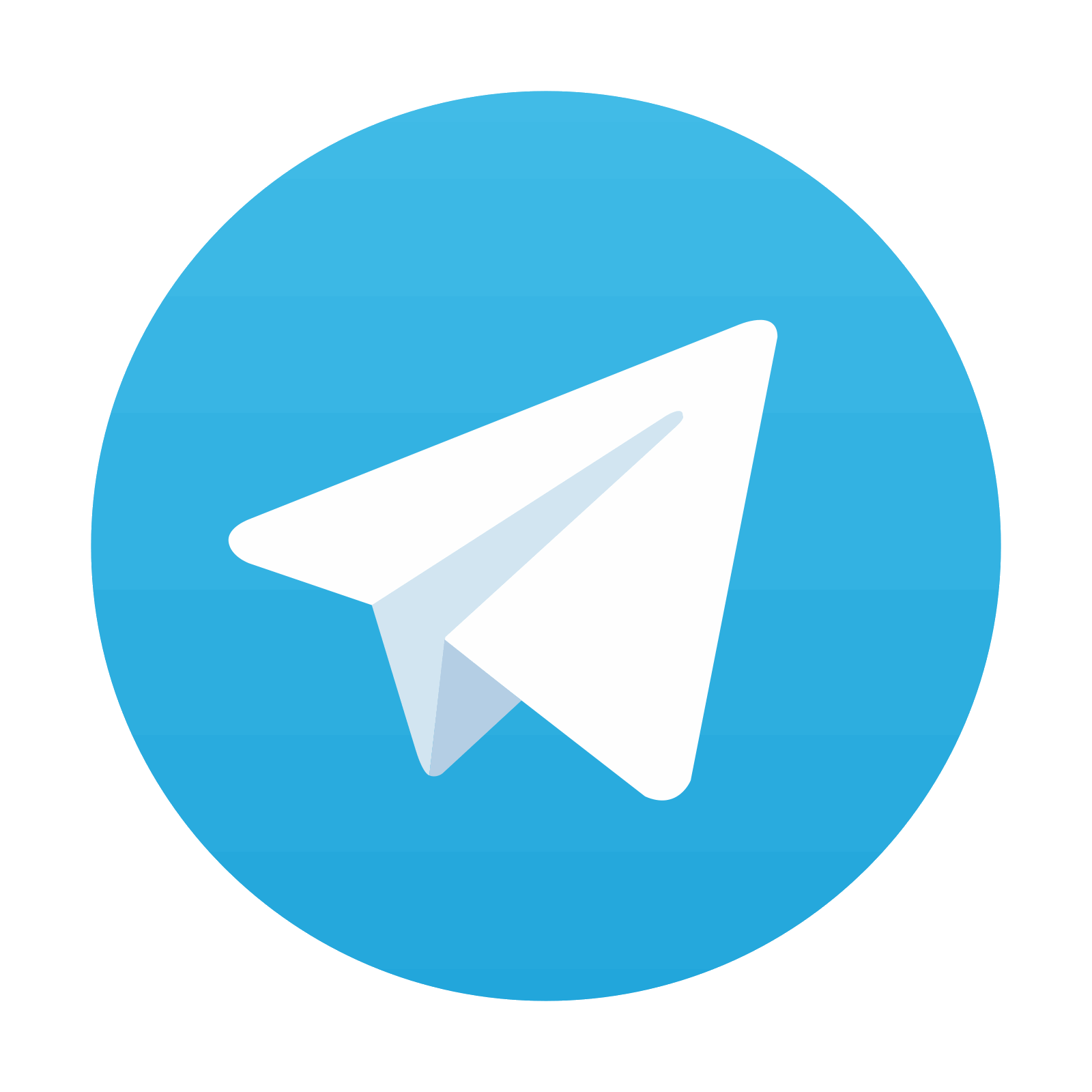
Stay updated, free dental videos. Join our Telegram channel

VIDEdental - Online dental courses
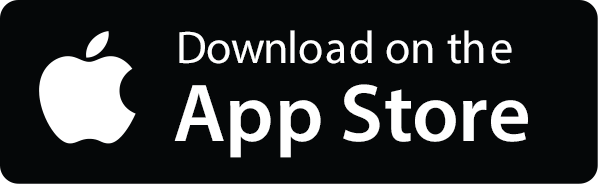
